Desarrollo integral de un sistema versátil para el temple por láser
La incorporación de sistemas láser de alta potencia unidos a escáneres tanto 2D como 3D para distintos procesos de fabricación en el mercado actual de las máquinas-herramienta es cada vez más común. Los escáneres son sistemas basados en espejos móviles que dotan de movimiento al haz láser con velocidades lineales que superan los 10.000 mm/s y con alta precisión. Normalmente estos sistemas se usan para el marcado, texturizado, soldadura o pulido de piezas metálicas, procesos donde predominan la fusión y sublimación de material. Su viabilidad para procesos de tratamiento superficial por láser está todavía por determinar en determinadas aplicaciones debido, entre otros factores, a la gran dificultad que presenta el control de la temperatura durante el proceso, hecho que por otro lado es imprescindible para lograr resultados satisfactorios en operaciones de tratamiento térmico.
1. Temple por láser con ópticas de escaneo (TLE)
En el temple por láser tradicional, o temple por láser con ópticas fijas, el haz láser se forma con lentes y espejos a los que no se les dota de movimiento. En este caso la densidad de energía en la zona de trabajo es constante en forma y si se quiere cambiar la forma, para realizar por ejemplo temples más anchos, hay que cambiar las lentes y/o espejos por otros más adecuados. En cambio, en el temple por láser con ópticas tipo escáner (TLE) o temple por láser con ópticas móviles, se varía la densidad de energía en la zona de trabajo por medio de unos espejos que mueven un haz láser de menor tamaño que el área a templar. Así, para variar la densidad de energía en el campo de trabajo no es necesario parar el proceso y cambiar de lentes con los recursos de tiempo y dinero que conlleva. Además, mediante el TLE, se pueden conseguir temples menos energéticos, más localizados y versátiles con menores deformaciones de la pieza. Por otro lado, un escáner, también denominado sistema galvanométrico o sistema de ópticas móviles, consiste en uno, dos o tres ejes adicionales compuestos por espejos que dotan de movimiento al haz láser. Es un sistema óptico de espejos que giran y guían el haz láser dibujando una trayectoria marcada a muy alta velocidad y con muy poca inercia debido a que un pequeño movimiento de giro en el espejo provoca un movimiento lineal equivalente considerable del haz láser en el campo de trabajo. En la figura 1a) se observa un esquema de un escáner compuesto por dos espejos móviles con sus respectivos motores, uno por cada eje X e Y, y una lente de campo plano cuya función es que el haz láser llegue perpendicular a la superficie en el plano focal o campo de trabajo. Estos sistemas se pueden colocar sobre un elemento fijo, sobre la muñeca de un robot serie [1] o sobre el cabezal de una máquina- herramienta cartesiana [2].
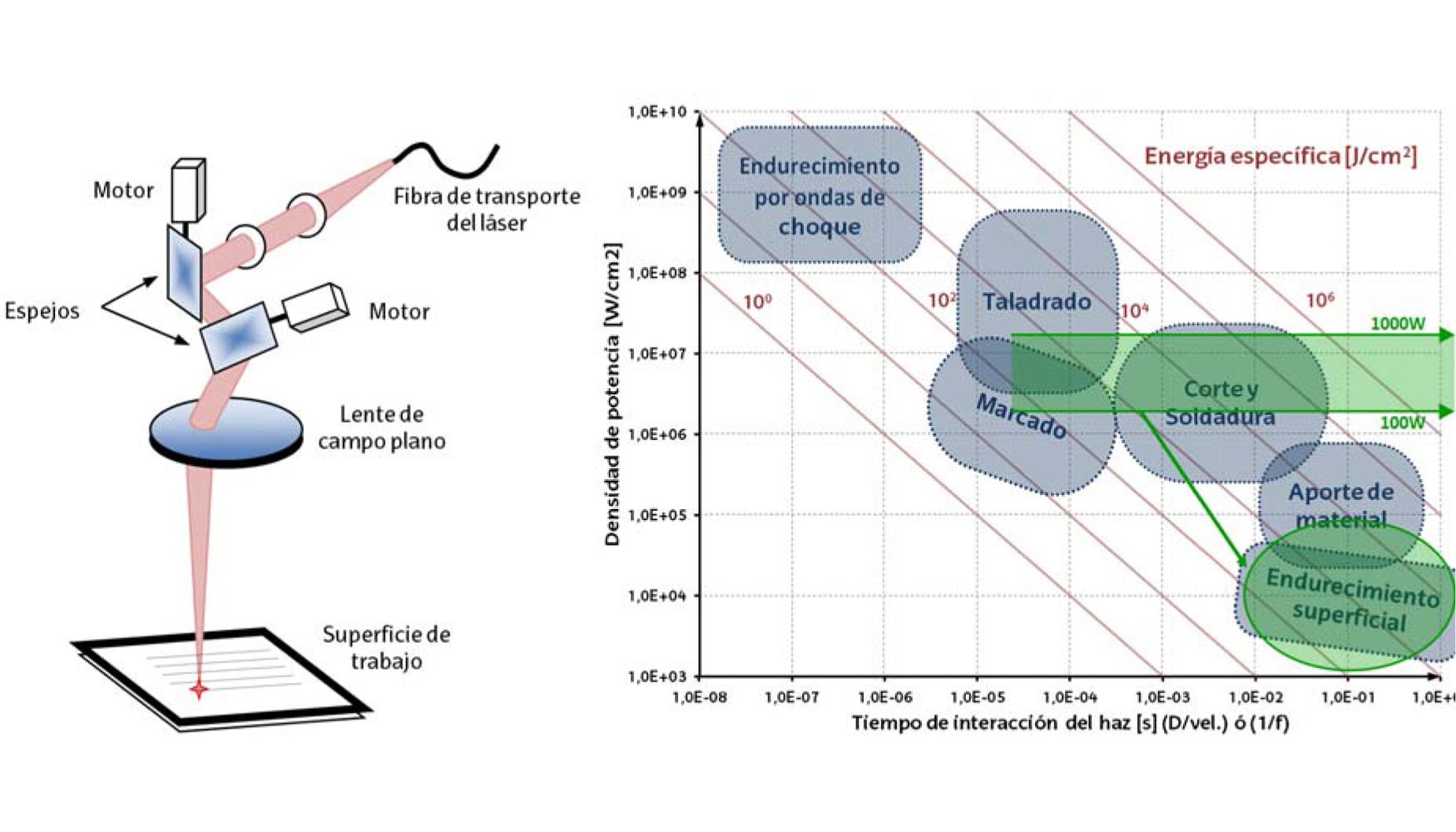
Los tipos de procesos láser que se pueden realizar con un escáner son muy variados. Un escáner es un sistema que se puede considerar ‘multi-tasking’ ya que con el mismo sistema óptico y láser es posible cortar [3], soldar [4], agujerear [5], marcar [6], texturizar [7], pulir [8] o en su caso, y por ahora menos común, templar [9]. Pero, como se puede observar en la figura 1b), cada proceso láser tiene sus requisitos en cuanto densidad de potencia del haz láser y tiempo de interacción entre el haz y la pieza. Así, un láser apto para el marcado o la soldadura por láser pero con altas densidades de potencia para poder templar, por medio de integrar un escáner en su sistema óptico puede llegar a templar o endurecer superficialmente una pieza. A diferencia del temple convencional, en el TLE coexisten dos velocidades, la velocidad de escaneo y la de avance. La velocidad de escaneo [mm/s] es la velocidad de movimiento real del haz láser, que en los escáneres actuales puede llegar a los 15.000 mm/s. Por otro lado está la velocidad de avance [mm/s] o área de avance [mm2/s] que es el movimiento real de avance de la línea templada sobre la pieza. Cuando se quiere dar un criterio de productividad sus dimensiones se dan en velocidad de área barrida, siendo está dependiente de la velocidad de escaneo [mm/s] y de la anchura del área barrida [mm]. No es comparable templar a velocidad de avance de 1 mm/s una línea de 5 mm de anchura que una línea de 10 mm, en un caso se estaría templando con un área de avance de 5 mm2/s y en el otro con 10 mm2/s. Normalmente el movimiento de avance es un movimiento lento que lo realizan los ejes de la máquina o el robot y el movimiento de escaneo es un movimiento muy rápido que lo realizan las ópticas de escaneo.
