Dispositivos de comunicación de alta frecuencia obtenidos mediante fabricación aditiva
M. Carmen Bachiller Martín (1), Aleksandr Voronov (1), Josefa Galvañ Gisbert (2), Dra. Asunción Martínez García (2), Lluc Sempere José (2)
17/06/2024(1) Instituto de Telecomunicaciones y Aplicaciones Multimedia, Universitat Politècnica de València, Camí de Vera, s/n, 46022 València, Tel. 963877000, e-mail; mabacmar@dcom.upv.es
(2) Asociación de Investigación de la Industria del Juguete, conexas y afines (Aiju), Avda. de la Industria,23, 03440 Ibi (Alicante), www.aiju.es, Tel. 965554475, e-mail; prototipos@aiju.es
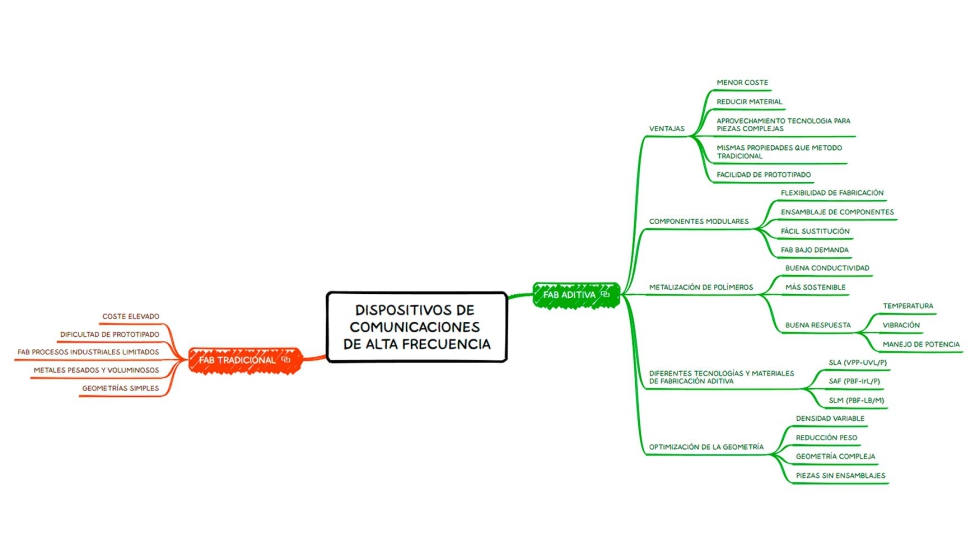
Resumen
Existen numerosas tecnologías para la fabricación de dispositivos de comunicaciones, no obstante, su éxito comercial exige una gran eficiencia en términos de coste y producción masiva junto con unas adecuadas prestaciones en términos electromagnéticos. Por ello, disponer de tecnologías de bajo coste, con altas prestaciones, y que se ajusten adecuadamente a los requerimientos de producción masiva, a la vez que permitan lograr una notable reducción del volumen, peso y consumo de los equipos de telecomunicaciones constituyen un requerimiento del mercado.
La tecnología de impresión 3D es un buen enfoque para fabricar dispositivos de microondas ligeros y baratos. Con esta técnica, el objeto tridimensional se construye depositando y solidificando un material polimérico capa por capa. Esta forma de fabricar permite un espectro amplísimo de topologías volumétricas, además de reducir el tiempo de fabricación, el peso y el costo en comparación con los procesos de fresado sobre metal tradicionales. Para dotar al dispositivo de conductividad eléctrica este objeto podría pasar por un proceso de metalización, para lo cual se necesitarían técnicas más eficientes que las actuales en el mercado, o bien disponer de un material para fabricación aditiva conductor.
1. Introducción
Los dispositivos de comunicaciones requieren de altas prestaciones para su inserción en el mercado. Las técnicas de fabricación actuales tienen unas limitaciones que podrían resolverse mediante el uso de tecnologías de impresión 3D. No obstante, para ello es necesario aplicar innovaciones relevantes en base a los últimos desarrollos tecnológicos, que se podrían centrar en cinco ámbitos principales.
- La fabricación de dispositivos con topologías complejas. La fabricación aditiva abre el abanico de posibles topologías para fabricar, y esto sirve tanto para antenas, filtros, o dispositivos integrados. Asimismo, la posibilidad de metalización selectiva abriría un amplio abanico de aplicaciones en distintas tipologías de antenas, así como soluciones específicas a problemas no resueltos.
