Granalladoras 4.0 gracias a la innovación de OMSG
La Industria 4.0 está presente en el entorno industrial y cada vez aumenta la prioridad por formar parte de ella y tener los medios que permitan ser más competitivos en esta nueva era. Por ello, Euromaher presenta uno de los más novedosos avances de OMSG-Banfi que posicionarán sus máquinas a la cabeza de la era 4.0.
Desde OMSG, pionero en el mundo de las granalladoras, equipos automáticos de granallado y shot-peening, ofrecen la posibilidad de crear o adaptar sus máquinas a lo que se conoce como Industria 4.0. Se trata de máquinas automáticas, intuitivas y automatizadas con mantenimiento predictivo integrado. Además, el sistema de granallado se comunicará con las otras plantas de la empresa y con el sistema de supervisión.
OMSG ha creado el paquete Evolution&Service, donde avanza el modo de convertir las granalladoras en máquinas perfectamente integradas en la Industria 4.0 mediante un conjunto de dispositivos que otorgarán a la máquina el estado de automatización, el diagnóstico en tiempo real y la asistencia en mantenimiento.
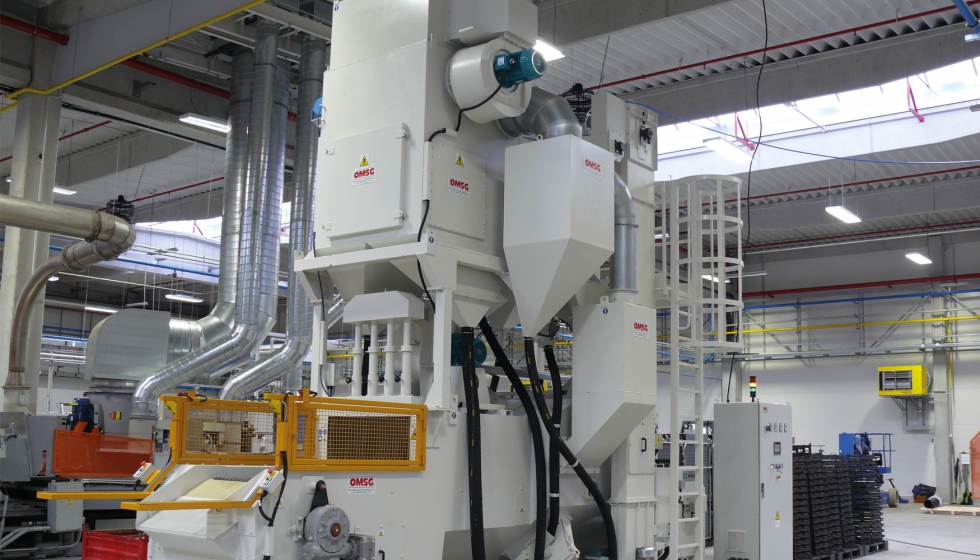
Gestión del sistema mediante PLC e interfaz gráfica HMI pantalla táctil
El uso de este dispositivo permite el procesamiento de las señales provenientes de los sensores instalados en el sistema. El usuario puede procesar y memorizar parámetros, cada uno relacionada con una cierta selección de variables. Además, el sistema puede realizar diagnósticos precisos en los periféricos en tiempo real, para garantizar un funcionamiento correcto y gestionar las anomalías en función del nivel de gravedad. Es un sistema más simple e intuitivo para el operador que tiene la posibilidad de interactuar con otros sistemas y con el sistema de supervisión.
