Optimización del proceso de soldadura por láser de materiales disimilares
Hoy en día, la unión de materiales disimilares es indispensable para la fabricación y construcción de equipamiento y maquinaria avanzada. No obstante, la soldadura de materiales disimilares suele resultar muy difícil, especialmente cuando las propiedades físicas y metalúrgicas de los materiales a soldar difieren sustancialmente. Se ha demostrado experimentalmente que el empleo de la tecnología láser para llevar a cabo estas soldaduras permite obtener uniones libres de defectos. No obstante, las diferencias de propiedades, tales como la absorción, conductividad térmica, reflectividad o el punto de fusión, tienden a producir defectos en las soldaduras. De hecho, al soldar materiales disimilares, si el coeficiente de expansión térmica de los dos materiales es muy diferente, se generan tensiones internas en la zona intermetálica durante los cambios de temperatura producidos en el propio proceso de soldadura, asociadas al desajuste de expansiones térmicas. Por tanto, para poder sacar el máximo partido a esta tecnología, es necesario realizar un detallado estudio para optimizar las condiciones de proceso.
1. Introducción
La progresiva sustitución de los aceros convencionales en los componentes de automoción por aceros de alta resistencia, aleaciones ligeras (aluminio, magnesio) y materiales compuestos está permitiendo la fabricación de componentes más ligeros, consiguiéndose una reducción significativa del consumo de combustible y de las emisiones de CO2 [1]. El diseño y fabricación de estructuras híbridas, en las que es necesario unir materiales disimilares entre sí, presenta un gran potencial tanto a nivel técnico como económico [2]. Sin embargo, es bien sabido que la soldadura entre materiales disimilares es complicada. En términos generales, para poder soldar dos materiales disimilares, se requiere una solubilidad mutua. Los defectos de la soldadura de metales disimilares ocurren en muchas aplicaciones industriales. Estos defectos se atribuyen generalmente a las diferentes propiedades físicas y metalúrgicas de los dos materiales, tales como la conductividad térmica, punto de fusión, posible formación de fases frágiles y la mojabilidad [3]. De hecho, al soldar materiales disimilares, si el coeficiente de expansión térmica de los dos materiales es muy diferente, se generan tensiones internas en la zona intermetálica durante los cambios de temperatura producidos en el propio proceso de soldadura, asociadas al desajuste de expansiones térmicas. Asimismo, la formación de ciertas fases intermetálicas puede provocar la disminución de las propiedades mecánicas y funcionales de la unión. La disminución de la solubilidad de los elementos de aleación puede provocar agrietamientos.
La soldadura por láser es una de las técnicas de unión más prometedoras, ya que, en comparación con las técnicas más convencionales de soldadura, la soldadura por láser presenta una alta productividad debido a las elevadas velocidades de proceso, buena calidad de las soldaduras, reducida zona afectada térmicamente (ZAT) y uniones delgadas, mínima perdida de material, baja distorsión, flexibilidad y facilidad de automatización. Es por esto que se sigue estudiando la viabilidad del proceso de soldadura por láser para numerosas aplicaciones. Muchas de las ventajas y limitaciones de la soldadura por láser, en comparación con otras técnicas, dependen de las propiedades del haz enfocado: La alta densidad de energía concentrada en un área (spot) reducida permite realizar la soldadura keyhole, y la limitada transferencia energética hacia el material base es lo que produce una ZAT muy fina, con bajas tensiones residuales y bajas distorsiones. Las altas velocidades de enfriamiento favorecen la formación de microestructuras finas (reducido tamaño de grano y finas estructuras dendríticas en el baño fundido), lo cual normalmente resulta en una mejora de las propiedades mecánicas. Este trabajo se centra en el estudio de dos casos de soldadura disimilar por láser: la soldadura de dos aceros inoxidables, uno austenítico y otro martensítico, y la soldadura de un acero inoxidable con una aleación de aluminio.
2. Método experimental
2.1. Material
Para el desarrollo de la experimentación se han empleado, por un lado muestras cilíndricas de acero inoxidable martensítico UNE-EN X45CrSi9-3 (en adelante X45) y acero austenítico UNE-EN X53CrMnNiN21-9 (en adelante X53), con diámetro de 8,3 mm. Para la soldadura aluminio-acero, se han empleado chapas de acero inoxidable austenítico AISI 304 de 0,8 mm de espesor y la aleación de Al-Si-Mg A357 con un espesor de 5 mm. Las composiciones químicas de estas cuatro aleaciones se muestran en la tabla 1.
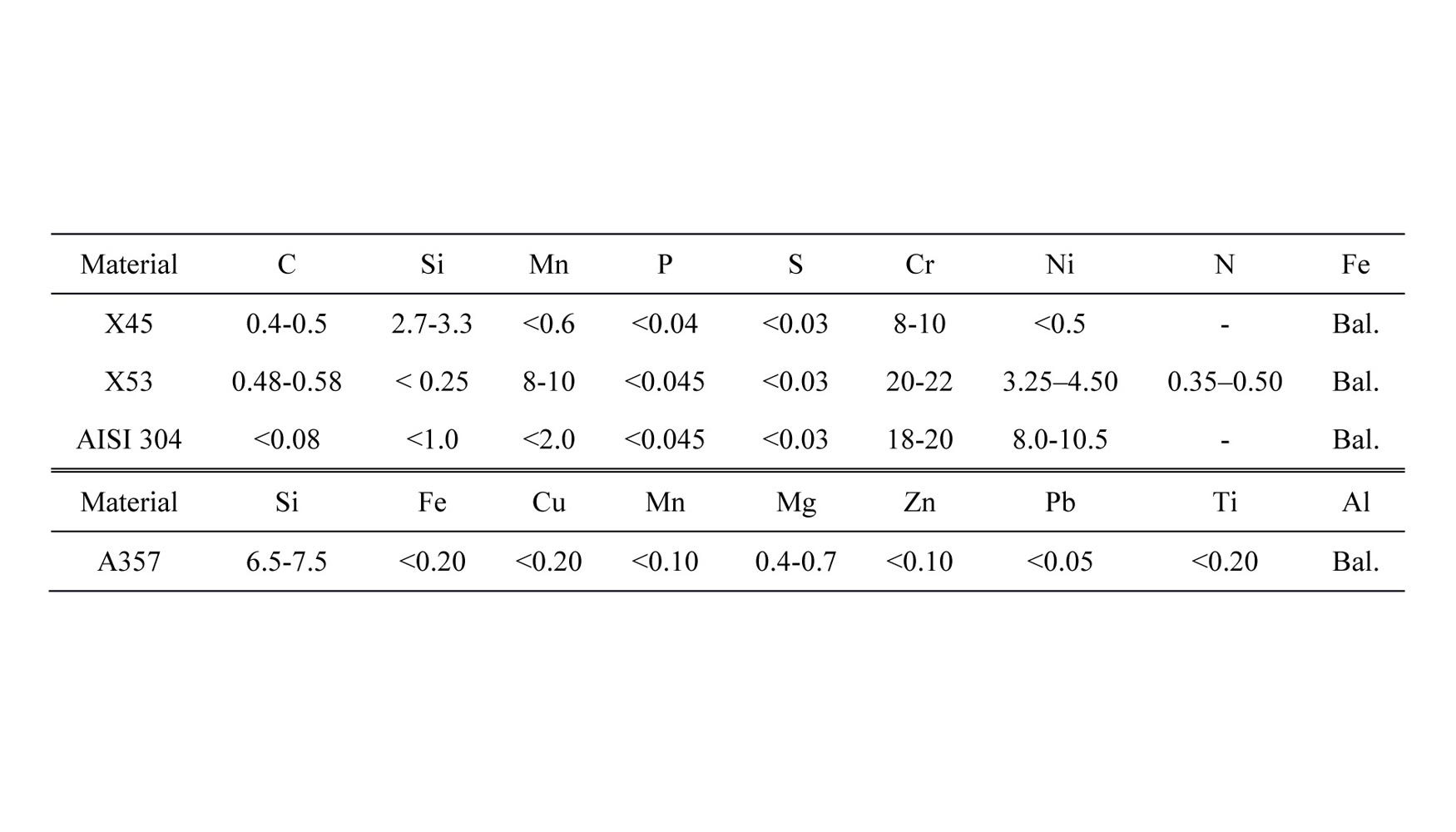
2.2. Equipamiento
Con el fin de llevar a cabo la experimentación concerniente a este estudio, se ha empleado un generador láser de Nd:YAG de onda continua (CW), modelo DY022 de Rofin-Baasel, bombeado por diodos y emisión en el espectro infrarrojo cercano (λemisióñ1064 nm) con una potencia máxima de 2.200 W. Para el guiado del láser a la zona de trabajo se ha hecho uso de una fibra óptica de sección circular de 600 μm de diámetro. El sistema óptico para el enfoque del haz láser está compuesto por un colimador de 200 mm de focal y una lente de enfoque de 200 mm. Este sistema de lentes proporciona un spot circular de 600 μm de diámetro en foco.
Se ha empleado un cabezal de soldadura fabricado por Precitec. Este cabezal permite emplear un gas de protección coaxial, que fluye a través del mismo orificio por donde pasa el haz del láser.
En el caso de la soladura de las muestras cilíndricas se ha empleado un torno CMZ donde se ha instalado el cabezal de soldadura. Para la soldadura de aluminio-acero se ha empleado un brazo robot de 6 ejes de ABB. La figura 1 muestra las dos configuraciones de soldadura.
