Neopor Ccycled de BASF es una solución innovadora de balance de masa con una huella de carbono de producto que se ha reducido en torno a un 90% en comparación con el Neopor convencional
Cascos de seguridad KASK con carcasa interior fabricada en Neopor® Ccycled® de BASF: máxima seguridad y mínima huella de carbono
KASK, la emblemática marca italiana de cascos, utiliza gránulos de poliestireno expandido (EPS) Neopor Ccycled de BASF para la fabricación de cascos de seguridad de trabajo. En el proceso de fabricación de Neopor Ccycled, las materias primas fósiles se sustituyen por aceite pirolítico obtenido a partir de residuos plásticos posconsumo sometidos a reciclaje químico en el inicio de la cadena de valor de BASF mediante un método de balance de masa1. De esta forma, BASF puede ofrecer Neopor Ccycled, con una huella de carbono de producto que se ha reducido en torno a un 90% en comparación con el Neopor convencional.
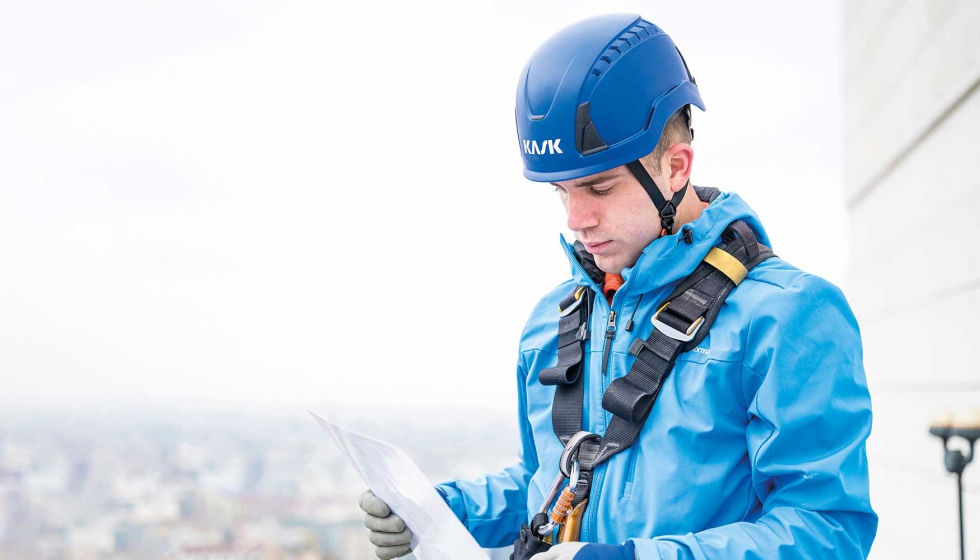
En la actualidad, KASK utiliza este EPS más sostenible para fabricar la carcasa interna de la serie Primero, a la que se unirán las carcasas internas de las series de cascos de seguridad Zenith X y Superplasma a partir de finales de octubre de 2024. Estos productos mantienen las mismas prestaciones en cuanto a calidad y seguridad, y mejoran la huella de carbono de producto en comparación con el uso del EPS convencional. Al elegir estas series de productos, que en su conjunto engloban la mayor parte de los cascos vendidos, KASK consigue tener un impacto positivo en la economía circular.
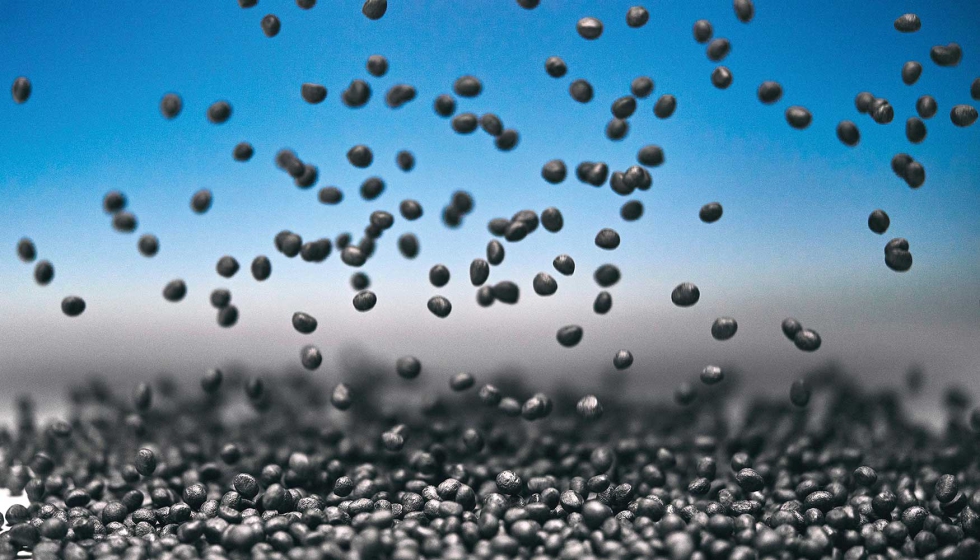
Los cascos KASK establecen estándares de seguridad desde hace dos décadas
KASK, que celebrará su 20º cumpleaños en 2024, ha crecido hasta convertirse en una marca pionera en el ámbito de la seguridad en el deporte y en el lugar de trabajo en las últimas dos décadas. Al dar prioridad a la protección personal sin renunciar a la comodidad, el diseño y el rendimiento, KASK ha establecido un nuevo enfoque en la protección de la cabeza. Además, todas las series de cascos KASK superan las normas de seguridad europeas e internacionales más exigentes.
