Publirreportaje: Línea robotizada para el mecanizado de aros de rodamientos
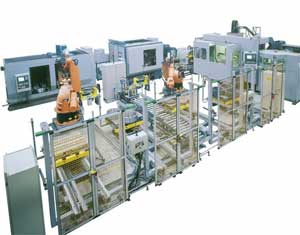
Acorde con esta política, Casals-Fonseca, S.A. ha tomado recientemente la representación de la firma italiana IMT Intermato, fundada en 1983 y especializada en la construcción de máquinas CNC y líneas de mecanizado con gran contenido tecnológico.
Desde su inicio, IMT Intermato se especializó en el sector del automóvil como fabricantes de líneas completas de fabricación de llantas de automóviles y de camiones y también en la construcción de líneas de fabricación de pistones para motores de explosión. Hace algunos años decidió ampliar su área de negocios introduciéndose en la mecánica general, fabricando tornos verticales de hasta más de 6 metros de diámetro de plato. Pero siempre ofreciendo también a sus clientes soluciones “completas” totalmente automatizadas y llaves en mano.
En este contexto se encuentra la construcción de esta línea robotizada que aquí presentamos para el proceso productivo completo de aros de rodamientos con diámetros variables de 400 a 700 mm.
Completa automatización
Así pues, esta línea robotizada está dedicada a la producción de aros para rodamientos de máquinas de movimiento de tierras.
Está estructurada en dos células, realizando los mecanizados de torneado, taladrado, roscado y tratamiento térmico en piezas con diámetros variables entre 400 y 700 mm. De forma totalmente automática y con un tiempo medio de recorrido de la pieza desde la entrada del desbaste hasta la salida del producto acabado de aproximadamente 6 minutos para las piezas más grandes.
La línea se ha subdividido en dos células, continua diciendo Casals, para permitir en caso de avería en alguna de ellas la funcionalidad de la otra. Todo se realiza en automático. Simplemente cambiando el flujo de ingreso / salida pallets -que de dos vías de entrada de los desbastes y de dos vías de salida de las piezas acabadas- se transforma en una de entrada de los desbastes y en otra de salida de los semiacabados. De esta forma la línea nunca quedará improductiva, en todo caso permanecerá a régimen reducido.
Las piezas en bruto se posicionan en los pallets sin ningún orden lógico, colocadas aleatoriamente por el operario. La primera dificultad que la línea debe afrontar es la de amarrar la pieza de la forma correcta. El robot dedicado a esta operación es un robot antropomorfo Kuka con pinzas flotantes que palpan la pieza y la pueden coger en cualquier posición en que se encuentre. Es importante recordar, continua diciendo Casals, que ésta es una línea completamente automática donde la intervención del hombre está limitada a la carga de las piezas en bruto en los pallets, a la descarga de las piezas al final de la línea y a una única operación (cuando es necesario) en el torneado.
El otro elemento a considerar es que la línea puede programarse para efectuar ciclos de mecanizado para rodamientos de diámetro 400 hasta 700 mm alternativamente y que el reutilaje de la línea para los diferentes diámetros se efectúa siempre de forma automática sin la intervención de ningún operario. Todo está gestionado vía software.
Para reconocer el diámetro de la pieza a coger, el robot lee el código de barras impreso en la misma pieza y de esta forma también verifica que el lote insertado corresponde al programado. En el caso que el operario por error haya colocado una pieza de 700 mm en un lote 400 mm, el robot detecta la anomalía y deposita la pieza en la zona de rechazo.
Una vez el robot ha recogido la pieza correcta la deposita en el torno vertical mod. S32-T2 de producción IMT, para efectuar la primera operación de torneado.
Este torno dispone de un plato autocentrante de 6 garras acopladas que realizan un centraje perfecto e impiden la deformación del anillo. Este anillo debe ser mecanizado tanto en el interior como en el exterior, por lo que es necesario un centraje interno y después otro externo. IMT ha diseñado garras únicas para todos los diámetros y todos los amarres, a través de los cuales es posible mecanizar todas las piezas sin perder tiempo de cambio de utilaje. La única operación en la que está prevista la intervención del operario, es cuando se pasa de un lote de piezas de 400 mm a otro de 700 mm y viceversa. Indica Casals, que “era demasiado difícil realizar en automático la adaptación del plato autocentrante al diámetro a mecanizar. En colaboración con el proveedor del plato y con el cliente final se estudió una solución muy refinada: el plato autocentrante está dotado de una dentadura Hirth. Con un solo cuarto de giro realizado manualmente se sueltan las 6 garras que se posicionan luego en base al diámetro de la nueva pieza a trabajar y son fijadas nuevamente con otro simple cuarto de giro de tuerca. Es una operación rapidísima y la única que necesita la intervención humana”.