Por otro lado, para el proceso de TLE se proponen dos tipos de estrategias a la hora de barrer el área que se esta templando, la de barrido continuo y la de barrido por áreas [9]. La más simple y la que se va a utilizar en este trabajo es estrategia de barrido continuo. Esta estrategia, como se puede observar en la figura 2, consiste en ir moviendo el láser en una línea ascendente y descendente a la velocidad de escaneo mientras la pieza se mueve en la mesa de trabajo con la velocidad de avance. En este caso el centro del haz láser sólo pasa una vez por cada punto. Es un esquema mucho más sencillo que la estrategia de barrido por áreas pero no es posible variar la densidad de energía del área que se está barriendo en el sentido de avance. Además, como se observa en la figura 2, la variabilidad en la temperatura en un punto de la pieza durante el temple es intrínseca al proceso de TLE. Hay temperaturas de pico o máximas cuando el láser se encuentra por la zona donde se está midiendo y temperaturas de fondo o mínimas cuando el láser está a punto de volver a pasar por la zona. La temperatura de fondo es la responsable de la profundidad templada y la de pico puede provocar el sobrecalentamiento o la fusión parcial de la superficie.
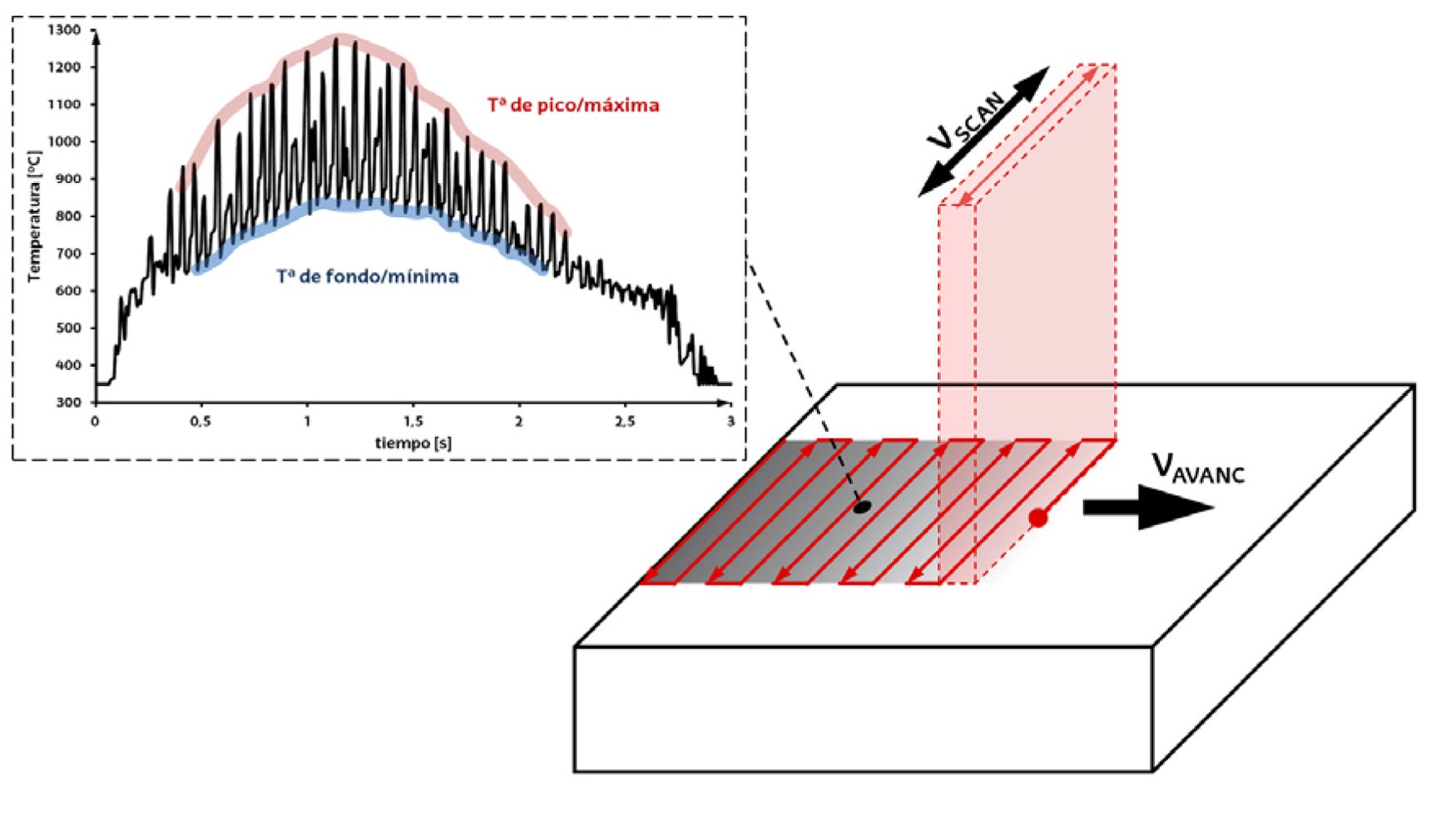
Así, en el presente trabajo se va a presentar el desarrollo realizado para integrar a una máquina cartesiana de 5 ejes un escáner con 2 ejes adicionales para realizar el proceso de TLE. Además, se explicará la integración de un control de temperatura activo que mantenga en todo momento la temperatura de la superficie de la pieza que se está templando constante. Para acabar, como ejemplo de aplicación del sistema, se presenta el templado de los bordes de doblado de una matriz de estampación de chapa en fundición nodular.
2. Integración del sistema de temple por escáner
Por un lado, en este apartado se explicará cómo se ha integrado el control de la temperatura sobre la superficie de la pieza. Esté se puede realizar de manera pasiva, para temples muy automáticos y repetitivos, pero en la mayoría de los casos se aconseja que se controle de forma activa o, lo que es lo mismo, variando la potencia del láser durante el temple para que la temperatura en la superficie se mantenga constante. En este caso se ha optado por un control de temperatura activo, un control PID, cuya sintonización se ha realizado mediante simulación numérica. Por otro lado, se explicará cómo se ha realizado la integración de los ejes de la máquina y del escáner. Para templar por láser con ópticas de escaneo geometrías complicadas y/o para templar por láser superficies de mayor extensión que el campo de trabajo del escáner, 120 x 120 mm, hay que sincronizar los ejes de la máquina y del escáner. En este caso en el centro de mecanizado láser se dispone de 7 ejes, los 5 ejes, lentos y de largo recorrido, de la máquina cartesiana y los dos ejes lineales, rápidos y de corto recorrido, del escáner. Por ello, la alineación y sincronización entre los ejes es muy importante ya que los dos ejes lineales rápidos del escáner se corresponden con los dos ejes lineales lentos de la máquina, el eje X y el eje Y.