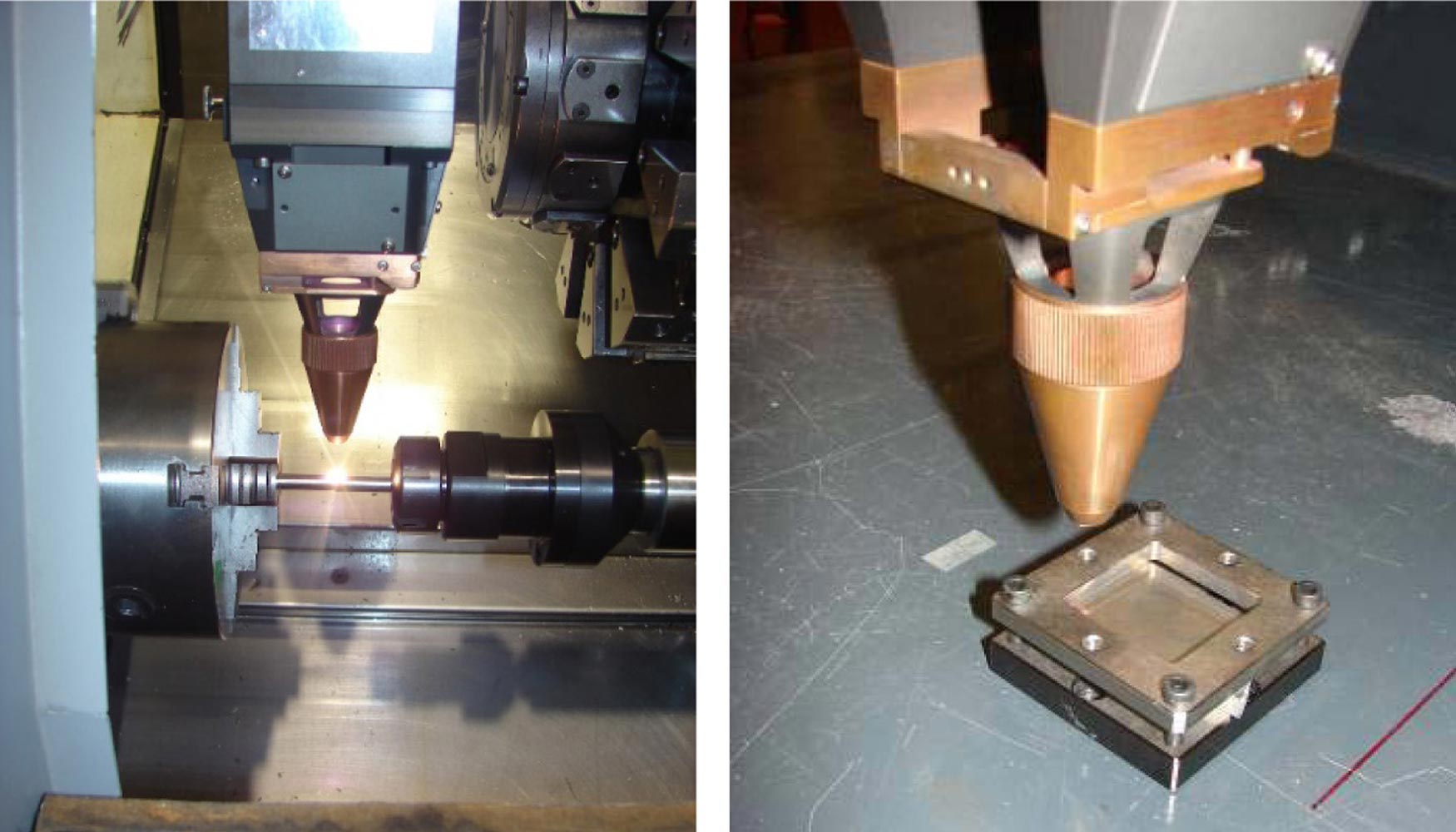
2.3. Procedimiento experimental
- 2.3.1. Soldadura de cilindros de aceros disimilares
El primer paso ha consistido en el estudio de la soldabilidad por láser de los dos aceros por separado mediante pruebas de fusión independientes. Para ello, se ha disparado sobre probetas cilíndricas de ambos materiales con el fin de acotar la ventana de parámetros estudiando el corte transversal de las zonas fundidas para ver la profundidad alcanzada y los posibles defectos obtenidos. En esta primera fase, se ha analizado el efecto de los parámetros de proceso como la potencia del láser, la velocidad de giro y el desenfoque o el diámetro del spot en la superficie. Asimismo, con el fin de minimizar los rebajes debidos al arrastre de material a lo largo de la soldadura, se han probado diferentes formas de aplicar la potencia gradualmente con rampas ascendentes y descendentes. La Tabla 2 muestra los parámetros empleados en esta primera parte de la experimentación.
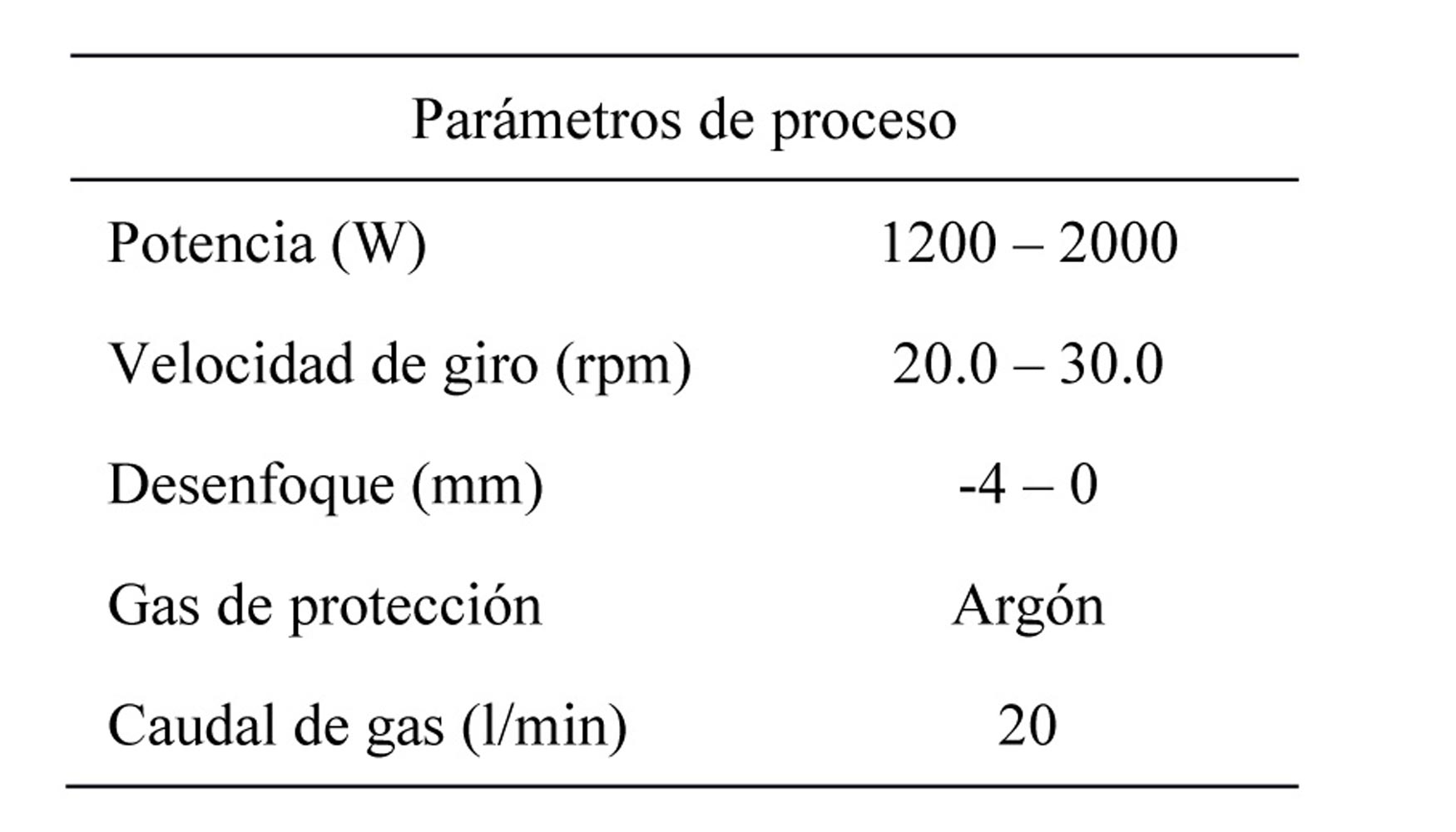
Una vez analizado el efecto de los parámetros de soldadura sobre cada uno de los aceros, se ha procedido a realizar las pruebas de soldadura. Para poder llevar a cabo la soldadura a tope de los dos cilindros, es necesario que ambos cilindros giren sincrónicamente, por lo que antes de realizar la soldadura final, se han unido las dos partes mediante un punto de soldadura producido con el mismo láser (P=500 W, t= 0,5 s). Hecho esto, se ha amarrado el cilindro de acero martensítico en el plato de garras, mientras que el cilindro austenítico se sujeta en el contrapunto mediante un cono morse, para evitar el desalineamiento de las dos piezas debido a tensiones producidas en el proceso de soldadura (Fig. 1). En la tabla 3 se muestran los parámetros empleados en la experimentación final de soldadura de aceros disimilares.
