Electropulido: tecnología clave para mejorar la vida útil de los componentes aeronáuticos
Dra. Belén García, Dra. Gemma Vara. Cidetec Surface Engineering. Parque Científico y Tecnológico de Gipuzkoa (gvara@cidetec.es)
11/03/2019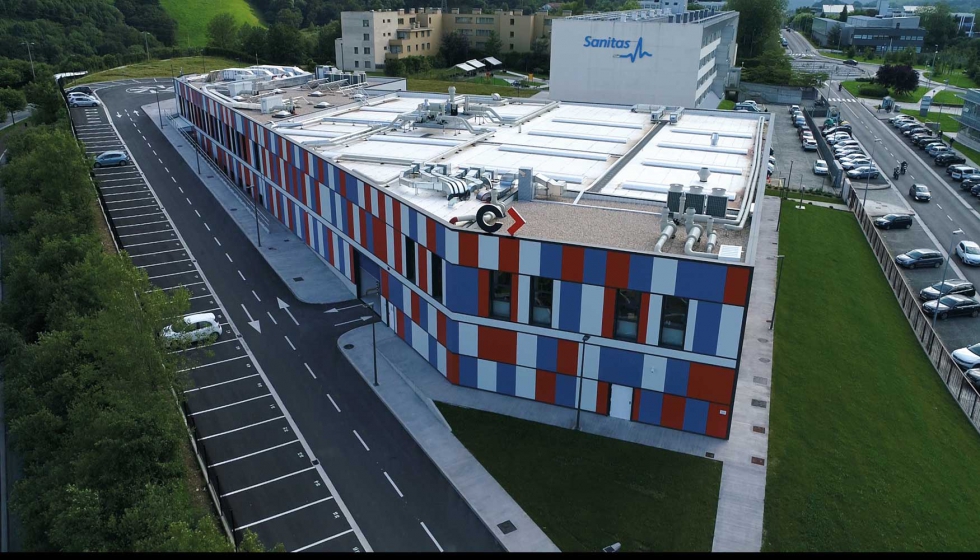
Instalaciones de Cidetec Surface Engineering.
En una escala macroscópica, el contorno de una superficie electropulida se puede considerar como una serie de picos y valles. La profundidad de los mismos y la distancia entre los picos dependen de los métodos utilizados para producir la superficie. En una escala microscópica, la superficie es aún más compleja, con pequeñas irregularidades sobrepuestas a los picos y valles. Con el fin de producir una superficie verdaderamente lisa, ambos tipos de irregularidades (macroscópicas y microscópicas) deben ser eliminadas. Así, las funciones de un proceso de pulido ideal se pueden distinguir como:
- Alisado: eliminación de las irregularidades a gran escala (tamaño superior a 1 µ).
- Abrillantado: remoción de pequeñas irregularidades de un tamaño inferior a 0,01 µ.
A día de hoy, es posible electropulir una gran variedad de materiales y el proceso se emplea principalmente para sustituir o disminuir las etapas de pulido mecánico y para aportar a las superficies propiedades estéticas, facilidad de limpieza, incremento de la resistencia a la corrosión y alivio de tensiones.
