Sistemes de mesura integrats en màquina per a processos de rectificat
Aquests senyals s'utilitzen per canviar els avenços del procés de rectificat i determinar quan la peça a assolit la dimensió programada interrompent l'avanç de la mola i finalitzant el procés de rectificat. A aquest tipus de mesura l'anomenarem en-procés.
Una vegada finalitzat el procés de producció, en funció dels procediments de qualitat existents, les peces produïdes es mesuren en equips de mesura externs per verificar que aquestes compleixen els requeriments de precisió exigits. Els paràmetres que se solen verificar són la rodonesa, cilindricitat, con, rugositat, etc. Aquests equips de mesura emeten determinats informes dels mesuraments realitzats. A aquest tipus de mesura l'anomenarem post-procés.
Els fabricants de CNC s actuals estan apostant cada vegada més pels anomenats controls oberts, els quals bàsicament aprofiten l'arquitectura PC per permetre a l'usuari implementar funcions pròpies, posant al seu abast molts recursos interns del control. Aquest tipus d'arquitectura de CNC s possibilita el desenvolupament de sistemes de mesura integrats amb el propi CNC que permeten incloure en la màquina la funcionalitat de mesurament en-procés i post-procés sense haver de recórrer a equips externs.
A més hi ha certs processos de rectificat la mesura no pot ser satisfeta amb la utilització d'equips comercials i per tant requereixen del desenvolupament de solucions específiques al mesurament. En aquest article es presentaran 2 desenvolupaments de mesuradors per a processos de rectificat que utilitzaran l'arquitectura dels controls oberts per a la seva implementació, concretament un mesurador multidiàmetre i un mesurador de puntes de àleps per procés de rectificat d'alta velocitat. Inicialment es presenten les bases per a la integració de sistemes de mesurament en les màquines.
La integració de funcions per a mesurament post-proces a la màquina fa que aquesta també es converteixi en una màquina de mesurament i, per tant, a més de les funcions de mecanitzat pròpiament dites, ha de suportar les funcions de mesura com ara emmagatzematge de resultats, generació d'informes i impressions, etc. És fonamental dotar aquests sistemes dels sistemes de calibratge que permetin una traçabilitat dels mesuraments d'acord amb els estàndards nacionals i internacionals.
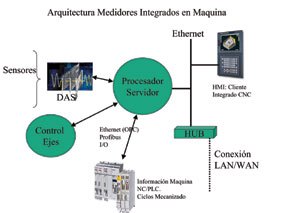
Arquitectura d'un sistema de mesurament integrat
- Sensors: Són els encarregats de convertir la magnitud física, en el nostre cas una dimensió, una magnitud elèctrica. En el cas del rectificat la tècnica més utilitzada és la del mesurament dimensional per contacte (LVDT, encoder lineal), principalment per la seva immunitat al operació amb refrigerant. El mesurament per contacte presenta limitacions per a l'operació a alta velocitat, per la qual cosa se solen s'utilitzen sensors sense contacte (fibra òptica, triangulació làser, corrents induïts, capacitius, etc.).
La interfície més habitual dels sensors és la disposició d'un senyal analògic proporcional a la magnitud a mesurar. En alguns casos també es disposen de senyals compatibles amb encoders (TTL, 1Vpp, etc.).
- DAS: (Data Acquisition System). És un sistema que permet adquirir (digitalitzar) la informació provinent d'un o més sensors. Els requeriments del sistema d'adquisició de dades varien en funció del tipus de sensor utilitzat i la resposta en freqüència necessària.
- Control Eixos Posicionament: Els sensors han de ser posicionats en els punts apropiats que els permetin capturar la informació requerida. El mesurador ha de ser capaç de comandar els eixos de posicionament dels sensors. Els requeriments de precisió d'aquests eixos són alts i se solen utilitzar sistemes de mesurament de molta precisió (<0,1 micres). El control de posicionament d'aquests eixos es pot integrar en el processador del mesurador o bé es pot comandar des del CNC de la màquina.
