El coste de no usar tecnología digital en el diseño de voladuras en banco
Javier Muñoz García. Ingeniero de Minas. Director de Formación Externa – EPC Groupe
16/10/2020De la goma pura a la era digital
La extracción de piedra y minerales que demanda la sociedad para su actividad económica depende de manera fundamental de las operaciones de perforación y voladura; el primer eslabón en la cadena de producción mineral. La dinamita y gelatinas explosivas inventadas por Alfred Nobel en la segunda mitad del siglo XIX, suponen un punto de inflexión crítico en la capacidad que hasta entonces tenía la especie humana para extraer las materias minerales necesarias para su desarrollo; ya que permiten a los ingenieros de la época proyectar movimientos de material mucho mayores y más eficientes. Los avances posteriores tanto en tecnología de explosivos y sistemas de iniciación como en la capacidad y tamaño de equipos de perforación y otros (carga, transporte, trituración…) nos otorgan desde hace décadas la capacidad de llevar a cabo obras descomunales en periodos de tiempo reducidos.
Desde los primeros años de este siglo, con la llegada de la era digital, el desarrollo de la técnica no ha estado tan centrado en el aumento de capacidades de carga y de potencias mecánicas de trabajo; sino que ha estado más enfocado en la optimización digital de la maquinaria y en el control de sus resultados mediante un uso exhaustivo de la tecnología de última generación. De esta manera se han desarrollado equipos de perforación que se posicionan en las coordenadas exactas mediante navegación por satélite y son capaces, además, de reportar parámetros de la roca perforada en tiempo real con el sistema MWD; equipos de transporte operados de forma remota, flotas de carga y transporte gestionados por satélite, sistemas de control cada vez más digitalizados en todo el proceso de tratamiento, etc. En el campo de la perforación y voladura, desde la aparición del detonador electrónico a finales del siglo XX (un invento digital), no ha habido ninguna otra innovación tecnológica merecedora de mención especial. Sin embargo, la tecnología digital, aplicada al diseño de voladuras y al control de carga en las MEMU, sí ha permitido avances significativos en la optimización de resultados.
Diseño tradicional de voladuras en banco
Ya hemos consumido casi 20 años del siglo XXI y aún hoy lo más frecuente es que los diseños de perforación y voladura en banco se lleven a cabo de una forma muy poco tecnificada; haciendo uso de métodos rudimentarios de supervisión de frentes y de marcado de emboquilles. De esta manera, la altura de los frentes, que casi nunca es la misma en dos barrenos consecutivos, suele estimarse 'a ojo' y, si se mide, se hace de manera muy básica, con cinta métrica lanzada desde la parte alta del banco o con una pértiga o caña que, además, sirve para dar una estimación muy basta de la piedra en el pie de banco. El marcado de la malla de barrenos (piedra y espaciamiento) se hace con cinta métrica, lo cual no es una mala práctica de por sí, pero su posición relativa al frente de voladura no puede ser determinada con la precisión suficiente. Esto, además, se complica cuando los frentes no son rectos o la forma de la superficie a volar no tiene una geometría simple. En resumen, estos métodos 'artesanales', no son acordes con la época en la que vivimos desde hace más de 20 años y no son capaces de proporcionar diseños de calidad en la gran mayoría de los casos.