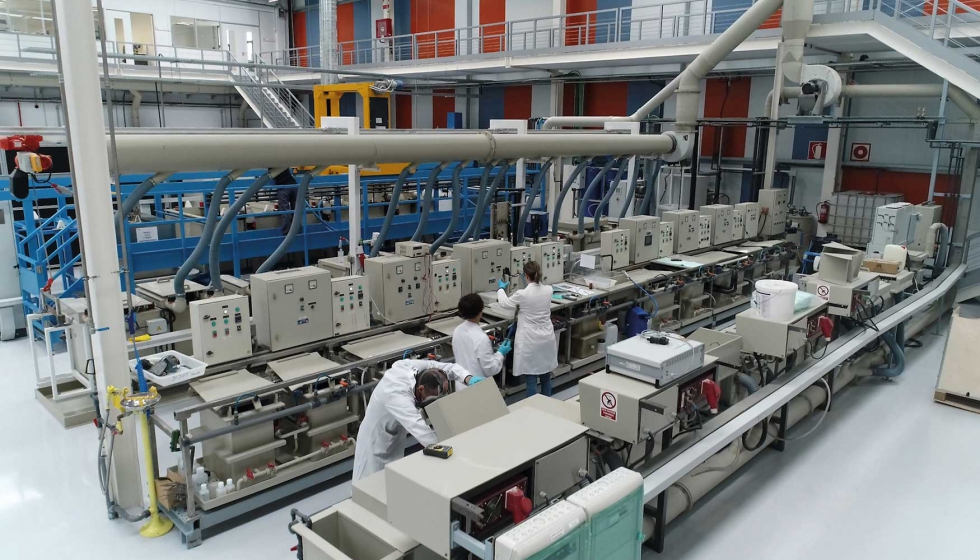
Plantas piloto Cidetec Surface Engineering.
Comparación entre el pulido mecánico y el electropulido
La preparación mecánica de las superficies se puede dividir convenientemente en dos etapas: el esmerilado (usando técnicas abrasivas para producir una superficie razonablemente lisa y plana) y el pulido (usando abrasivos finos sobre poleas para dar una superficie lisa y brillante). Se han realizado considerables esfuerzos para investigar la estructura de las superficies metálicas preparadas por estos métodos y se ha establecido perfectamente que conducen a obtener una zona severamente deformada cercana a la superficie. Esta zona tiene propiedades diferentes a las del metal de base y se produce fundamentalmente por un proceso de fluencia, esto es: bajo la intensa acción mecánica del pulido, el material de los picos es obligado a fluir para rellenar los valles. Esta capa superficial recibe usualmente el nombre de “capa de Bielby”, en honor a su descubridor, y tiene un espesor de varias micras, espesor que se incrementa con la intensidad del pulido. La estructura resultante es prácticamente amorfa y contiene inclusiones de óxidos del metal de base y compuestos utilizados en las pastas de pulir. Se comprende entonces que las propiedades físico-químicas de la capa superficial obtenida por pulido mecánico son distintas a las del metal subyacente, originando tensiones mecánicas que, en determinadas condiciones, pueden dar lugar a procesos de corrosión.
El electropulido funciona básicamente debido que, al disolverse el metal bajo la circulación de corriente, se forma una capa viscosa de productos de la disolución, la cual se va difundiendo lentamente en el baño electrolítico. El espesor de esta capa no es constante, siendo mayor en los valles y, como su resistencia eléctrica es superior a la de la solución de electropulido, conduce a una disolución preferencial de los picos y a una nivelación de la superficie.
Electropulido en el sector aeronáutico
Como se ha comentado anteriormente, el electropulido es un proceso presente en el sector aeronáutico para la mejora de las propiedades superficiales de diversos componentes fabricados en diferentes tipos de materiales:
- Componentes aeronáuticos comúnmente electropulidos: soportes, bridas, casquillos, engranajes, boquillas, reflectores, tuercas de bolas, husillos de bolas, cierres, carcasas, resortes, etc.
- Aleaciones que pueden electropulirse con éxito: aceros inoxidables, aceros endurecidos, aceros de herramienta, aceros al carbono, aleaciones de cobre, aluminio, titanio y aleaciones de níquel.
Los beneficios que aporta el electropulido, con respecto a otros procesos de acabado superficial como el pulido mecánico y/o manual, son diversos y van desde una eliminación homogénea de rebabas y aporte de ultra-limpieza, hasta una mejora de las propiedades funcionales como resistencia a la corrosión y a la fatiga. A continuación se detallan los beneficios del empleo del proceso de electropulido sobre componentes aeronáuticos.
