Anton Paar se prepara para el futuro gracias a la tecnología de soldadura robotizada inteligente
La empresa austriaca Anton Paar fabrica aparatos de medición de alta precisión para diferentes sectores. Para ello, los equipos de investigación, ingeniería y producción involucrados se esfuerzan por superar los límites de lo posible. En la actualidad, Anton Paar GmbH es pionero en el mercado de la medición de la densidad y la concentración, la reometría y el análisis de CO2 disuelto. Dada la creciente escasez de trabajadores cualificados y el aumento constante del número de piezas, se exigen soluciones de producción inteligentes. Por ello, la empresa invirtió en una celda de soldadura robotizada de última generación.
Hasta ahora, todos los componentes de los dispositivos de medición y control fabricados en Graz se soldaban a mano. Esto se debía a que usar sistemas de soldadura robotizada para fabricar lotes pequeños, de entre 1 y 400 unidades, parecía poco rentable. El crecimiento constante del volumen de negocio, la escasez de mano de obra cualificada en el mercado laboral austriaco y las innovadoras tecnologías robóticas, gracias a las cuales la soldadura automatizada resulta económica incluso para lotes pequeños, llevaron a la empresa de alta tecnología a invertir en un moderno sistema de soldadura robotizada. La flexibilidad en todas las líneas, combinada con una alta rentabilidad, fue el requisito de los especialistas en medición y control de Anton Paar. Esta flexibilidad se refiere tanto al número, la forma, el tamaño y el posicionamiento de los componentes, como al uso de distintos procesos de soldadura.
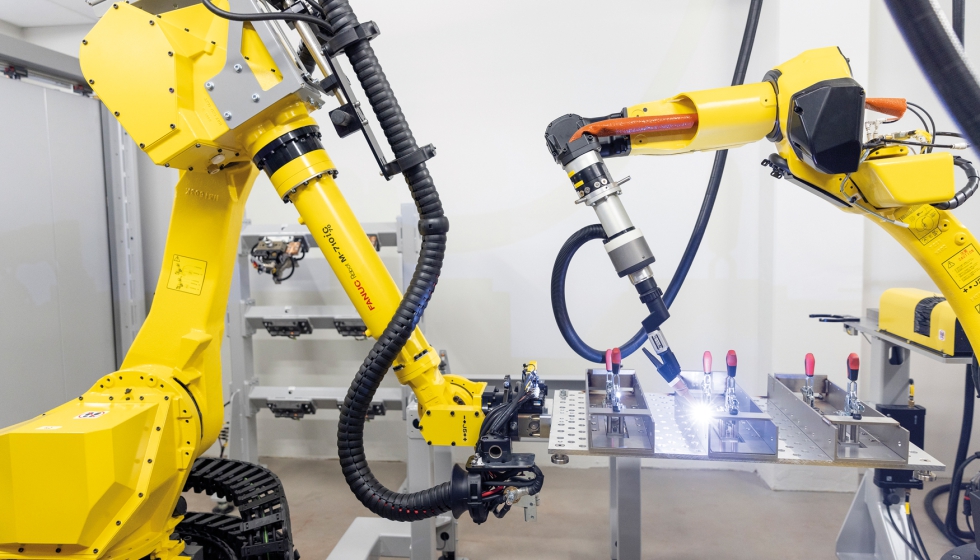
Dominik Santner, director de Operaciones de Anton Paar GmbH, subraya: “La escasez de trabajadores cualificados y el aumento continuo en la cantidad de unidades fabricadas exigen nuevas soluciones en la producción. La nueva celda de soldadura robotizada es un gran paso en la automatización de nuestra producción. Si siguiéramos soldando manualmente nuestra tecnología de sensores de procesos, tendríamos enormes dificultades para alcanzar las cantidades previstas en los próximos años”.
Soldadura autónoma y diversidad de componentes
Desde el principio, los expertos de Anton Paar se centraron en la autonomía de los sistemas: Una vez configurado, el sistema de soldadura debe ser capaz de realizar una tarea completa de principio a fin de una sola vez; por ejemplo, soldar un conjunto de componentes diferentes, como carcasas de transductores, vigas maestras o contra enfriadores, y debe hacerlo de forma totalmente independiente y sin la intervención de soldadores.
