Diseño y puesta a punto de una máquina de corte por láser tipo pórtico multicabezal de gran dinámica
Lazpiur S.A., en colaboración con IK4-Tekniker, ha diseñado y fabricado una máquina de corte por láser con arquitectura tipo pórtico multicabezal de gran tamaño. Esta máquina se dedicará al corte de piezas de formas muy complejas con gran precisión y una elevada dinámica. Tras una fase inicial de diseño, se ha desarrollado un modelo teórico para verificar el comportamiento dinámico de la máquina antes de su fabricación. Este modelo ha permitido hacer un diseño iterativo en el que se han introducido las variaciones mecánicas necesarias para conseguir el compromiso precisión-velocidad óptimo. En la fase de puesta a punto se ha observado la influencia de la estrategia seguida para llevar a cabo el redondeo de aristas vivas.
1. Introducción
Una de las principales ventajas de los procesos de corte por láser de chapas finas es la gran velocidad de avance admisible [1]. Por ello, las máquinas de corte por láser deben tener unas capacidades dinámicas lo más elevadas posibles para sacar provecho de esta característica y hacer que los tiempos de ciclo de las piezas a fabricar sean lo más pequeñas posibles. Lazpiur S.A., en colaboración con IK4-Tekniker, ha desarrollado una máquina de corte por láser de chapa.
Para que un proceso de corte de chapa mediante láser sea rentable, los tiempos de ciclo de la máquina deben ser muy bajos lo que se requiere que la dinámica de la máquina sea especialmente alta. La habitual forma compleja de las piezas cortadas mediante este proceso hace que el tiempo de ciclo sea aún más dependiente de las capacidades dinámicas (aceleración y jerk) de la máquina.
En este trabajo se reflejan los pasos seguidos para el diseño, fabricación y puesta a punto de la máquina. Inicialmente, se define la arquitectura de la máquina y las condiciones dinámicas (velocidad, aceleración y jerk) para cumplir con los tiempos de ciclo requeridos, con los que se realizará un primer diseño. Seguidamente, se realizará un modelo teórico basado en elementos finitos que permitirá analizar el comportamiento dinámico de la máquina, facilitando la realización de cambios en los accionamientos y estructura y analizar su efecto. Finalmente, tras la fabricación de la máquina, se pasará a una fase de puesta punto en la que se verificará que ésta cumple con los requerimientos establecidos.
2. Diseño
Se ha optado por una arquitectura tipo pórtico para el diseño de la máquina. Para aumentar la productividad de la misma se van a usar dos pórticos que montarán dos cabezales de corte cada uno (Figura 1). Así, a expensas de un mayor tamaño de máquina (aproximadamente, 3 metros de recorrido en X y 2 metros de longitud de pórtico) y la consecuente reducción de sus capacidades dinámicas, se podrán cortar 4 chapas al mismo tiempo.
Se han utilizado motores lineales para la generación de movimiento de todos los ejes de la máquina. Al evitar las flexibilidades e inercias de los husillos, acoplamientos, ejes, etc. los motores lineales permiten mayores aceleraciones y posicionamientos con un mayor ancho de banda [2].
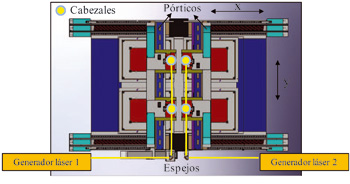
El tiempo de ciclo de cada una de las piezas dependerá de las limitaciones dinámicas impuestas: velocidad, aceleración y jerk máximos. La velocidad máxima está definida por el proceso de corte y, en la aplicación definida, será de 1 m•s-1. La aceleración máxima viene limitada por el accionamiento, en este caso los motores lineales elegidos (Tecnotion TBW30 y TBW18), y la masa total a mover. Debido a la complejidad de las geometrías a cortar en este tipo de máquinas, el jerk (derivada de la aceleración en el tiempo) tiene un efecto importante en los tiempos de ciclo. A un mayor valor de jerk le corresponderá un menor tiempo de ciclo. Sin embargo, un valor alto puede dar lugar a una excitación de los modos de vibración de la máquina y una pérdida de precisión en la geometría lograda, por lo que la configuración de este parámetro es importante. La Tabla 1 muestra los valores predefinidos de aceleración y jerk en cada eje.
Los requerimientos de alta dinámica impiden el montaje del generador láser sobre las partes móviles de la máquina y, por tanto, debe estar situado en la parte fija (bancada). Para la transmisión del haz láser desde el generador (parte fija) a los cabezales (partes móviles) se va a utilizar un sistema de reenvío mediante espejo. De esta manera, un mismo generador láser puede alimentar a los dos cabezales de un mismo pórtico.
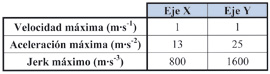
3. Modelo teórico
Con las bases presentadas en el anterior apartado se ha realizado un primer diseño de la máquina del que se ha desarrollado un modelo de elementos finitos. El modelo indica la existencia de un modo de flexión del pórtico aparece a 35 Hz (Figura 2) que va a tener una influencia directa en la posición del haz.
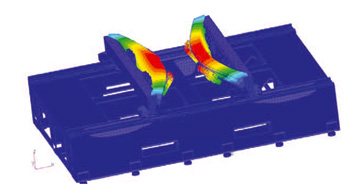
Seguidamente, se ha realizado un modelo teórico de la máquina, habitualmente llamado ‘Máquina Virtual’, que agrupa la dinámica de la estructura, obtenida mediante el análisis FEM, y la parte de control [3]. Se ha implementado la arquitectura de control típica de estas aplicaciones, con un lazo de velocidad (PI) y uno de posición (P). Como esta aplicación requiere de un error de seguimiento mínimo para que la forma de las piezas sea aceptable se implementan tanto el feedforward de velocidad como de aceleración. Introduciendo las señales temporales generadas usando un programa CAD/CAM y un simulador de CNC Fagor como input del modelo se puede estudiar la respuesta dinámica de la máquina y verificar que al aplicar las condiciones dinámicas (aceleración y jerk) predefinidas en cada eje (Tabla 1), las precisiones geométricas obtenidas son satisfactorias.