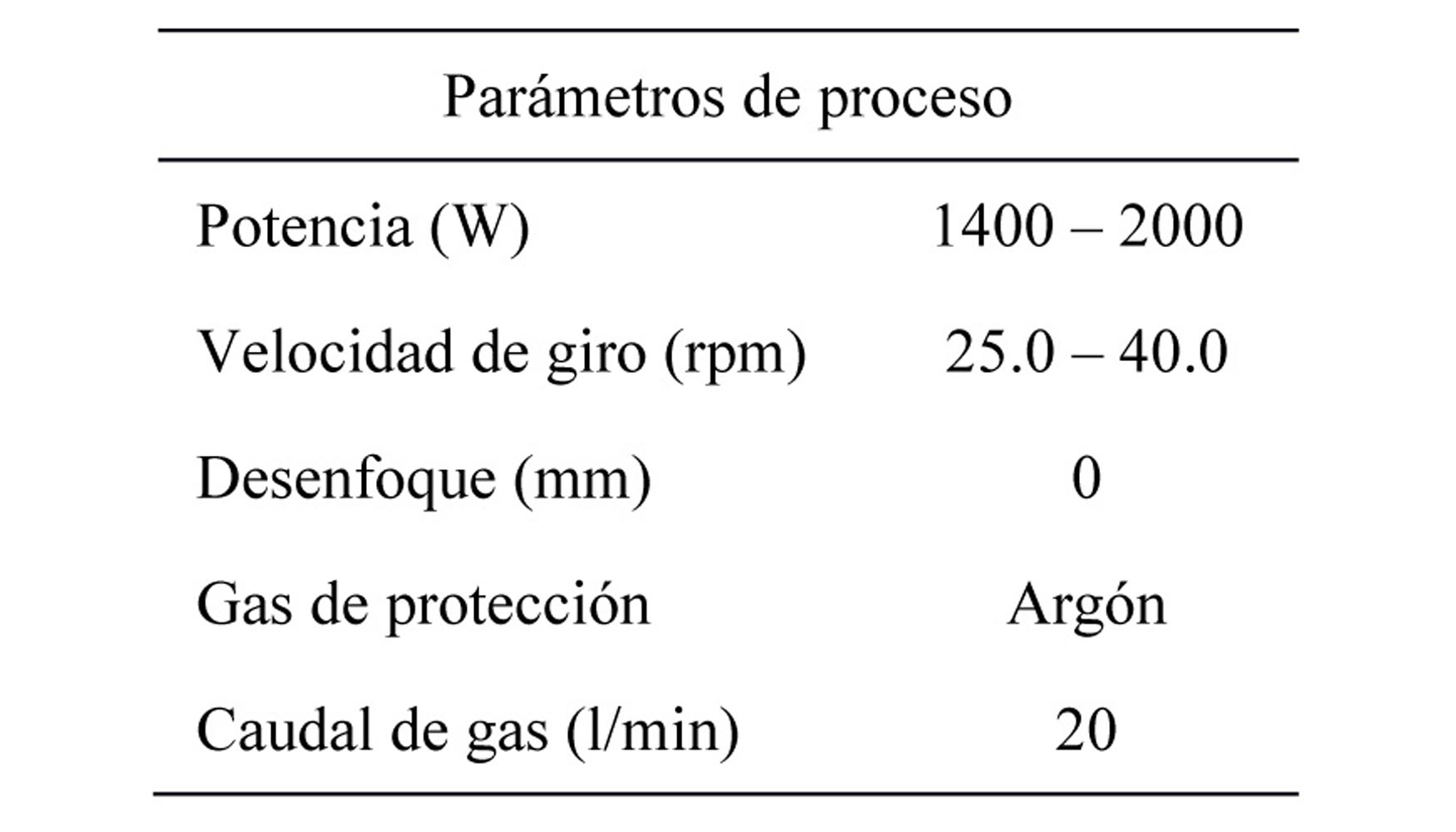
- 2.3.2. Soldadura de chapas de aluminio-acero
Para la soldadura a tope de chapas de aluminio-acero, se ha empleado un utillaje para amarrar las dos chapas garantizando una buena unión entre ambas y evitando posibles deformaciones debido a las tensiones producidas durante el proceso de soldadura (figura 1). Se han probado dos procesos de soldadura: soldadura por conducción y por keyhole irradiando en ambos casos la chapa de acero. Para la soldadura por conducción, se ha aumentado el tamaño del spot del láser sobre la superficie de la chapa de acero mediante el desenfoque, con el fin de generar gradientes de temperatura más suaves, mientras que para el proceso de soldadura por keyhole se ha posicionado el foco del láser sobre la superficie de la chapa de acero, para aumentar al máximo la irradiancia o densidad de potencia del haz láser en la línea de soldadura.
La tabla 4 muestra los parámetros de proceso más relevantes para ambos procesos de soldadura.
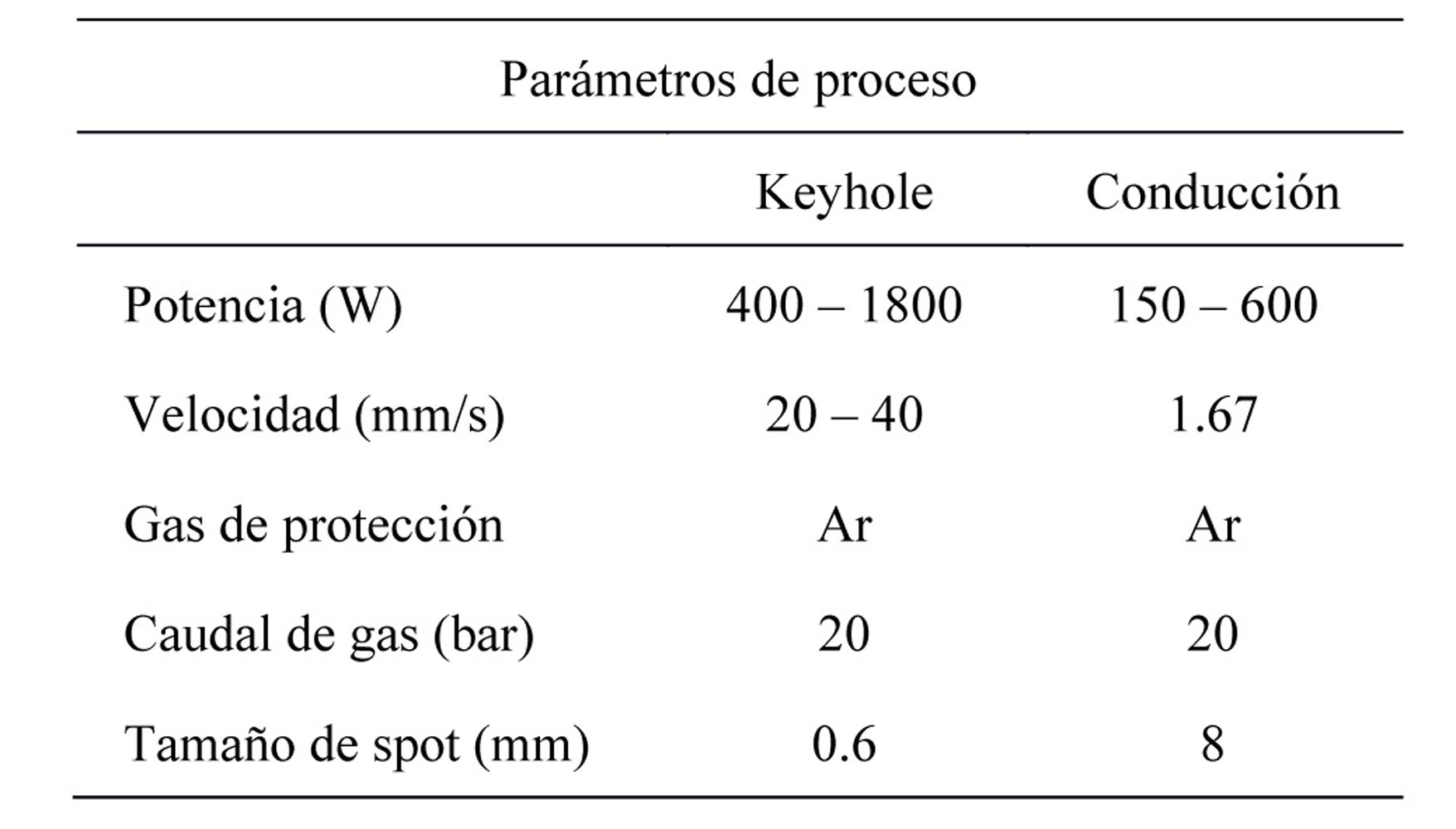
2.4. Métodos de caracterización
Con objeto de analizar la microestructura resultante tras los aportes y diferentes tratamientos térmicos, se ha procedido a la preparación metalográfica de las soldaduras. Para ello, se han cortado las uniones en la dirección perpendicular a la línea de soldadura, puliendo dichas superficies con pasta de diamante para después atacarlas químicamente y así revelar la microestructura. Para el estudio microestructural se ha empleado microscopía óptica y microscopía electrónica de barrido (SEM), complementada con análisis químico semi-cuantitativo EDS. Además, se han realizado cadenas de microdureza, empleando para ello un microdurómetro con una carga de 0,3 kg en la dirección perpendicular a la soldadura. Por último, se ha empleado un difractómetro de rayos-X para medir las tensiones residuales en la superficie de la soldadura.
3. Resultados y discusión
3.1. Soldadura de cilindros de aceros disimilares
La figura 2 muestra los cortes transversales de las zonas fundidas con diferentes potencias y velocidades de giro en cada uno de los aceros inoxidables. En todos los casos se ha posicionado el foco del láser sobre la superficie del cilindro. Tal y como se puede observar, se obtienen resultados similares con ambos materiales. La penetración de la zona fundida crece al aumentar la potencia y disminuir la velocidad de giro, como cabía esperar, ya que la energía aportada es proporcional a la potencia y al tiempo de interacción, que a su vez es inversamente proporcional a la velocidad. Así pues, cuando la energía aportada es demasiado reducida las zonas fundidas no llegan al núcleo de los cilindros, mientras que cuando es demasiado elevada, comienzan a producirse defectos como poros o rechupes en el núcleo de la zona fundida, así como rebajes excesivos en la superficie debido al arrastre de material fundido a lo largo de la línea de fusión. Si se aumenta aún más la energía aportada, es posible llegar incluso a cortar el cilindro, como ocurre en el caso de las celdas que aparecen marcadas en rojo en la figura 2. En cuanto a las diferencias observadas entre los dos materiales, se obtienen zonas fundidas de mayor penetración en el caso del acero martensítico X45, aunque las diferencias son mínimas, por lo que es de esperar que en las soldaduras entre ambos materiales se obtengan zonas con secciones simétricas con respecto a la superficie de contacto sin necesidad de emplear métodos para compensar estas diferencias como desplazar o inclinar el haz láser para hacia el material menos absorbente[4].