2.1. Sincronización de los ejes de la máquina y del escáner
La máquina cartesiana Kondia-Aktinos 500 en la que se ha hecho la integración tiene tres ejes lineales (X1, Y1 y Z) a los que se les puede integrar un plato divisor con dos ejes rotativos adicionales, B y C. Todos ellos se pueden mover de forma continua en 5 ejes mediante el control numérico Fagor 8070. Además en el cabezal se encuentra situado un escáner 2D con los ejes U y V (X2 y Y2). En la figura 3 se observa la disposición en máquina de cada uno de los ejes mencionados.
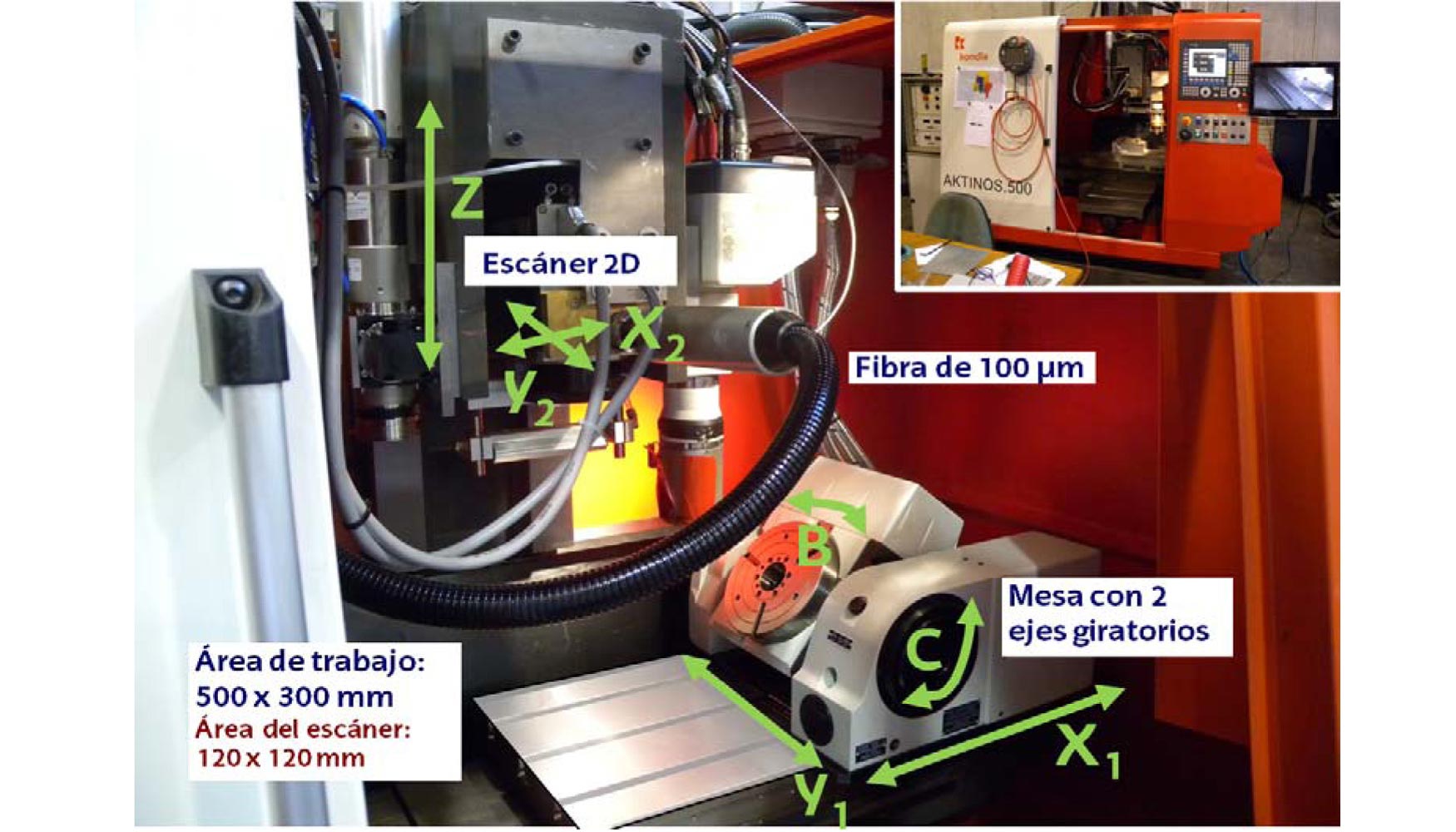
En la figura 4 se observan las partes que integran el sistema desarrollado para la sincronización de movimientos así como su interrelación. Se presenta en dos colores. El color azul se corresponde con el sistema disponible anteriormente a la integración de los ejes de la máquina y el escáner. Así, por un lado se introduce un programa, al control numérico Fagor 8070 de la máquina, que mueve los ejes de la máquina sin comunicarse en ningún momento con el escáner. Por otro lado, el software comercial Visual Laser Maker, un software de la empresa Rofin controla tanto los movimientos de los espejos del escáner como los parámetros de encendido y apagado del láser mediante ordenador interno al láser que es el que se encarga de todo. Este software está principalmente diseñado para el proceso de marcado por láser, siendo bastante cerrada y complicada una programación adicional, como puede ser la comunicación mediante sentencias en vez de trayectorias.
Por ello, para la sincronización de movimientos se ha desarrollado el sistema que figura en color verde. En primer lugar se ha instalado la tarjeta RTC4, de la empresa Scanlab, en un ordenador externo al láser. Esta tarjeta controla el movimiento de los ejes de escáner mediante sentencias programadas por el usuario. Además, se ha añadido un relé en la máquina, conexionado con el ordenador donde se encuentra la tarjeta, que se activa y desactiva mediante funciones M programadas en el control numérico Fagor 8070. Para finalizar, se ha cableado el ordenador con el resonador láser para poder controlar el apagado y encendido del láser así cómo su valor de potencia nominal. El movimiento de los ejes del escáner con junto con la potencia del láser y las nuevas funciones M de la máquina que se introducen en el programa de control de los ejes de la máquina se controlan mediante un software propio desarrollado para tal efecto y programado en lenguaje C# mediante el programa Visual Studio.