4. Puesta a punto
Tras la validación del diseño se procede a la fabricación y montaje de la máquina y a su posterior puesta a punto. En esta fase se detectan errores en el corte mayores que los estimados en el modelo teórico desarrollado.
Primeramente, se observa que al sustituir el cabezal láser por un utillaje en el que se monta un rotulador la geometría conseguida es considerablemente mejor, similar a la obtenida en el modelo teórico. Así, se concluye que el sistema de espejos para el desvío del láser es poco rígido y hace que el propio haz llegue al cabezal con un movimiento oscilatorio. Este fenómeno ha sido previsto ya que estos elementos no habían sido incluidos en el modelo de elementos finitos. Afortunadamente, dotar de una mayor rigidez a este sistema resulta sencillo, eliminando las oscilaciones.
A pesar de haber solucionado este problema, se siguen observando errores en la geometría de la pieza aunque a una escala mucho menor (también se observaban en el modelo teórico). A pesar de reducir las restricciones dinámicas de los ejes y minimizar, así, la posibilidad de excitar el modo de vibración del pórtico, no se observan mejoras. Analizando los perfiles de aceleración de las consignas generadas por el control numérico para cada eje se observa que en muchos puntos no se respetan estas restricciones dinámicas (escalones de aceleración en la Figura 3.a que no respetan el límite de jerk), excitándose los modos de vibración de la máquina. Estos puntos coinciden con los instantes en que el CNC tiene que generar un redondeo de una de las múltiples aristas vivas que tienen las piezas a cortar. Tras probar diferentes opciones para hacer los redondeos (circular, parabólica, curvas de Bezier…) y jugar con los parámetros configurables no se consigue evitar que las restricciones dinámicas no sean sobrepasadas. De hecho, el problema de realizar transiciones entre segmentos para suavizar las trayectorias no debe de estar totalmente dominado por los fabricantes de controles numéricos y actualmente se siguen realizando trabajos en torno a este tema [4-5]. Eliminado la suavización en las transiciones, es decir, trazando aristas vivas, se observa que el comportamiento dinámico es mucho mejor (Figura 3.b) y la calidad de las piezas mejora notablemente, entrando dentro de los límites aceptables.
5. Conclusiones y líneas futuras
Se ha diseñado y fabricado una máquina de corte por láser de chapa. Debido a la alta productividad exigida, se ha optado por una arquitectura tipo multipórtico en el que 4 cabezales láser trabajan de manera simultánea. Esta arquitectura, con una gran longitud de pórtico, hace que la máquina sea un sistema con una dinámica limitada por lo que la correcta selección de las restricciones dinámicas (aceleración y jerk máximos) y de la configuración de los lazos de control cobra una gran importancia para obtener piezas de calidad aceptable y dentro de los tiempos de ciclo requeridos.
Antes de la fabricación y puesta a punto de la máquina se ha realizado un modelo teórico en el que se engloban tanto la estructura de la máquina como el control de los ejes de movimiento para verificar el comportamiento dinámico de la misma. Los resultados obtenidos en la máquina real concuerdan con los obtenidos en este modelo teórico. Para futuros trabajos conviene incluir en el modelo teórico el sistema de desvío del haz del láser.
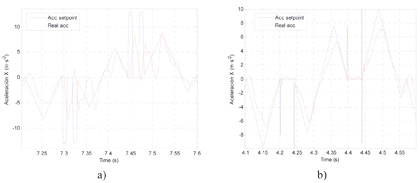
Tras la realización de este trabajo se han visto varios puntos con los que se podría optimizar el comportamiento de la máquina:
- Modificar el sistema de transmisión del haz láser para evitar las oscilaciones del haz causadas por la vibraciones de los espejos (p. e. fibra óptica).
- Modificar las estrategias de redondeo de aristas vivas para lograr trayectorias más suaves y rápidas (actualmente la máquina se detiene en cada arista viva).
- Aplicación de sistemas axis on axis [6] que están especialmente ideados para este tipo de máquinas que combinan largos recorridos con altas prestaciones dinámicas y/o gran precisión.
Referencias
[1] N. Dahotre, S. Harimkar; Laser Fabrication and Machining of Materials, Springer, 2008.
[2] Y. Altintas, A. Verl, C. Brecher, L. Uriarte, G. Pritschow; Machine Tool Feed Drives, CIRP Annals - Manufacturing Technology, v60-2, p 779–796, 2011.
[3] Y. Altintas, C. Brecher, M. Weck, S. Witt; Virtual Machine Tool, CIRP Annals - Manufacturing Technology, v54-2, p 115–138, 2005.
[4] X. Beudaert, S. Lavernhe, C. Tournier; Feedrate interpolation with axis jerk constraints on 5-axis NURBS and G1 tool path, International Journal of Machine Tools and Manufacture, v57, p 73–82, 2012.
[5] S. J. Yutkowitz, Apparatus and Method for Smooth Cornering in a Motion Control System (SIEMENS), United States Patent – US 6922606 B1, 2005.
[6] M. Armendia, J. Madariaga, I. Ruiz de Argandoña; Axis On Axis System To Improve Machine Tool Productivity, 9th International High Speed Machining, March 2012.