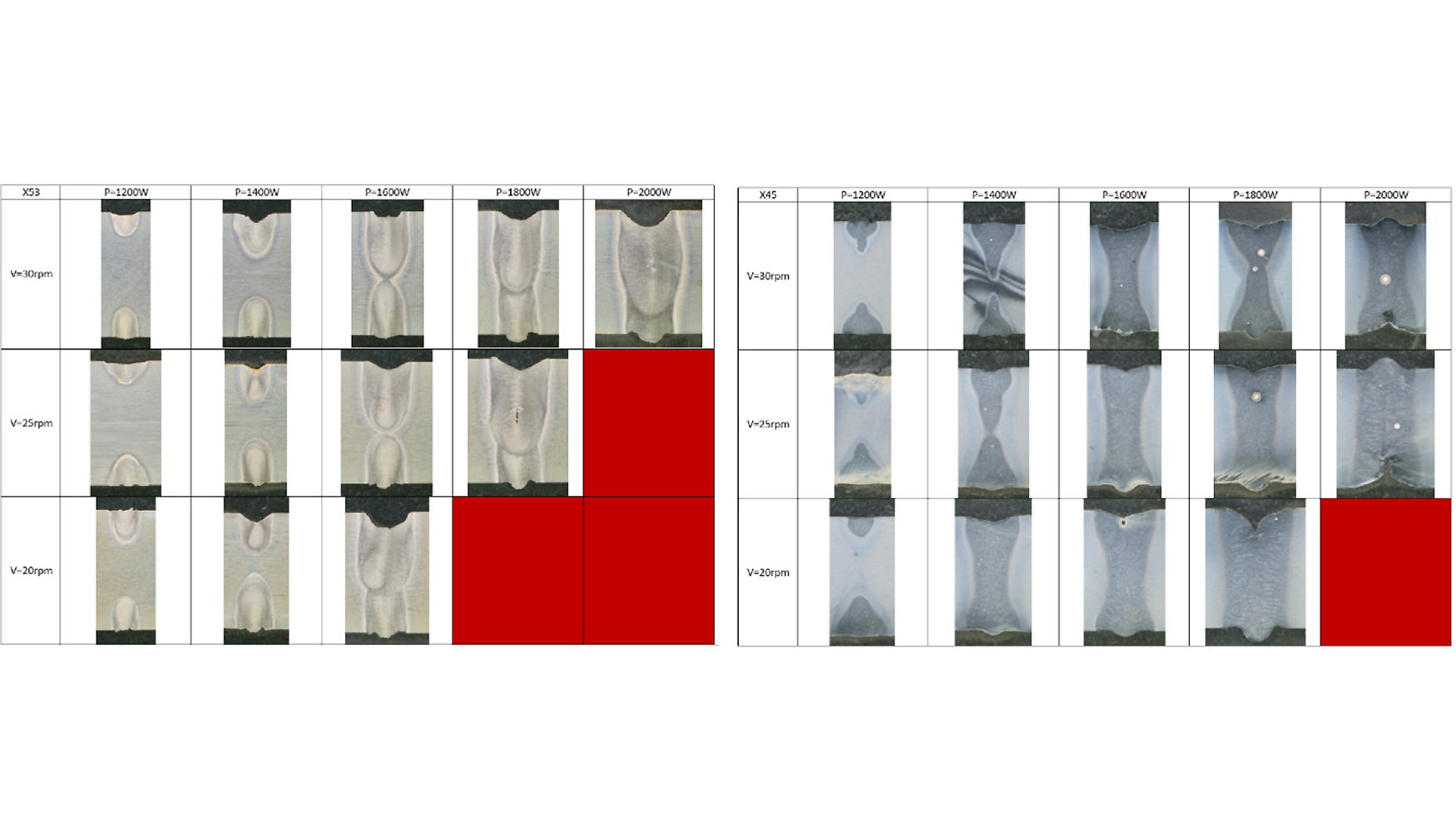
La figura 3 muestra el efecto del desenfoque sobre la geometría de las zonas fundidas obtenidas en ambos materiales con diferentes velocidades de giro. En todos los casos se ha fijado la potencia del láser a 2.000 W. Es una práctica frecuente en procesos de soldadura láser por keyhole la de posicionar el foco por debajo de la superficie para poder alcanzar mayores profundidades sin afectar de forma apreciable a la geometría de la soldadura [5]. No obstante, en este caso, se observa que al enfocar por debajo de la superficie, especialmente a 3 ó 4 mm, la penetración disminuye debido a que la disminución de la irradiancia en la superficie del cilindro impide la formación de un keyhole suficientemente profundo.
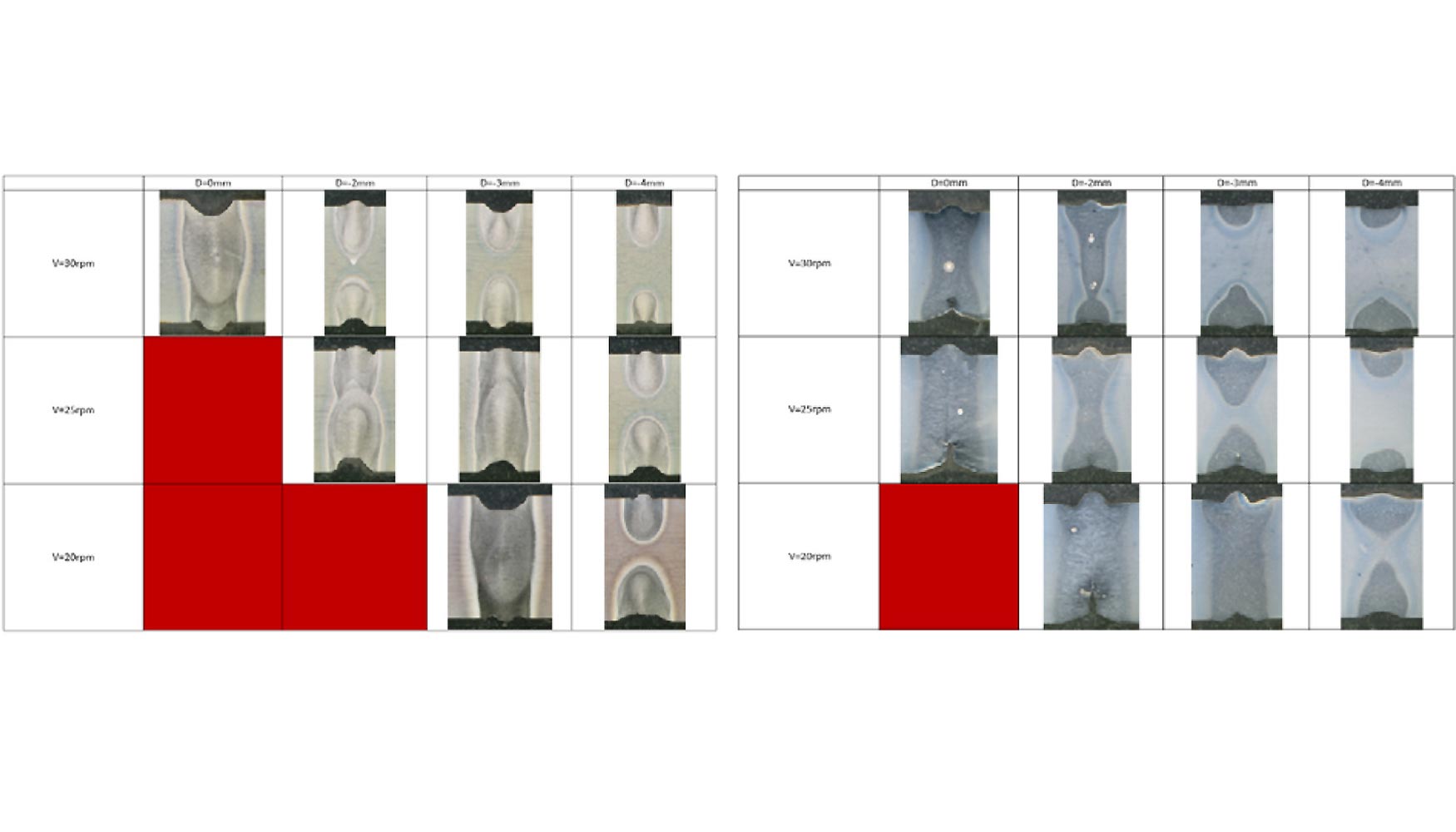
En vista de estos resultados, se decide realizar las soldaduras finales posicionando el haz láser perfectamente centrado en la unión entre ambos cilindros, con el foco en la superficie de los cilindros.
Por último, a fin de reducir el rebaje que se produce en la superficie de los cilindros debido al arrastre de material fundido a lo largo del cordón de fusión, se han empleado diferentes rampas de potencia, tal y como se muestra en la figura 4. Al aumentar y disminuir la potencia del láser de forma gradual durante la soldadura, se consigue minimizar los rebajes superficiales en todos los casos. Cuando las variaciones de potencia son más graduales, esta mejora se hace más notable, aunque debido a que los tiempos de soldadura son relativamente cortos (2 s para una velocidad de 30 rpm), al aumentar el tiempo correspondiente a las rampas de potencia, la energía total aportada disminuye considerablemente, haciendo que la penetración también se vea afectada, como se puede observar en el caso de la rampa 2. Por tanto, se decide emplear un tiempo de irradiación más largo, de forma que se puedan implementar rampas de potencia más suaves sin afectar a la penetración de la zona fundida (rampa 3 en la figura 4). No obstante, hay que tener en cuenta que esto implica un ligero aumento del tiempo de proceso y el solape de la zona final del cordón de soldadura con el inicio del mismo. Sin embargo, y aunque no es posible eliminar completamente este efecto, la mejora obtenida es notable.