Componentes con diferente forma, peso y tamaño, distintas opciones de agarre, posicionamiento y almacenamiento, la posibilidad de utilizar dos procesos de soldadura diferentes (TIG y MIG/MAG) en un componente, así como el uso del gas de respaldo necesario para los cuerpos cilíndricos para proteger los componentes. Todas estas ideas convirtieron el diseño del sistema en un reto especial para los equipos de ingeniería y programación.
“Buscábamos un socio fiable que fuera muy similar a nosotros en cuanto a precisión y calidad. Alguien que nos escuchara con atención, respondiera a nuestros deseos y propusiera soluciones sostenibles. El tipo de socio que nos daría ventajas competitivas en los próximos años”, explica Daniel Moik, director del Departamento de Tecnologías de Unión. “Fronius International cumplía estos criterios para una colaboración sostenible. En estrecha cooperación con nuestros técnicos, el equipo de Welding Automation desarrolló una celda de soldadura robotizada que cumplía nuestros requisitos en todas las áreas. Además, Fronius está dispuesto a colaborar para seguir desarrollando el sistema y adaptarlo a nuevas necesidades”.
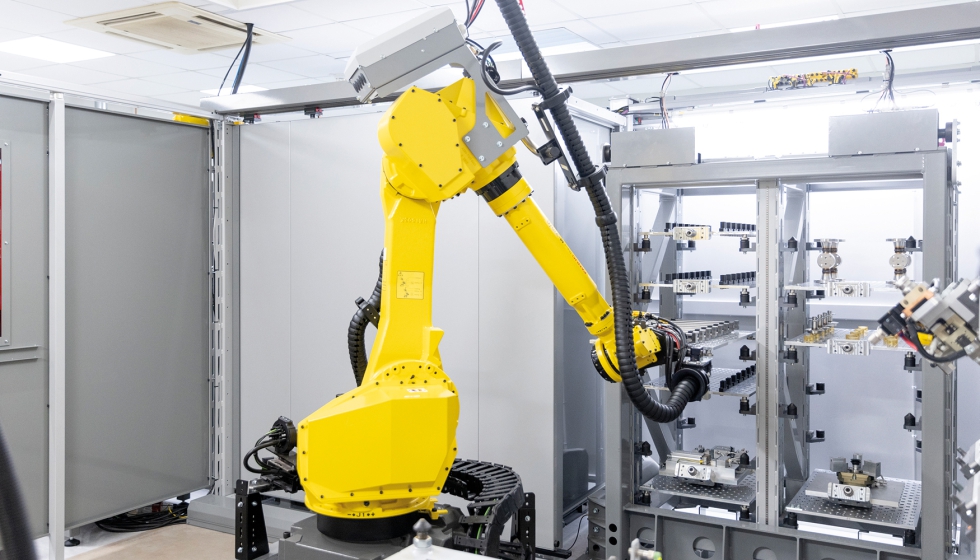
Sinónimo de eficiencia: Fronius Pathfinder
En Anton Paar, los nuevos cordones de soldadura se programan offline (fuera del sistema de soldadura) y no directamente en la celda, como suele ser el caso. En lugar de detener el trabajo de soldadura en curso para programar, la soldadura continúa, lo que aumenta la productividad. Para ello, los técnicos de soldadura importan en el Fronius Pathfinder los datos CAD de los componentes del aparato de medición que se van a soldar. A continuación, se prueban diversos escenarios de ensamblaje, se definen secuencias de soldadura y se optimizan durante el proceso de simulación.
Esto afecta a las trayectorias de aproximación, los ángulos de incidencia de la antorcha, las compensaciones de la antorcha en las esquinas y todas las reorientaciones del robot de soldadura. Pathfinder detecta cuando se supera el alcance del robot, los denominados límites de los ejes. Al corregir la ubicación de la pieza y colocarla dentro de la longitud del brazo del robot de soldadura, los operadores del software evitan posibles colisiones de la antorcha con cantos de componentes desde el principio.
