Un proceso robusto para el mecanizado en 5 ejes de rotores de álabes integrados de motor aeronáutico
Debido a los requisitos funcionales y técnicos, los rotores de álabes integrados (IBR) de motores aeronáuticos se han convertido en piezas de referencia en la investigación y desarrollo del mecanizado de cinco ejes. A pesar de los avances en el mecanizado en cinco ejes, la fabricación de componentes como ‘blisks’ e ‘impellers’ de manera fiable y eficiente sigue siendo un campo con amplio desarrollo y mejora.
En el presente trabajo se describe una metodología de trabajo fiable para la fabricación de este tipo de turbocomponentes. Para desarrollar y optimizar esta metodología se ha trabajado con diferentes geometrías de discos, materiales y fresas. Se han comparado estrategias de desbaste en cinco ejes, así como diversas técnicas para el acabado de los álabes. Se han realizado simulaciones del mecanizado para visualizar el resultado geométrico de las operaciones y observar las zonas más conflictivas, así como para detectar posibles colisiones incorporando la cinemática de la máquina-herramienta. Por otro lado para complementar estos análisis geométricos convencionales, se han utilizado modelos de fuerzas de corte que permiten analizar los esfuerzos mecánicos. De esta manera se puede evitar flexiones de herramienta y/o vibraciones, que conllevan rechazos de piezas de alto valor añadido. Por último, se han realizado procesos de comprobación, que permiten por un lado verificar la pieza obtenida, y por otro validar y optimizar los cálculos y análisis realizados.
1. Introducción
Actualmente, la fabricación de rotores de álabes integrados (IBR) es todavía un reto tecnológico. Estos componentes de motores aeronáuticos son diseñados con superficies complejas para obtener unas óptimas transformaciones de los parámetros del flujo. El fresado de estas geometrías requiere una gran flexibilidad en la orientación de la herramienta. Mecanizar interpolando en 5 ejes de manera continua permite optimizar la accesibilidad de la fresa en la pieza diseñando trayectorias más ajustadas a la geometría final. Además también se posibilita un aumento del ratio de volumen de material mecanizado por herramienta, la reducción de tiempos de ciclo y el uso de herramientas más cortas.
Por otro lado, hay que tener en cuenta que las propiedades mecánicas de estos turbocomponentes se han de mantener a altas temperaturas, presiones y ambientes corrosivos. Por lo tanto, la alta resistencia en estos materiales, no se ve afectada prácticamente por el aumento de las temperaturas durante el mecanizado. A esto hay que añadir que los materiales habitualmente utilizados, como son las aleaciones de Titanio o las aleaciones base de Níquel son materiales de poca conductividad térmica. Esto significa que las altas temperaturas generadas durante el mecanizado no se disipan rápidamente a la pieza, sino que se concentran en la zona de corte. Esta combinación de alta temperatura en la herramienta y altas fuerzas de corte, da lugar a una baja maquinabilidad. La demanda actual en el sector aeronáutico se centra en el diseño de aleaciones avanzadas que mejoren las propiedades mecánicas a mayores temperaturas, debido a la necesidad de aumentar el ciclo de vida de los componentes y de incrementar las temperaturas en el proceso del motor para llegar a cumplir las regulaciones internacionales de control de emisiones [1].
Todo esto implica que el proceso de creación de operaciones de mecanizado conlleve complejos cálculos y se hagan necesarios diferentes análisis y simulaciones del proceso. En el presente trabajo se propone una metodología de trabajo optimizada para la fabricación fiable de piezas integrales de turbinas mediante mecanizado. Se recogen los avances realizados por la UPV/EHU junto con las empresas Novalti e ITP. En la figura 1 se puede observar de manera global las etapas de las que consta el proceso.
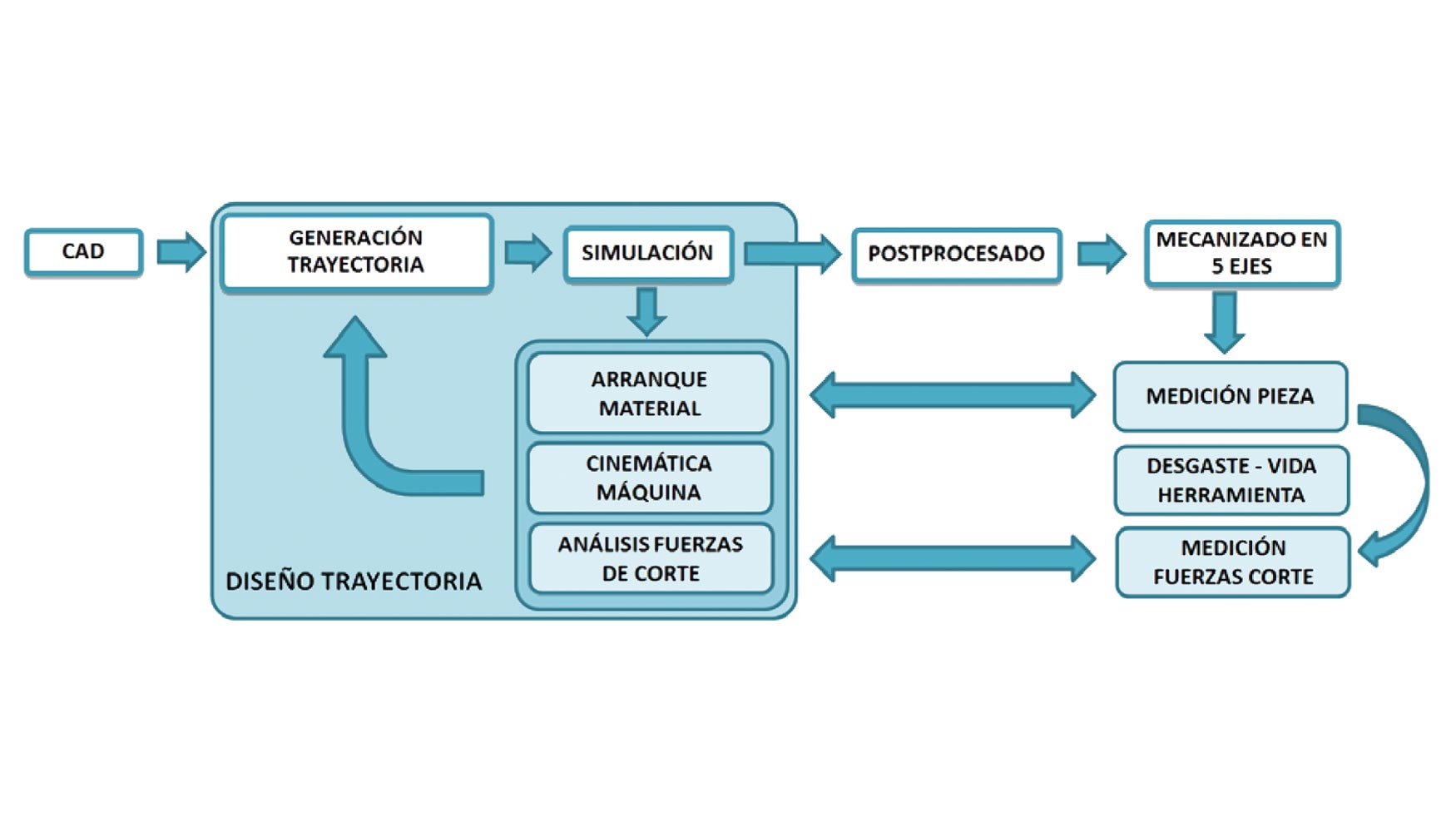
Para la fabricación de álabes integrales de rotores, como los ‘impellers’ o ‘blisks’, se parte de una preforma de revolución. En esta preforma se realizan las operaciones de desbaste, semiacabado y acabado mediante operaciones de fresado hasta obtener la pieza final.
