Handling parts in white rooms
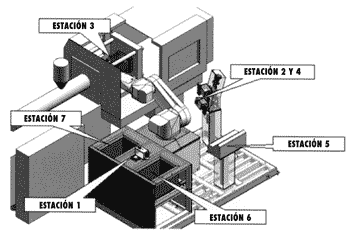
Manufacturing in clean rooms poses a fundamental challenge: when the pieces that will occur are made of plastic and are intended for medical uses, the requirements are much stricter. An example is the fully automated production as described below, which carried out a threefold process: manufacturing of rings of subject of membranes by moulding by injection, quality control and packaging.
The company originator and promoter of the project has been Gemü GmbH (Rotkreuz, Switzerland), while that the production team has been designed and manufactured by GUS Automation AG (formerly Geiger Handling Systems GmbH, see the info box), which has also been the general contractor. This company is specialized in the design of fully automated machines for the production of plastic parts; GUS Automation AG develops projects of very different classes based on their own systems and components, which include: machines for cutting burrs, linear robots, and external supply 6 axis industrial robots. Depending on how they are integrated molding machines by injection or thermoforming and according to the provision of peripheral equipment (material flow), these machines can be operated without interruption. The design of the machine was made difficult by the fact that the rings of subject of membranes should occur, retire and packed in Cleanroom conditions.
Production automated in white room
The plant is equipped with drawers carriers serving as a means of interconnection between the white room of class 6 (machine of molding injection and manipulation of the robot) and the white room of class 7. Thanks to this element, it is not necessary that no one within the clean rooms during production. The production line is so automated that it is only necessary that among staff for scheduled maintenance operations or if there is a bug.
The main element of the unit of production of rings of subject of membranes is the industrial 6 axis robot, which handles all operations, from the handling, distribution and packaging until the transfer of parts to the appropriate boxes. In order to maintain the conditions of white room, was chosen a Stäubli RX130 robot, which is equipped with a multifunctional grip designed and manufactured by GHS Automation System. The rest of the components of the production line are:
• Machine of molding injection Demag Ergotech 80/420, white room version;
• Machine of molding by injection of a single cavity, which can be adjusted to create three different types of rings;
• Support base for the placement of the sliding deposit (for empty metal containers), drawer carrier for the storage of the already packed rings and receiver holder for storage of the leftover elements;
• Station for the filling of containers; and
• Station for closure (soldier) of the packaging.
Multifunctional grip system and 6-axis industrial robot
From here, through the grip the robot vacuum device, the package is transferred to station 2 provision of packaging, where it stands and immobilize via suction cups. To open the container, the robot runs grip device by vacuum: from above, a hopper is inserted into the open bag (season 4). At the same time, through the system of grip, the robot takes a complete ring, along with its trough (season 5) of the injection mould. The robot expels the trough a container located under the mold and passes through the upper part of the hopper with membrane clamping ring.
Once introduced the piece molded metal container, through the grip by vacuum device package is transported to the station soldier (season 5), where the containers are sealed on an ongoing basis. Then the robot carries the container sealed until the storage of finished parts (season 6) receiver and deposits it according to a pattern of provision in pallets.
• The length of the cycle
• The time of injection
• The measurement time
• Elespacio of food
• Mass pad
• The temperature of the mold or
• The specific pressure of injection
They exceed the limits of tolerance, the injection molding machine or the own mold send a signal to the robot at the beginning of the cycle. In these cases, immediately after removing the piece, the robot moves to the drawer of pieces of waste (season 7) and there lays the faulty part. Both finished parts drawer and drawer of pieces of waste can be transported manually; to this end, the modules are displaced persons from the white room class 6 to the sector of cleanroom class 7, you can access authorized personnel and download deposits.
Summary
Due to the weight of the grip system, dynamic movement and various stations to which it should arrive, separated by the corresponding distance, they chose a large robot that could perform all these tasks in a reproducible way. On the other hand, thanks to the high level of functional integration, the production line has been automated with a relatively low number of components. This in turn ensures a high level of availability and stability of process.