Noves tecnologies d'injecció per a la fabricació de peces grans
19 maig 2009
Anem a comentar dos temes relacionats amb l'esmentat: la utilització de materials compostos de fusta i termoplàstics, i l'emmotllament amb ajuda de vapor per a aplicacions concretes.
Emmotllament per injecció de compost de fusta i plàstic
La barreja de fusta i plàstic (WPC), gaudeix ja d'una reputació en el camp de l'extrusió. Actualment està arribant també al sector de la injecció. Molts transformadors tenen una certa resistència a experimentar amb aquest tipus de materials i aquells que l'han fet han trobat una sèrie d'obstacles com ara la qualitat no constant, problemes d'aprovisionament, etc. i en general, majors dificultats en l'ús d'aquests materials respecte als termoplàstics habituals.
No obstant això, recents desenvolupaments en aquests compostos, han millorat significativament la qualitat, consistència i capacitat d'aquest material ecològic. Les últimes generacions de WPC poden ser processades amb ajustaments mínims en el procés, sense modificar l'equip de la màquina.
Els WPC poden produir-se amb diversos tipus de resina, com ara polietilè, polipropilè i poliestirè. Els WPC són només una de les categories de materials emergents que poden ser denominats com 'biocomposites termoplàstics'. A més de la fusta, aquests compòsits poden utilitzar altres fibres naturals com l'escorça de l'arròs, descarts de fibra de palma, i fins i tot lli. Les condicions de transformació a les que anem a referir-nos, es concreten a la barreja fusta / PP, però els principis es poden aplicar en línies generals a la resta biocomposites termoplàstics.
Per què utilitzar els biocomposites?
Hi ha moltes raons per a utilitzar biocomposites per a la producció de diversos productes. Amb el contingut de fibres naturals superiors al 50%, ofereixen als transformadors una opció més ecològica amb respecte als polímers derivats del petroli. A més del 'factor verd', els biocomposites redueixen el risc per al transformador respecte a l'augment del preu del petroli, requereixen menys energia per a la fabricació i proporcionen productes amb una òptima rigidesa estructural, un agradable acabat estètic i un important atractiu per al mercat.
Els biocomposotes fusta / termoplàstic tendeixen a gaudir d'un menor pas pel que fa a les resines no carregades o amb fibra de vidre. Són competitius en termes de cost, característiques mecàniques i desenvolupament del procés pel que fa al PP amb càrrega de talc o de carbonat càlcic. Té a més l'avantatge d'una menor densitat, que redueix el seu cost efectiu i poden ser avantatjosos en els costos de transport per la seva lleugeresa. La seva aplicació és possible en el sector de l'automòbil, construcció, joguines, i altres productes de consum.
Bons candidats per a la utilització d'aquests materials són les peces amb parets gruixudes i aquelles que necessiten una òptima rigidesa i estabilitat dimensional. Tot i que resulten molt apropiats per a peces amb parets gruixudes, els transformadors poden utilitzar també per a parets més fines, augmentant la proporció del termoplàstic a la mescla.
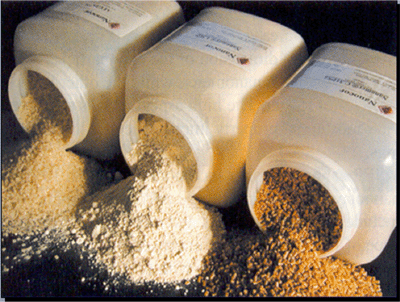
Nota: aquest article està basat en la presentació del treball que Negri Bossi va presentar en les jornades d'innovació que el CEP va organitzar en la passada edició d'Equiplast.
Per assegurar la qualitat del producte acabat, és necessari l'ús de termoplàstics d'alta qualitat de la gransa. Hi ha dos aspectes als quals cal dedicar especial atenció:
- La humitat: la humitat superficial ha de ser inferior al 1,5%, mentre que a l'interior no ha de sobrepassar l'1%. Un grau d'humitat no controlat augmenta la fragilitat del producte acabat.
- La qualitat de la gransa: la gransa ha de ser neta i uniforme en les seves dimensions i forma. No ha d'haver residus de pols, que és una responsabilitat del fabricant del compound.
Per mitjà de la variació dels percentatges dels components de la mescla, es poden variar les característiques del material, per exemple millorant la resistència al desgast dels para-xocs augmentant el percentatge de plàstic o millorar la rigidesa augmentant el percentatge de fusta.
Quan es modela amb la temperatura justa, velocitat i fluxos ben distribuïts, les peces de WPC presenten colors uniformes i una bona dispersió de la fibra, mínimes deformacions, superfícies polides i cap evidència de xuclets. Els dos factors més importants perquè la injecció d'aquest material són l'escalfament i les tensions excessives.
En un principi es pot pensar que la fibra de fusta pot actuar com un inhibidor del flux, i no obstant això és tot el contrari. La barreja de fusta / PP flueix amb facilitat amb baixa velocitat i pressió (igual que el PP amb càrrega mineral). Com a resultat tenim un menor consum energètic. Es poden obtenir millores de productivitat per un menor temps de cicle per un ompliment i refredament més ràpids.