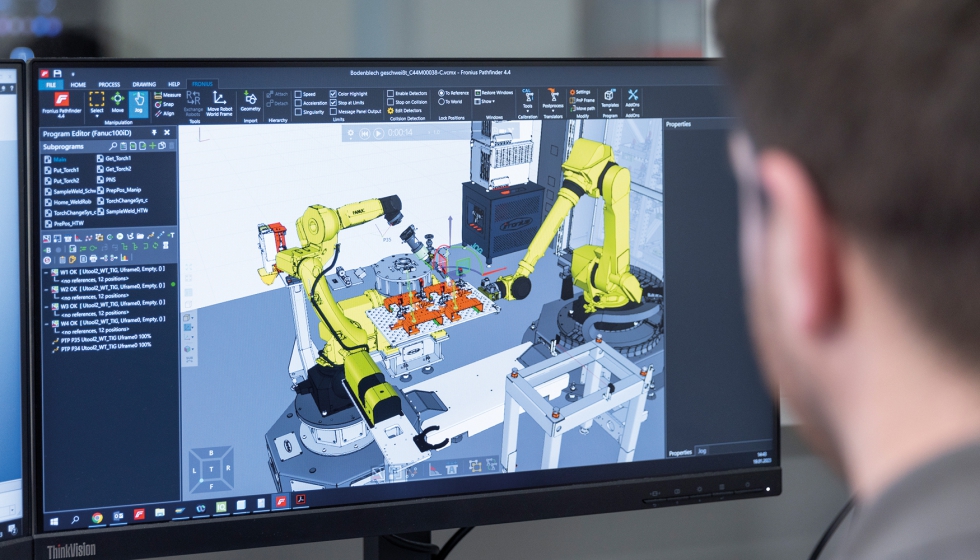
Detección los errores a tiempo
Si es necesario corregir la trayectoria, los respectivos puntos programados pueden desplazarse cómodamente arrastrando y soltando (Drag & Drop). Si es necesario cambiar la aproximación al componente, el soldador puede simplemente pulsar ‘Reset’. A continuación, el robot virtual se desplaza a la posición de origen para iniciar una nueva aproximación. En un caso de funcionamiento real, se tendría que liberar el robot en un proceso que requiere mucho tiempo, moverlo a la posición de origen mediante el control y reiniciar el proceso de programación. Al optar por el software de programación y simulación offline Pathfinder, los expertos de Anton Paar no solo ganan un tiempo valioso para realizar trabajos de soldadura, sino que también identifican las fuentes de error con antelación.
Una vez completado un programa de soldadura en Pathfinder, se traduce al código específico del robot de soldadura Fanuc mediante el denominado postprocesador. A continuación, puede transferirse al equipo de soldadura mediante transferencia de datos, por ejemplo, con una conexión LAN. Uno de los elementos destacados que constituye una gran ayuda a la hora de planificar la producción es la función denominada ‘determinación del tiempo de ciclo’, que incluye las velocidades de soldadura, el tiempo de flujo previo de gas o el de llenado de cráter final. En comparación con la programación realizada con el control del robot, el uso de Pathfinder supone un ahorro de tiempo de hasta el 90%, dependiendo de la geometría del componente y de los requisitos de soldadura.
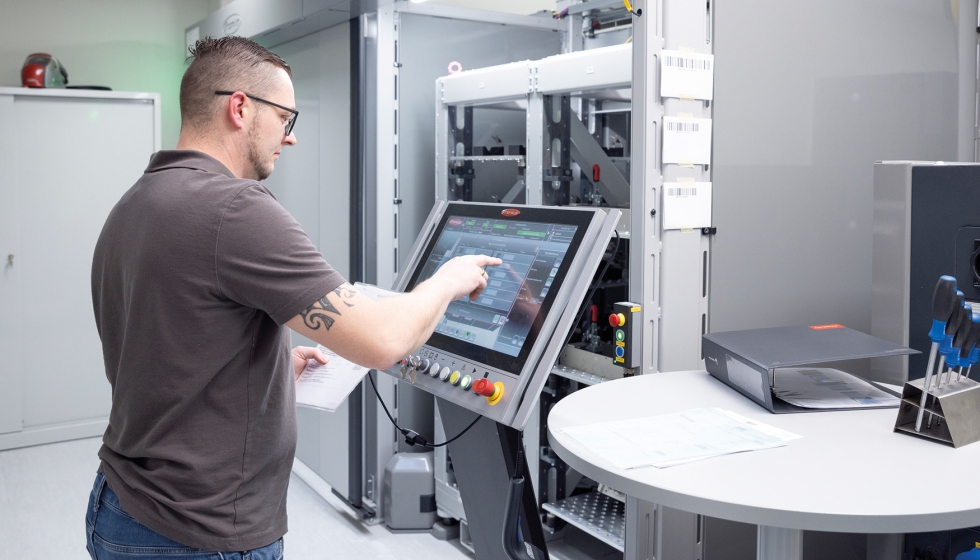
Personalizado para Anton Paar
Para soldar la gran variedad de componentes existentes, Anton Paar dispone de flujos de trabajo personalizados, entre los que se encuentran tres flujos de trabajo principales que ilustran la enorme flexibilidad del rango de componentes.