2. Diseño de trayectoria
Estas operaciones de mecanizado se diseñan en un proceso cíclico que se divide en dos subprocesos. Por un lado se ha de generar la trayectoria de la operación configurada por el usuario. Por otro lado la trayectoria requiere ser simulada y analizada para verificar su idoneidad y optimizarla. La generación de trayectorias de fresado en 5 ejes de superficies libres es un campo de investigación de amplio desarrollo en los últimos años, y que abarca múltiples líneas debido al gran número de factores que toman parte en el proceso. En concreto, el mayor número de investigaciones se centra principalmente en la creación de algoritmos para la generación de la trayectoria y el posicionamiento de la herramienta con una orientación óptima libre de colisiones [2-4].
Hay que tener en cuenta que estos cálculos están relacionados entre ellos, de tal manera que la solución al problema de cálculo global de la trayectoria se dividiría en la siguientes etapas: una vez seleccionada la fresa, se seleccionan el patrón y la dirección de la trayectoria, se especifican los puntos de contacto en la superficie y por último se verifican las interferencias locales y globales para obtener la orientación de la herramienta. Los algoritmos desarrollados se han de adaptar a diferentes tipos de superficies y han de ser eficientes respecto al uso de memoria. Un aspecto importante del proceso de diseño de trayectorias es la estrategia o técnica de mecanizado que se va a utilizar en las operaciones de desbaste y acabado.
2.1. Estrategias de desbaste
Entre las estrategias utilizadas para realizar el desbaste se puede destacar el ranurado (‘slot milling’), el fresado trocoidal y el fresado en penetración (‘plunge milling’, ‘dive milling’) (ver figura 2). El ranurado es una estrategia donde la profundidad radial es igual al diámetro de la herramienta. Se utiliza como estrategia inicial de corte con los patrones habituales de trayectorias tipo zig o zig-zag. En estos casos se toma como referencia las intersecciones con la geometría a determinados niveles para generar las trayectorias curvas entre los álabes. Lo habitual es que estos niveles sean superficies paralelas a una de las superficies de revolución de la pieza o una interpolación entre ambas. La superficie de revolución interior se denomina ‘hub’ y la exterior ‘shroud’. A pesar de la alta tasa de arranque de viruta de esta estrategia, se generan altas fuerzas de corte radial. Para reducir los esfuerzos sobre la fresa se puede dividir el ranurado de un nivel en varias pasadas.
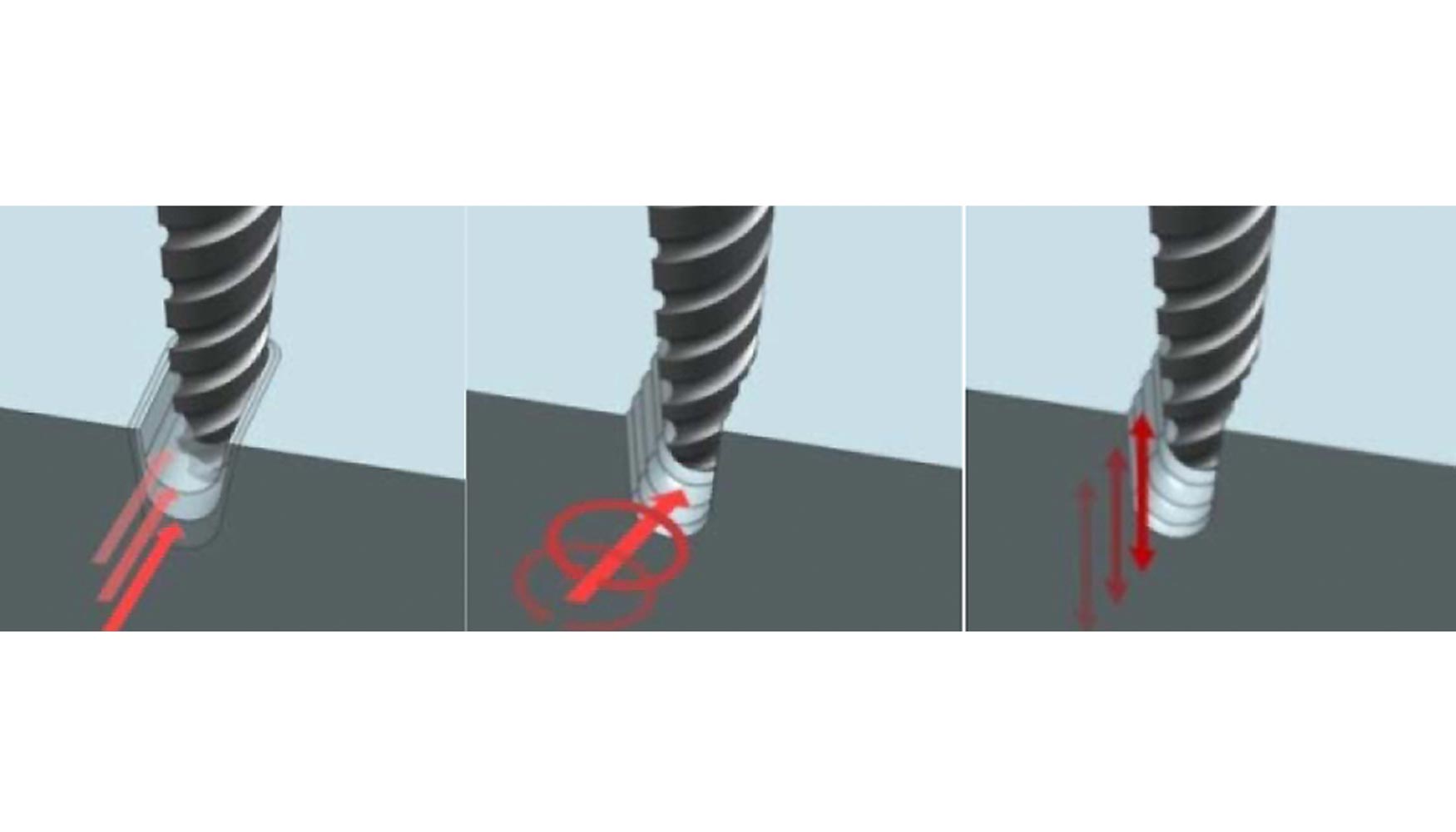
El fresado trocoidal consiste en la combinación del movimiento de avance de la herramienta con el de trayectorias circulares. La principal ventajas respecto al ‘slot milling’ es la generación de menores fuerzas de corte radiales, pudiéndose utilizar velocidades de corte y profundidades de corte axial superiores. Por contra, el diseño y generación de trayectorias trocoidales en cinco ejes adaptándose a la geometría de la pieza requiere un mayor coste. Además, exige mayores capacidades dinámicas de la máquina-herramienta.