Esta solución marca explícitamente otra de las características de la filosofía IMT: “la colaboración con el cliente y con el proveedor de los diversos utilajes es para nosotros fundamental. IMT - prosigue Casals - es especialista en las máquinas, el cliente es el especialista del proceso y gracias a su colaboración podemos saber por ejemplo, cuál es la mejor herramienta para mecanizar un determinado tipo de material”.
Terminada la primera operación de torneado, la pieza es retirada por el mismo robot se deposita sobre el banco de volteo para ser luego cargada en el centro de mecanizado horizontal mod. HDM-1, también construido por IMT. Esta máquina realiza el taladrado y los roscados radiales. “Ser especialistas de soluciones de automatización significa saber adaptar todas aquellas observaciones que sólo la experiencia de los años enseña. Aquí un ejemplo: aparentemente utilizando un robot antropomorfo, esta célula no debería necesitar un banco de volteo. Pero para asegurar la máxima precisión es necesario que la pieza nunca sea abandonada. Que esté siempre en posición positiva”.
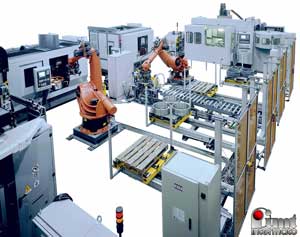
Efectuada estas operaciones, la pieza semielaborada está lista para la segunda fase. Esta fase incluye el torneado de las pistas de desplazamiento de las esferas y el control dimensional sobre una máquina de medición MARPOSS. Los valores dimensionales detectados son retroalimentados hacia los mecanizados interesados.
Acaban aquí las operaciones de la primera célula y la pieza semielaborada es recogida ahora por el segundo robot Kuka para iniciar el proceso de mecanizado en la segunda célula.
Antes de iniciar las operaciones de taladrado, la pieza se coloca en otra máquina no suministrada por IMT, que la templa por inducción en la parte de las pistas de desplazamiento de las bolas. Dado que el tratamiento térmico provoca siempre una deformación de la pieza, ésta se coloca en una prensa que la endereza correctamente, después la pieza se coloca en el centro de mecanizado vertical mod. DW-22VP que trabaja en forma pendular. En esta máquina se realiza el mecanizado más largo de todo el ciclo: los agujeros axiales.
Al tratarse de un mecanizado muy largo, IMT decidió utilizar un centro de mecanizado tipo pendular que consiente reducir los tiempos: mientras una pieza es mecanizada en un extremo de la mesa, en el otro se carga y descarga otra pieza. Después de esta operación el anillo está acabado y puede ser apilado en el pallet para salir de la línea robotizada.
El panel de control, ubicado fuera de la línea, permite monitorizar cada estación individual, verificar cualquier anomalía y lanzar los ciclos de mecanizado. Esta línea ha sido estudiada para trabajar en continuo en tres turnos diarios, de los cuales dos parcialmente vigilados y otro completamente sin vigilancia. La experiencia acumulada por esta línea demuestra que puede trabajar con un solo turno vigilado de los tres.
Así pues, el objetivo ha sido ampliamente alcanzado: optimizar los tiempos y reducir los costes.
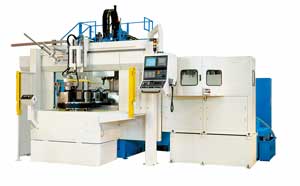
Características de las máquinas
Torno vertical modelo S32-T2
Máquina extremamente flexible, que permite el mecanizado de piezas de pequeñas / medianas dimensiones. Volteo máximo de 800 mm. Facilidad de carga, ergonomía y seguridad son las características de este torno. Que para mecanizados muy gravosos y/o de alta precisión se puede equipar en versión Ram con sustentación hidrostática 230 x 230 mm del carro vertical.
El husillo con ASA 15” es del tipo cartucho y están disponible en varias versiones como la P1 estándar, la rápida V y la P2 para mecanizados pesados. Todos con lubrificación permanente Long Life y con la variante de niebla de aceite.
Centro de mecanizado horizontal modelo HDM-1
De esta forma se cubren todas las posibles combinaciones que necesita el mecanizado de un anillo para rodamientos.
Centro de mecanizado vertical pendular modelo DW-22VP
IMT demuestra su elevado dinamismo al proponer a sus clientes soluciones personalizadas que nacen de una elevada estandarización de sus componentes. Las ventajas de la modularidad son la elevada fiabilidad y la eficiencia productiva de las máquinas y de los sistemas. IMT se hace garante ante sus clientes de una inmediata respuesta del servicio de asistencia que incorpora personal altamente cualificado y la intercambiabilidad de sus componentes.