Fabricación eficiente de piezas con materiales compuestos
Dicen que la nueva revolución industrial, la tercera, nace de la unión de las nuevas tecnologías de la información conjuntamente con la utilización de nuevas fuentes de energía. En este caso, éstas serían las energías renovables. Si admitimos este planteamiento y lo utilizamos como punto de partida, el respeto al medio ambiente se inserta en el corazón de esta nueva revolución al incorporar el concepto de sostenibilidad en toda su extensión. Dicho respeto no solamente se manifiesta en la producción energética, sino sobre todo, en su consumo responsable en todos los ámbitos, siendo el industrial uno de los más afectados.
La revolución hacia los nuevos conceptos de producto pasa por la utilización de materiales diferentes a los conocidos, con propiedades mejoradas y procesos de producción y transformación también nuevos. Los materiales compuestos son protagonistas en este aspecto, y los sectores que demandan la aplicación de la tecnología con mayor urgencia son los típicamente industriales manufactureros, con muy alta producción e impacto económico en la sociedad y gran repercusión medioambiental, por ejemplo el automóvil y el aeronáutico. Sobre la base de esta tendencia positiva, los analistas prevén una tasa de crecimiento anual compuesto (CAGR) del 17% en la producción de compuestos CFRP (Carbon Fibre Reinforced Plastics) de aquí a 2020, tal y como se ilustra en la Figura 1, produciendo un total de 100.000 toneladas para el año 2017 en el mercado mundial, en el que el mercado europeo por sí solo representa 25.000 toneladas (25% del total).
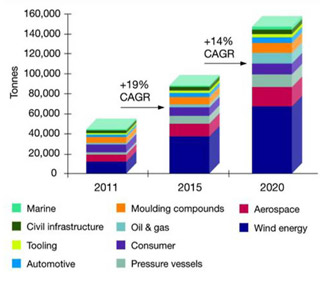
Tabla. Previsión de la demanda de CFRP (Ricardo analysis, Composite World, 2012).
La evolución de los procesos de fabricación y transformación de materiales compuestos tiene el punto de mira en la productividad económica de las instalaciones y en la resolución de problemas dentro del propio proceso. En esta investigación se sitúa la iniciativa sobre nuevas tecnologías para la fabricación eficiente de componentes con materiales compuestos, organizada en el proyecto Reform (Ressource-Efficient Factory Of Recyclable Manufacturing composite components).
Reform es un proyecto comenzado en 2011 con una duración de cuatro años y financiado por el 7º Programa Marco de la Comisión Europea (Grant agreement Nº: 283336). En este proyecto participan 13 socios de 6 estados diferentes, entre los que se encuentra Tecnalia R&I a través de su División de Industria y Transporte.
El objetivo principal es desarrollar tecnologías verdes y eficientes para la fabricación de componentes de materiales compuestos. La actividad de Tecnalia R&I se centra en el desarrollo del corte y recanteado de materiales compuestos mediante la tecnología de chorro de agua y abrasivo (AWJ, Abrasive Water Jet).
Corte por chorro de agua y abrasivo (AWJ)
La tecnología de chorro de agua abrasivo (AWJ) ha recibido una atención considerable por parte de sectores como el aeronáutico o el de la automoción para el mecanizado de compuestos, gracias a las ventajas específicas cuando se mecanizan este tipo de materiales, entre las que destacan:
- Corte en frío: El agua elimina el calor que se genera instantáneamente por el impacto de las partículas abrasivas con el material, de forma que el material no soporta ningún incremento de temperatura y no existe distorsión térmica en la pieza. Es decir, no se produce la zona dañada térmicamente (ZAT).
- El bajo desgaste de la herramienta: En este caso la herramienta de corte es el propio chorro de agua y abrasivos, y por lo tanto, el desgaste que se produce en los componentes donde se genera el chorro (orificio, cámara de mezclado y boquilla, ver Figura 2), es independiente del material a mecanizar. Estos componentes pueden tener una duración y un coste de aproximadamente 120-150 h y 12€ en el caso del orificio, 400-500 h y 90€ en el caso de la cámara de mezclado, y 50-100 h y 100€ en el caso de la boquilla.
- Las bajas fuerzas de corte: Al no haber contacto directo entre el cabezal de corte y la pieza no existen problemas como el chatter, y además, las deformaciones que se producen en la pieza son mínimas y el amarre de pieza requerido es sencillo.
- La alta productividad con una buena calidad de corte: Por ejemplo, la fibra de carbono de 10 mm de espesor se puede cortar a 2.000 mm/min, obteniendo una rugosidad superficial Ra de 10 µm.
- Amigable con el medio ambiente: Este proceso no crea ni gases ni vapores tóxicos.