En el fresado en penetración o ‘plunge milling’ el mecanizado se realiza con el filo secundario de la fresa, en vez de realizarse con el filo principal. En esta estrategia las fuerzas de corte predominantes son en dirección axial. En general, el ‘plunge milling’ es un método alternativo cuando no se puede utilizar fresado lateral debido a la vibración. Por ejemplo, si el voladizo de herramienta es elevado, en caso de ranurado profundo o en general si la estabilidad es deficiente.
Con el objetivo de conseguir estrategias adecuadas para el mecanizado de ‘blisks’ e ‘impellers’, se han diseñado diferentes tipos de trayectorias utilizando el software de CAD/CAM comercial NXTM de Siemens. Se han optimizado las orientaciones de la herramienta para obtener en la geometría generada una demasía de material lo más homogénea posible a la pieza final. De esta manera se ha conseguido que en las operaciones de semiacabado los esfuerzos sean más regulares. Cumpliendo este requisito se han restringido las orientaciones de herramienta a valores de ‘lead’ y ‘tilt angle’ para un corte favorable. En la figura 3 se puede observar una trayectoria optimizada para la primera etapa de desbaste en el mecanizado de un ‘impeller’ de Ti6Al4V y el mecanizado posterior. Se ha utilizado un patrón de corte zig-zag, donde se ha realizado un primer ranurado entre álabe y ‘splitter’ para ir abriéndose en concordancia hacia éstos. Se ha dividido el ranurado inicial en tres pasadas, hasta llegar a la profundidad axial de la pasada. Se han utilizado una profundidad axial ap de 10 mm (profundidad en el ‘leading edge’) y una radial ae del 30% del diámetro de la herramienta. Para esta operación se ha elegido una herramienta tórica de metal duro de diámetro 10 mm, radio en la punta de 2,5 mm, longitud de filo 22 mm, ángulo de hélice de 45º, cuatro filos y refrigeración interna.
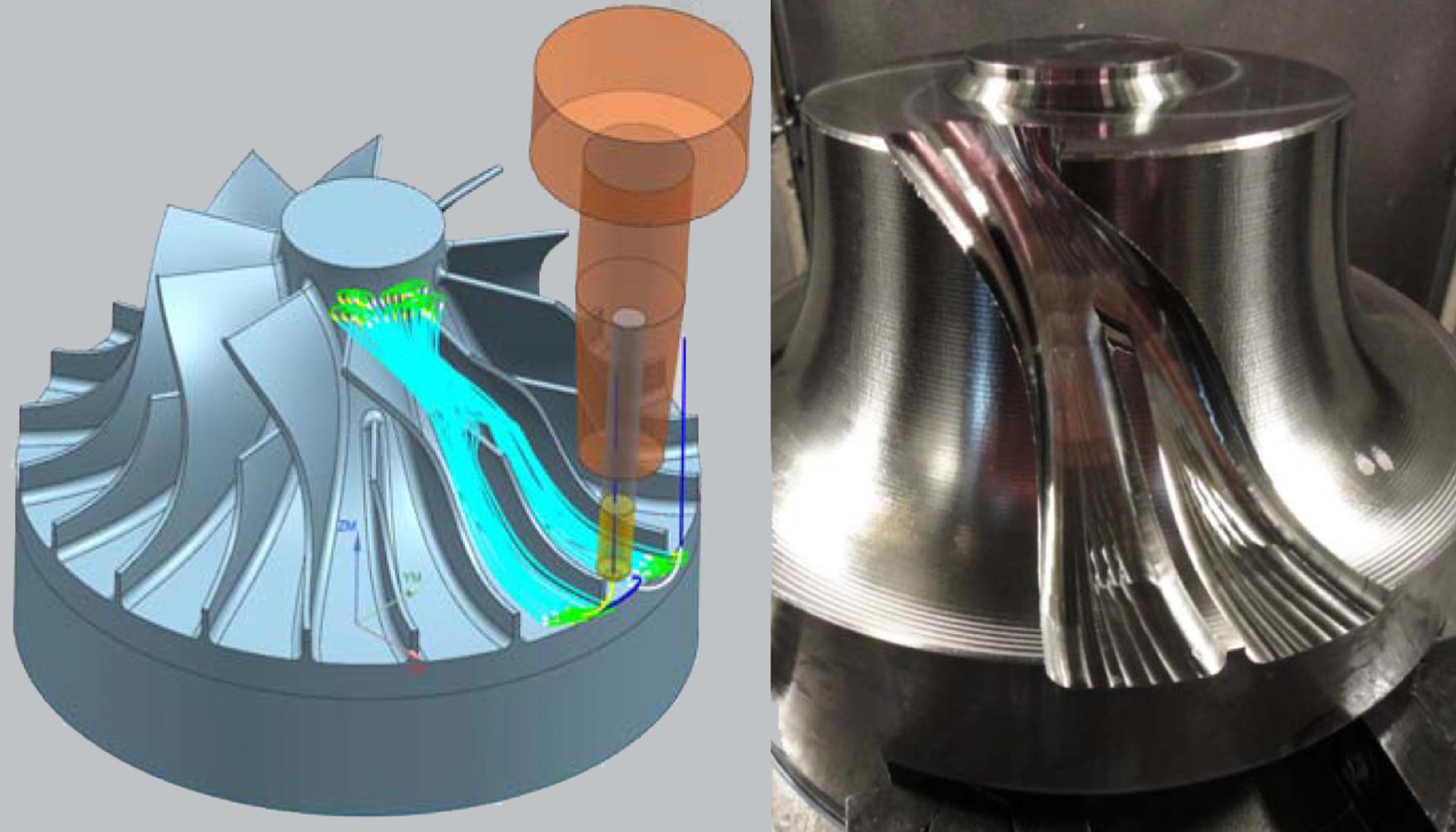
2.2. Estrategias de acabado
Una vez realizado el desbaste entre álabes se realizan las operaciones de semiacabado y acabado de los álabes y el hub. También puede ser necesario repasar los radios de acuerdo u otras zonas de la pieza donde hayan quedado demasías de material. Cabe destacar la importancia de la técnica de fresado utilizada en el acabado. Las técnicas de fresado se diferencian en función de la parte de la herramienta que realiza el contacto con la pieza durante el mecanizado. En operaciones de acabado de superficies complejas podemos destacar las técnicas de ‘point milling’ y ‘flank milling’. En el ‘point milling’ el contacto durante el arranque de viruta se realiza en un área cercana a un punto. En el ‘flank milling’ el arranque de material se realiza a lo largo de una arista del contorno de la herramienta. En la figura 4 se pueden observar los contactos en operaciones de ‘point milling’ y ‘flank milling’, en color rojo y azul respectivamente, para diferentes geometrías de fresa. Se han representado una fresa de punta esférica, una frontal, una cónica y una de barril. Las fresas cónicas con grandes longitudes de filo de corte son ampliamente utilizadas para el acabado de álabes reglados mediante mecanizado con el flanco. Permiten una gran flexibilidad en la accesibilidad desde diferentes ángulos, además de ganar rigidez respecto a fresas cilíndricas de mismo diámetro de bola (figura 4). En lo que respecta al ‘point milling’ en las fresa de barril el radio en el contacto, y por lo tanto el volumen de viruta que se arranca, es mayor que en una fresa esférica de diámetro de mango similar. Es decir utilizando una fresa de barril podemos reducir considerablemente el tiempo de mecanizado en el acabado del álabe.