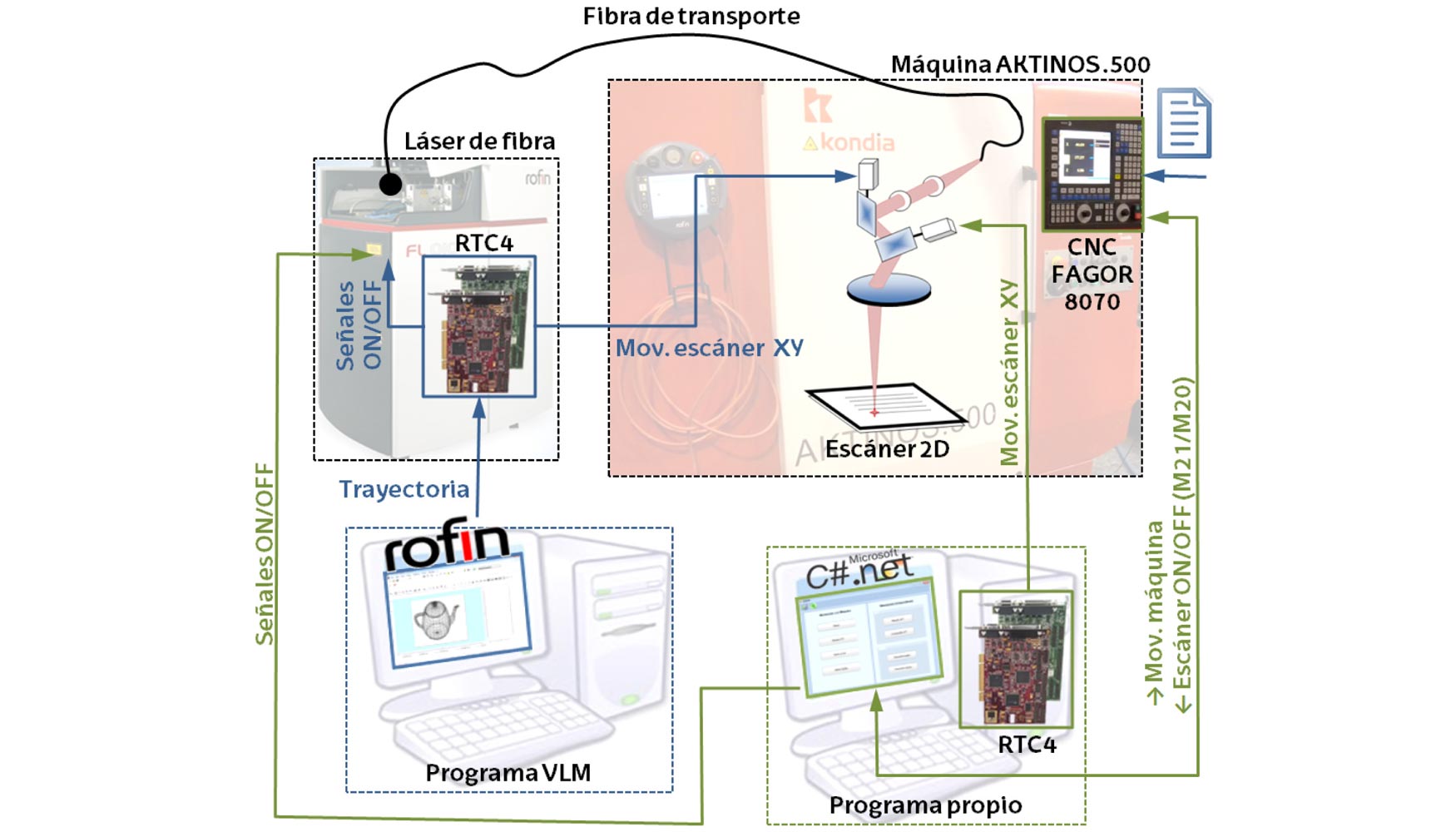
Se han diseñado distintos tipos de movimientos sincronizados entre máquina y escáner, pero para el proceso de TLE se ha optado por mantener en todo momento la trayectoria marcada por los ejes del escáner perpendicular a la marcada por los ejes X e Y de la máquina. Para ello, previamente al templado, se saca el archivo APT de la trayectoria de avance o de máquina que se quiere templar. Si está es muy complicada se programa mediante un software de CAM. A partir de esta trayectoria se saca la trayectoria de escaneo mediante el ángulo de giro con respecto a la horizontal y la longitud de la hipotenusa que depende de la anchura del área a templar, pudiendo ser esta anchura variable. Estos cálculos se realizan sobre los ejes X e Y que son los que están repetidos. El requisito más importante durante la programación es que el temple sea uniforme en velocidades desde el inicio hasta el final. En la figura 5 se observan el resultado del marcado de un octaedro y de un círculo, sincronizando los ejes de la máquina, a 1 mm/s de velocidad de avance, y los ejes del escáner, a 1.000 mm/s de velocidad de escaneo.
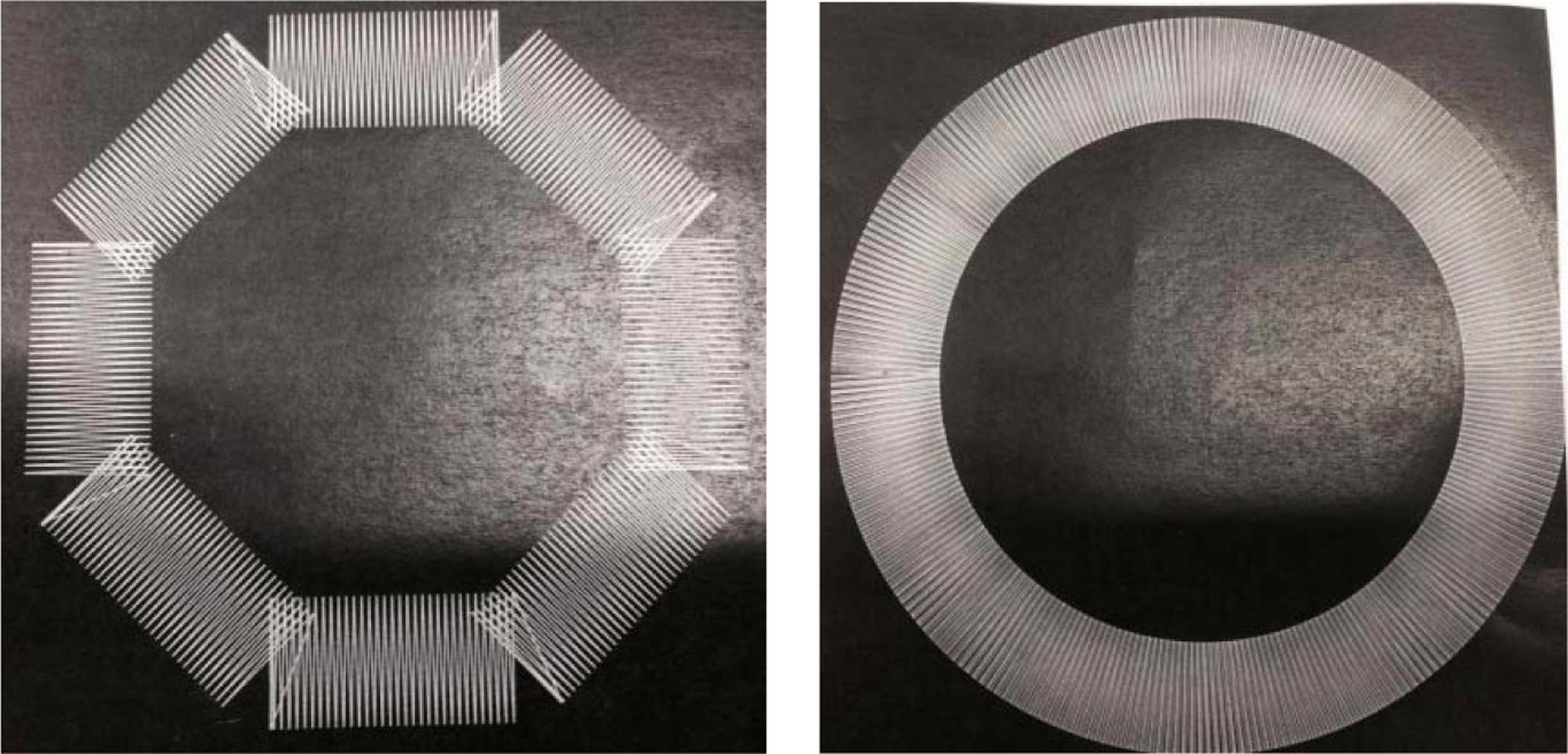
2.2. Control activo de temperatura
Como se ha comentado, el proceso de temple por láser es inconcebible industrialmente sin el control de la temperatura que se da durante el proceso. En este caso, las piezas a templar son piezas de distinta naturaleza, con distintas geometrías, materiales y estados superficiales. Estas características de piezas implican que para el proceso de TLE se haya optado por implementar un control activo en lazo cerrado. Así, en la figura 6 se muestra un esquema del control de temperatura PID en lazo cerrado implementado. La temperatura durante el proceso se mide sin contacto con un pirómetro de dos colores que da la temperatura real sin necesidad de introducir parámetros de emisividad. Esta temperatura la recoge un ordenador que la compara con la temperatura de consigna a la que se quiere realizar el temple. El error en temperatura sirve como entrada a un control PID digital que ajusta y obtiene una variación de potencia que se le suma a la del instante anterior y se envía al resonador láser. Un haz láser con la potencia requerida es guiado por una fibra al escáner. El escáner dirige el haz láser hacia la zona de la pieza correspondiente calentando la pieza hasta la temperatura de consigna deseada y cerrando así el ciclo de control.
