La mayor línea de conservación en la industria de la construcción naval se va a Finlandia
Tres años después de la puesta en marcha de la línea de conservación en ND Coatings, un socio estratégico del astillero Meyer Werft de la ciudad de Papenburg en Alemania, Rösler ha entregado una segunda línea para el astillero Meyer Werft en Turku, Finlandia. Se trata del mayor proyecto de equipamiento que jamás haya emprendido Rösler.
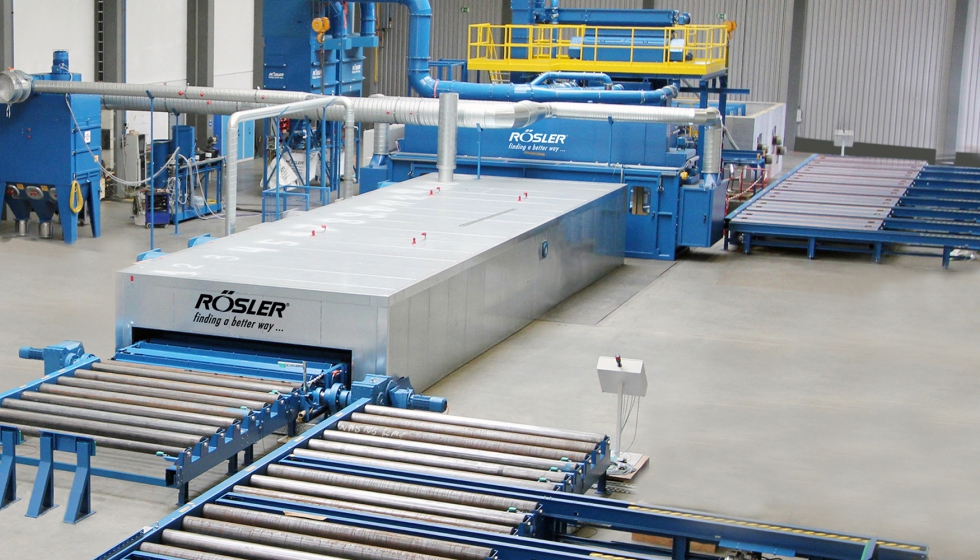
La adquisición del astillero de Turku en 2014 fue un hito estratégico para la familia Meyer. Coincidió con una inversión importante en equipamiento de última generación para la producción de cruceros. Esto incluía una línea de conservación con estaciones de nivelación para llantas de acero con bulbo, perfiles de acero planos y placas de acero, todo diseñado y construido por Rösler. Un factor clave para que el cliente se decidiera por el concepto de Rösler fue la alta productividad y fiabilidad de la línea de conservación que Rösler le había suministrado a ND Coatings, el socio estratégico del astillero de Meyer Werft en Papenburg para la protección contra la corrosión, el aislamiento y el tratamiento de la superficie. Esta es una de las líneas de conservación más modernas y ecológicas del mundo.
Línea totalmente automática incluyendo dos granalladoras
La línea de conservación y nivelación y granallado de 225 metros de longitud fue diseñada de forma totalmente personalizada para las necesidades de Meyer Turku y consiste en un sistema interconectado de transporte de la pieza de trabajo, precalentadores, dos granalladoras independientes, sistemas de nivelación apropiados para vigas y planchas y una estación de pintura y secado. Todos los componentes del sistema están conectados entre sí e integrados en el sistema de control de producción del astillero. A la llegada de las piezas de trabajo a la entrada de la línea, el sistema de control determina automáticamente si las piezas de trabajo deben ser limpiadas, granalladas, niveladas, de qué color se deben pintar o si deben someterse a un proceso parcial. El sistema de control de producción recibe información sobre los parámetros de proceso de cada uno de los componentes acabados, lo que permite una documentación completa y precisa. Los perfiles de acero que se guardan en el exterior se cubren de óxido o de cascarilla debido al proceso de formación de los rollos. Dependiendo de la estación del año, es posible que se cubran también de nieve o hielo. El sistema de transporte toma siete piezas de trabajo en un solo lote y las pasa por la estación de limpieza/precalentamiento para eliminar el hielo —si fuera necesario— a razón de 3 m/min. En la fase siguiente, las piezas de trabajo se someten a una limpieza por granallado en una granalladora de rodillos tipo RRB 16/5. Cuatro turbinas Gamma 400 G con una potencia de 15 kW cada una garantizan un resultado óptimo del granallado. Están montadas en el techo y el suelo de la cabina de granallado fabricada en acero al manganeso. El forro de acero al manganeso es fácil de sustituir y ofrece una protección adicional contra un desgaste prematuro. Después de pasar por el cepillo de granallado y la estación de soplado, lo perfiles se alinean en una fila única para pasar por los siguientes sistemas de nivelación a una velocidad de 30 m por minuto. Los perfiles defectuosos son descartados inmediatamente por el sistema. Los perfiles que cumplen con las especificaciones se agrupan en lotes en la siguiente estación, que permite lotes con un ancho de hasta 3.200 mm.
Las planchas de acero, almacenadas en exterior bajo techo, pueden ser de hasta 100 mm de espesor, 3.300 mm de anchura y 24.000 mm de longitud. Una grúa pórtico con electro imán las levanta y las coloca en una posición centrada sobre la estación de carga del transportador de rodillos, es decir la línea principal de transporte. Un sensor monitoriza todo el proceso de carga. En la primera etapa, las placas de acero pasan por una estación de soplado para retirar agua y otros restos, a lo que sigue una fase de precalentamiento. A partir de ahí, entran en la granalladora de rodillos RRB 35/6-HD a una velocidad media de 5 m (16 pies) por minuto. La granalladora está equipada con ocho (8) turbinas de alto rendimiento tipo Rutten Gamma 400, con una potencia instalada de 37 kW cada una. Para minimizar la velocidad de desgaste y facilitar el mantenimiento, la cabina de la granalladora está fabricada en acero al manganeso y forrada con placas anti-desgaste de acero al manganeso fáciles de sustituir. Después de retirar los residuos del granallado con un cepillo y una estación de soplado, las piezas de trabajo se someten a un proceso de nivelación. Para permitir la canalización de lotes de perfiles granallados hacia la línea principal de transporte para su pintado, se detiene automáticamente la carga de placas en crudo en el momento en que un lote de perfiles acabado está en espera. Dichos lotes pasan por varias estaciones, incluso se permite que los perfiles sean precalentados y se sometan a un segundo granallado.
Pintado con pulverización mínima y recuperación de disolvente
El proceso de pintado al final de la línea se produce con pinturas de dos componentes con base disolvente de dos colores, que se mezclan al instante según sea necesario. La pintura se aplica mediante pistolas desde arriba y desde debajo de las piezas de trabajo. Para reducir el pulverizado al mínimo, las pistolas se controlan mediante un sistema de reconocimiento de la pieza de trabajo y medición del desplazamiento. El disolvente utilizado para el aclarado y limpieza se reacondiciona y recupera en una planta de procesado que permite la recuperación y reciclado del 98% del consumible. La secadora ha sido diseñada para asegurar una curación rápida y óptima de la pintura. Está equipada con quemadores de gas y espitas de recirculación en el techo y el fondo de la cabina. En la última fase, las planchas y los perfiles se clasifican en diferentes estaciones de descarga según se determine en el sistema de control de producción.