Flujo de trabajo 1: Los componentes se sueldan en el posicionador de giro e inclinación. En este proceso, un palé cargado con componentes se retira de la estantería de palés y se almacena temporalmente en una mesa de palés. A continuación, el robot de manipulación elige la pinza adecuada para la recogida de componentes. Hay seis pinzas diferentes situadas en una denominada estación de pinzas. Una vez equipado con las pinzas, el robot de manipulación recoge los componentes y los coloca en unas fijaciones específicas para cada componente, que ya están colocadas en la mesa giratoria inclinable. Se retira un solo componente a la vez, se une y se vuelve a colocar en el palé.
Flujo de trabajo 2: Los componentes se sueldan directamente en los palés, para lo cual el robot de manipulación transporta los palés desde la estantería y los coloca delante del robot de soldadura. Durante la soldadura, los robots de manipulación y de soldadura pueden realizar movimientos coordinados entre sí y soldar geometrías de cordones sencillas y complejas.
Flujo de trabajo 3: Los componentes se retiran uno a uno, el robot de manipulación los coloca en su posición y se mueven de forma sincronizada con el robot de soldadura durante el soldeo (movimiento coordinado).
Garantizar que el sistema sepa qué debe hacer
Además de la innovadora tecnología de soldadura Fronius, los controles, la medición del Tool Center Point (TCP), la estación de limpieza de la antorcha y el aislamiento, el sistema de soldadura robotizada consta de siete módulos principales que colaboran entre sí controlados por software: un robot de manipulación, un robot de soldadura, un posicionador de giro e inclinación con unidad de gas de respaldo un almacén de palés con dos estanterías, una estación de pinzas, un sistema de cambio de antorcha y una estantería de palés dentro de la instalación.
Para garantizar que dichos módulos interactúen de forma precisa durante los ciclos de trabajo, es necesario seguir estos pasos:
En primer lugar, los palés y los componentes se crean juntos en el panel de control HMI-T21 RS. Este recibe cuatro datos importantes del soldador responsable: (1) el tipo de palé, (2) el modelo, (3) el número y (4) la posición de los componentes en el palé, por ejemplo, cuántas vigas maestras o carcasas de transductores están en qué posición de qué palé. Si se trata de un palé desplazado, la posición de los componentes se calcula a partir de las llamadas distancias de desplazamiento entre los componentes, tomando el primer componente la posición maestra. Por ejemplo, un desplazamiento puede ser de 200 mm en la coordenada y, y de +200 mm en la coordenada x. Los palés fabricados por Anton Paar constan de paneles perforados de un centímetro de grosor y funcionan como un sistema enchufable. Estos se encuentran en un almacén de palés compuesto por dos estanterías y están diseñados para albergar cada una de las diferentes piezas de trabajo, por lo que las posiciones de recogida y almacenamiento de cada uno de los componentes suelen variar en función de las propiedades del componente y de la pinza del robot de manipulación.