“En KASK nos comprometemos de forma permanente con la investigación y el desarrollo de tecnologías y soluciones innovadoras destinadas a mejorar constantemente seguridad, comodidad y diseño de los cascos”, afirma Angelo Gotti, fundador y propietario de KASK. “Nuestro objetivo es lograr que cada trabajador maximice su rendimiento a lo largo del día, garantizando la libertad y la sensación de protección incluso en las situaciones más exigentes y arriesgadas”.
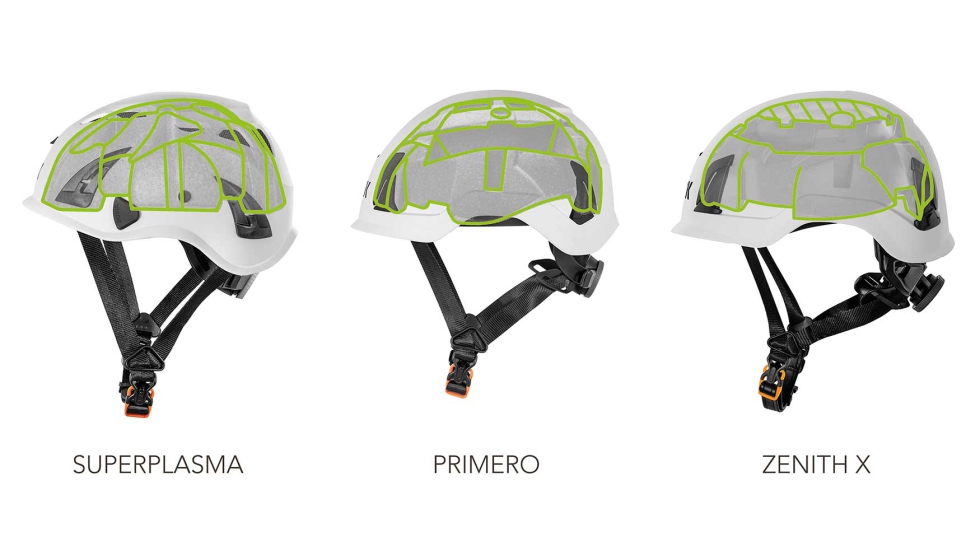
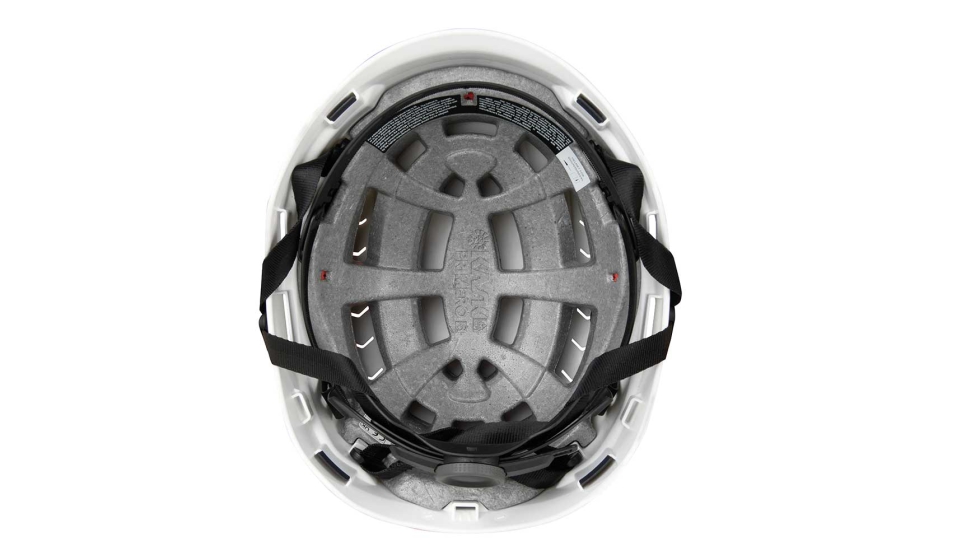
Neopor Ccycled de BASF contribuye a preservar las materias primas fósiles
La decisión de utilizar Neopor Ccycled para la carcasa interna de los cascos de seguridad de KASK se ha tomado tras pruebas de rendimiento intensivas, que demostraron que Neopor Ccycled es capaz de garantizar las mismas propiedades mecánicas que el Neopor estándar, como la alta absorción de energía de impacto en todas las direcciones.