Les temperatures habituals del cilindre van de 170 a 190 ° C en la part posterior, 180-200 a la part central i 200-210 a la zona del broquet.
La pressió depèn de la geometria de la peça, així com dels canals i punts d'injecció. Habitualment es requereix una pressió inferior a la dels materials tradicionals.
La velocitat d'ompliment requereix una atenció especial ja que, si bé és cert que el material flueix fàcilment, és important evitar temps d'ompliment molt baixos perquè el material és sensible a l'estrès. L'escalfament causat per una velocitat excessiva d'ompliment poden causar possibles defectes superficials. S'eliminen fàcilment aquests defectes disminuint la velocitat d'injecció.
Donades les baixes temperatures emprades, el temps de pressió posterior és inferior al dels materials habituals.
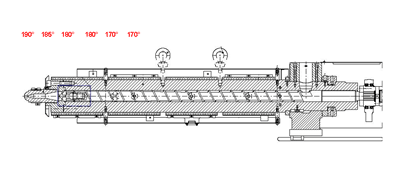
El filtre ha de tenir un orifici de sortida amb una dimensió el més semblant possible al diàmetre de la bugada.
Les peces fabricades amb WPC presenten una finor d'acabat homogeni i un color marró clar. Amb aquest tipus d'acabat és molt fàcil procedir a la seva envernissat o pintura.
Resulten apropiades les màquines d'injecció estàndard per a aquest tipus de transformació, si bé són necessàries algunes precaucions. És crític el control del grau d'humitat i no tenir un escalfament excessiu.
Les recomanacions per transformar aquest material i evitar un excés d'estrès, són:
- El cargol ha de tenir una secció de compressió llarga U un laminació curta.
- Una puntera amb mesclador pot trencar la fibra. Es recomana l'ús d'eixos de tres zones, amb relació L / D entre 20 i 24 i una relació de compressió de 2:1 a 2,5:1.
- Mantenir baixes les revolucions del cargol. Cal preveure un cilindre amb una capacitat de 3-4 injectades.
- Injectar a baixa velocitat.
- Evitar obturadors en el motlle i punteres amb vàlvula en la claveguera.
- Preveure el major nombre possible de punts d'injecció i amb dimensions n inferiors a 2,5 mm.
- Emprar una baixa contrapressió.
- Mantenir una temperatura interna del cilindre inferior als 200 ° C. El material ha de ser escalfat preferentment per conducció i no per fricció.
- Utilitza broquets amb l'orifici igual al diàmetre de la bugada.
- Projectar colades amb canals el més grans possibles, per poder tenir baixes velocitats d'injecció.
- Atenció als canals calents: poden causar un escalfament excessiu de la fibra.
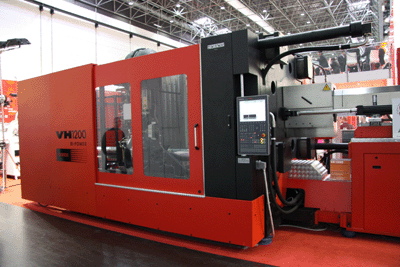
Motlles
Els motlles han de tenir canals amplis de distribució del material amb mínimes obstruccions per evitar tensions en el material. Els punts d'injecció han de ser els més dimensionats. Els punts d'injecció inapropiats produeixen decoloracions i ràfegues en les peces. Preferiblement els punts d'injecció han d'estar situats a les parets gruixudes de la peça. En cas de gruixos fins, el punt d'injecció ha de ser com a mínim 2 / 3 del gruix de la paret. Han d'estar posicionats de manera que no hi hagi zones d'unió de flux o soldadura en zones subjectes a esforços, ja que podrien resultar més fràgils.
Emmotllament amb vapor
La col·laboració amb un important transformador plàstic, ens ha permès desenvolupar en dos anys aquest tipus de tecnologia i fer que pugui ser utilitzada en un elenc important de màquines.
Si bé no es tracta d'una novetat absoluta, aquesta tècnica de moldeig és encara poc coneguda i troba la seva aplicació especial en les carcasses per a televisors.
Substancialment es tracta d'escalfar algunes parts del motlle amb una injecció de vapor a una temperatura propera als 180 º C, utilitzant canals RHCM, per passar immediatament de la fase d'ompliment a un brusc refredament d'aquestes mateixes parts.
El resultat és una lluentor molt particular, amb efecte mirall de la superfície a PC / ABS i amb la total eliminació de les antiestètiques línies d'unió .. La incidència sobre el cicle de la injectora varia entre el 10% al 30% en funció de la geometria de la peça.
Aquesta tecnologia està suplantant a la fabricació de mobles de TV, a la fase d'acabat i pintura, amb evidents avantatges tant en cost com d'impacte mediambiental.
El vapor està subministrat per dos potents equips capaços de generar respectivament 1600 i 2000 kcal / h, mentre que el sistema de control (en les màquines Negri Bossi), està integrat gràcies a una innovadora solució.
Gràcies a la col·laboració amb aquest transformador, s'ha desenvolupat un nou programari de gestió per a les electrovàlvules de comandament que permeten reemplaçar completament les voluminoses centralinas actualment situades al costat de la injectora.