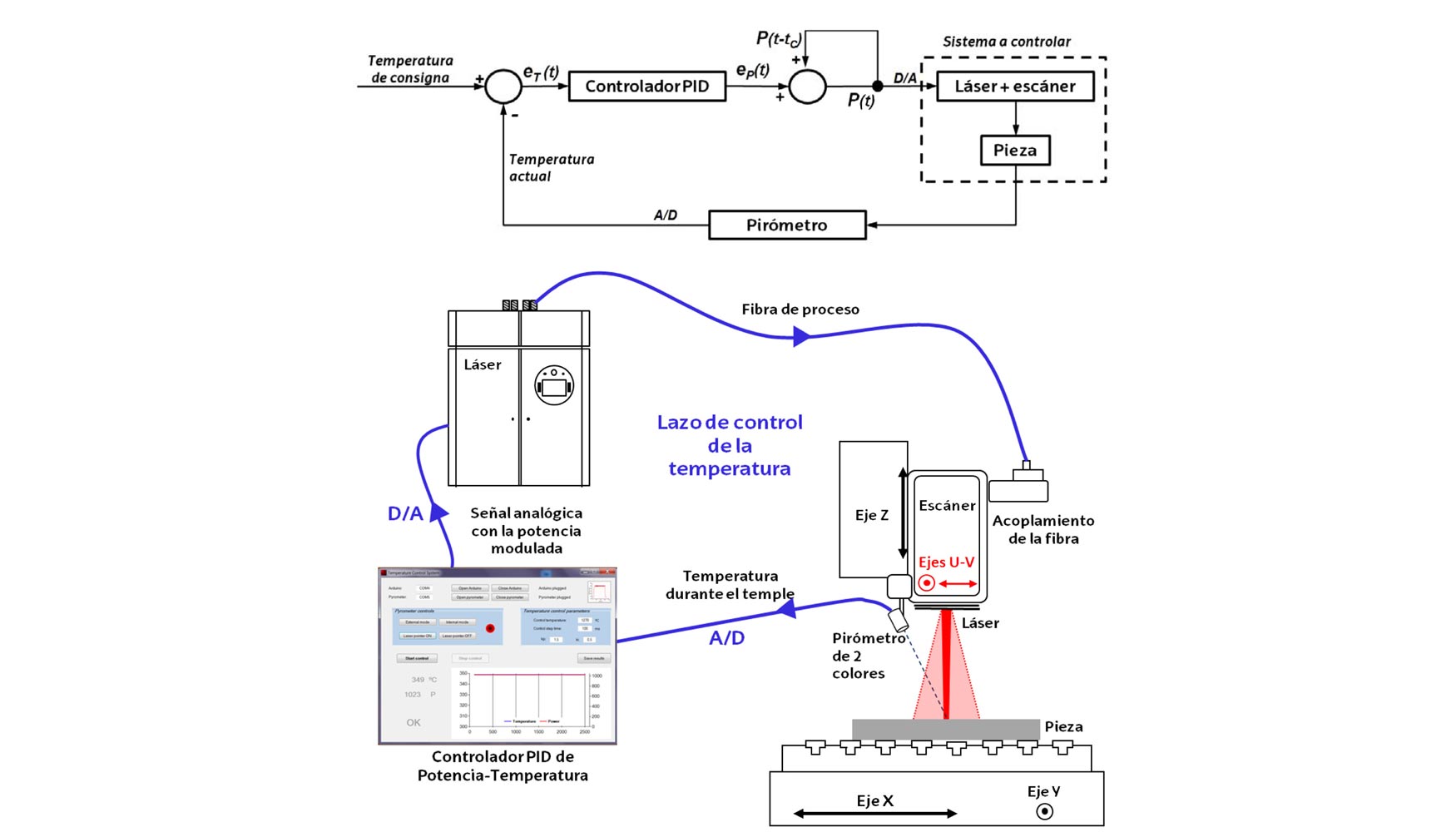
Por otro lado, en lo referente a la medición de temperaturas, el rizado de la temperatura que se produce durante el proceso de TLE es inevitable e intrínseco al propio proceso, esté se puede minimizar pero nunca anular. El rizado provoca una gran variabilidad de la temperatura en la superficie de la pieza durante el proceso, lo que dificulta bastante el control de está. Lo ideal sería introducir el pirómetro por el mismo camino óptico que lleva el haz láser pero daría errores de posicionamiento y, por lo tanto, medidas de temperatura erróneas [10]. En este caso se ha decidido poner el pirómetro externamente al camino óptico. Así, lo ideal durante el control sería ver en qué punto del barrido la temperatura bajo el haz láser tiene su pico máximo y posicionar en ese punto el pirómetro, pero este punto no es intuitivo y por simplicidad se ha apuntando al centro de la línea que se está templando o, lo que es lo mismo, al centro de la trayectoria del movimiento de la máquina. Así, en la gráfica de la figura 7 se presentan diferentes medidas de temperatura para un mismo ensayo. Por un lado, está en color azul la correspondiente a la temperatura bajo el haz láser que hace referencia en todo momento con la temperatura máxima que hay durante el proceso. Idealmente es la que debería mantenerse constante, pero, como se ha comentado anteriormente, para ello el pirómetro debe de seguir el camino óptico del láser y esto no es posible sin cometer errores. Por otro lado, está en negro la temperatura que mide el pirómetro moviéndose a la velocidad de avance, la medida en el punto verde. Al no estar el láser incidiendo en todo momento en esa posición, el rizado que tiene es mucho mayor. Debido a esta variabilidad intrínseca del proceso si se usa cualquier punto de esta temperatura para el control, esté, sería inestable. Por ello, el pirómetro se programa para que guarde únicamente el valor máximo de todos los que recoge durante el ciclo de control. Para una correcta adquisición de este valor la frecuencia de control debe de ser menor a la frecuencia de escaneo y recoger en cada periodo de control el valor máximo de temperatura de entre todos los valores recogidos por el pirómetro para sacar el error en temperatura que se introduce al control PID.