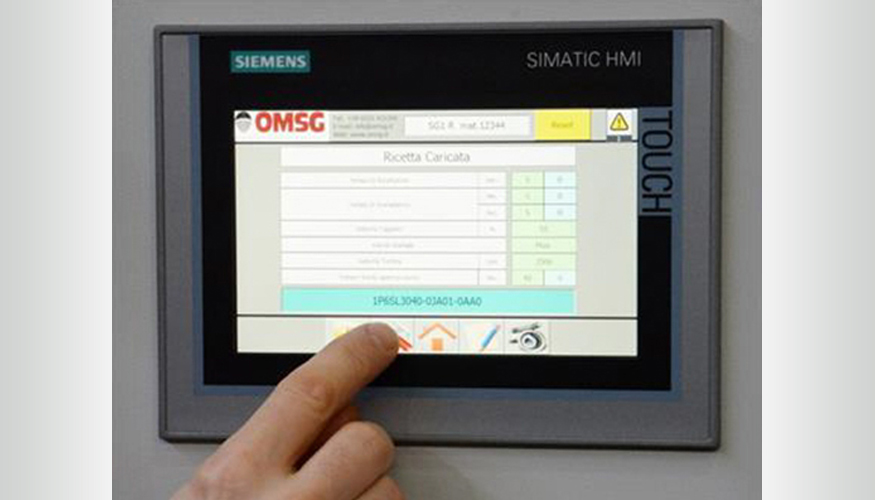
Dispositivo de teleasistencia
El dispositivo de teleasistencia permite el acceso remoto, por técnicos de OMSG, a las funcionalidades del sistema, como si estuviese operando directamente en el PLC. Así, en tiempo real, se puede realizar un diagnóstico eléctrico / electrónico de la máquina granalladora, una identificación precisa de la anomalía y la activación de acciones correctivas apropiadas.
Verificación amperométrica
Consiste en un sistema de monitorización continua para medir la corriente absorbida por cada turbina. En caso de excederse, el sistema puede establecer las acciones más adecuadas, tales como: activar una alarma, detener el sistema o ajustar el flujo abrasivo (si las válvulas RCD están instaladas conjuntamente).
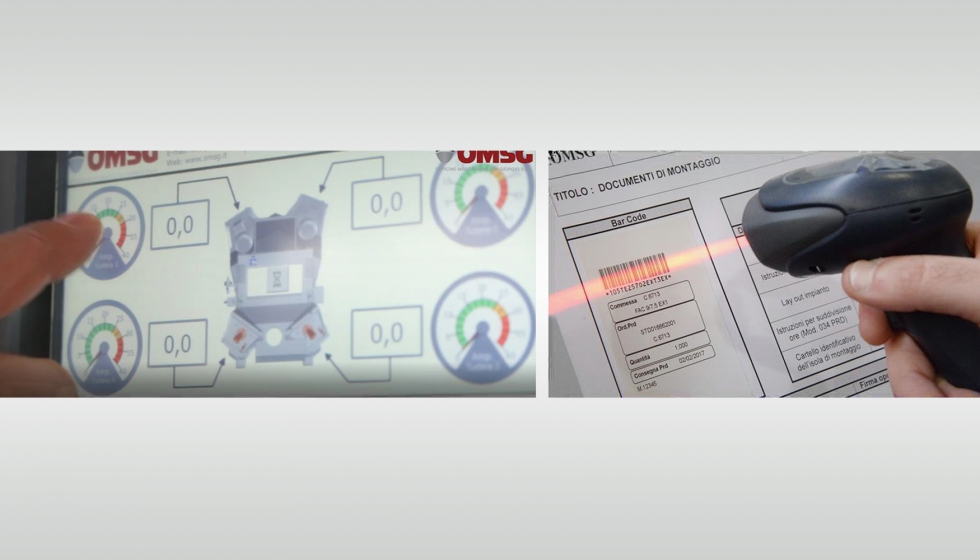
Lector de código de barras (código de barras)
Lector de código de barras para la adquisición rápida del número de identificación de la pieza a tratar. El código adquirido se utiliza para seleccionar, rápidamente, una pauta de trabajo preestablecida, minimizando las operaciones manuales y asegurando la exactitud de los datos adquiridos.
Módulos de E / S a bordo
Ofrecen funciones adicionales para el procesamiento de señal en el campo, tales como: sensores, interruptores de límite, válvulas de solenoide, etc. con opciones de diagnóstico extendidas en comparación con la versión estándar. Con el control de todos los dispositivos conectados se consigue un diagnóstico rápido y preciso.