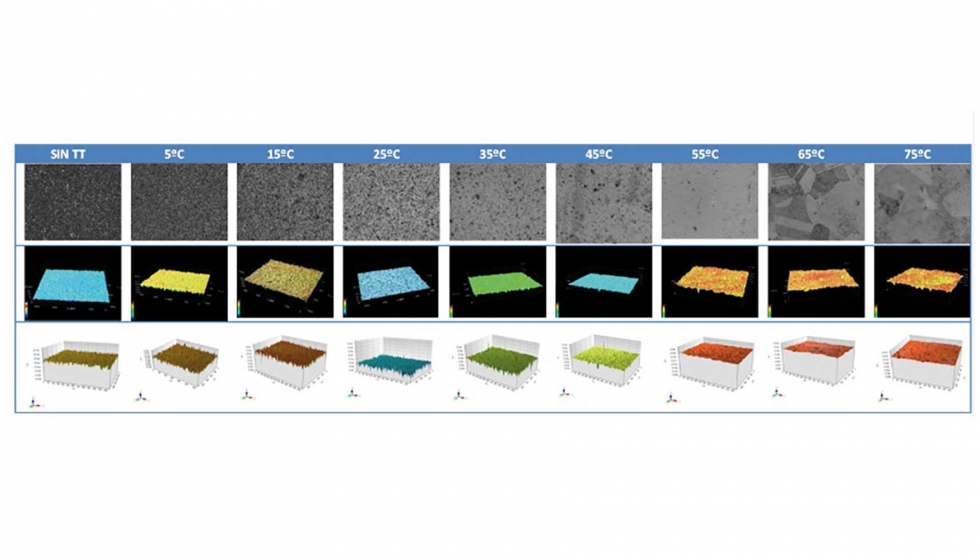
Mejora de las propiedades de los componentes aeronáuticos electropulidos
A continuación, se detallan los beneficios del empleo de procesos de electropulido sobre componentes aeronáuticos:
- Eliminación homogénea de rebabas
El electropulido es uno de los procesos superficiales más comunes para mejorar la calidad general de componentes metálicos empleados en aeronáutica. Estos componentes pueden ser accesorios, boquillas, carcasas y conjuntos soldados que deben ser fabricados de manera precisa además de tener un implacable acabado superficial, libre de rebabas y contaminantes, para asegurar un correcto rendimiento. El proceso de electropulido es una solución efectiva para eliminar rebabas de manera homogénea manteniendo la integridad de los componentes. Además, mediante este proceso es posible eliminar una cantidad marginal de metal manteniendo las esquinas afiladas.
- Mejora de la resistencia a la corrosión
Uno de los beneficios del electropulido es la capacidad de proporcionar una mayor resistencia a la corrosión a las superficies de acero inoxidable tratadas. Durante el proceso se elimina una fina y uniforme capa de material superficial y se genera una capa pasiva enriquecida en Cr que aumenta la resistencia a la corrosión de estos materiales. Además de los aceros inoxidables, se ha reportado la mejora de la resistencia a la corrosión de otro tipo de materiales como aleaciones de titanio y de aluminio tras el proceso de electropulido.
- Mejora de la resistencia a la fatiga
El beneficio más significativo del electropulido aplicado a componentes aeronáuticos es la mejora de la vida a fatiga. Los componentes metálicos presentes en helicópteros y aviones deben soportar estrés y corrosión durante un largo periodo de uso y deben cumplir las exigentes especificaciones de ciclo de vida demandadas por el sector. Los defectos residuales provenientes de los procesos de fabricación de los componentes, bien sean procesos de mecanizado o de estampación, generalmente en forma de micro-cracks o picaduras, pueden ser puntos de iniciación y propagación de grietas y de corrosión. La eliminación de estos defectos en la superficie de los componentes metálicos mediante el proceso de electropulido mejora de manera significativa la vida a fatiga de este tipo de piezas aeronáuticas.