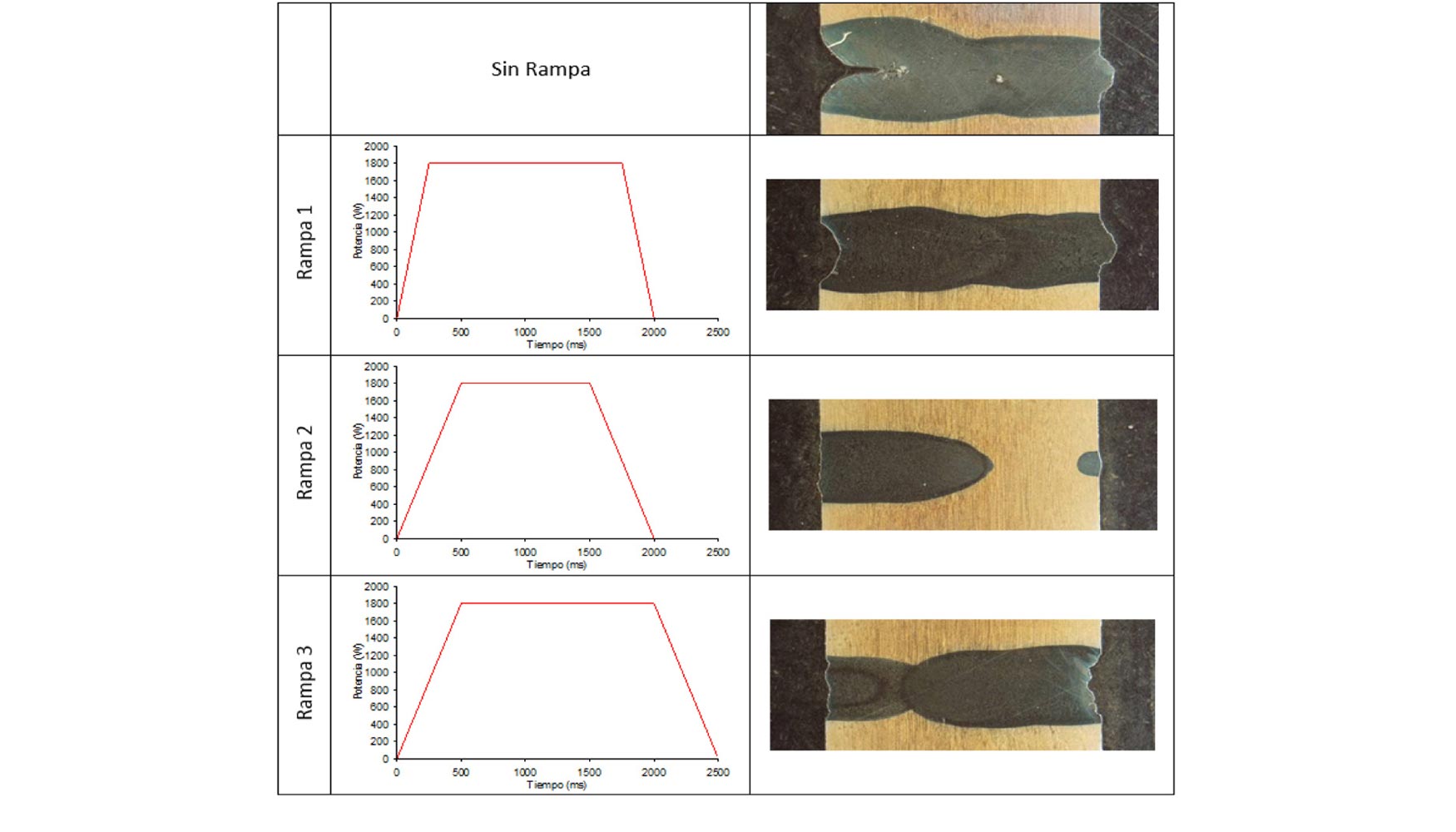
Por tanto, se definen las rampas de potencia para las soldaduras de la siguiente forma: siendo T el tiempo que se tarda en dar una vuelta completa alrededor del eje de los cilindros para una velocidad dada, la potencia pasa de cero hasta el valor máximo en T/4, se mantiene a ese valor durante 3T/4 y finalmente vuelve a cero en T/4, lo cual produce un solape de un cuarto de vuelta.
La figura 5 muestra los cortes transversales de soldaduras de aceros disimilares producidas con diferentes parámetros de proceso, teniendo en cuenta los resultados obtenidos en la experimentación realizada sobre cada uno de los aceros de forma independiente. Tal y como se observa en la imagen, con potencias inferiores a 1.800 W no se obtiene una penetración total del baño fundido, incluso empleando velocidades de giro más bajas. En lo referente a las soldaduras que han llegado hasta el núcleo, cabe destacar que las soldaduras producidas con mayor velocidad presentan un perfil más uniforme además de rebajes de menor profundidad, por lo que con el proceso para optimizar la soldadura por láser de cilindros de aceros inoxidables disimilares pasaría por fijar la potencia al máximo (en este caso a 2.200 W) y aumentar la velocidad de giro hasta el valor máximo que permita obtener una penetración completa hasta el núcleo, empleando rampas de potencia como las que se han discutido previamente y enfocando el haz del láser en la superficie de los cilindros, centrado en la unión de ambos.
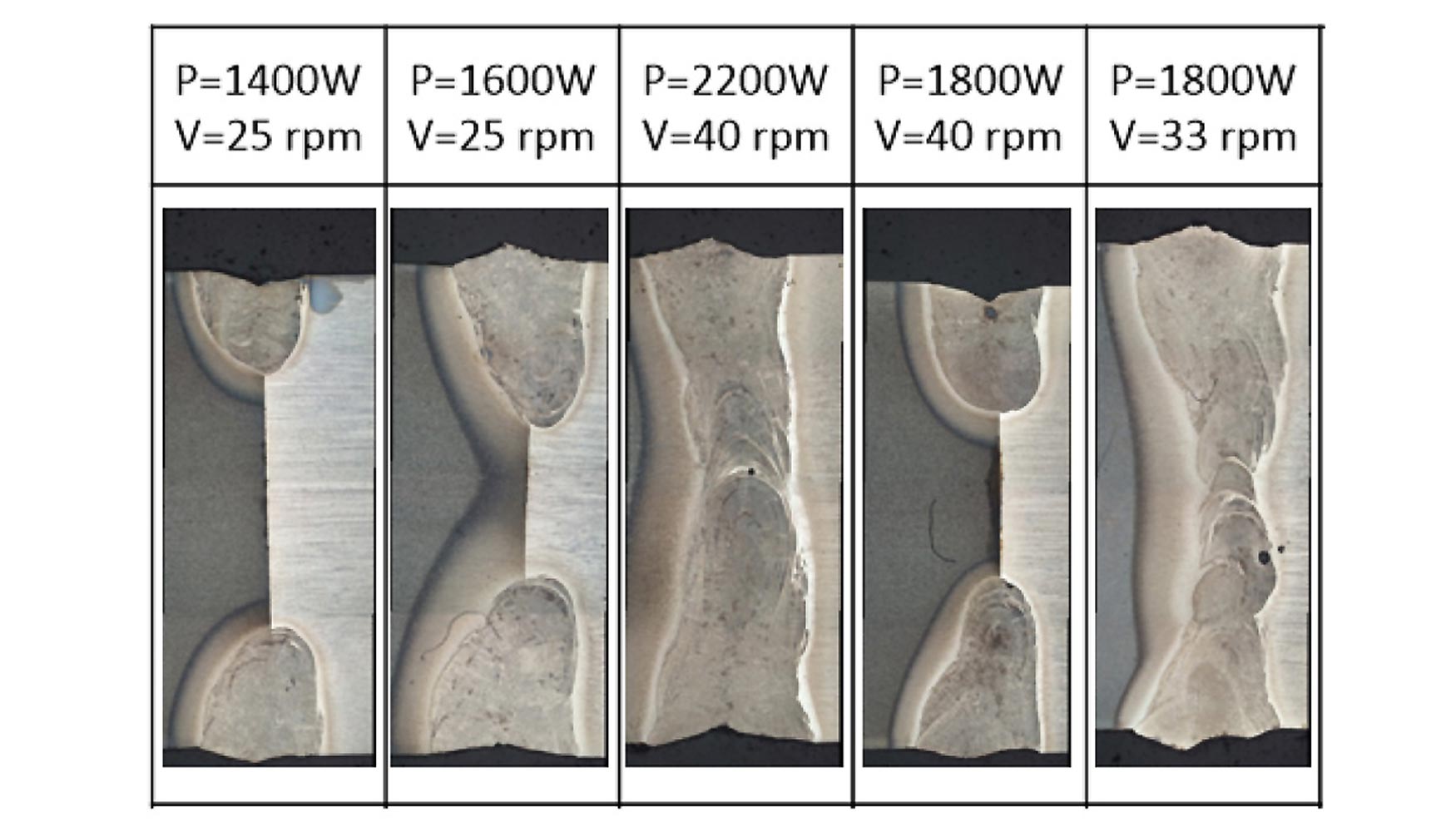
Con el fin de caracterizar la unión, se ha medido la microdureza en la dirección perpendicular de la misma, paralela al eje del cilindro, a 0,5 mm por debajo de la superficie del mismo, tal y como se puede observar en la figura 6. Se puede observar que la dureza de ambos metales en la zona no afectada por el proceso (laterales de la imagen) está en torno a 300-400 HV0.3. En la zona fundida (la parte central de la imagen) muestra un valor similar y muy uniforme alrededor de 300 HV0.3. No obstante, en la zona térmicamente afectada del acero martensítico se observa un aumento de dureza hasta valores superiores a 600 HV0.3. Esto se debe a que en dicha zona se produce un calentamiento hasta temperaturas superiores a la de austenización, seguido de un enfriamiento rápido por conducción del calor hacia las zonas más frías del propio cilindro. Este proceso, que es esencialmente un proceso de temple, produce una estructura martensítica de elevada dureza. Este efecto no suele ser deseable en soldaduras, ya que el aumento de dureza también suele implicar un aumento de la fragilidad y formación de tensiones residuales tractivas, perjudiciales para la vida en servicio del componente.