“En KASK, la seguridad es nuestra máxima prioridad. En nuestra continua búsqueda de soluciones más sostenibles, recurrimos a BASF para encontrar los mejores materiales que pudieran garantizar un impacto medioambiental más reducido y, al mismo tiempo, mantener el mismo nivel de protección y confort para los trabajadores. Nos sentimos orgullosos de esta colaboración, que nos ayuda a reducir el uso de materias primas vírgenes y a contribuir a la transición hacia alternativas más sostenibles, explica Marta Beltramello, directora de Ventas y Marketing de KASK Safety. ”La colección Primero, que salió al mercado en 2023, fue la primera en incorporar el EPS Ccycled de BASF. Sin embargo, no nos detuvimos ahí: ahora, tanto la colección Zenith X como la Superplasma cuentan con una carcasa interna fabricada en Neopor Ccycled.
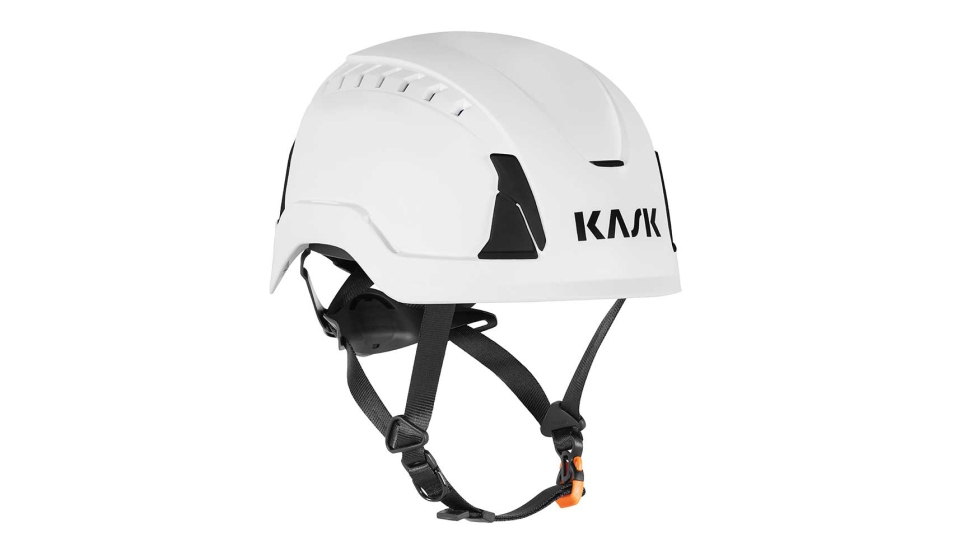
En la fabricación de Neopor Ccycled, las materias primas fósiles se sustituyen por aceite pirolítico al inicio de la cadena de valor petroquímica. Esta materia prima alternativa se obtiene de la pirólisis de residuos plásticos que, de otro modo, se destinarían a la recuperación de energía o terminarían en el vertedero. La atribución del aceite pirolítico a Neopor Ccycled según un método de balance de masa se ha certificado de forma independiente de acuerdo con REDcert².
“Para nosotros es sumamente importante que nuestros productos contribuyan a reducir el consumo de recursos fósiles y a hacer posible la transición a una economía circular, sin comprometer la calidad ni la seguridad”, afirma Alessandro Gandini, director comercial de Espumas Estirénicas del Área Mediterránea de BASF. “Estamos sumamente orgullosos de que Neopor Ccycled haya sido seleccionado para los cascos de seguridad de alta calidad de KASK, algo que contribuirá a la seguridad de los trabajadores cada día”.
- Las materias primas fósiles convencionales que se necesitan para fabricar los productos de BASF se sustituyen por materias primas recicladas procedentes del reciclaje químico de residuos plásticos o neumáticos al final de su vida útil a lo largo de la cadena de producción integrada de BASF. La parte correspondiente de materia prima reciclada, por ejemplo aceite pirolítico, se atribuye al producto Ccycled específico mediante un método de balance de masa certificado. Los centros de BASF y los productos Ccycled han sido certificados por terceros según sistemas de certificación reconocidos internacionalmente, como REDcert2 e ISCC PLUS, y se ajustan a las definiciones de la norma ISO 22095:2020. La materia prima reciclada no es cuantificable en el producto de balance de masa de BASF. La huella de carbono de producto de principio a fin se calcula según la Metodología TfS utilizando un enfoque de Expansión del Sistema Upstream (USE). El USE contabiliza un crédito por el tratamiento de residuos que se ha sustituido ya en el primer ciclo de vida (por ejemplo, la incineración), reduciendo así la huella de carbono de producto en comparación con el producto fósil convencional equivalente. Los datos de la huella de carbono de producto están sujetos a revisiones periódicas.