The Lost Foam process with models of expanded polystyrene
This process has some similarities with the lost wax process, as both use non-permanent models, but while the wax is melted and therefore does not destroy, the EPS disappears completely by vaporization in the casting stage.
Foundry process
The initial coating of the model is typically done with a consisting of finely divided siliceous materials refractory porridge and a liquid of transport that is usually water. It is then covered with refractory sand compacted by vibration.
When the sand has reached the adequate height you can proceed to the casting of metal which can be done following the same techniques employed in conventional molding. In this case the key parameters will be the temperature of casting and casting speed. To go adding the casting metal, high temperature, will lead to the destruction of the model leading to gas which run through the coating.
Comparison of the traditional process in sand with the process lost foam
Advantages of the process lost foam
- As in all processes that use non-permanent models, it avoids the problem of storage models.
- The accuracy of the strained parts is great, allowing the use of EPS to very tight tolerances.
- Simplicity in stages and possibility of recycling that can save some of their materials.
- Facilitates the recycling of the sand due to the absence of binder
- The amount of used sand is generally lower than in a traditional method.
- The use of males and the intervention of specialised personnel in its production is not necessary.
- Models may be prepared by combining simpler parts with suitable adhesives.
- Ease of automation which is a decrease in costs of operation and defects of models parts and molds.
- Better surface finish than with the molding of surface sand, and absence of burrs and lines of partition in the final piece.
- Freedom of design, being this practically unlimited.
- Possibility to incorporate inserts metal in the piece of cast iron
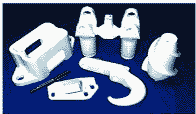
The absence of partition lines is another advantage resulting from the use of a mould without dividing; reduces the finishing operations and it is easier to make high precision parts.
Applications:
Another great application is the sculpture that in this case, the lost, and the wax model not only allows the Elimination of the negative mold, but ignores all a repertoire of tedious operations such as the development of a way to motherthe preparation of the mold by piece, the manufacture of the male, the dumping of the wax and the Elimination of the same, the cooking of the mould, etc.
Currently, they are even integrating the mass of heterogeneous material EPS which plastically will be incorporated into the sculptural work