Descripción técnica
2.1 Selección de los componentes
El componente seleccionado en este caso era una pieza pequeña (véase figura 1) y finalmente fue producida por el proceso de fundición de escayola (especial), una variante del proceso de fundición a la cera perdida en el cual el molde refractario es un bloque de escayola o yeso. Sus dimensiones principales eran 126 x 37.2 x 45.30 milímetros.
El componente seleccionado para la aplicación de la inyección de plástico fue constituido por insertos macho y hembra. En este caso la dimensión de los insertos eran más grandes; el inserto hembra era de 313.1x176.8x85.9 mm, y las dimensiones del inserto macho eran de 285.6x147.9x95.1 mm (véase figura 2). En este caso se intentó que macho y hembra se ensamblasen con el menor número de operaciones de mecanizado posible.
2.2 Selección de las tecnologías RP
De hecho, casi todos pueden producir modelos hechos de diversos materiales poliméricos o de ceras especiales que se pueden recubrir con materiales cerámicos o refractarios de escayola, y después quemar totalmente para obtener el molde hueco de cerámica o yeso en el cual el metal fundido se vierte y se deja solidificar. Sin embargo, considerando que el producto final que se obtendrá en este caso eran insertos de molde en los cuales la calidad superficial y las tolerancias que debían ser obtenidas eran parámetros críticos, era esencial realizar un análisis profundo del estado del arte del prototipado rápido.
Las características principales que se consideraron para hacer la selección final fueron las siguientes: tolerancias, calidad superficial, el comportamiento durante el quemado y la cantidad de cenizas (restos) producidas, y la compatibilidad con los procedimientos habituales de la fundición.
Las características de los modelos obtenidos con las diversas tecnologías fueron primeramente analizadas a partir de datos recogidos de una revisión bibliográfica, lo que permitió hacer una selección preliminar de cuatro tecnologías convenientes: el proceso de Quickcast Stereolithography, el proceso selectivo de sinterización láser de Castform (SLS), y los procesos de Thermojet y Sanders 3D.
Otras tecnologías que habrían podido ser consideradas (Layer Object Manufacturing LOM - Z-Corp - FDM, etc.) fueron desechadas debido a diversas razones, como la cantidad de cenizas producidas durante el proceso de quemado, a la rugosidad superficial excesiva, a las tolerancias o la estabilidad dimensional, etc.
Las primeras experiencias realizadas con los modelos hechos con las cuatro tecnologías preseleccionadas mostraron que las cuatro eran convenientes para las aplicaciones de fundición de cera perdida. Sin embargo, se vio que aunque la tecnología Quickcast presentó un nivel alto de tolerancia y una superficie especialmente lisa tras el pulido, el proceso de quemado fue más complicado que con las tecnologías de Thermojet, de Sanders y de Castform.
La tecnología Sanders presentó una alta exactitud en sus modelos y la superficie podía pulirse fácilmente. Su única desventaja era que las dimensiones de las piezas que podrían ser producidas eran pequeñas, y por lo tanto fue seleccionada solamente para construir el modelo que se utilizaría en la producción de los insertos pequeños de SMC. El grado del detalle que podría ser obtenido con este proceso, junto con la fácil manipulación en las operaciones de fundición de precisión a la cera perdida, hace de él el candidato óptimo para este inserto.
La fabricación de los moldes macho y hembra de inyección de plástico se realizaron con los modelos de Thermojet. La tecnología Sanders no podía ser utilizada debido a la limitación de tamaño y coste de esta tecnología. La selección de Thermojet frente a Castform fue hecha teniendo en cuenta la calidad superficial obtenida (tabla 1) y la precisión de los modelos prototipo (tabla 6), que era también superior. Para el quemado y la fabricación del molde cerámico, ambas tecnologías eran similares.
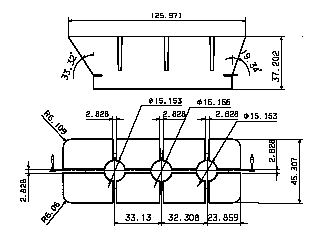
2.3 Optimización de la fundición
No hay prácticamente datos bibliográficos sobre el uso de éste o cualquier otro composite de matriz metálica para las aplicaciones de la fundición a la cera perdida. Por lo tanto, se llevó a cabo un estudio completo antes de la fabricación de las fundiciones en el que se estudiaron los diseño óptimos para un sistema de alimentación, las temperaturas de fundido y moldeo, y el control de la solidificación. El comportamiento de este material - y de otros compuestos reforzados con partículas cerámicas que fueron también ensayados - difieren bastante de aquellas aleaciones no reforzadas. Estos compuestos son muy propensos a absorber el hidrógeno cuando están fundidos y se debe tener, por tanto, mucho cuidado durante la fase de fundición.
Hay que prestar especial cuidado a la preparación de las partículas de cerámica densas. Por otra parte, la presencia de partículas de cerámica significa que la obtención de los componentes con la calidad metalúrgica necesaria fuera mucho más difícil.
