Tiempo de permanencia y tiempo de residencia, dos tiempos que se confunden (Parte 2)
José Ramón Lerma, escritor técnico y docente
04/12/2023Análisis del material fundido durante el tiempo de permanencia: La influencia de estos tiempos de permanencia en la zona delantera del husillo y en el hot runner respecto a la masa fundida y cómo se comporta esta térmicamente, han sido estudiados a través de experimentos.
Permanencia en zona delantera de la unidad de inyección y en el canal caliente
Debemos pensar en lo que pasa en esa masa fundida en la parte delantera del cilindro.
Mientras el material viaja desde la tolva hasta la zona delantera de la unidad de inyección, le aplicamos temperatura exterior a través de las resistencias del cilindro y también aplicamos bastante calor a través de la cizalla generada por la velocidad tangencial del husillo y la compresión del material en la zona de compresión de del husillo.
Pero, cuando el material alcanza la zona delantera de la unidad de inyección a través de la válvula de la punta del husillo, en este momento pasamos a calentar esa masa fundida desde el exterior a través de las resistencias del cilindro. Ya no tenemos el calor aportado por el giro y la compresión del husillo. A partir del paso del material a través de la válvula de la punta del husillo, el flujo del material es laminar, sin aportación de calor por rotación.
En este momento con el material ya ubicado en la zona delantera de la unidad de inyección, las resistencias calientan el acero del cilindro desde el exterior. Este acero caliente transmite y calienta el material que se encuentra en la periferia del volumen dosificado. Por tanto, el diferencial de temperatura entre la capa exterior limítrofe de este volumen, en contacto con el acero caliente del cilindro, y el núcleo interior de este volumen irá en aumento.
A medida que el material se encuentra esperando a ser inyectado, forma diferentes capas de temperatura de fusión. Imaginemos la alegoría de las capas dentro del interior de la tierra. En este caso, hay dos secciones diferenciadas en la sección de la masa fundida que permanece en la zona delantera del cilindro, frente al husillo.
- Está el área más cercana al diámetro interior del cilindro y más influenciada por las temperaturas del mismo. Llamémosle a esta área la coraza.
- La capa fundida en el centro del cilindro o núcleo de la masa fundida.
Aquí, el material se ha fundido principalmente por el calor generado por la fricción del husillo que transportaba el material plástico hacia adelante. Durante su recorrido a través de las diferentes zonas del husillo y debido al diseño de este, zona de compresión etc., el material ha ido fundiéndose, partiendo de granza sólida y se ha ido homogeneizando térmicamente a través del mecanismo del husillo que ha fundido y mezclado homogéneamente la masa.
Lo más probable es que en el momento de finalización de la etapa de dosificación, la capa externa o coraza –a pesar de estar en contacto con el acero calentado por las resistencias–, esté más fría que la capa fundida cerca del centro o núcleo que ha recibido la fricción del husillo.
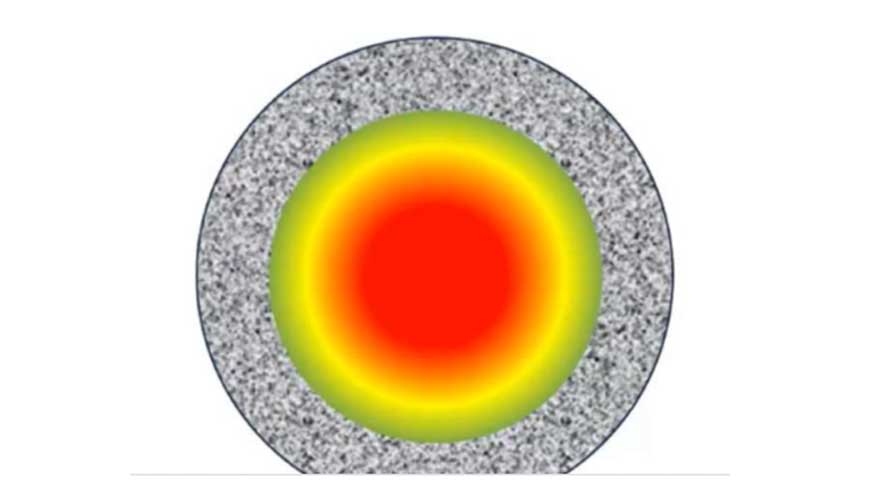
Temperatura del cilindro de inyección versus fricción
Algunos de nosotros hemos experimentado o nos han contado alguna anécdota de algún caso donde una inyectora trabajando (normalmente con poliolefinas, PP, HDPE con temperaturas de fusión moderada), sigue trabajando a pesar de poner en 'off' la calefacción del husillo, o en algunos casos con alguna resistencia del cilindro no operativa.
¿Qué es lo que aporta calor para mantener el plástico fundido? La respuesta es que la mayor parte del calor necesario para fundir el plástico es aportada por la fricción y el diseño del husillo.
En realidad, esta fricción que genera el husillo al girar incrementa la temperatura del material incluso por encima de las temperaturas programadas en el cilindro y explica por qué esa capa fundida interior en el núcleo del volumen dosificado esté más caliente que la capa de la cubierta, que técnicamente se está enfriando a la temperatura del diámetro interior del acero de la cámara.
Visto este efecto de una mayor aportación de calor debido a la fricción del husillo, es poco probable que con aumentos del tiempo de permanencia, con el husillo estático, se incremente la uniformidad de la masa fundida. Al aumentar el tiempo de permanencia en la zona delantera del husillo en estático podría, eventualmente, generarse una transmisión de calor del núcleo que está más caliente hacia el exterior, que está ligeramente a menor temperatura. Y acabar de fundir algún elemento infundido hasta ese momento.