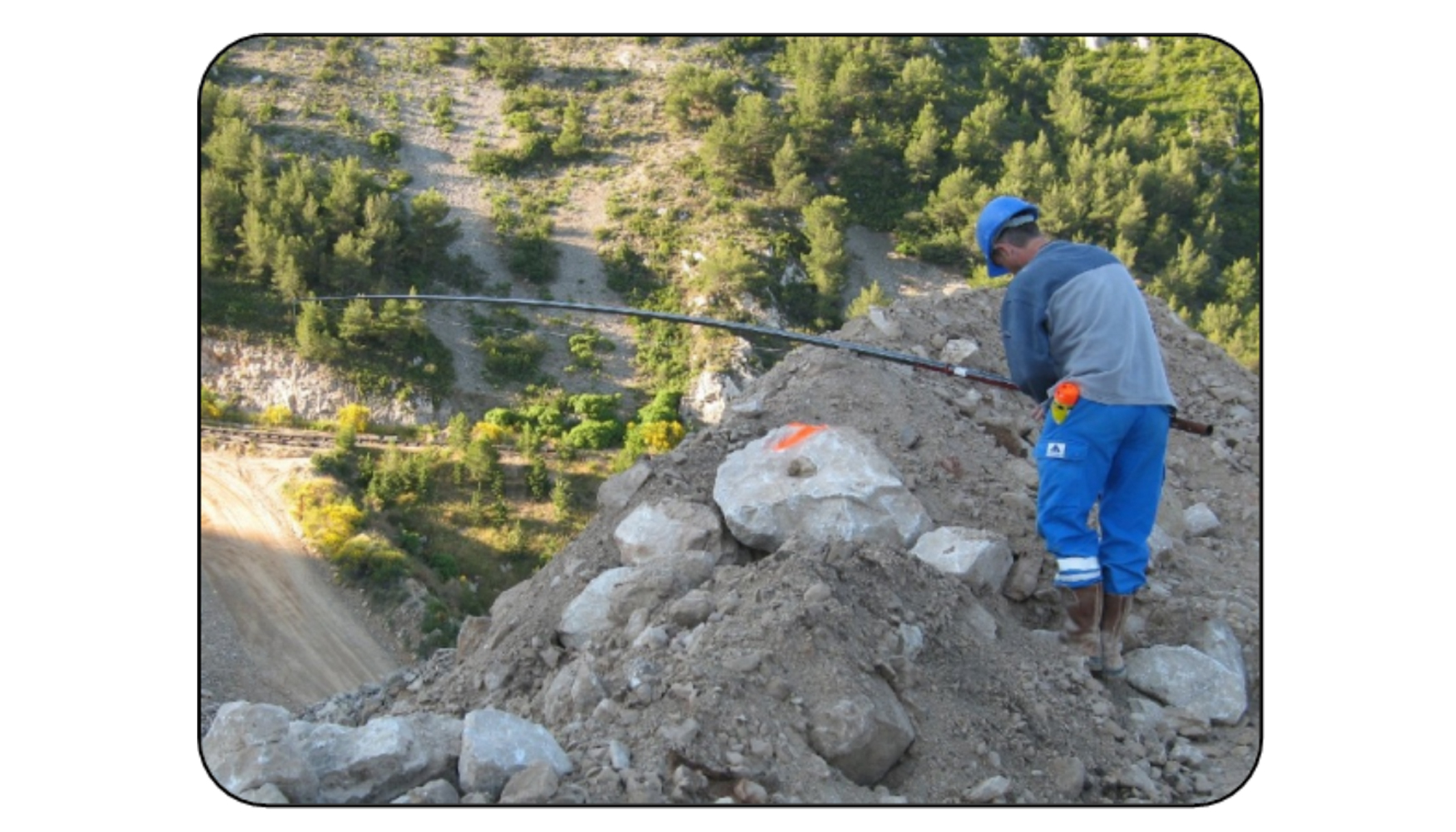
El diseño de cualquier voladura debe garantizar los siguientes objetivos por este orden:
- Seguridad. Durante su preparación, carga, disparo y facilitar, además, unas condiciones de trabajo posteriores seguras: frentes estables, ausencia de barrenos fallidos, evitar zapateras y taqueos posteriores, etc.
- Efectos ambientales tolerables. Generación reducida de vibraciones y ruido.
- Resultados óptimos de fragmentación y empuje conforme a los equipos de carga disponibles en la explotación y al uso posterior del material a volar.
El método 'artesanal' de marcado de la perforación y el diseño convencional de cargas por barreno, haciendo uso nulo de la tecnología actual, simplemente no puede asegurar estos tres objetivos de manera simultánea. Por ejemplo, para asegurar diseños que no produzcan peligrosas proyecciones se tiende a sobredimensionar la piedra de diseño, produciendo un arranque inadecuado en el pie del banco y un exceso de vibraciones. De manera inversa, la seguridad se ve seriamente comprometida al tratar de ajustar 'a ojo' la piedra de diseño a su valor óptimo.