El inserto de SMC fue realizado por medio de la tecnología de la fundición de precisión a la cera perdida con molde de escayola o yeso. En este proceso, un sistema de alimentación integrado por diversos componentes de cera se integra con el modelo del componente final (en este caso era un modelo de Sanders). Entonces se introduce todo el ensamblaje en un cilindro metálico en el cual se producirá el molde del yeso. La mezcla del yeso y del agua se vierte bajo vacío y, una vez que el yeso se ha endurecido, se introduce el ensamblaje en un horno de modo que se funda la cera y se quemen los restos. El paso final es la fundición y el vertido del material compuesto bajo vacío en el molde hueco de yeso. El uso del vacío ayuda al material para llenar las partes más enrevesadas del molde de forma que se asegura la obtención de una pieza completa y casi acabada.
Los insertos macho y hembra del molde de inyección de plástico se realizaron con la variante de la fundición de cera perdida denominada “shell casting”. Aquí el yeso es sustituido por un material cerámico. El ensamblaje del modelo (en este caso eran modelos de Thermojet) y del sistema de alimentación se sumerge en las mezclas de cerámica, revestidas con distintas capas de distintos espesores, que son secadas, tratadas y vueltas a sumergir para alcanzar la consistencia suficiente para resistir el proceso de fundición posterior. El tiempo empleado para construir los moldes cerámicos está controlado por el proceso de secado de cada capa. Las dos primeras capas de cerámica se dejaron secar durante la noche, y se aplicaron posteriormente otras dos capas cada día para obtener la carcasa de cerámica.
Se realizaron multitud de pruebas para obtener los parámetros óptimos de fundición de ambas tecnologías.
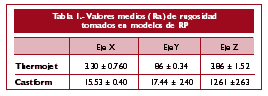
2.4 Producción de los insertos prototipo
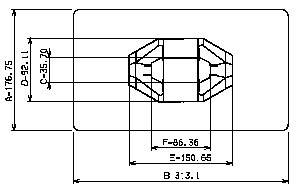
Los diversos modelos producidos fueron medidos en puntos previamente seleccionados para analizar los cambios dimensionales producidos durante los diversos pasos del proceso entero.
El sistema de alimentación hecho de ceras fue incorporado a los modelos, y se produjeron los moldes de yeso y de cerámica siguiendo los pasos explicados previamente. El último paso fue fundir el material MMC para obtener los componentes finales.
Los componentes fueron finalmente desmoldeados y medidos otra vez en los mismos puntos de referencia utilizados previamente. Las medidas tomadas en estos puntos fueron comparadas a posteriori, con el fin de controlar la precisión del proceso completo.
Los componentes fueron mecanizados para eliminar el sistema de alimentación y, en algunos casos, pulidos para mejorar la calidad superficial de los componentes finales y encajar macho y hembra de la inyección de plástico. También fue necesario un cierto trabajo adicional para ajustar los componentes finales del ensamblaje de los moldes de SMC y de la inyección de plástico antes de que las pruebas en condiciones del servicio se realizaran. El mecanizado de los agujeros para los expulsores, así como el ajuste de los insertos macho y hembra llevaron del orden de 8 y 16 horas para el molde SMC y los de inyección, respectivamente. Cuando todos estos trabajos de ajuste se acabaron, se produjeron algunas piezas para validar los insertos fabricados y la mayor resistencia al desgaste del material compuesto utilizado.
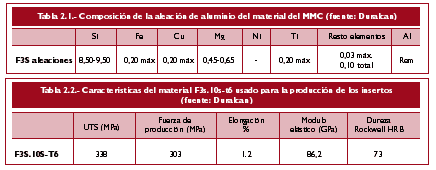
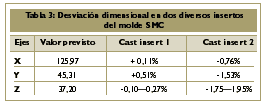
3. Resultados
Se vio que la rugosidad superficial que fue obtenida por fundición en todos los casos era bastante buena. Una operación de pulido a mano leve del material del MMC fue suficiente para obtener una rugosidad superficial que hizo posible desmoldear y obtener piezas de plástico y piezas de SMC con un buen aspecto superficial. Los resultados obtenidos con los diferentes insertos se presentan en el tablas 3, 4 y 5.
Cuando estos datos fueron comparados con las medidas adquiridas de los modelos prototipados rápidos, la primera conclusión que podría ser extraída era que el paso del proceso que limita hoy en día la obtención de piezas con una precisión más alta no es el proceso de fundición, sino del modelo de prototipado rápido.
El inserto de SMC con el cual sólo se fabricó el inserto hembra no presentó ningún problema especial. El ajuste de los insertos macho y hembra que correspondían al molde de inyección consumió más tiempo del previsto. Esta operación requirió 8 horas de mecanizado y de operaciones de ajuste no previstos inicialmente.
