Extrusion machinery
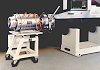
The extruder of plasticizing has three functions: first, removed material into granules of the supply system and leads it to the time that it compresses and, sometimes, vented; Secondly, mixes and produces a cast homogeneous, and, thirdly, develops sufficient pressure to overcome the resistance to the flow of the open row, so that the profile emerges form row continuously.
The extruders are also used for mixing and granulation complexes, to form preforms for molding blow and to feed other machines such as the Calenders. Some types are designed to combine the polymerization, compounding and production in a single unit.
Hydraulic extruders are used for thermoplastics with very high viscosity of the melt, as in the case of the extrusion process for piston of PTFE. The Engel process uses two twin Pistons working cycle to plastify the mass adiabatically to pressures from 1000 N/mm in the shortest time. They can be used in some cases, a very precise extrusion gear pumps filed between the extruder and the row that relieve the extruder's work to generate sufficient pressure to provide a stream of regular cast.
One or several screw extruders
Screw extruders can be equipped with one or more bolts working coordinately. Construction and size are internationally designated by numeric codes. According to Euromap 20, the first number gives the number of screws, the second the diameter in mm and the third the effective length of the screw as a multiple of the diameter. Thus, 2-90-20 designation indicates an extruder of two screws with 90 mm in diameter and 1,800 mm effective length of the screw. The additional letter V indicates cylinder desgasificante (vented).
The extruders multitornillo require more gears and bearings of thrust in the box of mechanisms and a section of the cylinder proper to the type of screw. In other words, they have the same components as an extruder monotornillo. The power is supplied through switches engines infinitely variable or regulated by thyristor which control its speed. Hydraulic traction used very infrequently.
Figure 1
Extrusion head row hose
Another system uses two extruders cascade: the melt is fed from the first extruder, usually with a filter to remove impurities, while the second extruder operates the homogenization and the generation of pressure.
Figure 2 Rows for structural foam tube
Feeding hopper is a separate component with cooling by water around the neck of food. The one or two stages under vacuum, which can warm up for pneumatic feeding, can get significant increases in quantity and quality. Material flow can be regulated through coils, elements of screen, agitators, or a vis-without-end of measure inside or after the hopper.
Protection against wear
Cameras and screw are built with high-strength steels nitrurados, protecting against corrosion by means of hard chromium. Wear protection is obtained carburizando camera and tightening the screw core. Warming and cooling of the camera is divided, as the case may be, between three and seven areas, heating each electrically or with steam or cooling (demineralized) water or compressed air. On the inner surface of the camera, more effective is heating by induction, but it is more cost for electrical resistance. Screws are also used with cavities for the internal control of the air, oil or water temperature.
Figure 3 Machines for greater performance, especially for PVC, PP and ABS compounding, are planetary roller as the Battenfeld illustrated with a power of 350 kW and a production capacity of up to 43,500 kg/hour.
As auxiliary elements between extruder and row include the flow restriction sleeve, adjustable tip width in the front end of the screw or perforated plates that are used to adjust the pressure of the melt to the resistance of the row. These plates also lead carriers to change screens during the operation. Other elements such as the flying restrictors from the tip of the camera, side feeders or distributors of the melt can obtain uniform distributions of the melt in the row. Filters, if necessary, also influence the delivery of pressure to the row.
The most important operating parameters are the speed and torque of the screw, the profile of temperature in the Chamber until the row, and the rate of supply of material and its temperature. They determine the melt pressure and temperature at the head of the screw, and together with the current team front row, determine the quality of the product, which can be monitored using non-contact of the contours, thickness of wall and weight control. The temperatures remain constant through individual control circuits and high-performance machines use computers to control the process, with sensors of pressure and viscosity of the melt.
Rows of complex shapes
Rows for complex design is basically a question of experience, although there are some simple rules which should always apply. First, is to be correct in the row the memory of the material of the helical flow in the Chamber of plasticizing: output stream must be laminated, that otherwise would result in deadlocks in the corners of the profile with irregular shear, a thermal history and the consequent risk of degradation.
If the convergence of the flow is too fast develop tensions high in the extruded, that cannot bear more than 106 Pa in the molten phase and will show signs of fracture of the melt. Tensions develop because the flow converges to its step closer towards the end. If the current flow is strictly parallel, there will be no wind shear, but no tension in the melt. The fracture of the melt is identified by a rough, irregular extruded and often with a helical appearance. An elongated exit conificación can alleviate these problems.
Figure 4 Extrusion equipment are used for the compounding, degassing and granulation of polymers. The equipment used in the primary plants reach have 4,600 kW installed power.
