Micromecanismos Of failure of structural steels during the galvanizing in hot
Introduction
The failure during the galvanizing of structural steels is a problem that detected for the first time in Germany in the years 50[1], although it is in the years 80 when from Japan begin to do systematic studies on the same [2]. The failure consists in the apparition of cracks in structural steels until 500 MPa of elastic limit during his galvanizing in hot in discontinuous (consistent in the immersion of the piece in Zn liquid to 450°C). Said failures are occasional and asistemáticos and only occur during the galvanizing. That is to say, a piece of steel that do not have fragilizado during the process of galvanizing no fragilizará afterwards and presents the same properties that a piece without galvanising.
This failure does not have to confuse with the failure by hydrogen that appears in pieces galvanised of steel of high resistance (elastic limit > 600 MPa), whose origin is the hydrogen absorbed during the phases of decapado and fluxado (immersions in acid) of previous superficial manufacturing to the galvanizing. This type of failures has been properly treated by the norms ASTM, especially the ASTM To123 [3] (whose first version arose in 1928) and ISO, especially the ISO 1461 [4]. The structural steels affected by failure during the galvanizing have structure ferrítico perlítica, little susceptible to fragilización by hydrogen. Besides, Donnay has showed that an increase of the aggressiveness of the decapado hardly has influence in the increase of the failure during the galvanizing of the structural steels, thanks to the inhibidores used usually in said stage [5].
From the years 90 produced a backstitch of the cases of failure during the galvanizing, in parallel to the apparition of new bathrooms of galvanizing, that in addition to the usual additive of 1% of Pb in the bathroom of Zn, included 1% of Sn and 0,1% of Bi, that used to control better the thickness of the coatings of Zn when they galvanised steels calmed to the If, pertinent of electrical oven of arch. As a result of this increase in the cases of failure, in North America and in Europe appeared big projects of investigation that treated to resolve the problem [5-9].
These projects centred a lot in resolving the problem on a large scale, in deleting the cracks of the structural components. Although they have done advances in the understanding of the phenomena that give place to the failure during the galvanizing, establishing that it treats of a process of corrosion under tension because of liquid metal, in which it is not clear the influence of the pertinent hydrogen of the previous stages to the galvanizing (the decapado and the fluxado), have not been able to elaborate a model that explain the micromecanismos by which takes place the failure during the galvanizing.
The presentation of this model is the aim of this article, basing in the experimental work of years already exposed by the authors in other articles [10-13], in a Thesis Doctoral [14], and also in other independent bibliographic sources.
MODEL OF MECHANISM OF FAILURE DURING THE GALVANIZING IN HOT
Treats of a model by stages, that explains how occurs the failure during the galvanizing from the beginning of the fluxado (stage immediately previous to the immersion in Zn liquid) until the stop of fissure or total break of the piece. They take into account, besides, two cases. That in which the bathroom of galvanizing has a content in Sn greater of 0,5% and that in which the content of the bathroom in said element is lower to this 0,5%. To continuation realizar the presentation of the stages of the model.
2.1. Fluxado
In the Figure 1 represents esquemáticamente what occurs in the stage of fluxado.
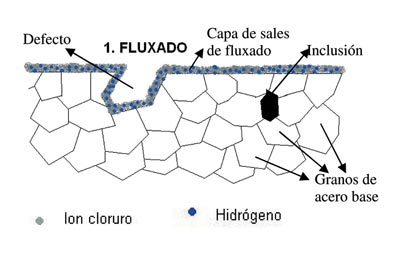
Against of what believed usually in industry, the authors showed in [11] that the reactions of activation between the salts of fluxado and the basic steel that are necessary for the galvanizing, described in [15], take place from the initial instant of the fluxado, to temperature slightly upper to the environingingment, no in the galvanizing to 45°C. These reactions produce the learning of deposits of phases Faith-Zn in the surface of the steel, increase of the rugosidad superficial of the same, what can be the origin of future defects from which produce fisuración, and an increase of the concentration of hydrogen in the surface of the steel. According to the same article [11], does not seem that the hydrogen happen in a significant quantity to the interior of the steel because of the short time of the fluxado (10-15 minutes) and to the structure ferrítico perlítica of the steel.