El 'flank milling' es una estrategia enfocada a operaciones de semiacabado y acabado, en superficies de álabes generadas por la revolución de una línea alrededor de un eje (‘single-curved surface’) o generadas por el barrido de una línea (isoparamétrica) a través de dos curvas guía (superficie reglada o ‘ruled surface’). Diversas referencias y datos experimentales muestran que la estrategia de ‘flank milling’ disminuye el tiempo de mecanizado y mejora la calidad superficial respecto al ‘point milling’ [5]. Por otro lado, a mayor contacto entre pieza y herramienta, se requieren mayor potencia, estabilidad, evacuación de viruta y capacidad de movimiento de la máquina, por lo que la operación de ‘flank milling’ puede quedar limitada por estos aspectos. Sin embargo el desarrollo de trayectorias óptimas para el uso del ‘flank milling’ sigue siendo el objetivo de diferentes investigaciones. Se trata de un problema de alta complejidad, ya que no toda superficie reglada es posible mecanizarla de manera perfecta [6,7]. Esto se debe a que se distinguen dos tipos de superficies regladas, las desarrollables, en las que el plano tangente a la superficie es el mismo en todos los puntos de una misma isoparamétrica, y las no desarrollables en caso contrario. En el caso de las superficies no desarrollables, cuanto mayor es el ángulo entre el plano tangente en los dos extremos de la isoparamétrica y mayores son los diámetros de herramienta utilizados, mayor es el error de interferencia con la pieza cometido, siendo geométricamente imposible mecanizar de forma perfecta la superficie. Por lo tanto, aunque con el fresado en ‘point milling’ se necesitan tiempos de mecanizado superiores para acabar un álabe, no tiene las limitaciones respecto a la geometría del alabe que tiene la operación de ‘flank milling’. Además las fuerzas de corte generadas son inferiores, un aspecto importante a considerar con materiales de baja maquinabilidad. Al igual que con las operaciones de desbaste se han diseñado diferentes operaciones de acabado en ‘point’ y ‘flank milling’. En la figura 5 se muestran dos trayectorias de acabado de un ‘impeller’ de Ti6Al4V. La primera trayectoria se trata de una operación de acabado de un splitter mediante ‘flank milling’. Se ha utilizado una fresa cónica de metal duro de radio de bola 3 mm, ángulo de conicidad 4º, 6 filos y recubrimiento de TiAlN. Se ha terminado el álabe con dos pasadas de profundidad radial ae de 0,15 mm y una profundidad axial ap máxima de 30 mm en el ‘leading edge’ del ‘splitter’. En la segunda trayectoria se puede ver una operación de acabado de un alabe del mismo ‘impeller’ mediante ‘point milling’. Las trayectorias se han generado en niveles paralelos al hub con el objetivo de minimizar tiempo de mecanizado. Se ha utilizado la misma fresa que la operación anterior, con unas profundidades radial y axial de 0,3 y 0,5 mm respectivamente. En la figura 5 también se puede ver el splitter mecanizado con la operación de ‘flank milling’.