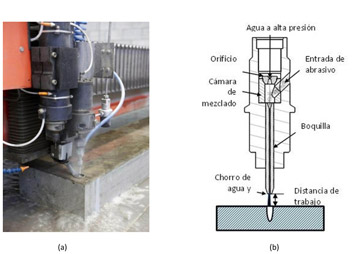
Aunque el corte por AWJ es una tecnología madura, su empleo se enfrenta a varios desafíos cuando se trata de cortar materiales compuestos, principalmente debido a la falta de una metodología de búsqueda de los parámetros de corte óptimos para este tipo de materiales. Habitualmente, los fabricantes de máquinas de corte por agua proporcionan una base de datos con los parámetros idóneos de corte de diferentes tipos de materiales. Sin embargo, cuando se trata de materiales compuestos estas bases de datos son escasas y, por lo tanto, la capacidad para encontrar los parámetros de corte óptimos depende del conocimiento específico y de la experiencia de los usuarios finales de estas máquinas. El desarrollo de una metodología para adaptar los parámetros de proceso para cada tipo de material permitirá ajustar fácilmente las operaciones de corte por AWJ al tiempo que permitirá una expansión del empleo de la tecnología.
Otro de los retos a los que se enfrenta la tecnología AWJ consiste en asegurar que los parámetros de corte son los adecuadas a lo largo de toda la operación, así como detectar cualquier problema que pueda surgir durante el proceso, como por ejemplo el atasco del abrasivo en el tubo de transporte de abrasivo, la rotura del orificio, el desgaste severo en la boquilla o el aseguramiento del control de la distancia de trabajo, conocido como stand-off.
Desarrollo de modelos de corte para materiales compuestos
Una parte importante de la actividad en el proyecto ha consistido en desarrollar bases de datos con los parámetros de proceso optimizados a los tipos de materiales compuestos más habituales. Entre los socios del consorcio, los usuarios finales demandantes de la tecnología cubren varios sectores de mercado con utilización real de materiales compuestos: Azimut-Benetti (Italia), centrado en náutica y yates de lujo, Acciona Infraestructuras (España), dentro del apartado de construcción, y Diad-Group (Italia), FormTech (Reino Unido) y Teks (Francia), fabricantes de componentes para aplicaciones avanzadas de automoción y aeroespacial.
El desarrollo tecnológico llevado a cabo en Tecnalia R&I se centra en la generación de modelos de corte para estos materiales, que se basan en ensayos experimentales realizados en la máquina Byjet L 2030, disponible en Tecnalia. Los materiales ensayados, en total 11, han sido de dos tipos:
- Tipo I: Materiales Compuestos reforzados con fibras;
- Tipo II: Paneles Sandwich.
La forma de caracterizar cada uno de estos tipos ha sido diferente. En los materiales tipo I, el corte se ha caracterizado con la anchura superior de corte (Wtop), la anchura inferior de corte (Wbottom), y la inclinación de la pared o ángulo taper (T), tal y como se muestra en la Figura 2-c. Sin embargo, los materiales tipo II se han caracterizado a través de la anchura superior, la inferior, la anchura máxima (Wmax) y la profundidad a la que se produce la anchura máxima (h) (Figura 2-d). Esto es debido a que en los paneles sándwich (tipo II), a diferencia de los materiales reforzados con fibras (tipo I), el chorro se encuentra con una capa intermedia de un material mucho menos denso y menos duro una vez que ha atravesado la primera capa, por lo que el flujo se dispersa, y vuelve a cerrarse cuando se encuentra con la última capa o cuando el exterior del chorro se queda sin suficiente energía como para seguir erosionando la capa intermedia.
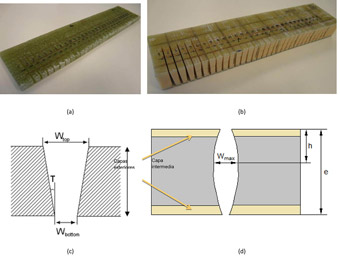
Con los resultados experimentales obtenidos, se han desarrollado modelos de corte que permiten predecir las características descritas anteriormente, así como la desviación del chorro durante el corte a lo largo de la trayectoria, y la calidad superficial de la pieza a través de la rugosidad superficial (Figura 3). A su vez, estos modelos también permiten encontrar los parámetros de proceso adecuados para cada tipo de material y espesor.
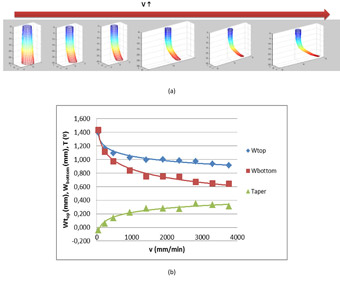
Desarrollo de sistemas de monitorización para el corte por AWJ
Los fallos por atascos de abrasivo son muy comunes en este tipo de procesos y pueden dar lugar a la oclusión de la boquilla o a un atasco en el conducto de abrasivo. En los casos en los que se obstruye el conducto de abrasivo la máquina sigue funcionando, pero al no disponer de abrasivo en el chorro se pierde la capacidad de corte, por lo que únicamente se consigue marcar las piezas y no cortarlas, malgastando tiempo, materia prima y energía. Además, el desgaste de los componentes del cabezal puede producir también una pérdida de potencia de corte del chorro y por tanto afectar a la pieza final. Por tanto, el control del suministro de abrasivo y del desgaste de los componentes del cabezal de corte son críticos durante el proceso.