- Processador: és la unitat encarregada de recollir i analitzar la informació dels diferents sensors i del seu processament. Així mateix ha de ser capaç d'actuar sobre els processos mecanitzat. Per això és necessari que aquest processador disposi de canals de comunicació amb el controlador de la màquina. Aquests canals també són necessaris com a canals d'entrada d'informació, ja que el processador no només ha d'avaluar la informació provinent dels sensors, sinó que necessita informació del procés de mecanitzat que aquesta continguda en el CNC / PLC, com per exemple paràmetres del procés (rpm, avenços, posicions dels eixos, etc.), sol ‡ licituds d'operacions de mesura, etc.
En funció del grau de processament requerit es pot optar per integrar el processament en el processador de la màquina (CNC obert) o bé optar per un processador independent amb comunicació amb el CNC / PLC si es requereix molta capacitat de càlcul i processament.
Canals de Comunicació (interface) amb la màquina (CNC / PLC).
Els interfícies de comunicació més utilitzats amb la màquina són els següents:
- Entrades / Sortides digitals: Són els més senzills. Un conjunt de senyals digitals permeten intercanviar informació amb altres dispositius. Són els més utilitzats en els mesuradors comercials, però limiten enormement la quantitat d'informació a intercanviar.
- Busos de camp. La connexió del mesurador al bus de camp del CNC / PLC és una possibilitat d'intercanviar informació entre el mesurador i el controlador de la màquina. PROFIBUS és la més opció més aconsellable en aquest tipus de comunicació ja que aquesta suportada per 2 grans fabricants de CNC'S Siemens i Fanuc. Mitjançant aquest tipus de bus s'accedeix a la informació del PLC pel que en cas de requerir informació continguda en el CNC cal passar aquesta informació al arrea del PLC.
- Ethernet. Cada vegada és més habitual que els CNC disposi d'aquest tipus d'interfícies per a intercanvi d'informació amb el CNC / PLC. Tant Temples com Fanuc disposen d'aquesta possibilitat, i el desenvolupament de llibreries de comunicació permet l'intercanvi d'informació amb la màquina. Utilitzant aquest tipus de comunicació és possible accedir a pràcticament tota la informació continguda en el controlador de la màquina (CNC / PLC). OPC (Ole Process Control) és una tècnica de programació que s'està imposant com intercanvi d'informació amb el CNC / PLC.
- En el cas dels mesuradors experimentats s'ha optat per una combinació de Ethernet i I / O cablejats. Les I / O cablejades s'utilitzen causa de requeriment de rapidesa de comunicació i seguretat cablejada.
- HMI (Human Machine Interface): L'entorn de maneig i programació ha d'estar integrat en el CNC. Per això la solució adoptada ha estat la de programari distribuït. Una arquitectura Servidor-Client possibilita que el client (HMI) demani qualsevol tipus d'informació i comandaments al servidor (Processador). Aquestes aplicacions Servidor-Client poden funcionar en un únic processador (PC) o en processadors independent. Una connexió en xarxa local entre servidor i client facilita l'intercanvi d'informació. Aquest tipus d'arquitectura facilita que els clients es puguin executar en qualsevol PC connectat en xarxa al servidor.
- Integració Xarxes del client: Mitjançant una connexió Ethernet permet integrar el mesurador en una xarxa local (Lan Area Network) o xarxa d'àrea extensa (Word Area Network). Aquest tipus de connexió facilita que els resultats dels mesuraments puguin ser emmagatzemats i avaluades en dispositius (PC) connectats a la xarxa. La integració en una xarxa d'àrea extensa (WAN) és important de cara al manteniment remot facilitant el teleservei.
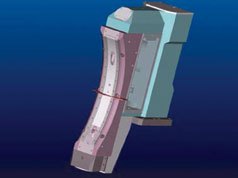
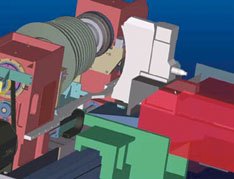
Mesurador de puntes de àleps
Les rectificadores d'alta velocitat són el mètod'utilitzat actualment i realitzen aquest procés a velocitats properes a la d'operació del motor, realitzant el mesurament dels àleps en unes condicions similars a les de vol (fins a 6000 RPM). Aquest és un factor molt important, ja que els àleps no estan fixos i per tant la força centrípeta originada durant la rotació del compressor a alta velocitat origina que aquests estan en condicions similars a les d'operació.