2.2. Immersion in the bathroom of galvanizing
In the Figure 2 shows of schematic form what occurs in this second phase of the model.
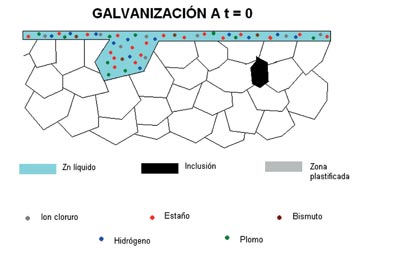
The contact of the basic steel with the liquid metal to 45 °C has three immediate effects that they can affect to the process of failure during the galvanizing:
To) The structural steel increases his temperature of brusque form, with what, as it showed in [11], reduce his values of resistance and ductility until roughly a 30 %.
b) As it describes the technical bibliography on the subject [15, 16], the salts of fluxado when happening to 450 °C in Zn liquid burn “”, accelerating the reactions commented in the point 2.1 previous. However, as it shows in [13, 14], it is usual that remain rests of salts of fluxado without reacting, remaining therefore big quantities of hydrogen in adjacent zones to defects in the surface of the steel to galvanise, that will continue accelerating react them Faith-Zn in these points, as they do in the process global of galvanizing.
c) According to Feldmann [9], due to the fact that the steel is to a temperature much more fry that the liquid metal, of temporary form produces a “freezing” of the just liquid metal in contact with the basic steel, until the said steel reach the temperature of the bathroom. This effect of freezing can be beneficial since it avoids the contact between the basic steel and the liquid metal fragilizante during a time in which they take place important tensions in the basic steel because of the thermal sensors crash. In the following steps of this model will take the case desfavorable (of the side of the hygiene) in which this effect of freezing is not notable to avoid the failure during the galvanizing.
2.3. Learning of phases Faith-Zn
In the Figure 3 shows of schematic form what occurs in the third stage of the model.
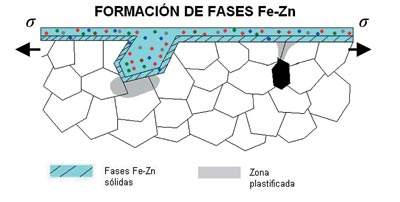
In this step what produces is the usual learning of the phases Faith-Zn, as the exposed by Marder [16], while it takes place a tension in the system by thermal sensors crash. The low solubility of the elements of low melting-point of the bathroom of galvanizing (Pb, Sn, Bi, etc.) in said phases Faith-Zn [17] does that in the central part of the small defects of the basic steel go up the concentration of said elements, forming a liquid metal of melting-point lower and, therefore, more corrosivo. This has checked experimentally in diverse real cases [5] and in laboratory [13]. See an example in the Figure 4.
![It appears 4. distribution of phases of the coating of galvanizing that fills up a fissure of the steel [14] It appears 4. distribution of phases of the coating of galvanizing that fills up a fissure of the steel [14]](https://img.interempresas.net/fotos/952726.jpeg)
Also has checked in [12] that, in spite of the tension of the system, while it do not produce that the factor of intensity of tensions KI do not surpass the threshold KIscc or, even surpassing it, was not increasing, will not produce the break of the phases Faith-Zn and will not produce the propagation of the defect or initial fissure.
2.4. Break of the phases Faith-Zn
In the Figure 5 shows of schematic form what occurs in the fourth stage of the model.