Para ello, se ha planteado un sistema para la monitorización de las condiciones de corte capaz de detectar de forma eficaz las situaciones de atasco en el conducto de abrasivo y en la boquilla así como el desgaste de los orificios.
La opción más fiable se basa en la monitorización de la depresión generada en el tubo de transporte de abrasivo debido al efecto Venturi que provoca el chorro de agua en la cámara de mezclado. En pruebas llevadas a cabo dentro del proyecto Reform, en los que han variado los parámetros de corte como por ejemplo, la presión y el caudal de abrasivo, y se han realizado ensayos de desgaste de orificios, se ha comprobado que se trata de un método adecuado para la detección del suministro correcto de abrasivo (Figura 4) así como del deterioro de la herramienta (Figura 5). En la Figura 4, se muestra la señal de la presión en el tubo de transporte de abrasivo en un proceso de taladrado de varios agujeros en material compuesto, en la que se diferencian claramente las zonas en las que el chorro está apagado (presión en torno a 1 bar), respecto a cuando solamente se dispone de agua (presión en torno a 0,95 bar) y cuando entra el abrasivo (presión en torno a 0,8 bar). se está funcionando tanto solo con agua como con agua y abrasivo. En la Figura 5, se muestra la variación de esta misma señal en los ensayos de desgaste del orificio.
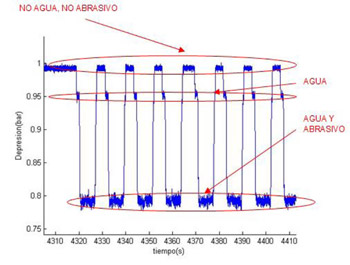
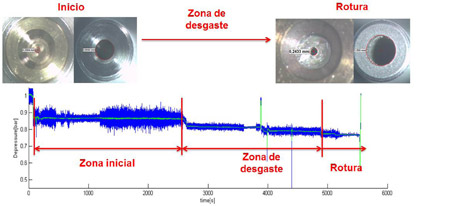
Otro de los parámetros críticos durante el proceso es el control de la distancia de trabajo. El stand-off o distancia de trabajo entre el cabezal de corte y la pieza a mecanizar, es una variable fundamental para alcanzar la máxima productividad del proceso. Dentro del proyecto Reform, Tecnalia está investigando el desarrollo de sistemas de monitorización capaces de detectar esta altura para lo que se está preparando una comparativa entre diferentes tipos de sensores comerciales (Figura 6) con el fin de analizar ventajas y desventajas de cada uno de ellos. A continuación se analizará su implementación en la máquina de corte para realizar tanto el control tanto de altura del cabezal como la profundidad de mecanizado.
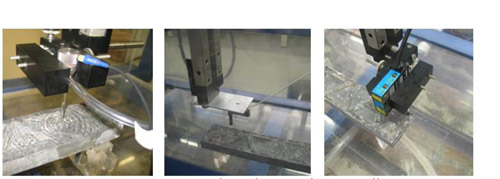
Conclusiones
La incorporación de los materiales compuestos a nuestra vida cotidiana depende casi exclusivamente del abaratamiento de su utilización, tanto en la fabricación del material como de los procesos de mecanizado y transformación. Mientras que la utilización del hierro y del acero cuenta con miles de años de experiencia, la investigación en los procesos de fabricación de los composites avanza decididamente hacia la aplicación industrial a gran escala gracias a proyectos como Reform.
Los esfuerzos de Tecnalia R&I dentro de Reform, se centran en el mecanizado de este tipo de materiales utilizando la tecnología de corte por agua y abrasivo (AWJ) y organizados en dos líneas de trabajo:
- Optimización parámetros de corte mediante el desarrollo de modelos de corte que permitan conocer los parámetros óptimos del proceso y permitan compensar los errores inherentes al mismo proceso (principalmente errores geométricos como por ejemplo, el ángulo taper)
- Sistemas de monitorización del proceso, para evitar problemas durante el mecanizado de este tipo de materiales de alto valor, controlando el flujo de abrasivo, el estado de herramienta y la distancia de trabajo.
Los resultados obtenidos en las dos líneas de trabajo ofrecen ya una muestra de los niveles de mejora y del aumento de rentabilidad de las instalaciones de AWJ, con unos valores muy positivos. Los resultados del trabajo en curso, tanto dentro del proyecto como en otras líneas de investigación relacionadas, terminarán de confirmar y dimensionar este aumento de productividad.
Más información: alfredo.suarez@tecnalia.com
Página web: reform.eu.com