És obvi que els mesuradors comercials que utilitzen les tècniques de mesura per contacte no són apropiats per al treball amb peces discontínues a alta velocitat. Per això s'ha desenvolupat un sensor al qual anomenarem TOD (Transductor Òptic Desplaçament) per a aquest tipus de mesura i s'ha desenvolupat un mesurador integrat a la rectificadora seguint l'arquitectura descrita anteriorment.
El sistema dissenyat disposa de l'arquitectura que es mostra a la figura 3.2.
- Un cap de mesurament o sensor que conté un TOD (transductor òptic de desplaçament) de fabricació pròpia.
- Un / dos eixos que posicionen el cap de mesurament en el punt de mesurament.
- Un encoder incremental per llegir la posició angular del rotor durant el rectificat i així sincronitzar el mesurament de cada lloi.
- Un processador per a l'adquisició i tractaments dels senyals generades pel cap de mesurament. Aquest sistema proporciona tot el interfície necessari amb els controladors del procés de rectificat.
Com es mostra a la figura el DONEN-BTM es munta a la rectificadora, en oposició a la mola. A mesura que el procés de rectificat genera una variació en la dimensió dels àleps, el sistema de mesurament proporciona en temps real la mesura dels àleps i interactua amb el controlador de la rectificadora.
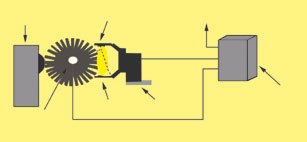
Usant aquest transductor òptic de desplaçament, el model DAN-BTM determina el radi del àleps del compressor mesurant l'arc del ins mentre gira. Com es mostra a la figura 3.3, es posa una font de llum colimada (díod'infrarojos) en un costat, posant un transductor òptic (càmera) en el costat oposat. Una lent i un sistema de miralls capten la imatge de la punta de l'lloança i la projecten sobre el fotocàtode del convertidor d'imatge o tub fotomultiplicador que és un transductor molt ràpid amb amples de banda de 1MHz. Mentre el lloat trencada a través de la font de llum, es generés un flanc negre / blanc (o ombra) al transductor. Mesurant la màxima longitud del flanc, representada pel pic de l'arc del àleps, es determina el radi. El TOD mesura el radi de cada un dels àleps, generant un senyal analògic proporcional al desplaçament de la vora o radi del lloança (veure figura 3.4).
El senyal analògic és analitzada per un sistema d'adquisició de dades, i mitjançant un processament d'aquest senyal en combinació amb la posició angular del rotor determinada amb un encoder es calcula el radi de cada àleps.
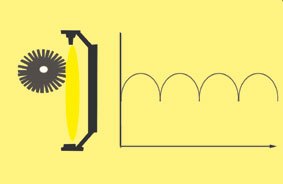
Sistema mesurament. Programari adquisició i anàlisi
El mesurador disposa de tractament de senyal optimitzat, amb implementació de filtres per a eliminació de sorolls elèctrics, anàlisi d'1 o diverses voltes amb càlculs de la mitjana o mitjana de cada ins i corbes de linealització dels senyals. Els sistemes comercials precedents únicament processen el senyal d'una volta. La gran capacitat de càlcul que disposa amb un PC dedicat al mesurament permet processar informació de diverses voltes, mitjana resultats de cada un dels àleps i eliminant les mesures errònies. Les proves realitzades utilitzant aquest algorisme produïts millors resultats de repetibilitat sent més immune a interferències elèctriques en el senyal a mesurar. S'han aconseguit repetibilitat de <0,003 mm enfront de les 0,016 mm obtingudes sense l'aplicació dels algorismes optimitzats.
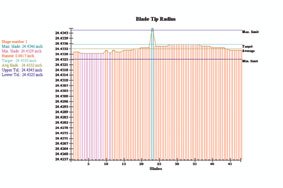
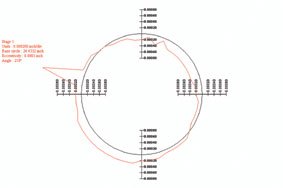
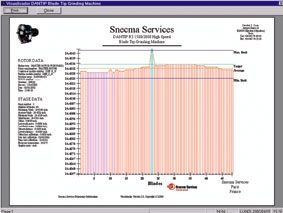
Mesurador multidiàmetre
Es tracta d'un Mesurador Absolut que permeti la mesura en procés integrat amb el CNC de la màquina. També es disposa de la possibilitat de realitzar mesuraments Post-Procés de rodonesa, cilindre, con i perfil, així com disposar de programari d'anàlisi de les mesures realitzades.