- Microacabado superficial
En todos los sistemas aeroespaciales los líquidos y los gases deben estar disponibles de manera inmediata y fluir fácilmente a través de tubos, tuberías y mangueras. Además en operaciones donde el contacto superficial metal-metal es crítico, la mejora de la superficie metálica también es esencial. En todos estos compontes, el empleo del electropulido como proceso de micro-acabado superficial proporciona una serie de ventajas frente a otro tipo de procesos mecánicos o de pulido manual. El electropulido es preciso y disuelve una capa uniforme de material a lo largo de toda la superficie de la pieza. Esto ahorra tiempo y recursos mediante la creación de un acabado uniforme en piezas con geometrías relativamente complejas.
- Ultralimpieza
El acabado superficial es importante en aplicaciones aeronáuticas, pero también es crucial el nivel de contaminación y limpieza superficial. El mecanizado y las subsecuentes operaciones de acabado secundarias introducen partículas, virutas y otros contaminantes superficiales en las piezas. Los fallos prematuros de componentes debidos a la presencia de material adicional pueden ser críticos en este sector. El electropulido es un proceso efectivo para eliminar tanto los contaminantes superficiales como las partículas exógenas embebidas en las superficies.
- Acabado de componentes producidos por fabricación aditiva
Durante los últimos años, el sector aeronáutico está experimentado en las aplicaciones más avanzadas de la tecnología de fabricación aditiva debido a la flexibilidad y adaptabilidad que posibilitan la producción de piezas con características específicas. La fabricación aditiva se refiere a un grupo de tecnologías que implican un proceso de unión de materiales a partir de datos de un modelo en 3D, usualmente capa sobre capa, a diferencia de las metodologías de fabricación sustractiva donde se elimina material de las zonas en las que no hace falta. La fabricación aditiva es una herramienta extraordinaria que ofrece la posibilidad de fabricar estructuras rígidas y ligeras, con geometrías complejas y aplicaciones interesantes para este sector. Sin embargo, una de las desventajas de estas tecnologías es el mal acabado superficial, una excesiva rugosidad, de los componentes fabricados. Esto implica que, para muchas aplicaciones, principalmente de tipo mecánico, sea necesario realizar un posprocesado de acabado superficial. Por tanto, existe una necesidad de emplear post-tratamientos rápidos y económicos sobre componentes de altas prestaciones mecánicas fabricados por tecnologías de fabricación aditiva para reducir su rugosidad superficial. Actualmente se barajan principalmente dos tipos de tratamientos de superficie: mecánicos (pulidos, granallado, vibrados) y EP siendo la combinación de ambos la que mejores resultados está proporcionando en cuanto a disminución de rugosidad, estética y limpieza superficial.