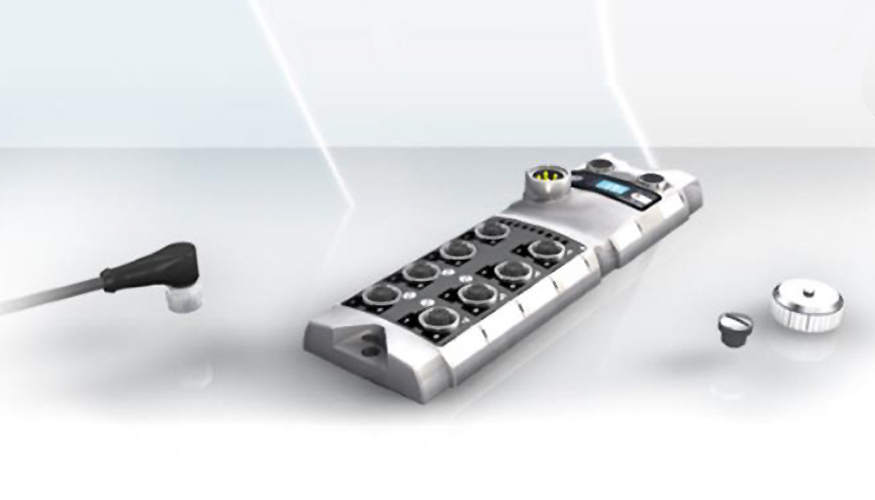
Control de rotación del elevador de cangilones
Dispositivo para controlar en tiempo real la velocidad de rotación cdel elevador de cangilones. Después de cualquier anomalía (por ejemplo, debido a un destensado de la correa), el sistema genera una parada de emergencia de la máquina, evitando cualquier obstrucción o daño.
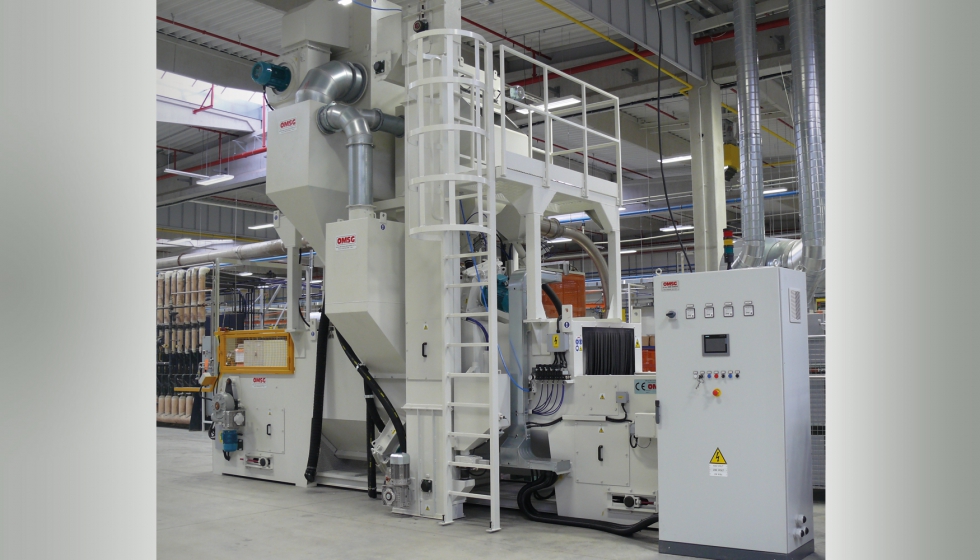
La ventaja principal de esta nueva generación de granalladoras comienza por una producción flexible y personalizada para cada producto, sin necesidad de alterar el proceso productivo. Gracias a lo cual, obtenemos una serie de beneficios que conviene destacar:
- Calidad constante gracias a un alto nivel de industrialización
- Reducción de la serie a trabajar. Al eliminarse la posibilidad de errores en los procesos, la producción final no sufre alteraciones de calidad y se obtienen piezas finales perfectas. Se eliminan los rechazos y reclamaciones.
- Control total del proceso. El proceso se autocorrige en tiempo real: permite una corrección inmediata de cualquiera de los parámetros lo que posibilita un aumento de la producción y la perfección de la pieza final.
- No existe dependencia de la persona.
- Menor costo operativo.