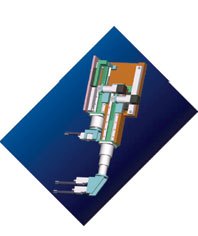
Els mesuradors comercials disposen de rangs de mesura limitats i no permeten mesurador diàmetres grans. Amb aquest tipus de mesurador es pot mesurar qualsevol diàmetre entre 5-30 mm, i es poden programar el mesurament de múltiples diàmetres en la mateixa peça.
La figura mostra el tipus de mesurador. Dos braços motoritzats i controlats numèricament pel mesurador, posicionen uns palpadors de contacte a la zona de mesurament. Depenent del diàmetre a mesurar el sistema de mesura calcula la posició dels braços, i processa la informació dels palpadors per obtenir les dimensions de la peça.
La integració amb el CNC permet al sistema de mesura conèixer en tot moment la posició de gir de la peça i la posició de la taula, obtenint les formes i perfils de les peces.
La resolució del sistema és <0,1 micres i la precisió de ± 2μm en tot el rang de mesura.
El maneig de mesurador, la programació dels cicles de mesurament, presentació d'informes de mesura està totalment integrada amb el CNC de la màquina.
També es faciliten la impressió d'informes, així con la connexió en xarxes LAN, WAN per a l'emmagatzematge de mesures o anàlisi de les mesures en altres PC connectats amb el CNC.
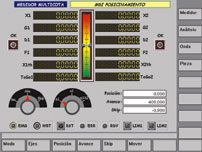
Conclusions
El desenvolupament de sistemes de mesura integrats en les màquines comporta el domini de certes tecnologies com són:
- Coneixement de la màquina i els processos de mecanitzat.
- El coneixement dels sensors i la seva aplicació. En la majoria dels casos es poden aplicar sensors comercials, realitzant la tasca de l'enginyeria de mesurament o processament dels senyals subministrades pels sensors i altres casos més complexos es requereix el disseny del propi sensor.
- Coneixement de processament de senyal.
- En coneixement de l'arquitectura dels CNC oberts i les tècniques de programació.
- Comunicacions industrials.
Els fabricants de les màquines més del domini tècnic en aquestes àrees, han d'avaluar el cost del desenvolupament de sistemes de mesurament propietaris integrats en el CNC, davant la utilització de sistemes comercials. Un cop realitzat el projecte el cost unitari es redueix amb el que hi ha més possibilitats d'incorporar noves prestacions en les màquines amb un menor increment de costos. El nombre d'unitats a produir per amortitzar el desenvolupament del producte és fonamental a l'hora de prendre decisions d'implementació.

D'altra banda l'arquitectura servidor / clients i les interfícies de comunicació d'alta velocitat desenvolupats permeten la total integració amb el controlador del procés de rectificat, fins i tot amb la possibilitat que tots dos sistemes funcionin en el mateix processador. Això permet un intercanvi d'informació en temps real entre procés de mecanitzat i mesurador, podent adaptar el procés en funció de la informació subministrada pel mesurador. Tot això unit al desenvolupament d'interfícies d'operador amigables i representacions gràfiques en un entorn Windows permeten disposar d'un programari actual i fàcil de manejar, enfront dels sistemes propietaris comercials que cadascú utilitza interfícies diferents.
A més de la verificació dimensional de les peces produïdes, es poden integrar un altre tipus de mesures mitjançant la inclusió de nous sensors, com poden ser:
- Qualitat superficial de la peça.
- Duresa del material.
- Detecció de fissura i esquerdes.
- Caracterització d'eines (moles).
- Desequilibri de mola, tall d'aire (GAP).
Tots aquests mesuraments s'integren en un mateix equip sense necessitat d'incorporar instrumentació i panells d'operador de diferents fabricants d'equips de mesura. Tot això facilita la tasca de l'operari de la màquina disposant d'un únic entorn de maneig en un llenguatge amigable.
L'aplicació de noves tecnologies en la miniaturització de sensors i la utilització de sensors sense fils (wireless) amb autogeneració d'energia (self energised) augmentarà les possibilitats de la integració de mesurament en la màquina. n