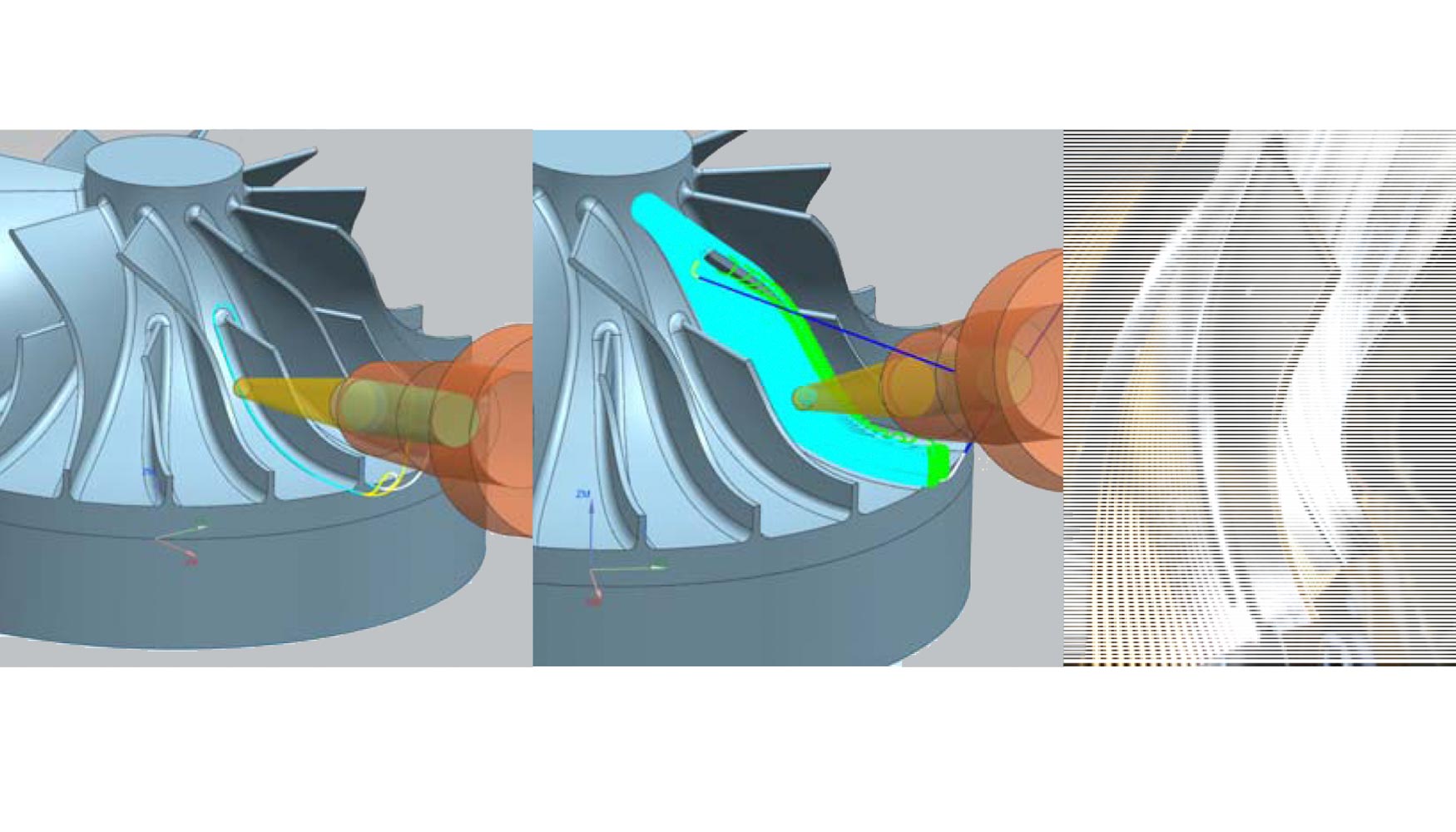
3. Simulación de trayectoria
La trayectoria generada debe ser verificada mediante un proceso de simulación. Un primer paso para comprobar si se requiere cambiar algún parámetro en la configuración de la operación es la simulación de arranque de material. Esta función incorporada en los softwares CAM, permite visualizar en un entorno CAD 3D el movimiento de la herramienta a lo largo de la trayectoria y cual va siendo el material arrancado. Una opción muy útil de cara a comprobar la calidad de la operación generada es el análisis de demasías de material respecto del sólido objetivo final (ver figura 6). Este análisis permite visualizar mediante una escala de colores el material sobrante teórico tras realizar la simulación de una operación. Por lo tanto, tras simular la última operación de acabado, se pueden observar las zonas más conflictivas en las que queda sobrespesor o en las que se ha mecanizado más de lo deseado. Un aspecto clave en la comprobación de trayectorias de mecanizado es la detección de posibles colisiones antes de ejecutar las operaciones en máquina. Los softwares de CAM incluyen la posibilidad de detectar colisiones locales entre pieza, herramienta y portaherramientas y evitarlas durante la generación de trayectoria. Sin embargo en operaciones de mecanizado en 5 ejes esto no es suficiente, y es necesario realizar una simulación cinemática con la máquina herramienta para detectar colisiones globales. En el mercado se puede encontrar software específico para realizar este análisis, y algunos softwares de CAM también incluyen la posibilidad de simular el mecanizado con el ensamblaje completo de la máquina. En la figura 6 se puede observar una colisión detectada entre el portaherramientas y la pieza durante una operación de mecanizado de un ‘impeller’. La simulación se ha realizado en el software de CAD/CAM NXTM. Para ello se ha dibujado el modelo 3D de los componentes de la máquina y los utillajes, y se han definido las dimensiones de las diferentes herramientas y portaherramientas. Posteriormente se han configurado los grados de libertad y los límites de movimiento del ensamblaje de la máquina. Tras realizar estos pasos se ha podido realizar la simulación del movimiento que siguen todos los componentes a lo largo de las diferentes operaciones de mecanizado, detectando las posibles colisiones. Con este proceso se puede comprobar si es necesario rediseñar la operación o utilizar algún componente de diferentes dimensiones para evitar una colisión.
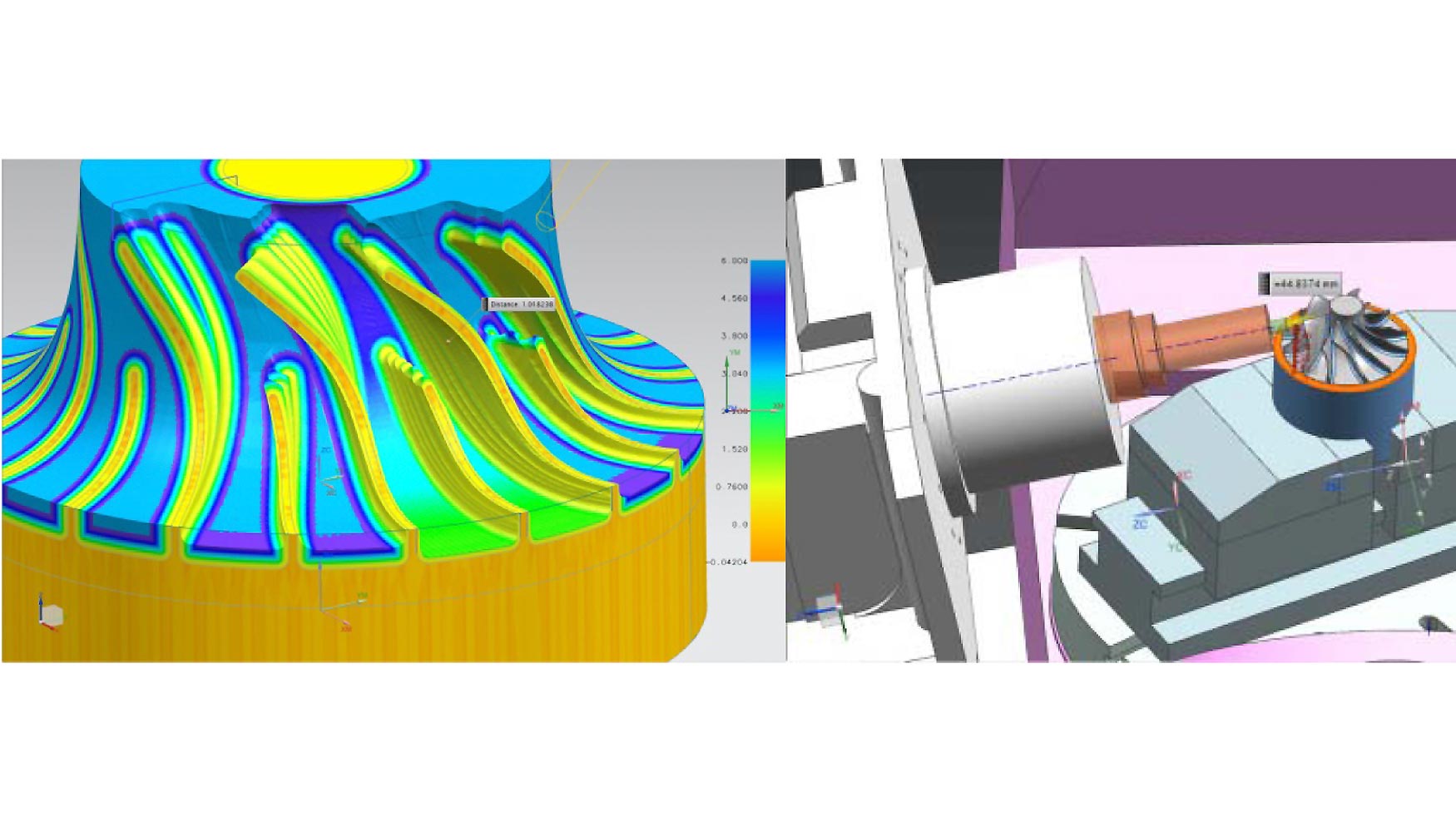
4. Análisis de fuerzas de corte