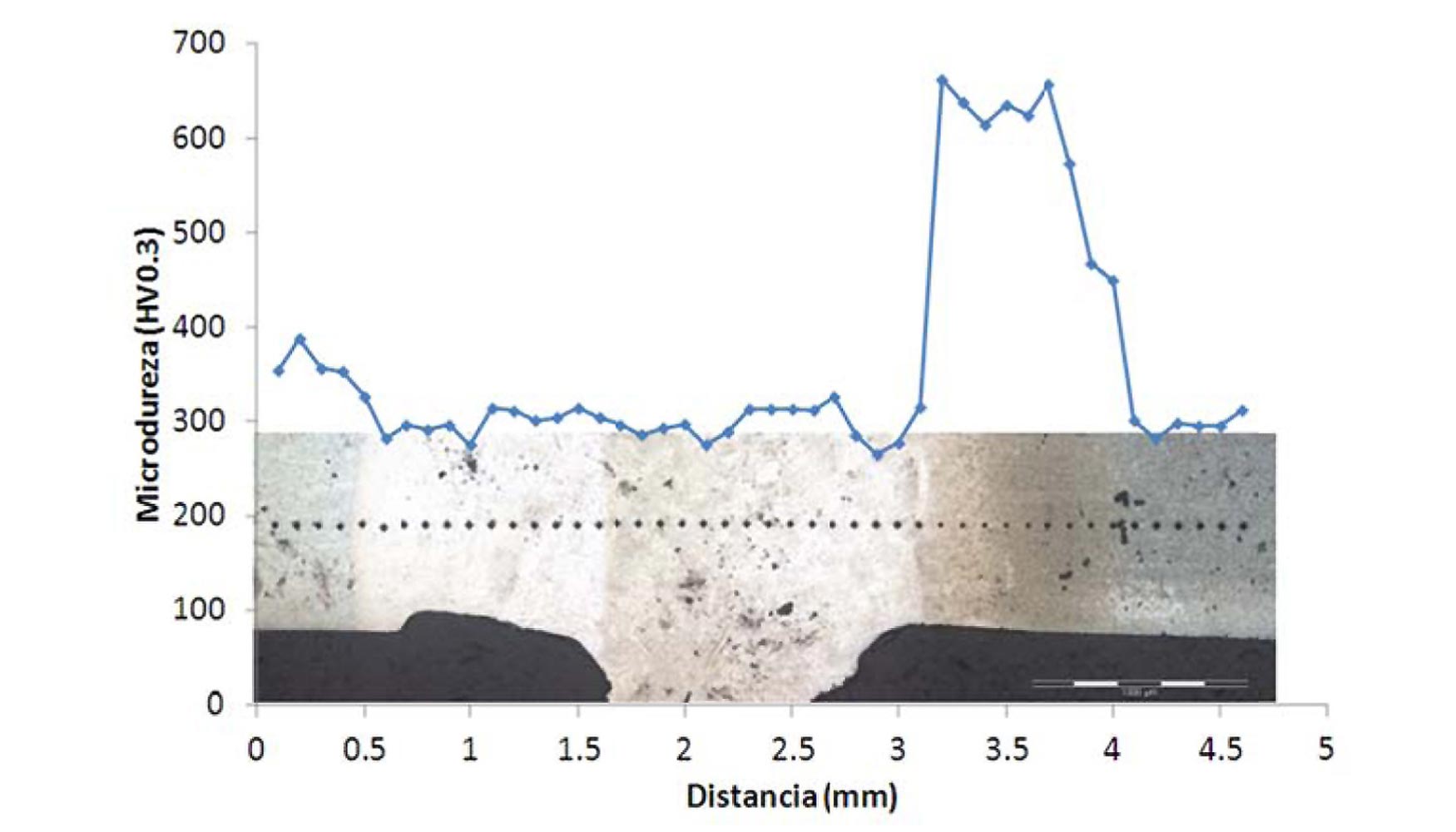
Con el fin de verificar esta hipótesis se han medido las tensiones residuales en la superficie del cilindro soldado con los parámetros optimizados, en diferentes puntos, partiendo desde el acero austenítico y a través de la unión soldada hasta alcanzar la zona no afectada del acero martensítico (figura 7). Se observa un pico tractivo de aproximadamente 150 MPa que coincide con la región endurecida, por lo que es de esperar que dicha región sea la más débil de la unión y, por tanto, por donde fallaría probablemente la pieza soldada. Para evitar este efecto, la solución pasaría por un tratamiento térmico de relajación o revenido posterior a la soldadura, lo cual queda fuera del alcance del presente trabajo.
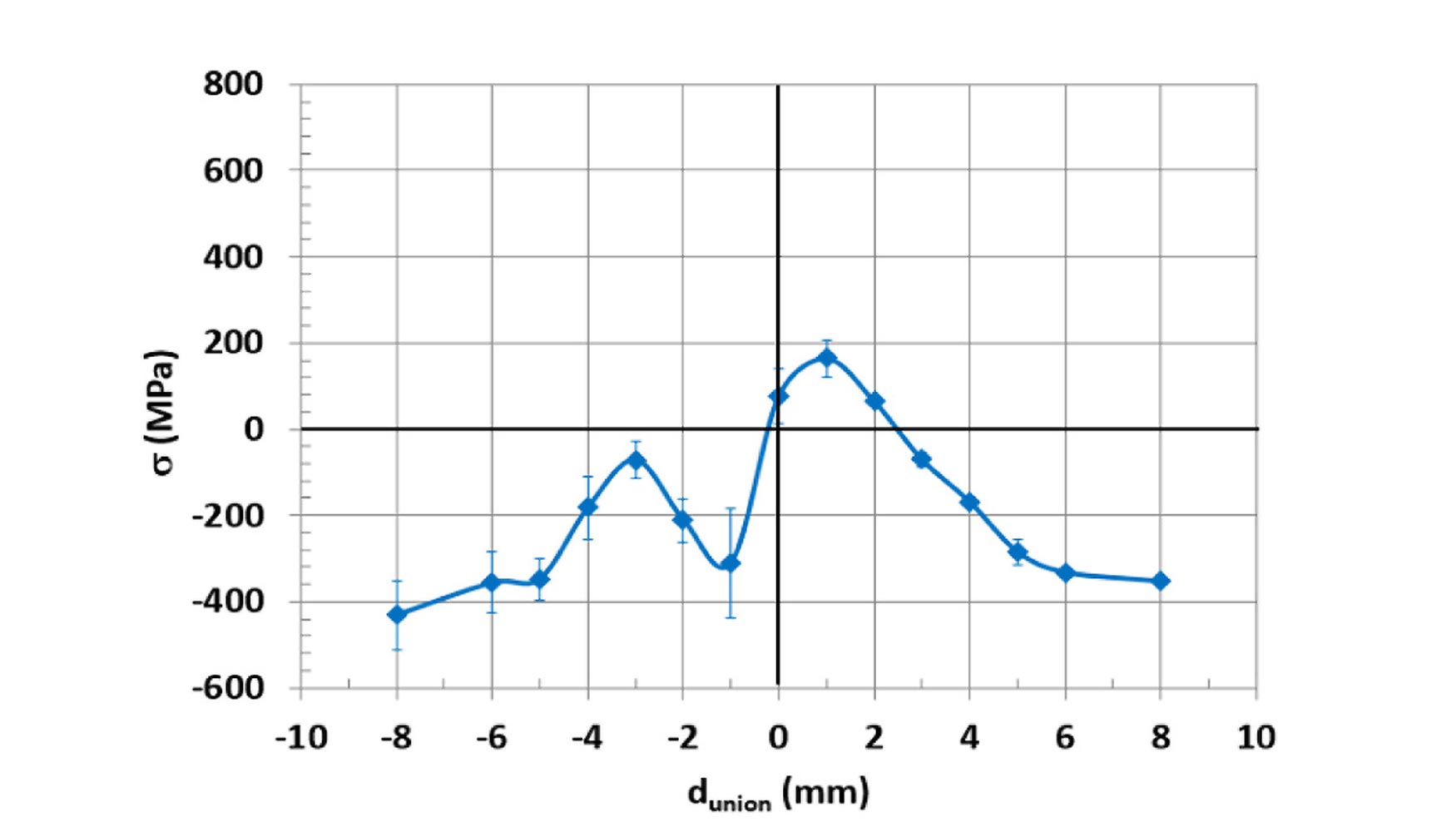
3.2. Soldadura de chapas de aluminio-acero
El principal problema a la hora de soldar aleaciones de aluminio con aceros suele residir en los compuestos intermetálicos que se forman en la unión. Estos compuestos son extremadamente duros y frágiles, lo cual puede provocar que la soldadura se fragilice por las regiones donde exista una concentración más elevada de intermetálicos. En términos generales, suelen ser aceptables capas de intermetálicos hasta 10 μm de espesor. Con el fin de minimizar la aparición de este tipo de compuestos, se ha optado por estudiar el proceso de soldadura por conducción. Este proceso permite aprovechar las diferencias de temperatura de fusión y conductividad térmica de ambos materiales para poder obtener gradientes de temperatura que permiten fundir la aleación de aluminio sin fundir el acero, pese a ser éste último el que recibe directamente la radiación del láser. Esta unión líquido-sólido restringe la difusión del aluminio hacia el acero, minimizando así el espesor de la capa de compuestos intermetálicos. Por el contrario, en el caso de la soladura por keyhole, donde ambas aleaciones se funden en la zona de unión, es mucho más difícil controlar la formación de este tipo de compuestos ya que la difusión aumenta al estar las dos aleaciones en fase líquida [6].
No obstante, la experimentación realizada con este método de soldadura por conducción no ha producido resultados satisfactorios, ya que en los casos en los que la potencia es demasiado baja, la temperatura alcanzada en la chapa de aluminio no es suficientemente alta como para producir la fusión superficial, y al aumentar gradualmente la potencia, se llega antes a fundir la chapa de acero, incluso agujereándola sin conseguir fundir la aleación de aluminio (figura 8).