El controlador del robot contiene un programa de robot jerárquicamente superior para cada tipo de flujo de trabajo. En él se almacenan los programas de soldadura creados con Pathfinder. Cuando se crea un palé para el flujo de trabajo 2 (los componentes se sueldan directamente en él) en el HMI, el software del robot filtra los programas de soldadura que correspondan, de manera que el soldador de Anton Paar puede elegir entre todos aquellos programas disponibles para el flujo de trabajo 2 y asignar al palé el que sea necesario. Además, no solo es posible utilizar un único programa de soldadura, sino que también se puede crear toda la secuencia de trabajo. Por ejemplo, en una secuencia es posible crear primero un programa TIG para un palé, seguido de un programa MAG (por ejemplo, CMT). En ese caso, el sistema de soldadura robotizada ejecutaría ambos programas uno tras otro, cambiando el proceso de soldadura automáticamente. Además, los expertos de Anton Paar pueden insertar ciertos pasos especiales en el proceso HMI. Por ejemplo, el sistema conoce el paso especial ‘Girar el componente’, que puede utilizarse entre los dos procesos de soldadura (TIG y CMT) si es necesario.
Si se necesita una pinza concreta para la manipulación de los palés, como se describe en el flujo de trabajo 1, el usuario debe seleccionarla en el sistema. Como se ha mencionado anteriormente, hay un total de seis pinzas diferentes, todas ellas ubicadas en una estación de pinzas.
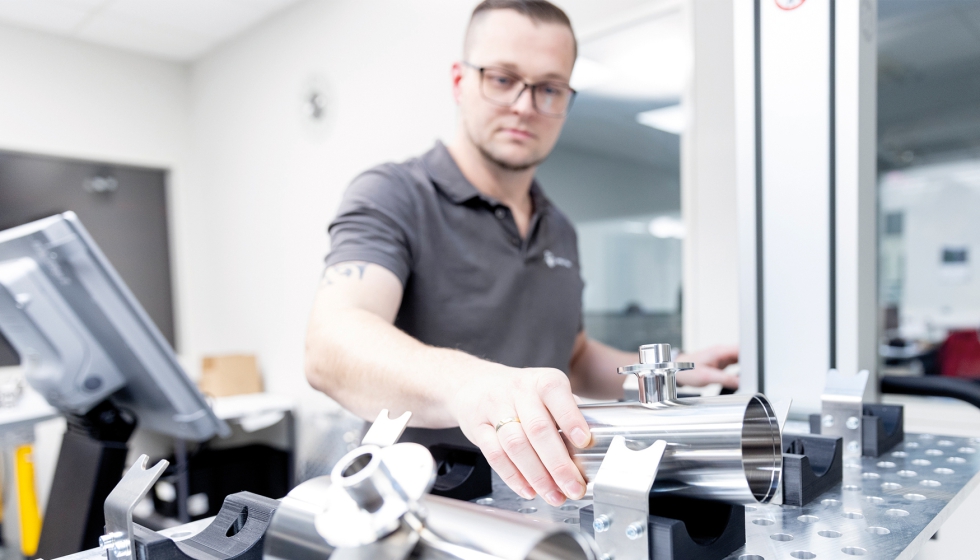
Programación de las posiciones de agarre y almacenamiento
La secuencia clásica de manipulación, recoger el palé, colocarlo en posición para soldar, transportarlo de vuelta y almacenarlo, es un programa estándar y no requiere la intervención del usuario. En lenguaje técnico, esto se denomina función “encapsulada“. Solo hay que indicar las posiciones de agarre.
Si se introduce un nuevo componente y este no es reconocido por ninguna de las estaciones de almacenamiento o recogida, el proceso automático se detiene ese punto. El soldador debe iniciar entonces un proceso de programación con el controlador del robot, el Fanuc iPendant. Para ello, recibe instrucciones paso a paso del software. De este modo, el sistema aprende la posición de agarre/almacenamiento necesaria para la estación en cuestión (por ejemplo, para el portapapeles). La posición se almacena en un registro y está disponible inmediatamente para el proceso de manipulación. De este modo, el proceso automático puede continuar en la siguiente estación. Si el componente tampoco es reconocido en la nueva estación, será necesario registrar también dicha posición. Una vez recorridas todas las estaciones según el esquema descrito anteriormente, el robot de manipulación transporta todos los componentes idénticos a través del sistema de forma totalmente automática y sin interrupciones.
Si se han planificado siete componentes para un palé, pero solo hay tres componentes en él, esto no supone ningún problema para el sistema. Se detectará un ‘agarre vacío’ y se pasará automáticamente a la siguiente posición del componente.