Sin embargo, a pesar de que estos análisis geométricos y volumétricos son de gran ayuda, los softwares CAM comerciales más habituales no permiten apoyarse en análisis mecánicos del proceso para poder valorar las operaciones enumeradas. Al no tener en cuenta los esfuerzos mecánicos que se están produciendo en el proceso de mecanizado, pueden obtenerse trayectorias que siendo correctas desde un punto de vista geométrico, den lugar a altas fuerzas de corte y vibraciones, y por tanto mala calidad de acabado superficial, altos desgastes en la herramienta e incluso daños en la máquina. El estudio de las fuerzas de corte y el modelado de estas es una de las áreas más clásicas de la literatura científica asociada al mecanizado. Se han desarrollado diferentes modelos de fuerzas que permiten simular el mecanizado en cinco ejes de ‘blisk’ e ‘impellers’ [8-11], con el objetivo de completar mediante un análisis mecánico el diseño de operaciones de fresado. Estos modelos tienen como parámetros de entrada el material, la geometría de la herramienta y de la pieza y los parámetros de mecanizado, como por ejemplo la velocidad de avance y la velocidad de giro de la herramienta. Con estos datos el modelo de fuerzas calcula las fuerzas de corte durante el mecanizado, lo que permite conocer si estas se mantienen dentro del rango deseado.
En el grupo de Fabricación de Alto Rendimiento de la UPV/EHU se ha trabajado en el desarrollo de diferentes modelos de fuerzas con el objetivo de optimizar el diseño de trayectorias. El conocer de antemano las fuerzas que se van a producir durante el mecanizado, toma gran importancia en las operaciones de acabado, donde el margen de error es menor. Por este motivo se ha creado un modelo de fuerzas para herramientas cónicas en operaciones de ‘flank milling’. Este modelo se ha integrado mediante programación interna en el CAM NXTM. De esta manera el usuario puede conocer los valores de las fuerzas de corte una vez generada la trayectoria de ‘flank milling’ sin necesidad de salir del software de CAM. Por otro lado, tal y como se ha comentado anteriormente se puede reducir notablemente el tiempo de mecanizado en operaciones de acabado en ‘point milling’ utilizando fresas de barril. Por este motivo se ha desarrollado un modelo de fuerzas para este tipo de herramientas con el objetivo de analizar trayectorias de mecanizado en 5 ejes de álabes de geometría compleja. Por otro lado se han desarrollado modelos para optimización de las trayectorias de mecanizado en operaciones de desbaste y semiacabado. La mejora de la productividad de estas dos etapas del mecanizado es crucial a la hora de reducir tiempos de fabricación y coste de producción. Los modelos desarrollados están orientados a la mejora de las estrategias de mecanizado, haciendo que el programa de mecanizado sea más eficiente en base a un compromiso entre conservación de la vida de la herramientas y reducción de tiempos de producción.
5. Mecanizado en 5 ejes
Superada la fase de diseño de trayectorias se posprocesan las operaciones para obtener los programas de control numérico a ejecutar en máquina. Para realizar el mecanizado se ha utilizado el centro de mecanizado de cinco ejes Ibarmia ZV25/U600 Extreme. Se han fabricado diferentes geometrías de ‘blisk’ e ‘impeller’, comparándose diferentes trayectorias y tipos de herramientas de cara a optimizar el proceso. En la figura 7 se puede observar el mecanizado del alabe de un ‘impeller’ de Ti6Al4V y el desbaste realizado de un ‘blisk’ de Inconel 718.