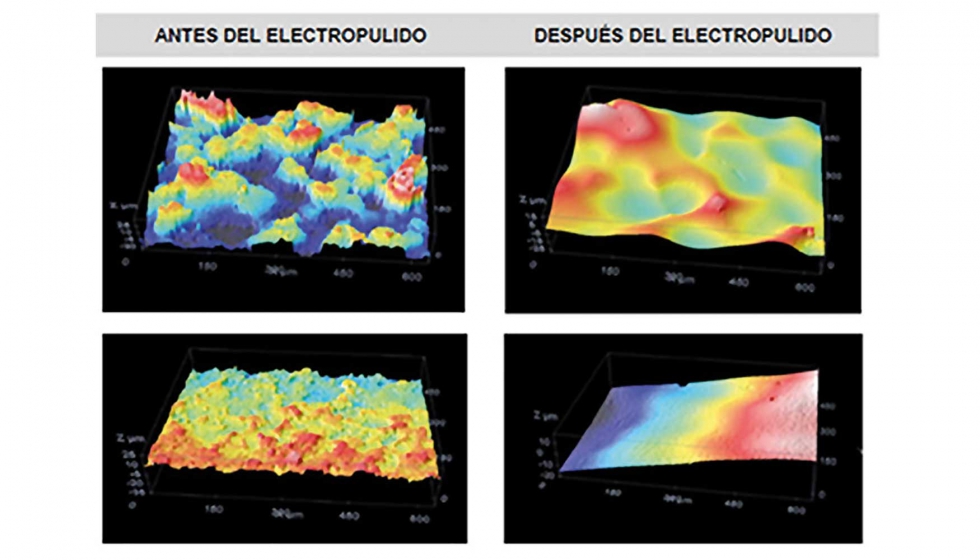
Conclusiones
El electropulido es un proceso ampliamente conocido y utilizado industrialmente desde hace décadas y que sigue vigente debido a los beneficios que aporta a sectores punteros como el aeronáutico. El electropulido, como acabado superficial de componentes metálicos aeronáuticos, permite obtener superficies uniformes, brillantes, libres de defectos y fisuras superficiales, permitiendo disminuir el coeficiente de fricción y mejorando la apariencia estética de las piezas y componentes. Además, se obtienen superficies ultralimpias en las cuales la suciedad no se adhiere, permitiendo la eliminación de impurezas. Por otro lado, dado que generan superficies muy limpias y de rugosidad controlada. Otro efecto clave del electropulido es que mejora el comportamiento a fatiga ya que elimina las anomalías superficiales que son las causantes de los fallos prematuros y la reducción del tiempo de vida en uso. Además, este proceso mejora la resistencia la corrosión de materiales como el acero inoxidable ya que favorece la generación de una capa pasiva enriquecida en Cr en la superficie del material electropulido. Asimismo, el electropulido es el proceso más prometedor para el acabado superficial de componentes producidos por procesos de fabricación aditiva, procesos con cada vez más presencia en el sector aeronáutico.
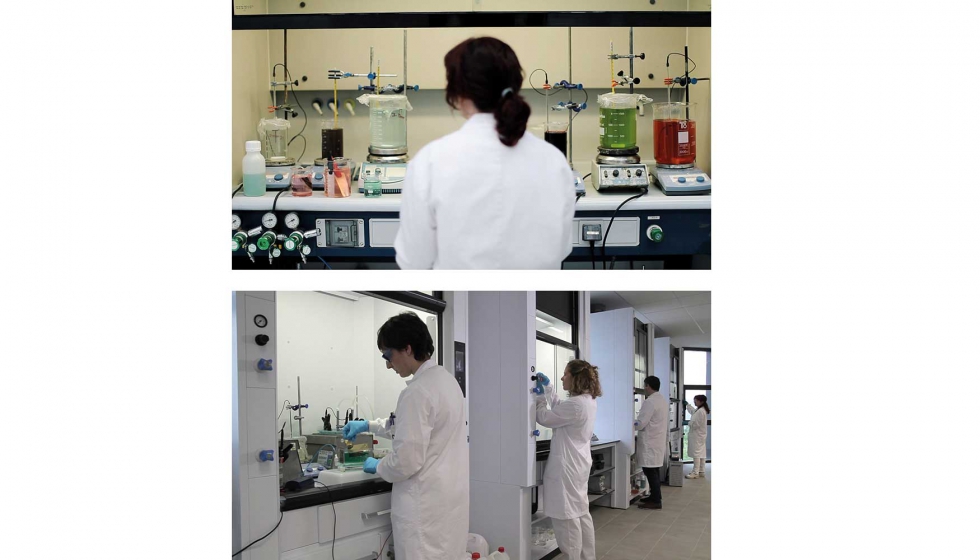
Cidetec Surface Engineering, como Centro Tecnológico especializado en el campo de la ingeniería de superficies, lleva muchos años dedicado al desarrollo y aplicación de procesos de electropulido para la mejora de las propiedades superficiales de diferentes tipos de metales y aleaciones. Cidetec dispone de laboratorios químicos y de caracterización altamente equipados para el desarrollo de nuevos procesos de electropulido. Asimismo, las plantas piloto de sus instalaciones que ocupan alrededor de 4000 m2 permiten realizar el escalado en condiciones semi-industriales de los procesos desarrollados en laboratorio. En los últimos años Cidetec ha colaborado con empresas y centros especializados en fabricación aditiva aportando su conocimiento en el desarrollo de procesos de EP para estos componentes metálicos, especialmente para aleaciones de titanio, acero e inconel. En particular las principales líneas de investigación en las que Cidetec se encuentra inmerso en la actualidad son:
- Selección/desarrollo de electrolíticos adecuados para electropulir nuevas aleaciones metálicas de modo eficiente, utilizando productos químicos amigables con el medioambiente.