A medida: función ‘Programar palé’
Además de la opción estándar offset, que está especialmente indicada para los componentes con formas sencillas, Anton Paar se fijó el objetivo de colocar hasta 30 componentes metálicos en cualquier posición del palé. Fronius nos permitió cumplir este objetivo creando la función ‘Programar palé’. Esta función permite programar por separado la posición de cada componente en el palé.
“Estas dos variantes, Offset y Teach-Pallet, nos ofrecen la máxima flexibilidad en la colocación de los componentes”, explica Ingo Riemenschneider, director del Departamento de Automatización de la Producción. “No siempre tiene sentido definir las posiciones de los componentes mediante distancias offset. Hay componentes que tenemos que fijar en distintas orientaciones debido a sus formas complejas”.
Preciso como el primer día, incluso tras varios meses
Para iniciar un proceso de soldadura, los soldadores solo tienen que escanear el número de artículo de la hoja de datos del componente con su escáner manual.
“Si el sistema reconoce el número de artículo y, por tanto, el componente, conocerá también el proceso de manipulación y soldadura y lo pondrá en marcha. Todo se controla a través del HMI-T21 RS. Para cada componente se memoriza qué pinza y qué dispositivo se necesitan”, explica Riemenschneider. “Lo mismo ocurre con el tiempo de purga del argón durante el respaldo y con el tiempo de soldadura. Del mismo modo, el sistema sabe si el proceso requiere la recogida de determinados datos y qué datos son en concreto”.
Meses después, la celda de soldadura robotizada trabaja con la misma precisión que el primer día. El cordón de soldadura queda perfectamente en el mismo sitio. Esto se debe también al hecho de que Anton Paar fabrica los componentes con una precisión de micras y los trabaja de forma ejemplar.
Los componentes pueden girarse en múltiples ocasiones, incluso durante el respaldo
El posicionador basculante dispone de un paso giratorio de medios para 4 líneas de paso, 2 para aire y 2 para argón, y puede transmitir hasta 32 señales de entrada-salida (IO). Está hecho de plástico y ha sido fabricado por Anton Paar mediante impresión 3D. Si se requiere respaldo, el robot de manipulación recoge primero el dispositivo de sujeción necesario de la estantería de palés y lo fija al manipulador con ayuda de un sistema de sujeción especial. A partir de ese momento, se conectan tanto los conductos de ventilación para los cilindros neumáticos como los conductos de gas para la purga con argón. Además, el dispositivo de fijación también transmite las señales eléctricas. A continuación, el robot de manipulación coloca los componentes y el sistema activa la señal de sujeción. Después se pueden formar las piezas y, a continuación, soldarlas. El sistema está diseñado para permitir girar varias veces los componentes con un único dispositivo de fijación.
“Para nosotros es importante que todos los procesos y propiedades implantados en la planta sean abiertos en cuanto a su repetitividad. Que un proceso de giro se realice una o cien veces no debe importar desde el punto de vista del sistema. Dado que la complejidad de los componentes cambia constantemente, junto con los expertos de Fronius nos hemos esforzado mucho para que los procesos fueran lo menos restrictivos posible”, subraya Riemenschneider.