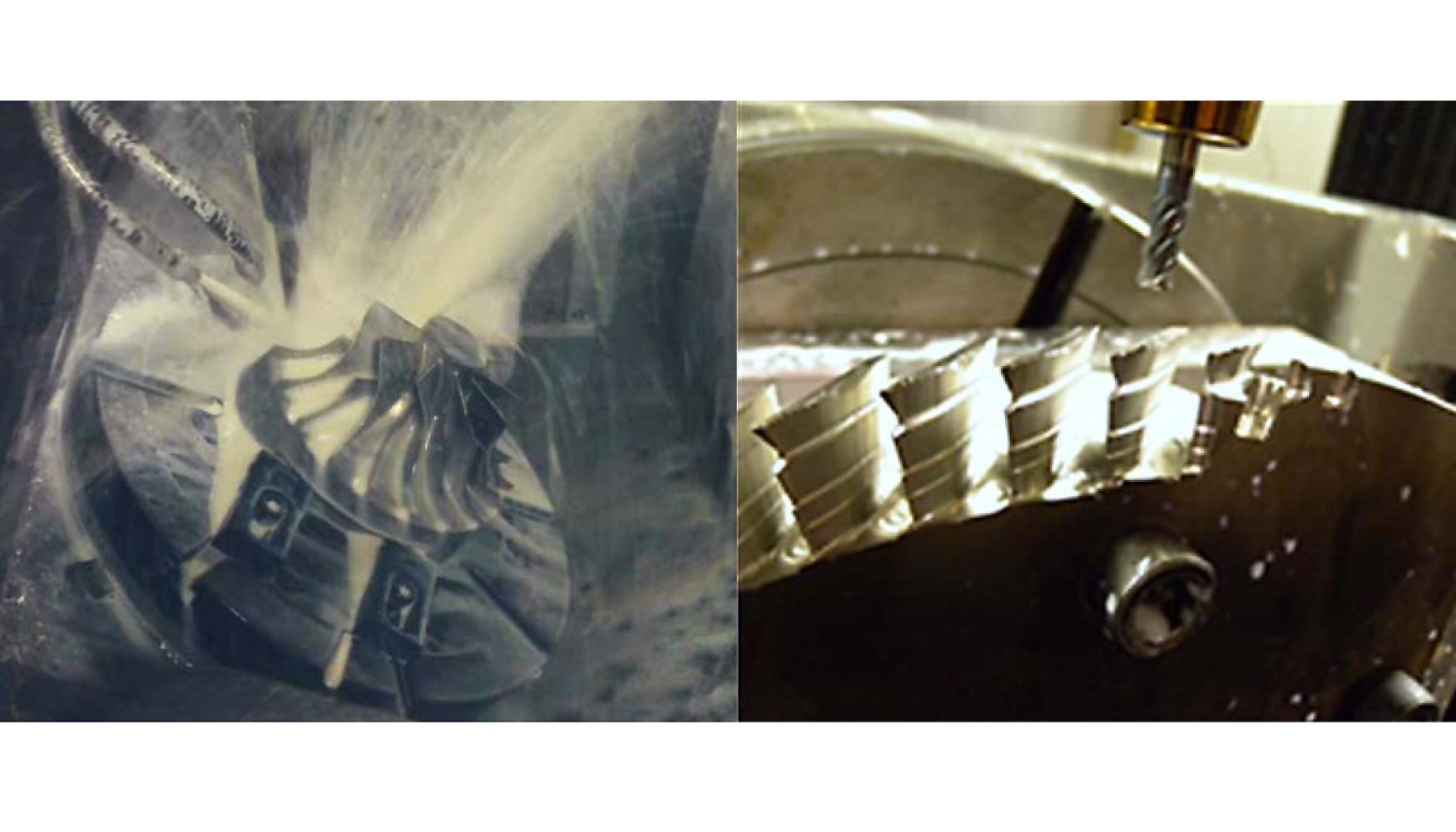
Figura 7. Mecanizados de ‘impeller’ y ‘blisk’.
Durante y después del mecanizado se han llevado a cabo análisis que han permitido verificar la idoneidad del proceso. La medición de las fuerzas generadas durante el mecanizado permite en primer lugar, analizar si las operaciones de mecanizado ejecutadas, generan un rango de fuerzas aceptable y conocer su vinculación a defectos superficiales que hayan podido ocasionar. La captura de fuerzas es una fase necesaria para validar los modelos de fuerza desarrollados. Con este objetivo se ha utilizado una mesa para la medición de fuerzas Kistler 9255B, que permite monitorizar durante el mecanizado y guardar los datos generados para analizarlos posteriormente. Otro parámetro con el que valorar las operaciones de fresado es analizar el ratio de volumen de material mecanizado por herramienta. La medición de los desgates producidos en los filos de las herramientas ha permitido valorar la idoneidad de diferentes trayectorias y comparar diferentes geometrías de herramientas y recubrimientos.
Por último, una vez finalizado el mecanizado de la pieza, la principal verificación del proceso es comprobar si la geometría final entra dentro de las tolerancias especificadas. Con el objetivo de comparar las medidas de la pieza mecanizada y el CAD original de la pieza, se ha utilizado el sistema ATOS Compact Scan 5M de GOM. Se trata de un escáner de luz azul de alta precisión y resolución, cuyo sistema se basa en el efecto de triangulación con dos cámaras capaces de obtener superficies con una gran resolución. En la figura 8 se observa un ‘impeller’ mecanizado en aluminio y la comparación realizada entre la superficie escaneada y la superficie del CAD 3D. Esta medición es de gran utilidad para conocer en qué zonas de la pieza existe exceso de material y en cuales se ha mecanizado en exceso. Por otro lado se ha realizado también la comparación del IPW final con la medición realizada, con el objetivo de conocer la precisión del análisis de arranque e material obtenido. Cabe resaltar que cuando mayores sean las fuerzas de corte y vibraciones en el proceso, más se alejará la superficie real obtenida de la virtual generada por un análisis simplemente geométrico y volumétrico.
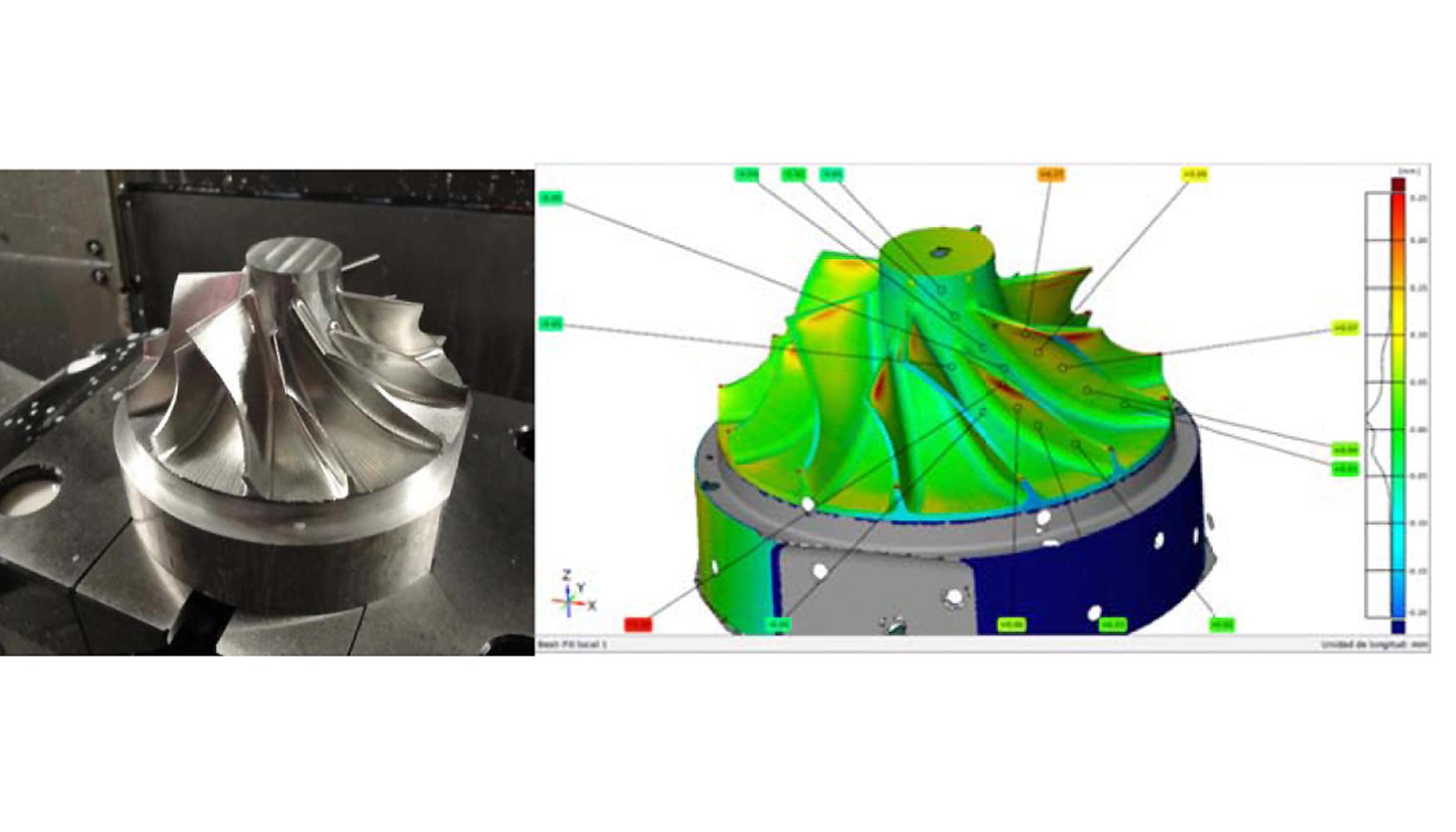
Figura 8. ‘Impeller’ mecanizado y comparación del escaneo con la pieza objetivo.