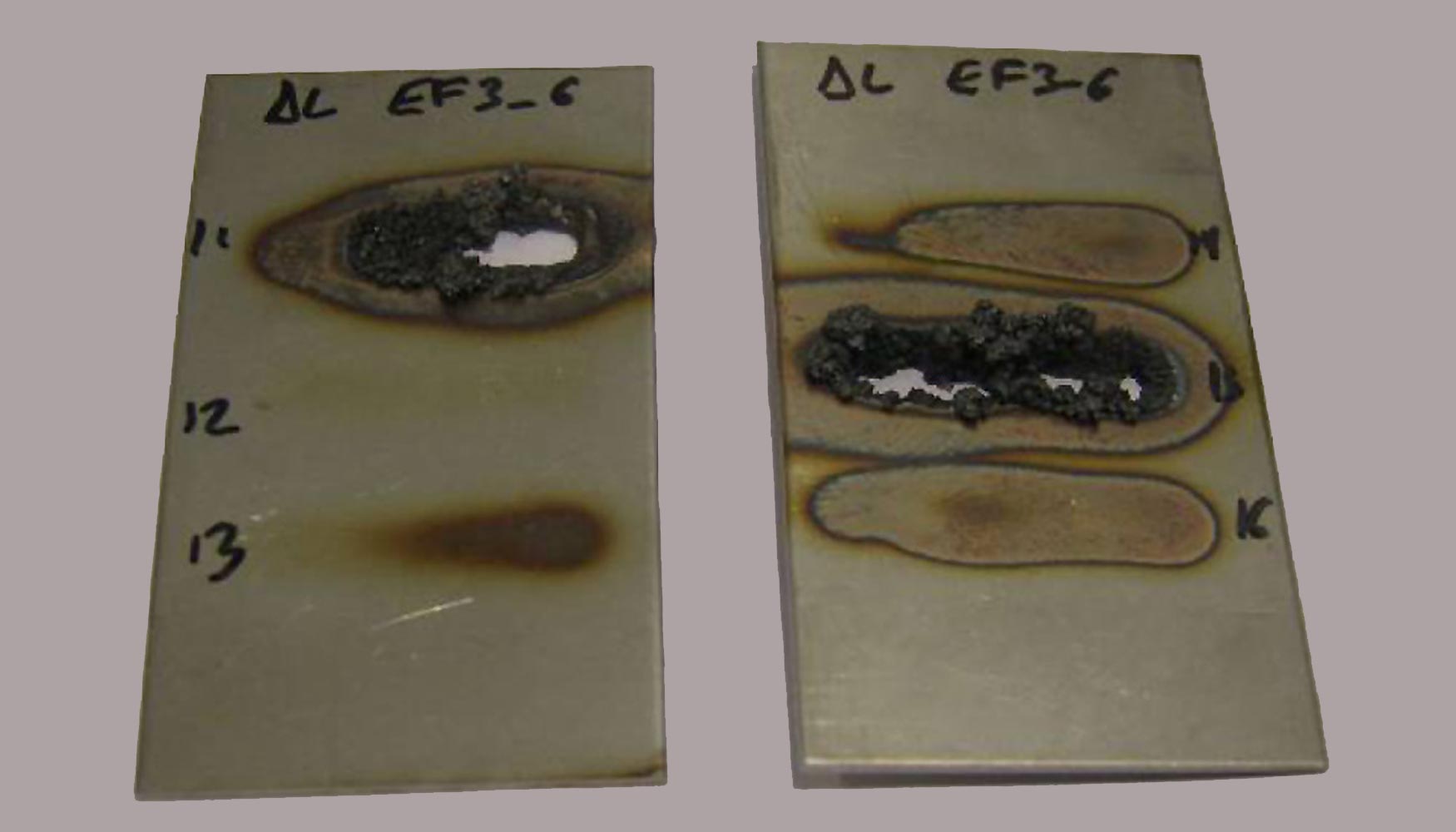
Esto no implica que este proceso sea imposible de llevar a cabo, no obstante, existen factores que dificultan producir uniones satisfactorias en este caso en particular. Por un lado, las dimensiones, y en particular el espesor de la chapa de acero son muy reducidas, por lo que la disipación de calor es muy limitada, lo que facilita la formación de estos agujeros de material fundido. Por otro lado, al aumentar el tamaño de spot del láser mediante el desenfoque, el perfil de irradiancia del haz deja de ser el top-hat uniforme que se produce en el foco para pasar a un perfil del tipo gaussiano donde la irradiancia es máxima en el centro del spot pero se reduce gradualmente en diámetros exteriores. Además, el hecho de barrer una línea con un haz circular acentúa aún más este efecto ya que la energía que llega a los laterales de la línea es menor que la que llega a la zona central. La combinación de estos dos efectos, hace que se produzcan gradientes de temperatura en la superficie del acero, que el reducido espesor de la chapa no llega a uniformizar del todo. Por tanto en la unión entre ambas chapas el perfil de temperatura dista mucho de ser uniforme, por lo que la fusión de la chapa de aluminio tampoco puede serlo. Así pues, con el fin de producir uniones por este método lo ideal sería emplear un spot rectangular con irradiancia uniforme.
No habiendo obtenido resultados satisfactorios con el proceso de soldadura por conducción, se ha optado por estudiar la viabilidad de la soldadura por keyhole de las mismas chapas. Para ello, se ha irradiado la chapa de acero con el haz enfocado, variando la potencia del láser y la velocidad lineal del proceso para estudiar el efecto de ambos parámetros. La figura 9 muestra los cortes transversales de estas soldaduras.
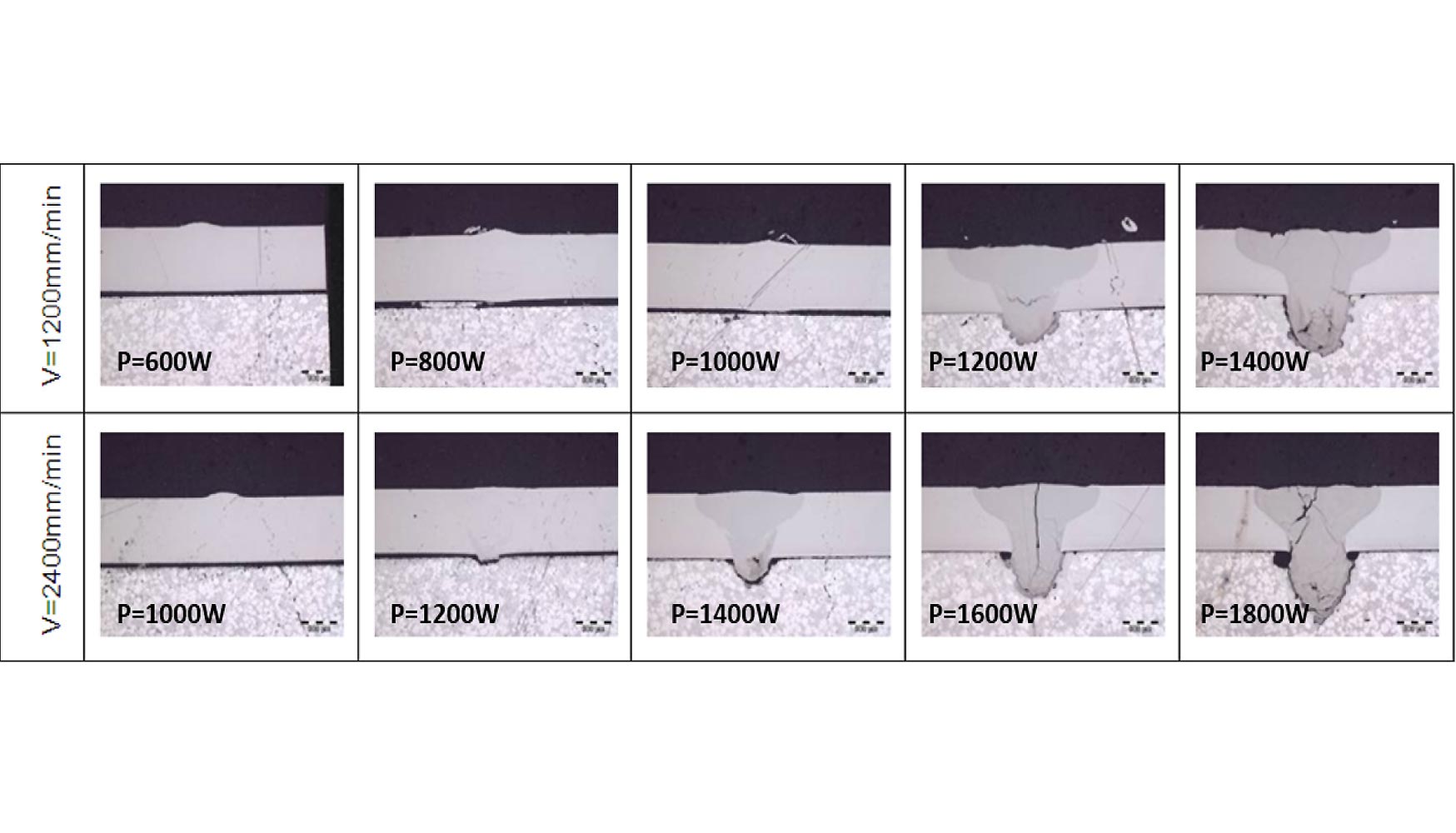
Se observa que la ventana de parámetros para obtener uniones soldadas libres de defectos es muy estrecha, ya que cuando la energía aportada es demasiado baja, se observa un hueco entre ambos materiales, de forma que a pesar de que las dos chapas queden pegadas, la soldadura es demasiado débil. Por otra parte, si la energía es demasiado elevada, la zona fundida se agrieta debido presumiblemente a la presencia de fases frágiles.
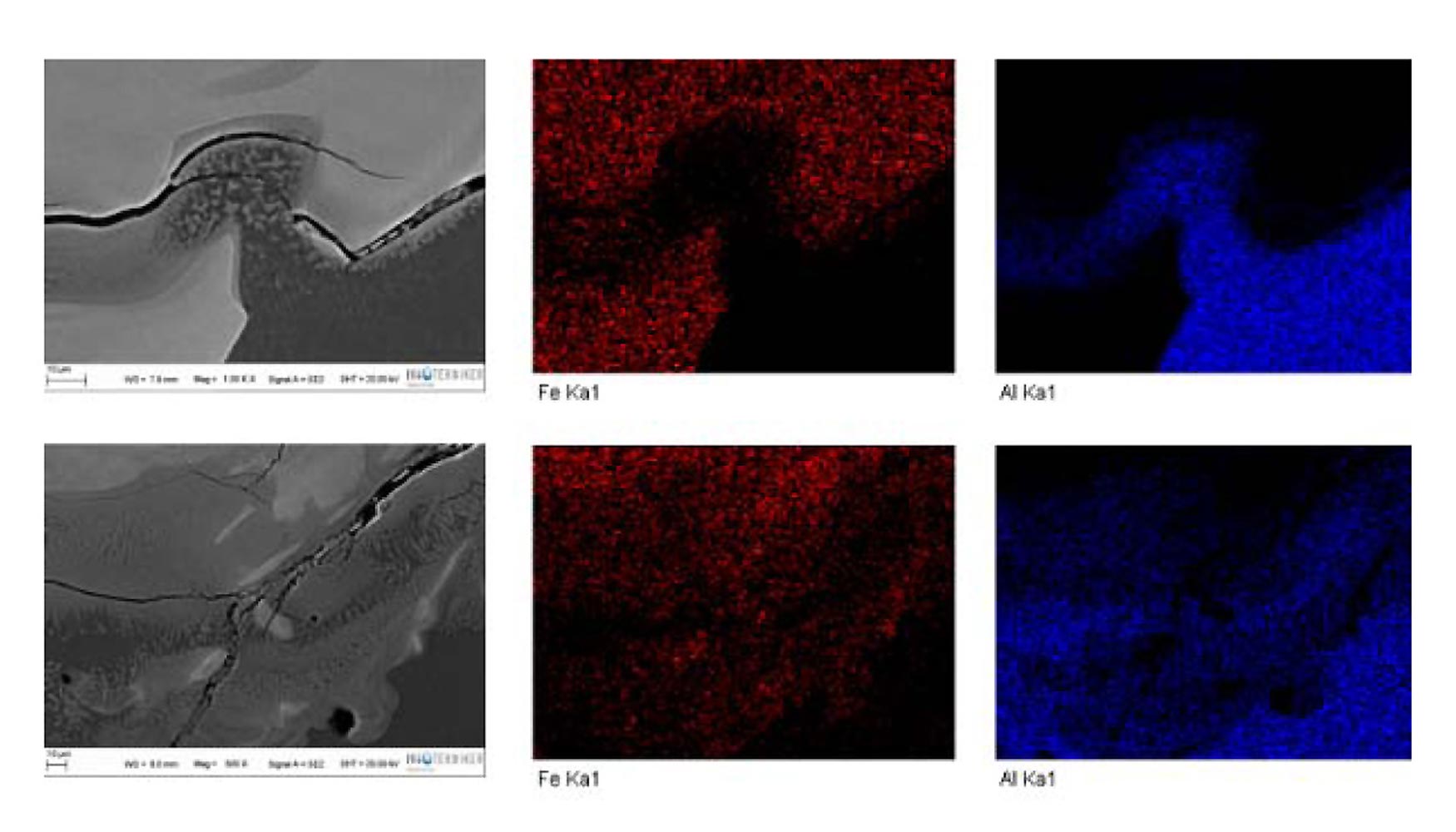
Con el fin de analizar más detalladamente las fases que se forman en la unión, se ha llevado a cabo un análisis por EDS. En primera instancia, se ha realizado un barrido para obtener unos mapas de composición, para poder identificar las regiones donde se han formado estos compuestos intermetálicos (figura 10). Es posible observar en estos mapas que la difusión del hierro hacia la chapa de aluminio es prácticamente nulo y lo mismo ocurre en el sentido opuesto, a pesar del hecho de haberse fundido una cantidad considerable de ambos materiales. No obstante, existen regiones cerca de la unión entre ambos materiales (en el límite de la zona fundida), donde se pueden encontrar tanto el hierro como el aluminio, lo que indica que en dichas zonas se han formado los compuestos intermetálicos. Asimismo, existe una gran concentración de pequeñas grietas en dichas regiones, lo que indica que en efecto existe una relación directa entre la precipitación de compuestos intermetálicos y la formación de grietas. Por último, se han identificado el tipo de intermetálicos que se forman en dichas regiones. Para ello se han analizado por EDS las diferentes estructuras que se muestran en la figura 11.