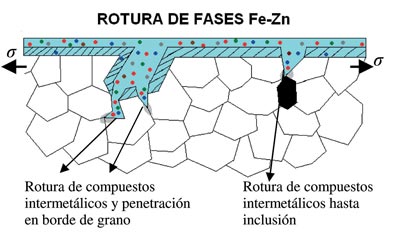
If they produce the quoted conditions in the previous section, that the factor of intensity of tensions KI surpass to the value threshold (so that they can break the phases Faith-Zn) and was increasing (so that they open roads of penetration of more liquid metal), will produce the propagation of the fissure. Due to the fact that KI is increasing, and following the classical theories of fragilización by liquid metal [18], that here assume , will produce an enromamiento of the front of fissure that allow the apparition of more basic metal fresco, preferably in edge of grain (in this case edge of subgrano ferrítico [12, 13]), that will react with more pertinent liquid metal of the open fissure. The process of fisuración will continue repeating of form cíclica the steps 3 and 4 of the model, as it shows the Figure 9 at the end of the article, while KI was upper to the threshold, increasing and besides the concentration of Sn in the bathroom of galvanizing or in the front of fissure was lower to 0,5%.
2.5. Learning of the compound FeSn
In the Figure 6 shows of schematic form the fifth stage of the model.
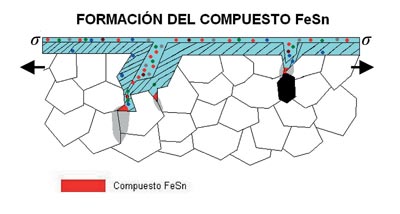
According to the information that gives us the diagram of ternary phases Faith-Zn-Sn to 450 °C [19], if it surpasses the concentration of 0,5% of Sn in a system Faith-Zn, produces a balance between the Faith, the phase Faith-Zn designated and the compound intermetálico FeSn. Therefore, at the bottom of a defect or fissure of a steel that is galvanising , where tends to increase the concentration of Sn, as the explained in 2.3, will arrive a moment in that it begin to form the compound FeSn instead of the usual phases Faith-Zn. This has checked experimentally, as it can appreciate in the Figure 7.
![It appears 7. To) Micrografía and b) Analysis of the bottom of fissure of a real case of failure during the galvanizing[13]... It appears 7. To) Micrografía and b) Analysis of the bottom of fissure of a real case of failure during the galvanizing[13]...](https://img.interempresas.net/fotos/952729.jpeg)
2.6. Break of the compound FeSn
In the Figure 8 shows of schematic form the sixth and last stage of the model of failure during the galvanizing.
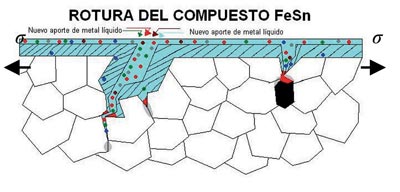
The FeSn is a material of a hardness of 500-700 HV, greater to the one of the phases Faith-Zn, and crystallises in a hexagonal system very rigid [20], by what theoretically has to present a greater fragility that said phases Faith- Zn in the process of failure during the galvanizing. The effect, according to the experiments presented in [11, 12], the tenacity to fracture of probetas CT of steel submerged in bathroom of Zn liquid to 450 °C with 1% of Sn was minor to the tenacity of the probetas submerged in a bathroom without Sn or, alternatively, the failure produced in a lower time. When examining the fractografías of the probetas tested in bathroom with 1% Sn appeared the compound FeSn, and where had not used Sn only appeared phases Faith-Zn.
As it comments in the section 2.4 and in the Figure 9 at the end of the article, in a failure during the galvanizing in a bathroom with more than 0,5% of Sn the fisuración will continue repeating of form cíclica the steps 5 and 6 of the model until it produce the total break of the piece or until KI leave to be increasing.
Conclusions and recommendations
In this article has presented a model of mechanism of failure during the galvanizing, whose summary shows in the Figure 9 to continuation. It treats of a model of corrosion under tension because of liquid metal, in which the hydrogen acts like catalyst, that is to say, acelerante of the failure. They consider two cases. The first of them is that the bathroom of galvanizing have less than 0,5% of Sn, in whose case only have to apply the 4 first steps of the model, and the second is that the bathroom have more than 0,5% of Sn, case in that it is necessary to apply the 6 steps.