Compensation for dilation
Despite the efforts to eliminate tensions, complex profiles require corrections to row configurations to compensate for uneven dilation due to relaxation of tension. Only radially symmetrical forms will be symmetric row holes without change of form, so rows designer must prepare compensation for changes in shape. It is possible to shorten the zone of conificación in the edges of the profiles to increase the speed of the fade and reduce resistance to the flow that is inversely proportional to the thickness Cubed, so that the row is less sensitive to changes in length as to changes in the contours. The row must be proved with short departures and expert manufacturer always leaves material to cut to extend them when it proves necessary.
Experience has shown that current front row produces only a decrease at the form level, so that preserved the proportions or ratio of dimensions and are little affected by stream, appliances such as guides or cooling baths.
Figure 5 Coesxtrusión systems
The pressure drop, rates of shearing and dilation in the rows of a complex profile can be analyzed with the theory for the Newtonian flow isothermal if profile is reasonably tailored to a combination of simpler forms. If the ratio of the length of the row width is greater than 8: 1, the profile is calculated as a combination of slots. Predict the dilation in the row are required for experimental correlations of the expansion as a function of the recoverable shear stress, which is not easy, as a first course, row manufacturers assume an equal expansion in all directions and prudently leave some metal to extract After rehearsing the row, if it proves necessary.
Postconformado operations
Anyway, it is possible to alter the shape of the extruded itself is just left of the row. An example is the production of tube wall with a pair of chilled drawing roller. Special elements such as helical telephone cables by means of a rotating mandrín to the output of the row where the coating of the wire cools and acquires shape memory are also produced. As it operates at temperatures below the melting point, they can develop voltages, so a selection of the material, product design and optimization of postforming temperature is required to minimize problems of distortion of shape or low impact resistance due to residual stresses.
At the exit of the row, if it's cable coating, the external dimensions of the product defined the diameter of the row and the relative velocity of the row and line drawing. This cannot be with tubes because there is no solid material inside support them, so using calipers immediately at the end of the row that, combined with the mentioned speeds, determine the final dimensions of the product. In some cases an external cooling profile and others, teams of vacuum with friction for Teflon or bronze is used to maintain its external dimension.
Figure 6 Extrusion machines feed to other teams. The production of high quality mechanical or optical flat film requires a cooler of cylinders at the exit of the extruder.
A bath for cooling and a final drive system, other accessories may be required to complete the process. An essential element is the dimensional galgado online without contact, such as the current measure laser tube along two diagonals. The thickness can be measured by ultrasound, which requires water coupling to transmit signals to the product and receive echoes or reflections. These systems automatically control line or extruder speeds through microprocessor, and alert the operator if they require manual settings.
Balanced temperature and speed
The efficiency of the operation depends on a judicious selection of line speeds and temperatures. The easiest starting point is to start with a flat profile of temperature of the camera set up about 50 C above the TF for semi-crystalline plastics and 100 (c) above the TG for the amorphous. If then fluctuates too much pressure on the row, seeks to increase the temperature of the area of food. If this does not give result, attempts to reduce the line and/or the screw speed.
Balanced temperatures and flow rates is delicate. The changes should be minimal and the operator has to wait for the re-establishment of the balance before you make others. If the metering area is heated without changing the temperature of the row or the speed of the line, it will lower the pressure of entry in the row and will be necessary to reduce the speed of the line to keep the dimensions. However, if the clean time increases the speed of the screw, it may be necessary to increase the speed of the line.
On the other hand, increasing the flow of heat outside the zone of transition and the speed of the screw is relatively high, shrinks viscous heat generation and can cause an incomplete fade. If the cast is very low, as in certain polyamides viscosity, there is no more solutions that increase warming in the transition zone.
Finally, to systematize the implementation of the extrusion process, it is convenient to obtain the characteristics of screw output temperature curves. Data of the temperature of the extruded, power consumption and quality of the cast can overcome on these curves to constant rotation speeds which are specific to resins in particular. The use of these data will help to optimize the numerous adjustments nescesarios for the operation of the system of extrusion.
1 A single screw extruders
2 Two-screw extruders
3 Special extruders
4 Extruders for coloring
5 Facilities for coextrusion
6 Extrusion machines for the manufacture of tape continuous
7 Extruders for manufacture of plates
8 Extruders for manufacture of frothed sheet
9 Extruders for the manufacture of monofilament and multifilamentos 10 extruders for manufacture of films and sheets per nozzle flat
11 Extruders for the manufacture of tubes and profiles
12 Extrusion machines for the manufacture of corrugated tube
13 Extrusion machines for the manufacture of tubes by winding
14 Extruders for coating of wires and tubes
15 Extruders or facilities of extrusion of other technologies
16 Teams of cooling, calibration and traction