Este desconocimiento de la irregularidad geométrica inherente a los frentes de voladura en toda su longitud es la principal fuente de los problemas que se producen al disparar una voladura; fundamentalmente: proyecciones de piedras, vibraciones, onda aérea, fragmentación y empuje inadecuados, repiés, exceso de sobreperforación, frentes inestables... y es materialmente imposible controlar a simple vista todas las irregularidades geométricas de un frente de voladura.
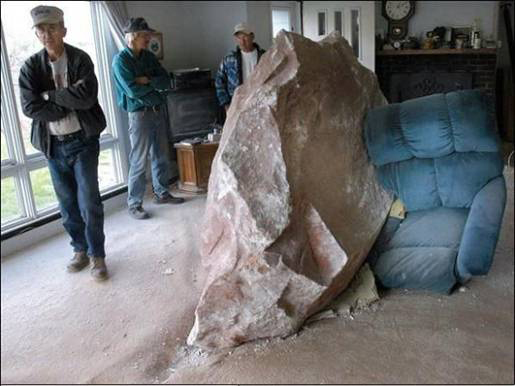
Desarrollo del estado de la técnica en medición de frentes de voladura y barrenos
Desde la segunda mitad de la década de los años 1990 existen sistemas electrónicos que permiten conocer de una manera fiable la geometría del frente de voladura y su altura. En un principio se manejaban sistemas de medición láser 2D que necesitaban posicionarse con cierta pericia delante de cada barreno para obtener los perfiles; la precisión no era muy buena, pero ciertamente mejor que el artesanal marcado 'a ojo' y suficiente para marcar los emboquilles a una distancia segura y buscando una piedra adecuada.
Estos sistemas evolucionaron, a partir de los primeros años de la década de 2000, a los llamados láser 3D que obtienen un modelo tridimensional del frente de voladura a partir de una nube de puntos más o menos cerrada del mismo. Este método permite obtener unos perfiles de diseño mucho más precisos y, además, se obtienen desde una sola posición, sin necesidad de tomar manualmente un perfil por barreno. Los equipos de medición, similares en forma a un teodolito de topografía, son específicos para este fin y necesitan de un mantenimiento regular para asegurar la calidad de las mediciones.
Desde hace algo más de 10 años, existen sistemas que obtienen el modelo tridimensional del frente a partir de varias fotografías digitales del mismo que se solapan parcialmente; es lo que se conoce como fotogrametría. Esta metodología, muy precisa, no requiere de equipos específicos de medida; tan solo de una cámara digital de cierta calidad de resolución. Con la reciente aparición de drones equipados con cámaras de gran calidad a un precio muy asequible, la fotogrametría ha pasado a desplazar por completo a los sistemas de medición láser 3D.