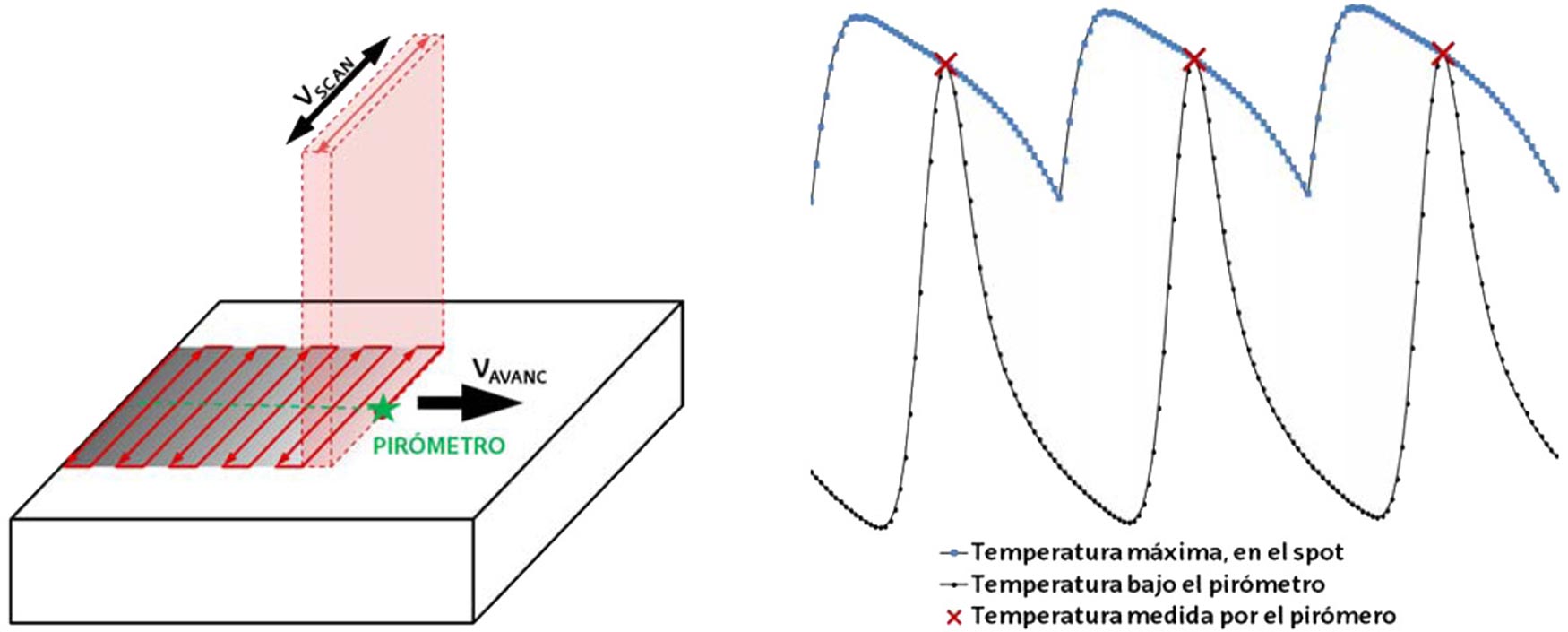
Para evitar o minimizar los ensayos necesarios durante la sintonización de las constantes del control de temperatura PID, esta sintonización se ha realizado mediante una simulación del control [11]. En este caso, debido a su complejidad y versatilidad, no existe una cuación de transferencia única que rija el comportamiento real del proceso de temple por láser con ópticas de escaneo para poder simularlo. Por ello, se ha usado como ecuación de transferencia un modelo de simulación numérica, Lathem, al que se le ha integrado un control de temperatura PID simulado, idéntico al simulado en la máquina real. En el esquema de la figura 8 se observan las distintas relaciones y equivalencias entre el conjunto real y el conjunto simulado. El control y el proceso simulado son códigos programados íntegramente en Matlab que se intercambian información cada periodo de control donde el programa de simulación numérica Lathem hace de ecuación de transferencia que alimenta al control. En cambio, en el conjunto real el proceso de TLE de una pieza real es la ecuación de transferencia que alimenta al control digital programado en un ordenador.
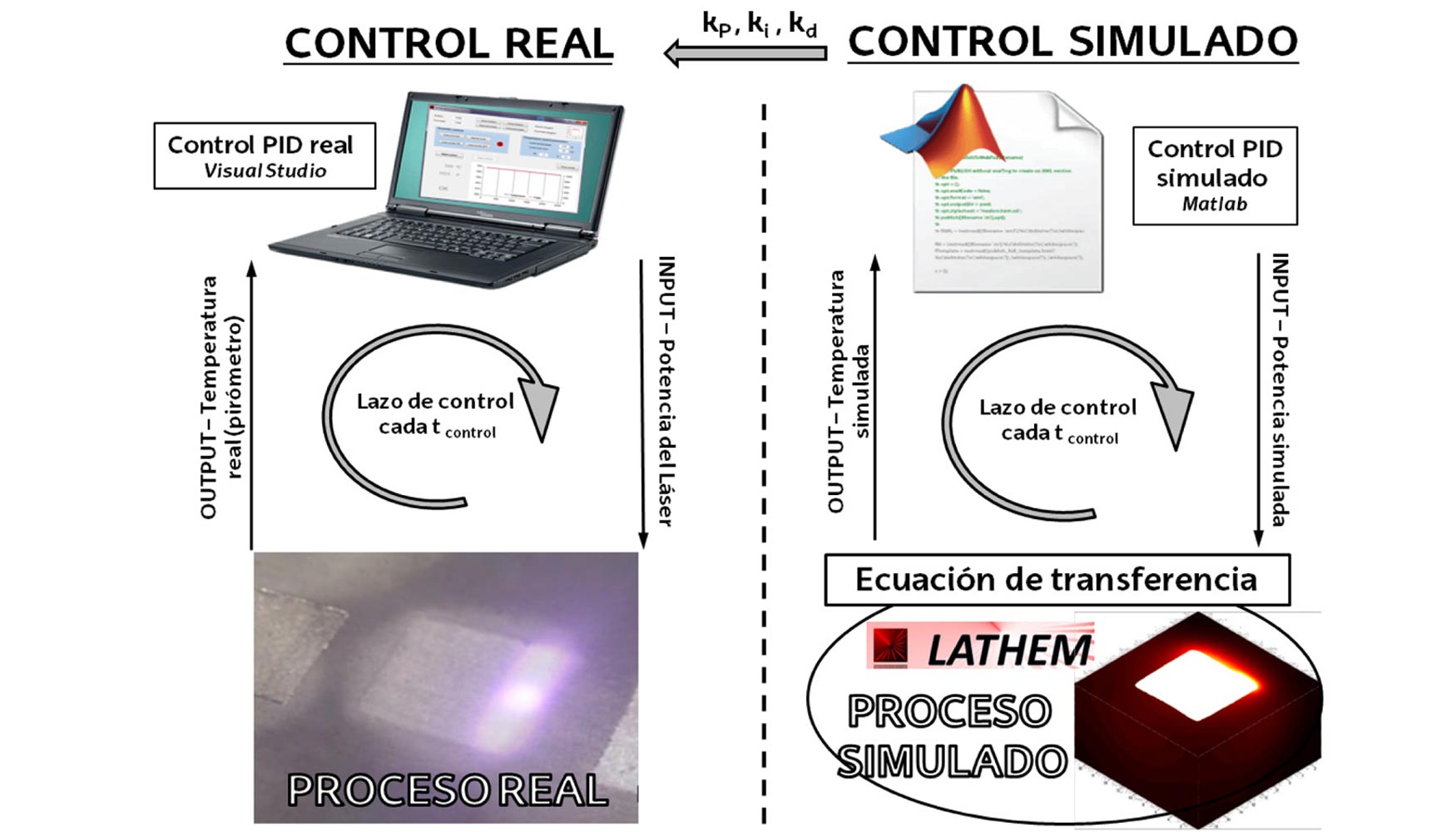
Como resultado del control de temperatura se obtiene un templado uniforme durante todo el proceso de temple. En la figura 9a) se han realizado distintos ensayos a distintas velocidades de avance y temperaturas de control. En este caso las constantes del control se han mantenido invariables. Así, para un mismo material, el proceso se hace independiente de las características superficiales, de oxidación o rugosidad, y de la geometría de la pieza. Además, se consigue una temperatura uniforme en toda la superficie de la línea templada. En la gráfica figura 9b) se pueden observar partes, como la salida de la pieza, que sin un control de temperatura estarían sobrecalentadas o fundidas, que se han mantenido a temperatura constante en base a disminuir la potencia hasta los 300 W.
