Álabes de turbina y compresor más seguros y eficientes
Un motor turbofán tiene muchas partes: en la parte delantera, el ventilador aspira el aire y lo dirige hacia el compresor, que está compuesto por varias aspas dispuestas en fila y cuyo tamaño disminuye hacia el final de un tubo de estrechamiento. Mediante un movimiento de rotación, el aire de succión se comprime hasta una trigésima parte de su volumen, que a su vez comprime y calienta el gas. A continuación, el aire se introduce en la cámara de combustión, donde se mezcla con queroseno inyectado y se quema. La energía resultante impulsa la turbina de alta presión donde están instalados los álabes de la turbina que accionan el compresor. La turbina de baja presión aguas abajo también se pone en marcha utilizando esta energía. La turbina de baja presión está formada por palas más largas y está conectada directamente al ventilador. La turbina asegura que el ventilador gire. El ventilador no sólo aspira el aire hacia el interior, sino que también pasa por el compresor y la turbina. El aire frío, que pasa por el interior, genera la mayor fuerza propulsora. El proceso en el interior del motor sólo garantiza que el motor siga funcionando. Así que el flujo de gases de escape produce el 20% de la propulsión y el ventilador, el 80%. Tanto las turbinas como los álabes de los compresores están sujetos a altas temperaturas y presiones. Por lo tanto, los fabricantes han implementado estrictas regulaciones para los métodos de producción y procesamiento utilizados.
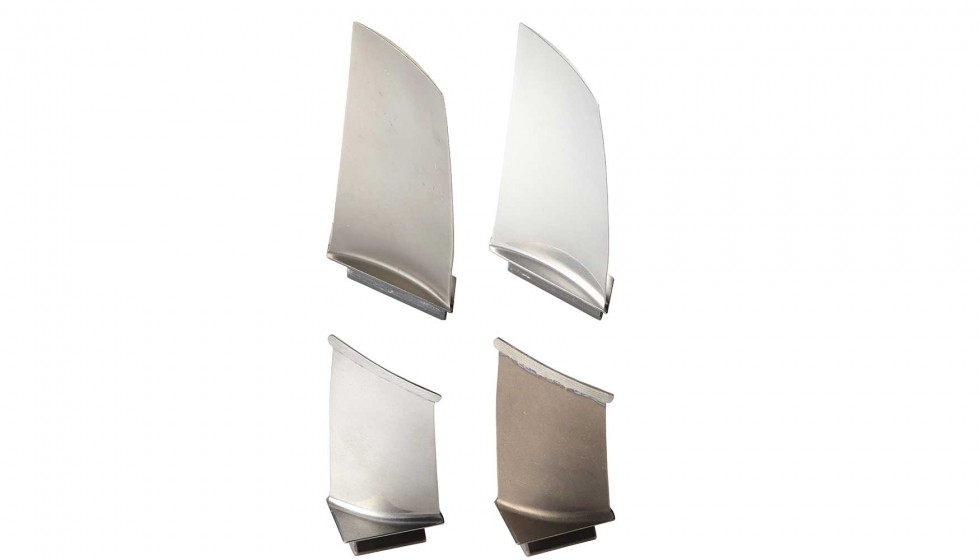
Las palas de los motores utilizados en la industria aeroespacial suelen estar fabricadas con materiales difíciles de mecanizar y con una baja tolerancia que se debe cumplir para obtener el caudal de aire ideal y la máxima resistencia al desgaste. Estos componentes están expuestos a temperaturas extremas de hasta 1.000 °C. Esto significa que las superficies de las palas también tienen que ser de la más alta calidad y estar óptimamente adaptadas a las condiciones del motor. Otec ha desarrollado un proceso especial para mejorar la eficiencia y seguridad de las palas del motor y producir menos defectos.
El alisado de la lámina de aire, es decir, del cuerpo de la pala, tiene un impacto positivo; dependiendo del resultado requerido, la superficie puede alisarse a valores de hasta Ra < 0,2 µm en pocos minutos, lo que aumenta la eficiencia de la pala. El material se retira de manera uniforme y sólo se extrae una cantidad mínima de la superficie. La reparación de los bordes de ataque y de salida con redondeo de precisión puede reducir la cantidad de piezas rechazadas. El proceso de mecanizado previo, por ejemplo, el chorreado, puede dañar estos bordes. El método Otec permite redondearlas a un radio determinado y, por lo tanto, repararlas. El proceso de redondeo es muy preciso y requiere una mínima extracción de material.