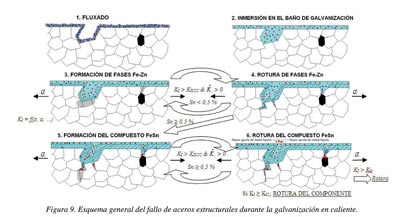
Imposes like mechanical conditionings that for produce the failure the factor of intensity of tensions KI has to be greater to a threshold KIscc and besides has to be increasing. These two conditionings, together with the composition of the bathroom of galvanizing in Sn, serve like criterion to evaluate if the recommendations given to the galvanizadores to avoid the failure during the galvanizing, recommendations that came of the experience in experiments on a large scale, are founded theoretically or no. Any recommendation found in any guide (for example [21, 22]) has to facilitate that KI leave to be increasing or elder that a threshold.
In general the recommendations in [21, 22] and of other similar guides [5], although they did not deduce of the study of the micromecanismos of failure but of experiences on a large scale yes fulfil with the quoted conditions. To these recommendations it would be necessary to add the following specific of the model developed in this article.
- Not surpassing a content in Sn of the greater bathroom of 0,5% in the galvanizing of structures of responsibility. Other recommendations put this limit between a 0,15-0,3% for the Sn, by what remained of the side of the hygiene.
- Limit the content of Pb to no more than 1% and delete the Bi in structures with responsibility.
- Avoid fluxados aggressive that, as it has seen in this article, aggravate the problem of the failure during the galvanizing.
And, although these recommendations already came in other compilations, suits to insist in that they have to choose steels of high degree of tenacity, with surfaces the smoothest possible and not prolonging the contact of the basic metal with the Zn liquid further of the necessary time so that the coating reach the minimum demanded by the norm ISO 1461.
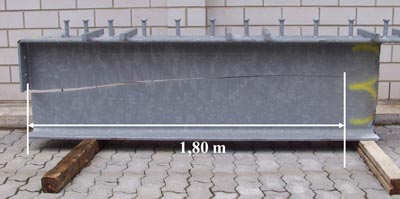
The authors wish to appreciate to the European Commission and to the Ministry of Science and Spanish Innovation (current Ministry of Economy and Competitiveness) the financials of the project FAMEGA, that constitutes the basic work for the realisation of this model. Also it wishes to appreciate the help and the material loaned to the companies Corus-Tata and Arcelor-Mittal and to the rest of partners of the project Famega.
References
[1] Rädeker, W., “Die Erzuegung von Spannugsrissen in Stahl durch flüssiges Zink”. “Stahl und Eisen”, 73, No.10. Dusseldorf, Germany, 1953. pp. 654-658.
[2] Kikuchi, M. Liquid Metal Embrittlement of Steels during Hot Dip Galvanizing. In Tetsu to hagane (Ironinging and Steel). Vol. 68, no. 14. Japan, 1982. pp. 1870-1879.
[3] ASTM To123/To123M-12. Standard Specification for Zinc (Hot-Dip Galvanized) Coatings on Ironinging and Steel Products. ASTM International. 8 pp., Pennsylvania, USES, May 2009.
[4] Norma JOINS-IN ISO 1461:2010. Coatings galvanised in hot on products finished of ironinging and steel. Specifications and methods of essay. AENOR. 21 pp., Madrid, January 2010.
[5] Rudd, W.J., Donnay, B., Gutiérrez-Solana, F., et al. FAMEGA. Failure Mechanisms During Galvanizing. Final Report. Research Fund for Coal and Steel (RFCS) Joint report EUR-23195-IN 2008. European Commission. 110 pp., Brussels, 2007.
[6] Kinstler, T.J. Current Knowledge of the Cracking of Steels During Galvanizing. To Synthesis of the Avaliable Technical Literature and Collective Experience for the American Institute of Steel Construction. In http://www.aisc.org/content/contentgroups/engineering_and_research/research1/final5906.pdf. Galvascience LLC. 79 pp., Springville, USES, 2005.
[7] Elboujdaini, M., Tyson, W.R., et al. ZM-396: Control of Cracking During Galvanised Structurals: Final Report Phase 2, 3 and 4b. CANMET, Metals Technology Laboratories, International Lead Zinc Organisation Inc. Canada, 1995-1997.