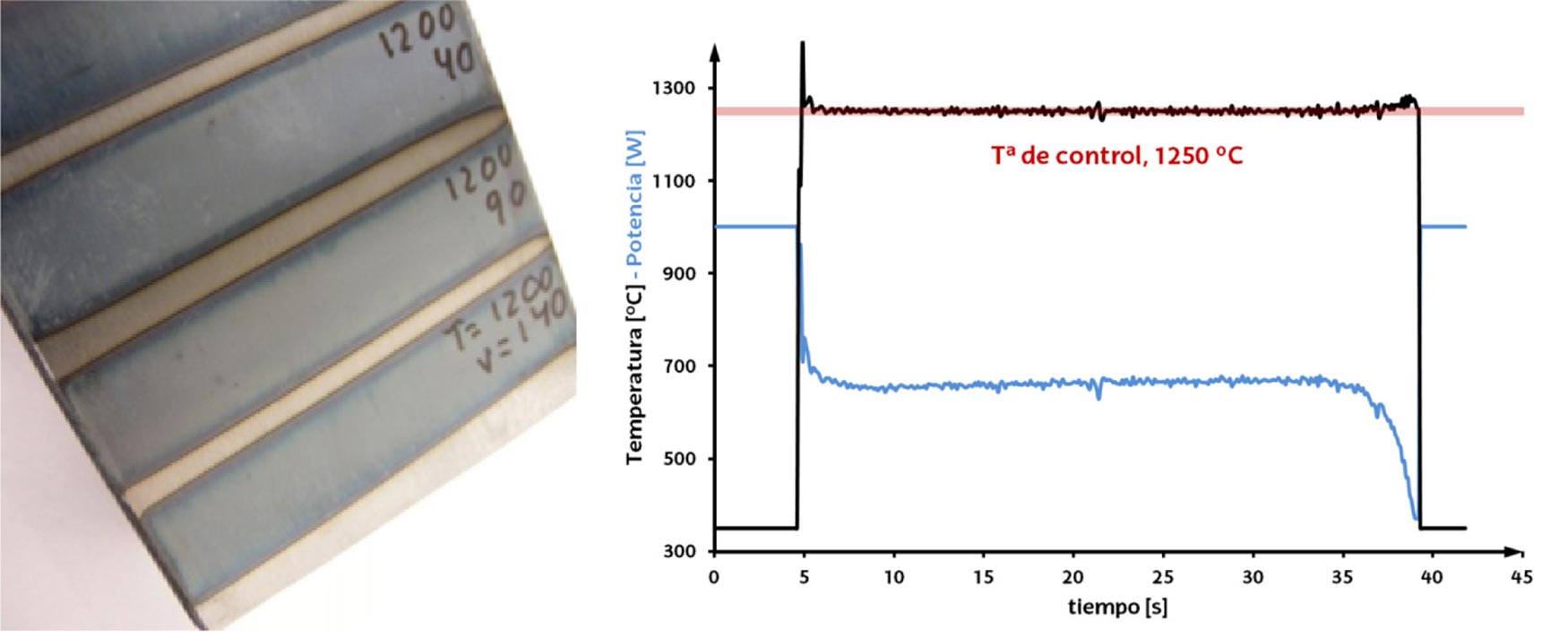
3. Templado de pieza test sobre fundición nodular
Como ejemplo de aplicación de la integración del sistema se han templado mediante el proceso de TLE los bordes de doblado de una matriz de estampación de chapa. Previamente al templado de la pieza se han hecho unos ensayos de caracterización del proceso de TLE sobre fundición nodular para obtener los parámetros óptimos de trabajo, ya que no se había trabajado anteriormente con este material.
3.1. Condiciones óptimas para el TLE sobre fundición nodular
Para obtener los parámetros óptimos de temple sobre fundición nodular se han realizado una serie de ensayos sobre un tocho rectificado de 20 mm de espesor. En los ensayos se han variado las velocidades de avance, velocidades de escaneo y temperaturas de control. En la tabla 1 se muestran los parámetros de entrada y los parámetros medidos para el ensayo Nº19 que es el que se ha considerado óptimo en cuanto a que el espesor templado sea máximo sin que se sobrecaliente en exceso la pieza.

En la figura 10 se observan los resultados del ensayo Nº19. Se ha obtenido una profundidad templada de casi 500 micras con una dureza media de 57 HRC constante en toda el área templada. Por otro lado la deformación máxima medida sobre una longitud de 30 mm es de 4 μm positiva en el centro de la línea templada y de otras 4 μm negativas en los extremos de la línea templada pero en la zona blanda, sin templar. Por otro lado se considera que con las mismas condiciones y parámetros de temple sobre la pieza test real habrá menores deformaciones ya que aunque las tensiones residuales sean las mismas el espesor es mucho mayor en la pieza test.
El principal problema durante el proceso de TLE sobre fundición nodular ha sido el control de la temperatura durante el proceso. La fundición GGG70L se caracteriza por estar compuesta por unas esferas de grafito hasta 100 micras de diámetro. Si estas esferas se encuentran sobre la superficie donde incide el láser, se crean zonas donde se absorbe más cantidad de radiación láser que en el resto y se dan picos de temperatura bastante elevados que desestabilizan el control. Para evitar esto se ha vuelto a sintonizar el control con parámetros diferentes a los válidos para otros tipos de aceros que no presentan una superficie tan poco homogénea.
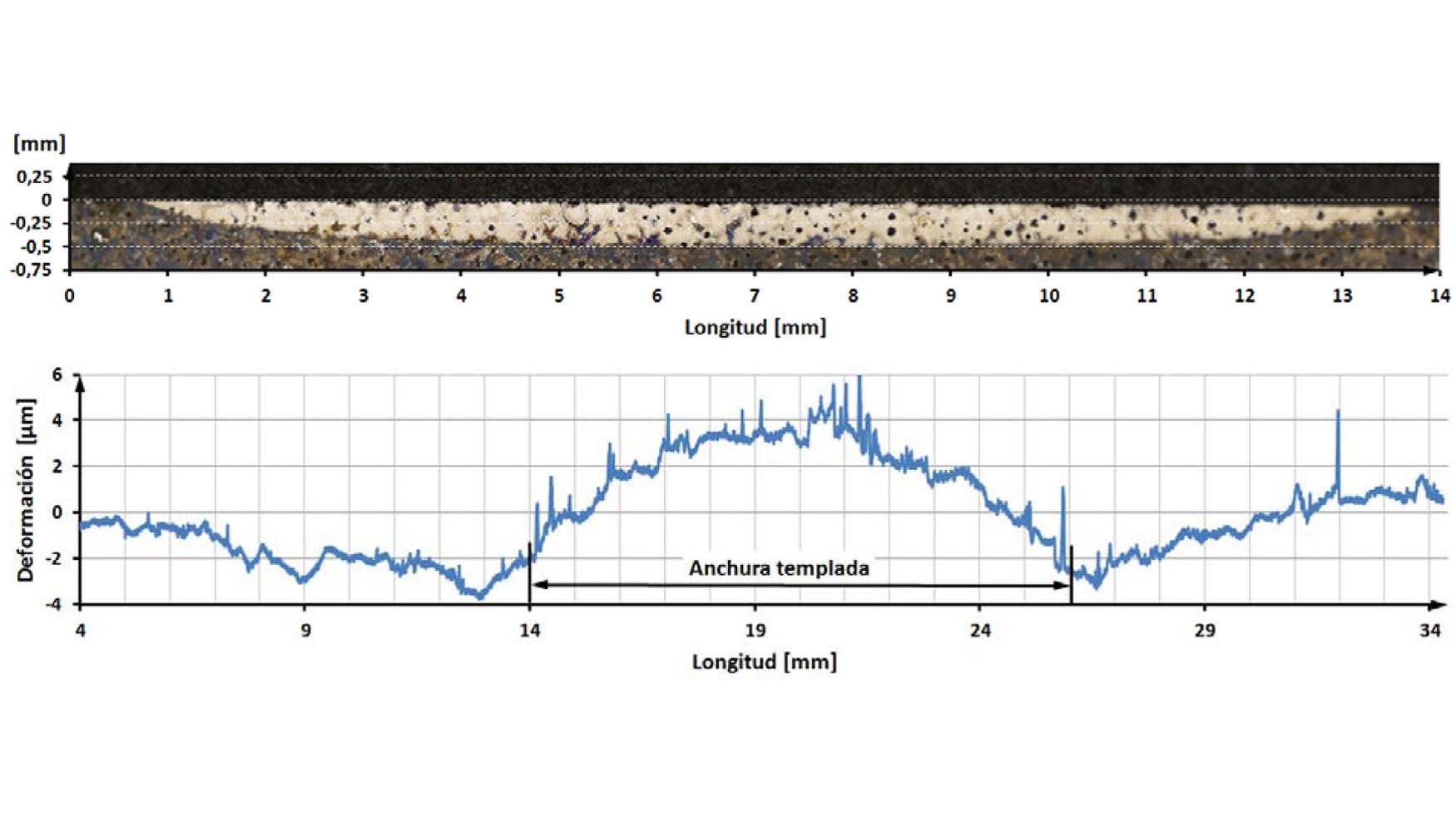
3.2. Templado de los bordes de una matriz test para la estampación de chapa
Como ejemplo de aplicación de una pieza real con geometría compleja se han templado mediante el proceso de TLE los bordes de doblado de una matriz de estampación de chapa. Se trata de una pieza test mecanizada en 5 ejes sobre fundición nodular GGG70L a la que se le han realizado radios de acuerdo de 3, 5 y 10 mm en distintas zonas de la matriz, figura 11a).

