Illig facilita el termoconformado para las más diversas piezas moldeadas
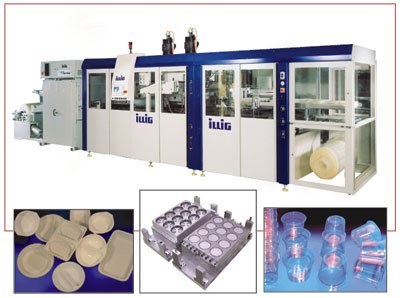
En su versión básica las máquinas están equipadas con calefacción superior e inferior, siendo posible procesar materiales como el PS, PVC, APET, OPS, PE y PP en grosores de 180 µm a 2,5 mm.
Las máquinas RDK marcan pautas tanto por su construcción mecánica como por su manejabilidad. El uso consecuente de dinámicos servomotores junto con la más moderna tecnología de control y regulación garantiza un ajuste exacto de recorridos y velocidades, permitiendo asimismo efectuar un ajuste básico asistido por ordenador de los datos de la máquina. Con ello se hace realidad una mayor disponibilidad, un incremento del rendimiento y mejoras en la calidad del producto.
La estación de moldeo/troquelado está equipada con una mesa móvil superior y una inferior. Para obtener óptimos resultados de corte se ha optimizado las palancas acodadas, las mesas y las columnas-guía para una fuerza de troquelado máxima. La fuerza de cierre y de troquelado necesaria se aporta a las mesas mediante palancas acodadas dobles y mediante servomotores con piñón movido por rosca. Para que no se formen fuerzas transversales en las guías de columna de las mesas de moldeo, la fuerza se introduce centralmente por la articulación de la palanca acodada doble. El perfil de velocidad concebido con precisión de la palanca acodada doble permite introducir la fuerza máxima durante el proceso de troquelado.
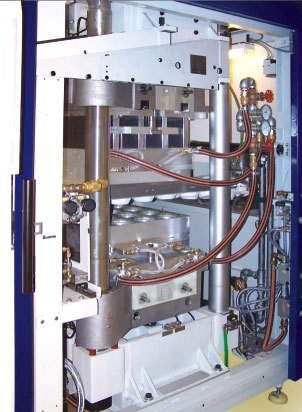
Gracias a la técnica del servoaccionamiento empleada por ILLIG, con la que es posible coordinar con gran precisión los movimientos de la mesa de moldeo con la del émbolo de preformado, puede lograrse una óptima distribución del grosor de las paredes laterales del producto. Esta mejor distribución de material permite además la misma estabilidad del producto para un menor grosor del plástico de partida. Ello da lugar a una mejora cualitativa de los productos, como por ejemplo una mayor rigidez de la pieza moldeada y unos bordes de sellado totalmente exactos y planos por toda la superficie de sellado, que se obtienen gracias a pisadores refrigerados en el útil.
La disposición directa de las válvulas de vacío y aire comprimido en la estación de moldeo permite tiempos de llenado muy cortos para cada una de las cavidades y con ello tiempos de ciclo muy cortos. El moldeo puede tener lugar, a elección, en la mesa superior y en la inferior por vacío y/o por aire comprimido. Al preseleccionar el programa de moldeo deseado en el panel de control se realizan automáticamente todos los ajustes necesarios.
Un detalle importante para el procesamiento del PP es el dispositivo de expansión para transportar el plástico. Mediante este dispositivo el transporte del plástico se separa neumáticamente en la zona de la estación de moldeo, se tensa el plástico y se evita de este modo que se formen arrugas en el proceso de moldeo. El valor de expansión necesario se obtiene a partir de la dilatación térmica del plástico.
Para adaptar la calefacción superior y la inferior al paso del transporte se pueden desconectar cuatro hileras de resistencias en el lado de entrada. De este modo se compensa las influencias de temperatura del útil de moldeo y el enfriamiento del marco tensor, y se evitan las marcas de enfriamiento en las paredes laterales de los productos. En la calefacción superior e inferior, cada una de las hileras de resistencias se regula mediante resistencias piloto. En función del paso de transporte y de la anchura del plástico se desconectan automáticamente las hileras de resistencias que no sean necesarias. Otras sucesiones de movimientos, como ayuda de desmoldeo para piezas moldeadas con entalladuras de apilamiento o un sistema de mando de piezas sueltas, ayudan a fabricar piezas moldeadas con entalladuras muy fuertes.
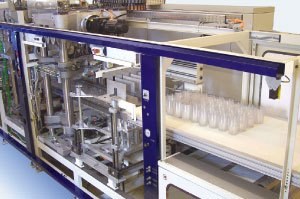
Ajuste básico asistido por ordenador de los datos de ajuste de la máquina
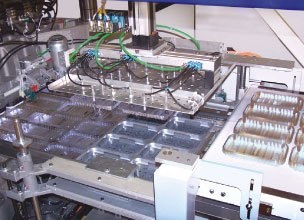
Para que las piezas moldeadas, como por ejemplo bases para bombones y galletas, no queden trabadas en la pila y puedan desapilarse sin problemas, se utiliza el apilamiento alternado.
En el caso de útiles de moldeo de varias hileras, los botones de apilado pueden ser diferentes y estar dispuestos de varias maneras. En la estación de apilamiento las hileras de productos que están unas junto a otras son empujadas unas sobre otras y se apilan en una sola hilera (apilamiento A-B). La posición de los botones de apilado, que varía según cada pieza moldeada, mantiene separadas las piezas.
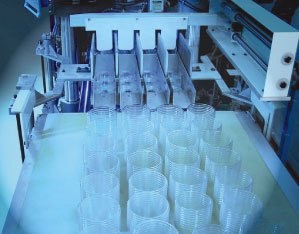
Series más pequeñas y una mayor diversidad de productos ponen más requisitos al cambio de formato
Además de la técnica convencional de cambio rápido de útil es posible cambiar insertos de molde y fondos sin tener que retirar la parte superior del útil. Las piezas de formato de la parte inferior del útil se cambian en un dispositivo a tal efecto.
La construcción modular de las máquinas RDK permite utilizar las más diversas técnicas de procesos para moldear, troquelar y apilar los productos, que pueden completarse con un molino triturador de retal de lámina. Para la colocación de bases de succión, para decorar los envases o para imprimir códigos de barras se utiliza un bastidor intermedio donde poder utilizar dichos dispositivos.
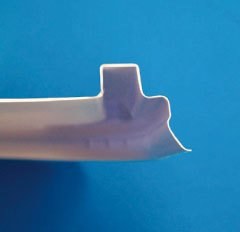
Gracias a las ventajas de la técnica de procesos, gran parte de las máquinas RDK se utiliza para la fabricación de tapas
Para procesar material preimpreso, como en la fabricación de tapas, hay disponible un dispositivo de mando con célula fotoeléctrica. El transporte servomotorizado del plástico permite, junto con la célula fotoeléctrica, el exacto posicionamiento del plástico impreso en el útil de moldeo.
Según aplicación y requisitos de la producción, la célula fotoeléctrica está situada en la máquina. El plástico debe llevar unas marcas de impresión a la distancia de los motivos. Una vez ajustado el avance a marcha rápida tiene lugar la búsqueda de la marca de impresión a marcha lenta. El ciclo de búsqueda finaliza en cuanto se reconoce la marca de impresión. El plástico aún seguirá transportándose la distancia correspondiente a la corrección de la marca de impresión. Este modo de obrar permite regular con precisión la posición de la imagen impresa.