- Adecuación de los parámetros del proceso para hacer frente a la distribución heterogénea de rugosidad superficial proporcionada por tecnologías de fabricación aditiva.
- Diseño de nuevo equipamiento/utillaje que se adapte a los nuevos conceptos de piezas fabricadas por las nuevas tecnologías industrales.
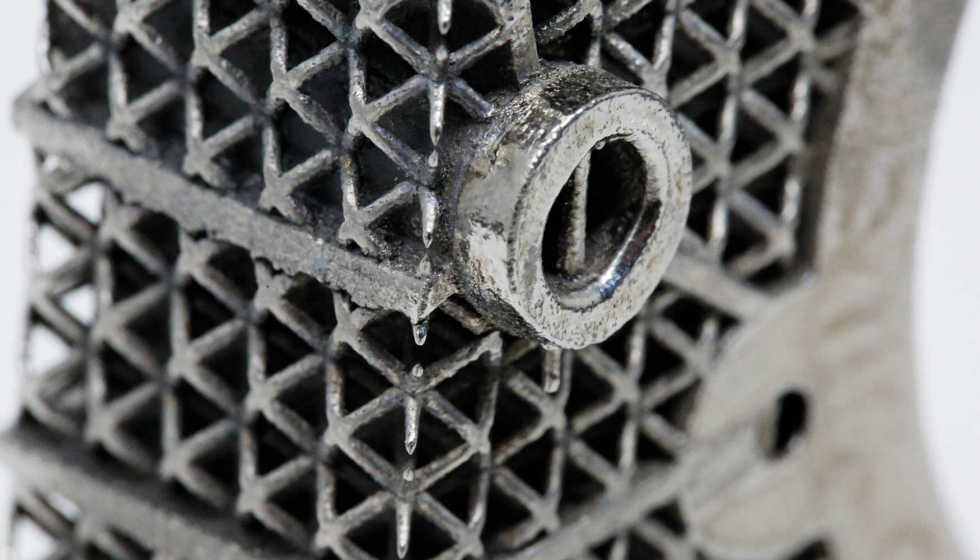
Ejemplo de pieza de AM posprocesada por Cidetec Surface Engineering.
Referencias
http://go.ableelectropolishing.com/electropolishing-aerospace-industry
M.B. García-Blanco; E. Butrón; G. Vara. “Challenges and opportunities in next generation of electropolishing surfaces”. Surface Engineering. 31 - 4, pp. 397 - 398. Maney, 30/06/2015.
M.B. García-Blanco; O. Garrido; G. Vara; J.A. Díez. “Electropolishing of Ti6Al4V alloy fabricated by Selective Laser Melting”, Proceedings of the Twenty Ninth International Conference on Surface Modification Technologies, June 10-12, 2015, Copenhagen, Denmark, ISBN: 978-81-926196-2-0
M.B.García-Blanco, M.Diaz-Fuentes, E. Espinosa1, A.M. Mancisidor, G.Vara, Study of the effect of EP, blasting and laser treatments on the surface roughness of Ti6Al4V alloy fabricated by SLM at different build angles, Proceedings of the EURO PM18 Congress (Bilbao, October 2018)