En cuanto al templado se ha decidido realizar con los 3 ejes lineales, no rotativos, de la máquina más los 2 ejes del escáner. A pesar de que la integración se ha realizado para los 5 ejes de la máquina, y que usar los 5 ejes no supone más trabajo adicional, se ha decido usar sólo tres para ver lo que ocurre cuando el láser se encuentra a cierto ángulo de la superficie, diseñándose zonas en la matriz test donde el haz láser pasa de estar perpendicular a la superficie, 90º, a estar paralelo de ésta a 0º. En cuanto a los parámetros del láser, las velocidades y la temperatura del proceso se han utilizado los valores del ensayo Nº19 considerado como óptimo en el apartado anterior y cuyas condiciones se observan en la tabla 1. El resultado del proceso se observa en la figura 11b), donde se ha obtenido un templado uniforme en las tres zonas que se han templado, sin sobrecalentamientos indeseados, gracias al control de temperatura en lazo cerrado. La dureza del material base de 22 HRC ha pasado a 56 HRC en la zona templada, siendo está constante por todas las áreas templadas. Por otro lado se ha observado que en geometrías con cambios de ángulo no es posible templar en tres ejes no es posible templar ángulos relativos menores de 30 grados con respecto al ángulo del haz láser que le está incidiendo.
Por último hay un aumento de profundidad templada en los redondeos de los bordes debido a una acumulación del calor, aunque la temperatura de la superficie se mantenga constante en el borde la conducción de calor es menor por haber menos masa y se acumula más el calor. En este caso la profundidad máxima se ha observado en el redondeo de radio 3 mm con una profundidad templada de casi 2 mm. En el redondeo de radio 10 mm la profundidad la del ensayo Nº 19, de unas 600 μm.
4. Conclusiones
En el presente trabajo se ha presentado el diseño y desarrollo de un sistema versátil para realizar operaciones de temple por láser con ópticas de escaneo, TLE. Para ello, se han integrado los 5 ejes de la máquina y con los 2 ejes del escáner en cuanto a sincronización de movimientos y la trayectoria que tiene que hacer cada uno. Por otro lado, debido a los requerimientos del proceso de temple por láser, se ha integrado al conjunto un control de temperatura activo en lazo cerrado, que en este caso, el templar con ópticas de escaneo tiene más dificultad por el rizado de la temperatura y las altas velocidades con las que se mueve el haz láser. Para sintonizar el control, esté se ha integrado y modelizado en un programa de simulación numérica propio, Lathem.
Tras el desarrollo del sistema se ha puesto como ejemplo de aplicación una matriz test para la estampación de chapa fabricada en fundición nodular GGG70L cuyas condiciones de ensayo se han sacado previamente sobre un tocho plano del mismo material. Así, se puede concluir diciendo que el sistema desarrollado es capaz de templar por el proceso de TLE piezas de geometrías complejas en 5 ejes máquina + 2 ejes escáner manteniendo una temperatura constante y dada por el usuario sobre la superficie de la pieza.
5. Agradecimientos Este trabajo se ha realizado gracias a la financiación de la Universidad del País Vasco UPV/EHU mediante la UFI 11/29 y del Gobierno Vasco dentro de los proyectos Etortek coordinados por el CIC marGUNE.
Referencias
[1] Blackbird Robotics. ‘ScanControlUnit (SCU)’. Disponible en la web: http://www.blackbird-robotics.de/. Consultado el 10 de abril de 2015.
[2] DMG MORI. ‘Gama de máquinas Lasertec’. Disponible en la web: http://www.moriseiki.com/. Consultado el 10 de abril de 2015.
[3] D. Lee, R. Patwa, H. Herfurth, J. Mazumder. High speed remote laser cutting of electrodes for lithium-ion batteries: Anode, Journal of Power Sources, 240 (2013), 368-380.
[4] A. Wetzig. Developments in beam scanning (remote) technologies and smart beam processing - Handbook of Laser Welding Technologies, Woodhead publishing, (2013).
[5] I. Arrizubieta, A. Lamikiz, S. Martínez, E. Ukar, I. Tabernero, F. Girot. Internal characterization and hole formation mechanism in the laser percussion drilling process, International Journal of Machine Tools & Manufacture, 75 (2013), 55-62.
[6] L. Costa, K. Lansford, D. Rajput, W. Hofmeister. Unique corrosion and wear resistant identification tags via LISI laser marking, Surface & Coatings Technology, 203 (2009), 1984-1990.
[7] D. Braun, C. Greiner, J. Schneider, P. Gumbsch. Efficiency of laser surface texturing in the reduction of friction under mixed lubrication, Tribology International, 77 (2014), 142-147.
[8] F.E. Pfefferkorn, N.A. Duffie, X. Li, M. Vadali, C. Ma. Improving surface finish in pulsed laser micro polishing using thermocapillary flow, CIRP Annals - Manufacturing Technology, 62 (2013), 203-206.
[9] S. Martínez, A. Lamikiz, I. Tabernero, E. Ukar. Laser hardening process with 2D scanning optics, Physics Procedia - LANE 2012, 39 (2012), 309-317.
[10] V. Wippo, M. Devrient, M. Kern, P. Jaeschke, T. Frick, U. Stute, M. Schmidt, H. Haferkamp. Evaluation of a pyrometric-based temperature measuring process for the laser transmission welding, Physics Procedia - LANE 2012, 39 (2012), 128-136.
[11] P. Zhang. Industrial control system simulation routines, Advanced Industrial Control Technology Laser hardening process with 2D scanning optics, 19 (2010), 781-810.