- El uso de materiales ligeros. El peso de los dispositivos fabricados mediante métodos tradicionales, frente a los dispositivos fabricados aditivamente con polímeros y posteriormente metalizados, se puede reducir de forma significativa. Además, la cantidad de metal que se utilizan para metalizar sería mínima, frente a todo el metal necesario para fabricar las mismas piezas con métodos tradicionales. En paralelo, minimizaría el uso de material necesario para fabricar estos dispositivos, dada las habilidades de la fabricación aditiva de construcción por capas. Por otra parte, incluso cuando se opta por fabricación aditiva utilizando metales, las posibilidades de topología son infinitas, se utiliza el material meramente necesario y se aporta mayor eficiencia de fabricación a piezas extremadamente costosas de fabricar mediante métodos tradicionales.
- El uso de tecnologías de metalizado novedosas y menos contaminantes y con mejores prestaciones conductoras [1, 2], facilitan el metalizado de un amplio espectro de polímeros utilizados en fabricación aditiva, alcanzan una capa de metalizado estable y resistente, altísima conductividad y permiten adaptar el tipo de acabado a la funcionalidad específica del dispositivo desarrollado y a las condiciones ambientales extremas a las que algunas de estas antenas se ven expuestas. Adicionalmente, no requiere de costosas instalaciones ni reactivos caros, dado que se trata de un método más respetuoso con el medio, de gran eficiencia y seguro.
- La integración de diferentes dispositivos de comunicaciones en una única pieza abre un abanico infinito de posibilidades, puesto que permite la fabricación de un rango amplísimo de topologías en una única pieza, permitiendo integrar filtros con antenas, antenas con elementos de alimentación y desfase, y un largo etcétera. Hasta ahora, los dispositivos de comunicaciones que requerían unas altas prestaciones se fabricaban por separado, y se ensamblaban luego por medio de tornillería, dado que las técnicas de fabricación tradicionales sobre metal así lo requerían.
- La integración de dispositivos de diferentes tecnologías. Un campo de interés creciente en la industria de las comunicaciones es la integración de dispositivos guiados en medios planares, es decir utilizar en el mismo sistema elementos sobre placa de circuito impreso con dispositivos fabricados mediante impresión 3D, pero para ello se utiliza el fresado, cortado, agujereado y metalizado de placas de circuito impreso, con resultados variables. La tecnología especificada en la patente indicada en [1] permite una integración de piezas fabricadas en tecnología de guía de onda con la circuitería impresa, de forma eficiente y sencilla.
Como casos de éxito de la aplicación de esta tecnología a la fabricación de dispositivos de alta frecuencia para comunicaciones se describen a continuación dos de los desarrollos obtenidos en el proyecto Caftam.
2. Antenas multihaz con reflector trasero para bandas sub 6GHz
Los dispositivos de comunicación, en el momento actual, se obtienen generalmente tras la mecanización por control numérico de bloques de metal. Los requerimientos técnicos de diseño para este tipo de proceso de fabricación son limitados, y dan como resultado, formas geométricas simples y un peso considerable que limita algunos tamaños.
Por ello, se planteó la posibilidad de verificar si la fabricación aditiva con materiales poliméricos metalizados alcanzaba la misma funcionalidad que los dispositivos realizados con tecnologías tradicionales.
A tal fin, se ha procedido al desarrollo de antenas de alta frecuencia con resinas poliméricas de altas prestaciones que, posteriormente, se han metalizado con materiales conductores. Con estos dispositivos, se ha comprobado el rendimiento del dispositivo.
Para ello, una vez diseñados y desarrollados, se han medido los parámetros de dispersión de la antena, para conocer a qué frecuencias la antena se comporta como emisor y qué porcentaje del total emite.
Seguidamente, se ha validado su diagrama de radiación con la finalidad de conocer la distribución espacial de la emisión de la antena.
Finalmente, se han realizado las medidas pertinentes para aplicar estas validaciones en ensayos de campo en condiciones reales.
Los resultados obtenidos permiten prever una funcionalidad sistémica de estos dispositivos de telecomunicaciones fabricados mediante tecnologías de fabricación aditiva, que ofrece gran versatilidad en cuanto a forma, tamaño y materiales. Además, estas tecnologías permiten acortar los ciclos de fabricación actuales.
3. Lente de microondas en banda X fabricada enteramente mediante fabricación aditiva
En el mismo contexto, se trabaja en el diseño de una lente de microondas en banda X que utiliza enteramente la fabricación aditiva para su implementación.
La lente consta de 3 partes. La primera parte es una pequeña bocina que actúa como elemento emisor. La segunda es una estructura modular formada por 4 secciones, que, ensambladas, hacen de soporte entre la bocina y la lente. Y, por último, se incluye la propia lente con diferentes densidades en la misma pieza. El objetivo de la lente es aumentar el rendimiento de emisión del conjunto. La bocina es una antena que es capaz de emitir señales de comunicaciones siguiendo un patrón en forma de corazón, es decir, con una dirección preferente pero que también emite en sus laterales. La lente consigue enfocar dicho patrón de emisión en una dirección concreta, haciendo que el conjunto sea más eficiente.