Conclusiones
Los rotores integrales de turbinas como ‘impeller’ y ‘blisks’ se han convertido en referencia del fresado en 5 ejes. La complejidad y los altos requisitos de estos turbocomponentes hacen necesaria la optimización del proceso de mecanizado. La generación de trayectorias de mecanizado para estas piezas lleva asociados diferentes análisis y simulaciones para su verificación. Por un lado se encuentran análisis puramente geométricos como son la simulación de arranque de material y la simulación cinemática con la máquina-herramienta. El primero permite detectar, entre otros defectos, orientaciones incorrectas de herramienta, sobreespesores y excesos de mecanizado. Por otro lado, la simulación cinemática hace posible detectar colisiones globales en la máquina. Sin embargo, a pesar de que estos análisis son de gran utilidad, es necesario apoyarse en análisis mecánico en un proceso de mecanizado tan exigente. Esto es debido a que altas fuerzas de corte, flexiones de herramienta o vibraciones, conllevan a que la superficie obtenida difiera de la calculada mediante análisis puramente volumétricos. Por este motivo se han desarrollado diferentes modelos de cara a optimizar el diseño de operaciones de mecanizado. Además, durante éste, y con posterioridad, se necesitan ciertas mediciones que permiten, por un lado, la verificación de la pieza y, por tanto, del proceso y, por otro lado, la validación y optimización de las herramientas de generación y análisis de proceso. Podemos destacar la medición de las fuerzas de corte, los desgastes y vida de la herramienta y, por supuesto, la comprobación de la geometría final de la pieza obtenida.
Agradecimientos
Este trabajo se ha realizado gracias a la financiación del Dpto. de Educación, Universidades e Investigación del Gobierno Vasco y del Dpto. de Industria, Comercio y Turismo del Gobierno Vasco mediante el proyecto InProRet del programa Etortek. Los autores también agradecen a la UPV/EHU la financiación recibida bajo el programa UFI 11/29 y las ayudas para personal investigador en cooperación con el entorno productivo y social del programa Zabalduz. Por último se agradece su colaboración a la investigación de las empresas ITP Industria de Turbopropulsores S.A y Novalti S.A..
Referencias
[1] G. Kappmeyer, C. Hubig, M. Hardy, M. Witty, M. Busch. Modern machining of advanced aerospace alloys - enabler for quality and performance, Procedia CIRP 1, (2012), 28-43.
[2] A. Lasemi, D. Xue, P. Gu. Recent development in CNC machining of freeform surfaces: a state-of-the-art review, Computer-Aided Design, 42, (2010), 641–54.
[3] T.D. Tang. Algorithms for collision detection and avoidance for five-axis NC machining: a state of the art review, Computer-Aided Design 51, (2014), 1-17.
[4] M. Rauch, J.Y. Hascoët. Milling tool-paths generation in adequacy with machining equipment capabilities and behavior, Machining of Complex Sculptured Surfaces, Chapter 4, 127-155, Springer-Verlag London Limited, (2012), ISBN 978-1-4471-2356-9.
[5] R.F. Harik, H. Gong, A. Brnard. 5-axis flank milling: A state of the art review, Computer-Aided Design 45(3), (2013), 796-808.
[6] Q. Liang, Y.Z. Wang, H.Y. Fu, Z.Y. Han. Cutting path planning for ruled surface impellers, Chinese Journal of Aeronautics 21, (2008), 462-471.
[7] J. Senatore, F. Moniès, W. Rubio. 5-Axis flank milling of sculptured surfaces, Machining of Complex Sculptured Surfaces, Chapter 2, 33-65, Springer-Verlag London Limited, (2012), ISBN 978-1-4471-2356-9.
[8] W.B. Ferry, Y. Altintas. Virtual five-axis flank milling of jet engine impellers- Part I: mechanics of five-axis flank milling, Journal of Manufacturing Science and Engineering 130, (2008), 011005-1–011005-11.
[9] W.B. Ferry, Y. Altintas. Virtual five-axis flank milling of jet engine impellers Part II: feed rate optimization of five-axis flank milling. Journal of Manufacturing Science and Engineering 130, (2008), 011013-1–011013-13.
[10] Y. Boz, S. E. L. Khavidaki, H. Erdim, I. Lazoglu, high performance 5-axis milling of complex sculptured surfaces, J. P. Davim (ed.), Machining of Complex Sculptured Surfaces, Chapter 3, 67-125, Springer-Verlag London Limited, (2012), ISBN 978-1-4471-2356-9.
[11] A. Calleja, A. Fernández, F.J. Campa, A. Lamikiz, L.N. López de Lacalle, Reliable manufacturing process in turbine blisks and compressors, Manufacturing Engineering Society International Conference, (2013).