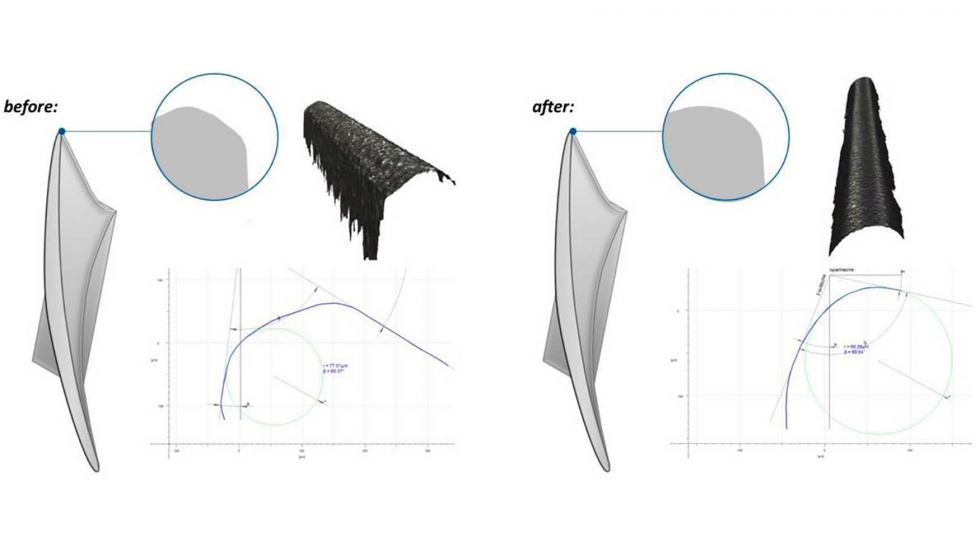
El alisado de la lámina de aire, es decir, del cuerpo de la pala, tiene un impacto positivo; la superficie puede alisarse a valores de hasta Ra < 0,2 µm en pocos minutos, lo que aumenta la eficiencia de la pala. El material se retira de manera uniforme y sólo se extrae una cantidad mínima de la superficie.
Resultados después de redondear los bordes de las cuchillas en el proceso de acabado del chorro
El desbarbado de la raíz ayuda a mejorar la seguridad al evitar que la cuchilla quede atrapada en el disco. El tratamiento de la superficie no sólo prolonga la vida útil de las cuchillas, sino que también aumenta su eficacia. También es la preparación ideal para el recubrimiento de los componentes. El alisado y redondeo de las palas del motor es posible en una sola operación gracias al innovador proceso de acabado en continuo de Otec. En el proceso de acabado de chorro, las cuchillas se sujetan a la máquina y se bajan a un contenedor de abrasivo. El procesamiento se lleva a cabo tanto por la rotación del contenedor como por el movimiento de la pieza de trabajo en el flujo de medios. El flujo hacia las cuchillas en la máquina es cronometrado, es decir, el ángulo de alineación de la pieza de trabajo cambia a intervalos frecuentes. Esto significa que el procesamiento puede ser alineado con precisión a puntos específicos de la pieza de trabajo, logrando una superficie lisa y un redondeo preciso sin alterar la forma de la hoja. Un beneficio importante del proceso de Otec son los tiempos de mecanizado ultracortos en comparación con los procesos convencionales. Dependiendo del tamaño y del estado inicial de la pieza de trabajo, el tratamiento de la superficie de las palas del motor dura entre 2 y 20 minutos. Como las cuchillas se sujetan individualmente, no se producen daños en la superficie de la pieza de trabajo. Todos los pasos de procesamiento se pueden llevar a cabo en una sola máquina. El sistema de acabado de flujo SF-5 puede procesar hasta cinco palas de motor a la vez, lo que garantiza un alto rendimiento y eficiencia de costes. Las pruebas realizadas después del procesamiento de Otec muestran resultados positivos para el control de la tensión residual, la resistencia a la fatiga y la fluorescencia.
Las palas de motor no sólo se utilizan en la industria aeroespacial, sino también en el sector energético. El tratamiento superficial de las palas de las turbinas de energía también se puede llevar a cabo en máquinas Otec.