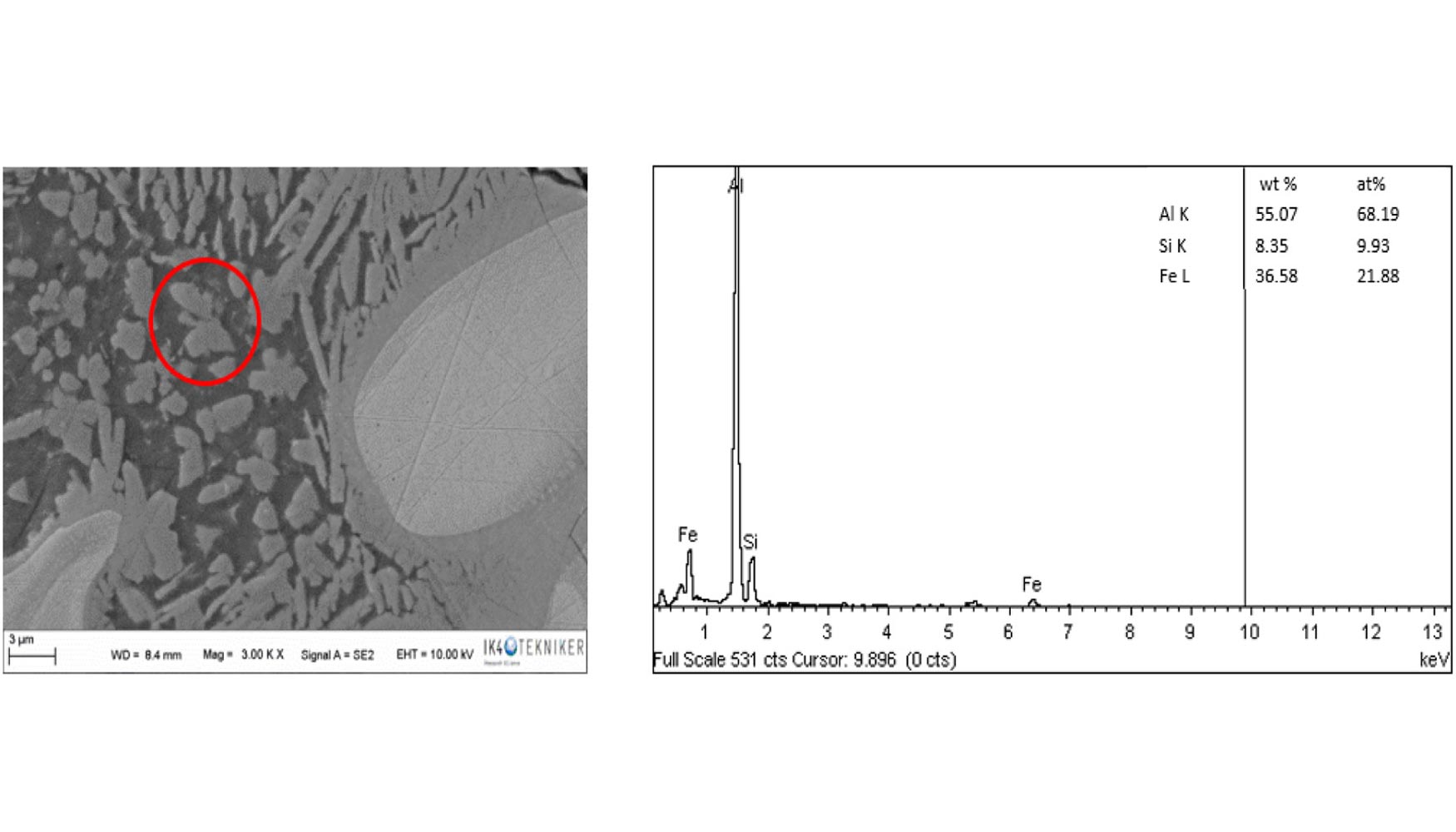
De acuerdo al diagrama de fases en equilibrio Fe-Al se pueden formar 6 compuestos intermetálicos: Fe3Al, FeAl, Fe2Al3, FeAl2, Fe2Al5 y FeAl3 [7]. Los 3 últimos son muy duros y frágiles y por ello fragilizan la propia soldadura, siendo por tanto intermetálicos no deseados. Para poder determinar la naturaleza de los intermetálicos que se forman, además del diagrama de fases hay que tener en cuenta la influencia de los otros elementos de aleación presentes en la región, como el silicio [8]. En este caso, se observa principalmente la presencia de la fase FeAl2, que es uno de los intermetálicos frágiles que se pueden formar.
4. Conclusiones
Se ha estudiado el proceso de soldadura por láser de dos combinaciones de materiales disimilares empleadas en el sector de automoción. De los resultados obtenidos en este trabajo se pueden extraer las siguientes conclusiones.
4.1. Soldadura de cilindros de aceros disimilares
- Se han podido soldar cilindros de aceros inoxidables disimilares, obteniendo los mejores resultados posicionando el foco del láser en la superficie de los cilindros, centrado en la intercara de ambos y empleando rampas de potencia
- La metodología para optimizar el proceso es fijar la potencia del láser al máximo y aumentar la velocidad de giro hasta el valor máximo que permita obtener una penetración completa hasta el núcleo de los cilindros
- Se producen tensiones residuales tractivas y un aumento de dureza en la región del acero martensítico adyacente al cordón de soldadura, por lo que es recomendable realizar un tratamiento final de relajación para evitar que el componente soldado falle por esa zona
4.2. Soldadura de chapas de aluminio-acero
- No se ha podido soldar por conducción debido a las dimensiones de la chapa de acero y al perfil de irradiancia del haz láser empleado
- La ventana de parámetros para obtener uniones soldadas libres de defectos es muy estrecha, obteniendo soldaduras demasiado débiles cuando el aporte energético es demasiado bajo, mientras que se producen grietas cuando se emplean condiciones demasiado energéticas
- Se detecta la fase intermetálica FeAl2 en la unión, lo que fragiliza la soldadura, produciendo agrietamientos en dichas zonas
5. Agradecimientos
Este trabajo ha sido financiado por el Gobierno Vasco a través de los programas Etortek y Gaitek (Manunet-2010-753) y mediante el presupuesto del Fondo Europeo de Desarrollo Regional (FEDER).
Referencias
[1] Wang, N.; Yamaguchi, T. and NISHIO, K. Interface Microstructure and Weld Strength of Steel/Aluminum Alloy Joints by Resistance Spot Welding. Applied Mechanics and Materials, 2012, vol. 117. pp. 1895-1899
[2] Choi, CY, et al. A Hybrid Joining Technology for Aluminum/Zinc Coated Steels in Vehicles. J.Mater.Sci.Technol, 2010, vol. 26, no. 9. pp. 858-864
[3] Joo, S. M., et al. Welding of Steel and Aluminum by Nd-YAG Laser. Key Engineering Materials, 2004, vol. 270. pp. 2389
[4] Z. Li, G. Fontana. Autogenous laser welding of stainless steel to free-cutting steel for the manufacture of hydraulic valves. Journal of Materials Processing Technology 74 [1-3] (February 1998) 174-182.
[5] J. R. Berretta, W. de Rossi, M. D. Martins das Neves, I. Alves de Almeida, N. Dias Vieira Junior. Pulsed Nd:YAG laser welding of AISI 304 to AISI 420 stainless steels. Optics and Lasers in Engineering 45 (2007) 960–966.
[6] S. Meco, G. Pardal, S. Ganguly, S. Williams, N. McPherson. Application of laser in seam welding of dissimilar steel to aluminium joints for thick structural components. Optics and Lasers in Engineering 67 (2015) 22–30
[7] Metals Handbook, Vol. 63, 10th Edition, ASM International, (1992)
[8] M. Potesser, T. Schoeberl, H. Antrekowitsch and J. Bruckner: EPD Congress 2006 (2006) pp. 167-176.