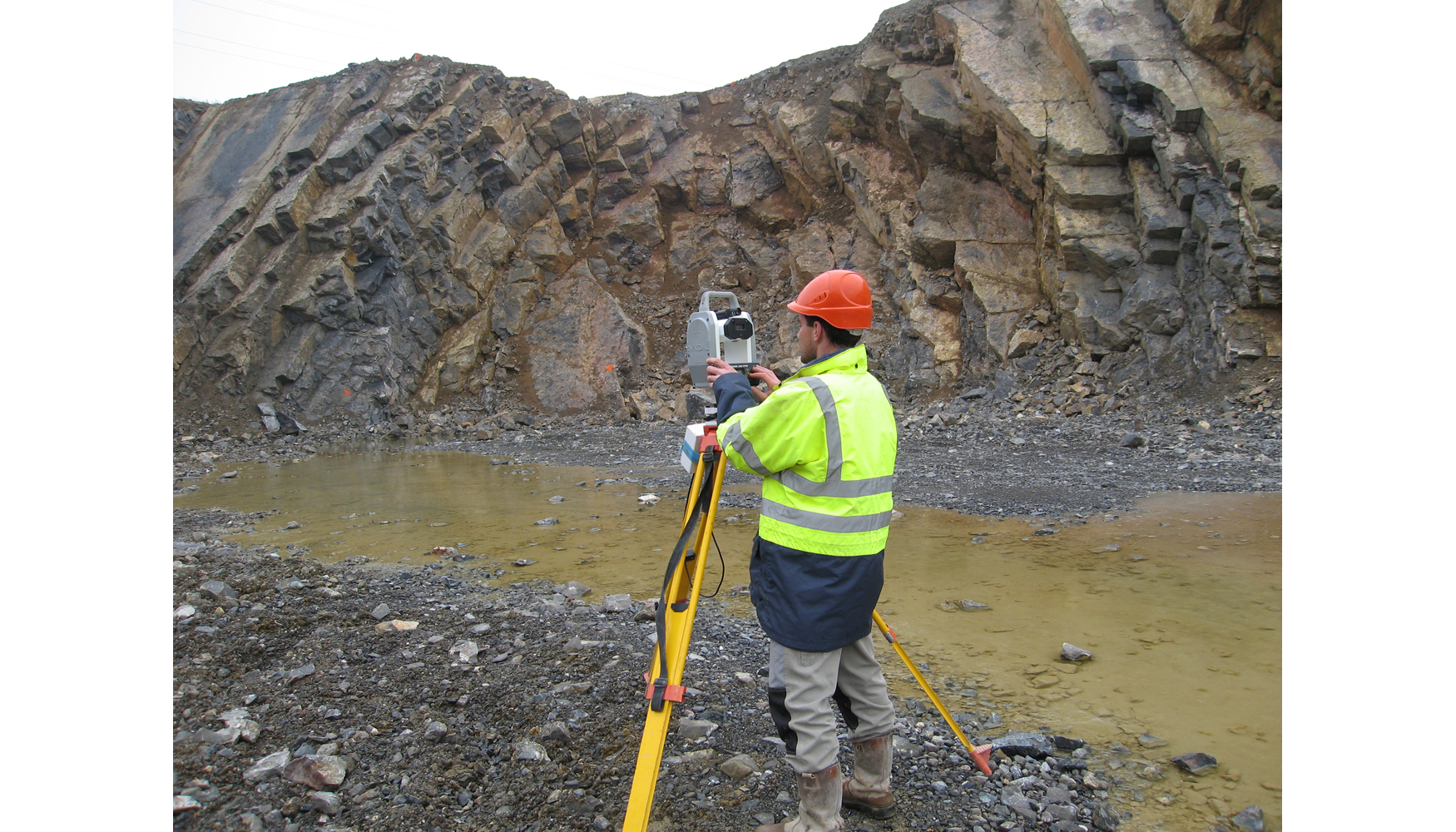
Los drones permiten hacer fotos del frente desde cualquier ángulo y altura muy fácilmente y producen modelos en 3D de gran calidad. El elemento más caro de este sistema es el software que trata la información fotográfica y la convierte en un modelo tridimensional. En cualquier caso, la fotogrametría mediante drones resulta más económica, fiable, segura y sencilla de manejar que el láser 3D. Los drones se pueden usar además para obtener filmaciones de gran calidad de la voladura desde posiciones privilegiadas; así como para tomar fotos y vídeos de los resultados de la misma. Por este motivo son una herramienta muy valiosa en el diseño y control de resultados de voladuras en banco.