En este caso, los insertos macho y hembra fabricados debían garantizar que, cuando el material plástico fuese inyectado, el molde se llenaría correctamente y no se produciría ninguna rebaba. Esto implicó la no utilización directa del molde, debido a una tolerancia insuficiente en el ajuste. El inserto macho fue mecanizado a mano, de forma que la holgura con la hembra fuese inferior a 0.05 mm. Aunque la contracción del material MMC durante la solidificación intervino en la precisión del componente final fabricado, se vio que la influencia de los prototipos rápidos era mucho mayor. Se vio también que diferentes proveedores proporcionaban prototipos de dimensiones distintas (0.5-3%) aunque el fichero STL enviado fuera el mismo.
Otro punto importante que debe también ser señalado es que el análisis del tiempo necesario para obtener estos componentes demostró que esta tecnología podría competir realmente con otras tecnologías de fabricación de moldes rápidas, tales como como el Keltool, Laserform, o mecanizado de alta velocidad. Podrían ser necesarios alrededor de 7 a 18 días después de que el fichero 3D de los insertos estuviera disponible por parte del cliente.
Una secuencia aproximada de los pasos principales de producción sería como sigue:
En el caso en el cual el cliente envía un fichero STL al cual solamente se le ha de aplicar la corrección para la contracción del material de MMC, y la variante plaster casting o fundición con molde de yeso pude ser utilizada, los insertos se podrían acabar en un tiempo de dos semanas.
Es también posible y algo común que el cliente envíe un fichero 3D que requiera de trabajo adicional antes de que pueda ser enviado a la oficina de prototipado rápido. En las piezas complicadas, el diseño del sistema de alimentación puede durar más de lo previsto.
Finalmente, la forma y tamaño de un inserto de molde puede suponer una limitación para el uso de la fundición con yeso. En ese caso hay que emplear la fundición shell casting, con lo que el tiempo dedicado a la fabricación del molde de cerámica es mayor. Como se trataría de piezas complicadas, pueden ser necesarias operaciones de mecanizado y de ajustes en general, lo que justifica que el ciclo de producción de las mismas pueda alcanzar los 18 días.
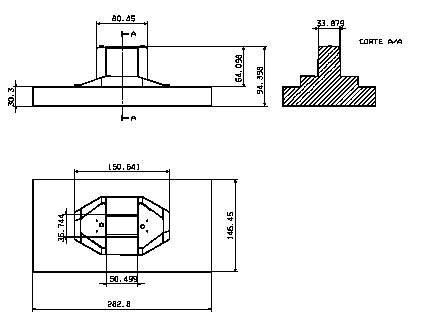
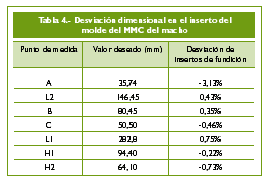
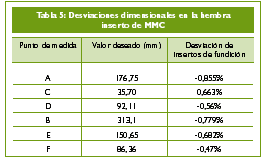
4. Conclusiones
El uso de insertos realizados con materiales MMC garantiza la fabricación de 5.000 componentes de SMC (con 30% de fibra de vidrio, muy abrasivo) sin signos de deterioro o desgaste en la superficie de los insertos. No se pudo probar durante más tiempo por carga de producción de otras piezas.
El paso del proceso que controla el mismo en términos de calidad es la producción de los modelos de prototipado rápido. Aunque estas tecnologías han avanzado mucho en los años recientes, parece clara la necesidad de una política de estandardización. El uso del mismo fichero STL no garantiza la obtención del mismo modelo.
Parece evidente que, para alcanzar un ajuste preciso y correcto entre las diferentes partes del molde, siempre será necesario un ligero mecanizado. La razón principal es que el estado actual de las tecnologías de prototipado rápido no garantiza la exactitud necesaria. Los fenómenos derivados de la contracción del material en la solidificación tras la fundición deben ser también considerados cuando diseñe el modelo.
Se recomienda el uso de la fundición con moldes de yeso, ya que puede disminuir hasta una semana la producción final de los moldes. Los puntos principales que deben ser estudiados más a fondo son cómo disminuir el tiempo de entrega del componente final para los componentes grandes y cómo mejorar la calidad de los modelos de prototipado rápido usados.
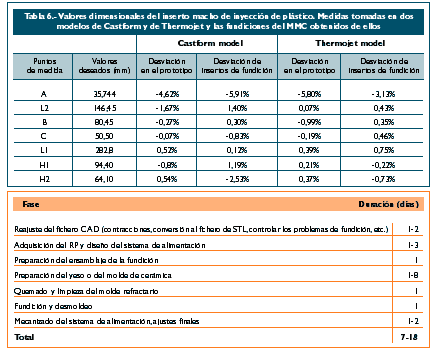
5. Agradecimientos
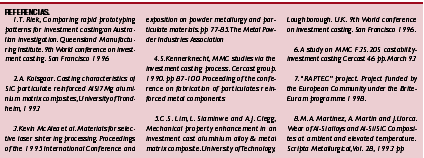