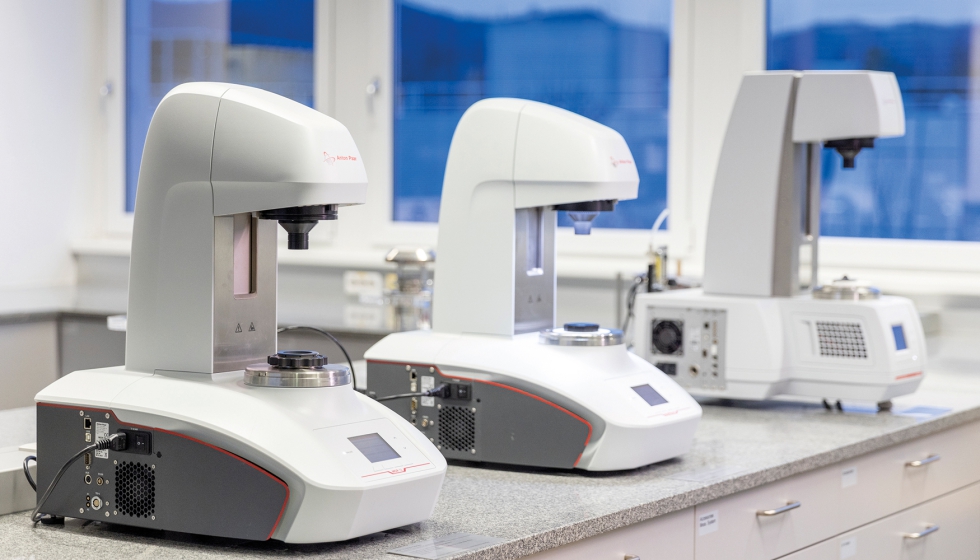
Medición de oxígeno residual por parte de Anton Paar
Durante el respaldo en el posicionador de giro e inclinación, el oxígeno residual en el componente se mide con Oxy 5100, un dispositivo de medición de fabricación propia. Este mide el oxígeno disuelto en el flujo de gas sin deriva y en tiempo real durante todo el proceso de soldadura. Normalmente, el componente se fija entre dos secciones de tubo. Por un lado, del tubo de entrada fluye el gas de respaldo y, por el otro, donde se mide el contenido residual de oxígeno, sale de nuevo como gas de escape. Esto sería contraproducente para el proceso de soldadura automatizado, ya que el robot tendría que colocar y retirar un tubo de escape para cada proceso de soldadura. Por ello, se decidió colocar el dispositivo de medición en el tubo de entrada. En cuanto el dispositivo informa de que se ha alcanzado el contenido de oxígeno residual deseado, se inicia la soldadura, para lo cual se tiene en cuenta de antemano un retraso en el tiempo de flujo del gas argón a través del componente. Este retraso es necesario para garantizar que no se supere el contenido de oxígeno residual requerido. El tiempo necesario hasta que el componente se llena por completo (el retraso) se mide de forma manual en cada uno de los componentes y se almacena en el sistema. Si vuelve el componente, el sistema de control podrá acceder a los valores y reaccionar en consecuencia.
Soldadura al más alto nivel
Para los soldadores de Anton Paar era especialmente importante poder combinar dos procesos de soldadura por componente; por ejemplo, TIG para pasadas de raíz y MAG para el relleno. Sin embargo, la elección final del proceso de soldadura depende de los cálculos técnicos y de la resistencia requerida por parte de cada uno de los componentes.
“Durante nuestras pruebas de soldadura se aclara si se utilizan procesos especiales, como CMT (Cold Metal Transfer), PMC (Pulse Multi Control) o LSC (Low Spatter Control). El proceso que elijamos dependerá del grosor de la pared del componente, del tipo de cordón de soldadura, por ejemplo, en I o de garganta, así como de la profundidad de penetración de la soldadura y de los patrones de rectificado necesarios”, explica Moik. “Necesitamos unas seis o siete pruebas antes de pasar a la producción en serie. Si el aporte térmico fuera demasiado elevado para las propiedades del material, la mejor opción es, sin duda, el proceso de soldadura en frío CMT. Si queremos aumentar la productividad incrementando la velocidad de soldadura, nos planteamos elegir el proceso PMC. Si queremos soldar con pocas proyecciones, una opción podría ser el LSC. Principalmente porque nos permite evitar costosos retrabajos”.
Los datos de soldadura se registran en el HMI. Si el soldador detecta algún defecto durante la comprobación visual, puede comprobar el registro de datos de soldadura para ver si se ha producido alguna desviación de los valores límite. Cada componente se somete a una comprobación visual y uno de cada diez componentes se somete a una inspección por líquidos penetrantes. Este procedimiento permite detectar grietas, poros y defectos de unión de hasta 1 µm. Cada cierto tiempo se toman micrografías de las piezas metálicas sometidas a inspección por líquidos penetrantes al final del ciclo de prueba.
Los innovadores procesos Fronius, el concepto de sistema inteligente y flexible al mismo tiempo y el potencial de desarrollo sostenible del sistema de soldadura robotizado garantizan a Anton Paar soldaduras perfectas para sus aparatos de medición de alta precisión durante años. Al mismo tiempo, los soldadores se benefician del aumento de la seguridad y la protección de su salud, ya que están protegidos del arco voltaico y sus humos gracias al aislamiento y la aspiración.