El diseño de la lente consiste en aprovechar las ventajas de la fabricación aditiva para tener sectores del volumen de la lente con diferentes características electromagnéticas gracias a las diferentes densidades de impresión del material. Con esta tecnología se puede implementar cualquier tipo de diseño de lente y utilizar diferentes algoritmos para conseguir las estructuras porosas de densidad variable.
Lo que es realmente novedoso es que, tanto el diseño como la fabricación de la lente se realice enteramente en material polimérico, utilizando la fabricación aditiva, y en concreto combinando dos tecnologías: fusión en lecho de polvo y fotopolimerización en tanque o cuba, empleando varios materiales y acabados.
Dado que la bocina, es decir, el elemento emisor, debe ser un elemento conductor, al contrario del soporte y de la lente en sí, debe ser metalizada para que realice su función. Para ello se utiliza un método de metalización auto-catalítica desarrollado previamente [1].
Esta tecnología de metalización permite un baño uniforme de cobre sobre el polímero utilizando métodos menos contaminantes que el cromado en la metalización tradicional, reduciendo considerablemente el peso del dispositivo frente a una fabricación convencional sobre bloque metálico mediante mecanizado.
4. Resultados
Como resultado de los desarrollos realizados se han alcanzo unas ventajas significativamente mejoradas, entre las que cabe destacar la indicadas a continuación:
- Las posibilidades de fabricar los dispositivos de comunicación de forma modular aporta unas prestaciones significativas a los dispositivos.
- La utilización de polímeros de distintas densidades, permite modificar las propiedades del material sin cambiar el propio material. Por ejemplo, se puede potenciar y canalizar el enfoque en una dirección específica de las lentes microondas en banda X.
- Se utilizan métodos de metalizado medioambientalmente más sostenibles, sustituyendo por ejemplo el uso de cromo hexavalente, que permiten reducir significativamente el coste de producción del dispositivo.
- Las posibilidades de utilizar la fabricación aditiva de metal, con topologías optimizadas, permite reducir significativamente el peso del dispositivo.
5. Agradecimientos
Estos desarrollos se han realizado en el marco de ejecución del proyecto Caftam, Desarrollo de dispositivos de Comunicaciones de Alta Frecuencia utilizando Tecnologías avanzadas de fabricación Aditiva y Metalizado, financiado por la Agència Valenciana d’Innovació (AVI Innest/2022/138), a la cual agradecemos sustancialmente la financiación concedida.
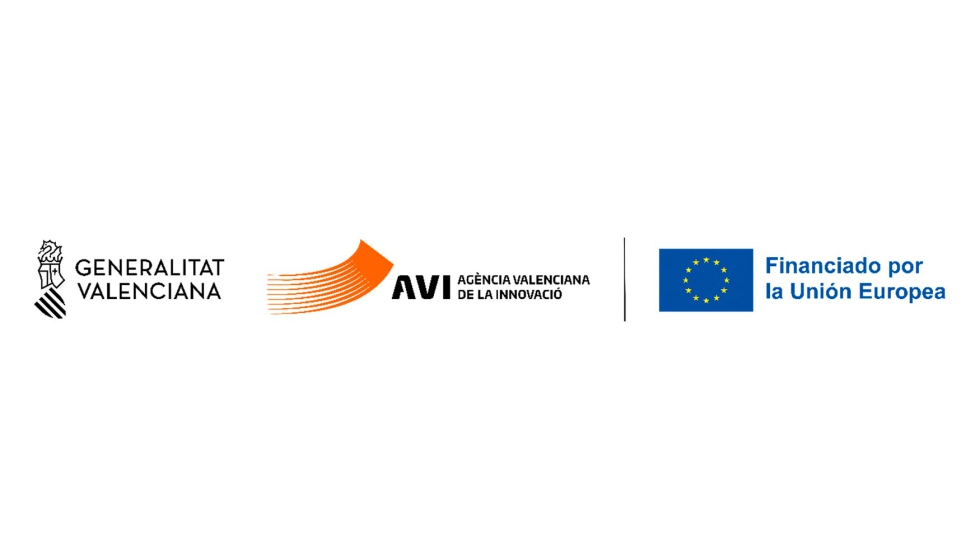
[1] ‘Método de Fabricación de Dispositivo de Microondas Basado en Guía de Onda Vacía Integrada en Sustrato’, nº P201830647
[2] Proyecto: Valorización de un método de fabricación 3D, metalización e Integración de Dispositivos de Alta Frecuencia – ALFREC3D, Agència Valenciana de Innovació, ref. INNVA1/2020/84