Además, se produce otro efecto durante el tiempo de permanencia. La masa fundida permanece inactiva: no hay movimiento, fricción ni mezcla. Además, las diferencias de temperatura en las capas externas de la masa fundida podrían incluso aumentar, lo que se llama el efecto “horno”. En el tiempo que el material está ubicado en estático en la zona delantera de la unidad de inyección, es decir, durante el tiempo de permanencia, no aportamos calor por fricción al núcleo y si calentamos el material desde el exterior del cilindro a través de las resistencias, lo que conseguimos es lo contrario de una masa fundida uniforme y homogénea: aumentamos el delta térmico entre la capa externa y el núcleo central del material dosificado.
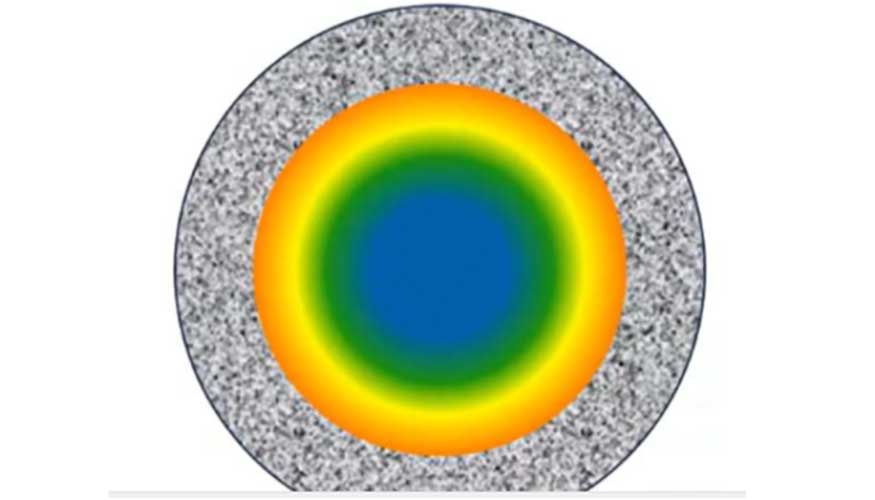
Consideraciones sobre los husillos
Es siempre recomendable para lograr una masa fundida uniforme y una temperatura de fusión correcta que el diseño del husillo utilizado sea para el material específico que se está procesando.
Se utilizan diferentes diseños de husillo con el objetivo de optimizar la calidad de la masa fundida y la productividad a través de la correcta aplicación de la fricción o cizalla en el interior del husillo para cada material. No obstante, dado que la mayoría de los transformadores utilizan diferentes materiales plásticos en una misma unidad de inyección, el husillo más utilizado por su versatilidad es el denominado husillo universal.
Proceso, condiciones
La forma más efectiva de garantizar una temperatura uniforme es a través de la programación de los distintos factores y parámetros que determinan la fase de dosificación
Las condiciones del proceso son críticas para una masa homogéne. La velocidad tangencial de giro del husillo, la contra presión durante la dosificación, el tiempo de retardo de la dosificación, son parámetros clave para conseguir reducir el tiempo de permanencia, de modo que el tiempo entre el fin de esta fase de dosificación y el inicio de la inyección del ciclo siguiente sea lo más corto posible. Así como las temperaturas del cilindro son fundamentales para garantizar que se produzca una masa fundida homogénea de material siendo esta uniformidad de la masa fundida absolutamente crítica para un proceso repetitivo y constante.
Finalmente es clave asegurarse de que la utilización de la unidad de inyección es del orden del no menos del 20% y no más del 60% de la capacidad máxima de inyección o también otra regla de taller interesante es aquella que dice que el recorrido de la dosis debe ser de al menos la longitud equivalente en mm a un diámetro 1D y máximo 3D, nunca más de cuatro diámetros 4 D.
Trabajar dentro de este rango ayuda a garantizar que el husillo rote lo suficiente como para generar suficiente fricción y homogeneidad en la masa fundida y no tengamos excesivos o insuficiente tiempo de residencia.
Preparación correcta y optimizada de la masa fundida
Pero esto lo trataremos en otra serie de artículos.
José Ramón Lerma es autor de los libros: 'Libro Manual Avanzado de Inyección de Termoplástico', que tiene como objetivo ser, por un lado, una herramienta para la formación y, por otro, un manual de ayuda para todo el personal de una empresa de inyección de plásticos y, del recientemente editado, 'Scientific Injection Molding Tools. Productividad a través del dominio del proceso'. Ambas publicaciones, comercializadas por Plásticos Universales / Interempresas (libros@interempresas.net), consta de detallados casos prácticos, amplia información de moldeo científico y un ‘pendrive’ con 20 hojas de cálculo y herramientas de SC Molding o Scientific Injection Molding, además de optimización y definición de proceso, lo que lo hacen único en el mercado. El libro Manual Avanzado de Transformación de Termoplásticos ha sido editado y comercializado en inglés a nivel mundial por la editorial Hanser Publications.
Página web sobre Scientific Injection Molding: www.asimm.es
Algunos hemos experimentado o nos han contado alguna anécdota de algún caso donde una inyectora trabajando (normalmente con poliolefinas, PP, HDPE con temperaturas de fusión moderada), sigue trabajando a pesar de poner en 'off' la calefacción del husillo, o en algunos casos con alguna resistencia del cilindro no operativa