[8] James, M. N. International Lead Zinc Research Organisation Programme ZC-21-1: Galvanizing High Performance Steels for the Construction Market. European General Galvanizers Association Assembly 2007. Edinburgh, United Kingdom, 12-14 June 2007. pp. 90-105.
[9] Feldmann, M., Pinger, T., Schäfer, D., Pope, R., Smith, W., Sedlacek, G. Hot-Dip-Zinc-Coating of Prefabricated Structural Steel Components. Background Document in Support to the Implementation, Harmonization and further Development of the Eurocodes. Joint Report. JRCEuropean Commission cooperation agreement for the evolution of the Eurocode 3 (programme of CEN/TC 250). EUR 24266 IN-2010. 110 pages.
[10] Carpio, J., Married, J.To, Álvarez, J.To., Gutiérrez-Solana, F. Design and Validation of To Device for Tensile and Toughness Tests of Specimens Immersed in Liquid Zinc. Engineering Failure Analysis. Vol. 15-3. Elsevier. Cambridge, United Kingdom, 2008. pp. 229-236.
[11] Carpio, J., Married, J.To, Álvarez, J.To., Gutiérrez-Solana, F. Environingingmental factors in failure during hot-dip galvanizing. Engineering Failure Analysis. Vol. 16-2. Elsevier. Cambridge, United Kingdom, 2009. pp. 585-595.
[12] Carpio, J., Married, J.To, Álvarez, J.To., Méndez, D., Gutiérrez-Solana, F. Stress Corrosion cracking of structural steels inmersed in hot-dip galvanizing tubs. Engineering Failure Analysis. Vol. 17-1. Elsevier. Cambridge, United Kingdom, 2010. pp. 19-27.
[13] Carpio, J., Married, J.To, Álvarez, J.To., Méndez, D., Gutiérrez-Solana, F. Microscopic study of the failure during the galvanizing: real cases and of laboratory. XXXI Meeting of the Spanish Group of Fracture. Saint Lorenzo of the Escorial, Spain. 6 pages, 2014.
[14] Carpio, J., Mechanism of failure of structural steels during the galvanizing in hot. PhD. Thesis. 339 pages. Santander, Spain, 2013.
[15] “Fluxing bathes”. In www.fib.be/en/products/rm_pages/00125b.htm. Him Fur Industriel Belge. Belgium, 2005.
[16] Marder, To.R. The Metallurgy of Zn-coated Steel. In Progress in Materials Science. Vol. 45. Pergamon. Pennsylvania, USES, 2000. pp. 191-271.
[17] http://www.crct.polymtl.ca/fact/documentation/sg YOU/SGTE_Figs.htm. Center for Researck in Computational Thermochemicals. Montreal, Canada.
[18] Pugh, And.N. Stress Corrosion Cracking and Hydrogen Embrittlement of Ironinging Based Alloys. National Association of Corrosion Engineers, 1977. P. 37.
[19] Avettand-Fénöel, M.N., David, N., Reumont, G., Fiorani, J.M., Vilasi, M., Perrot, P. Assessment of the Faith-Sn-Zn Phase Diagram at 450°C. Application to the Batch Galvanizing. Journal of thermal sensors sensors Analysis and Calorimetry. Vol. 90-2. Springer. New York, 2007. pp. 329-332.
[20] Giefers, H., Nicol, M. High Pressesure X-ray Difraction Study of all Faith-Sn Intermetallic Compounds and one Faith-Sn Solid Solution. Journal of Alloys and Compounds. Vol. 422. Elsevier. 2006. pp. 132-144.
[21] Galvanizing Structural Steelwork. An Approach to the Management of Liquid Metal Assisted Cracking. The British Constructional Steelwork Association Ltd. London, United Kingdom, 2005. 20 pages.
[22] Recommendations for the Prevention of Cracking in Hot Dip Galvanized Steel Structures. Draft report. German Steel Union Industrial Association of Hot Dip Galvanizers. Germany, 2005. 4 pages.