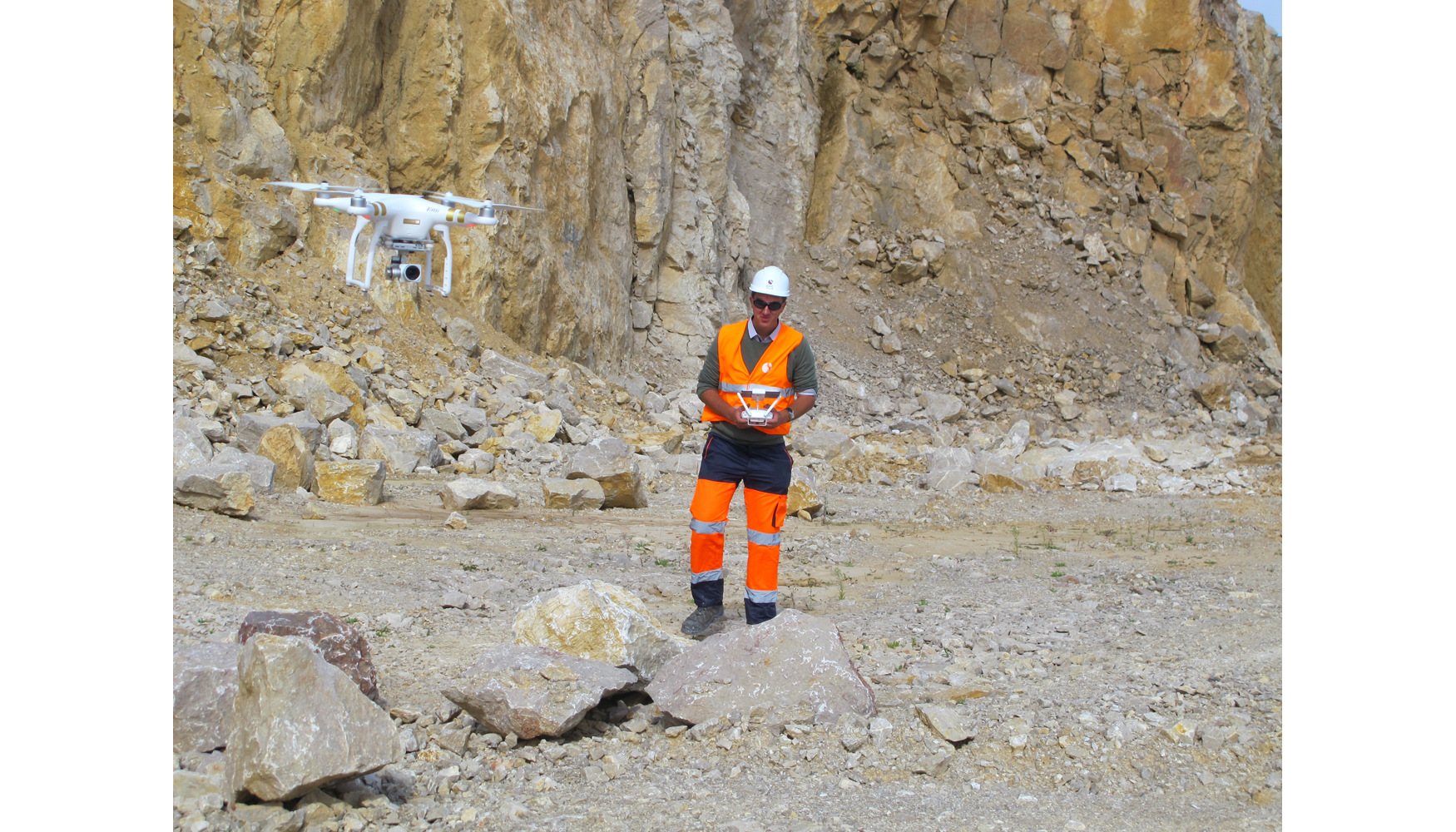
Las herramientas de medición de barrenos son las sondas electrónicas, disponibles también desde hace más de 20 años. La sonda se hace descender al fondo del barreno y unos inclinómetros en su interior proporcionan la trayectoria real del barreno, metro a metro.
La combinación de ambas informaciones: modelo tridimensional del frente y trayectoria real de barrenos, se lleva a cabo en el software Expertir y permite generar diseños de voladuras en banco que proporcionan la seguridad necesaria y un reparto óptimo y uniforme de la energía del explosivo en el volumen de roca a volar.
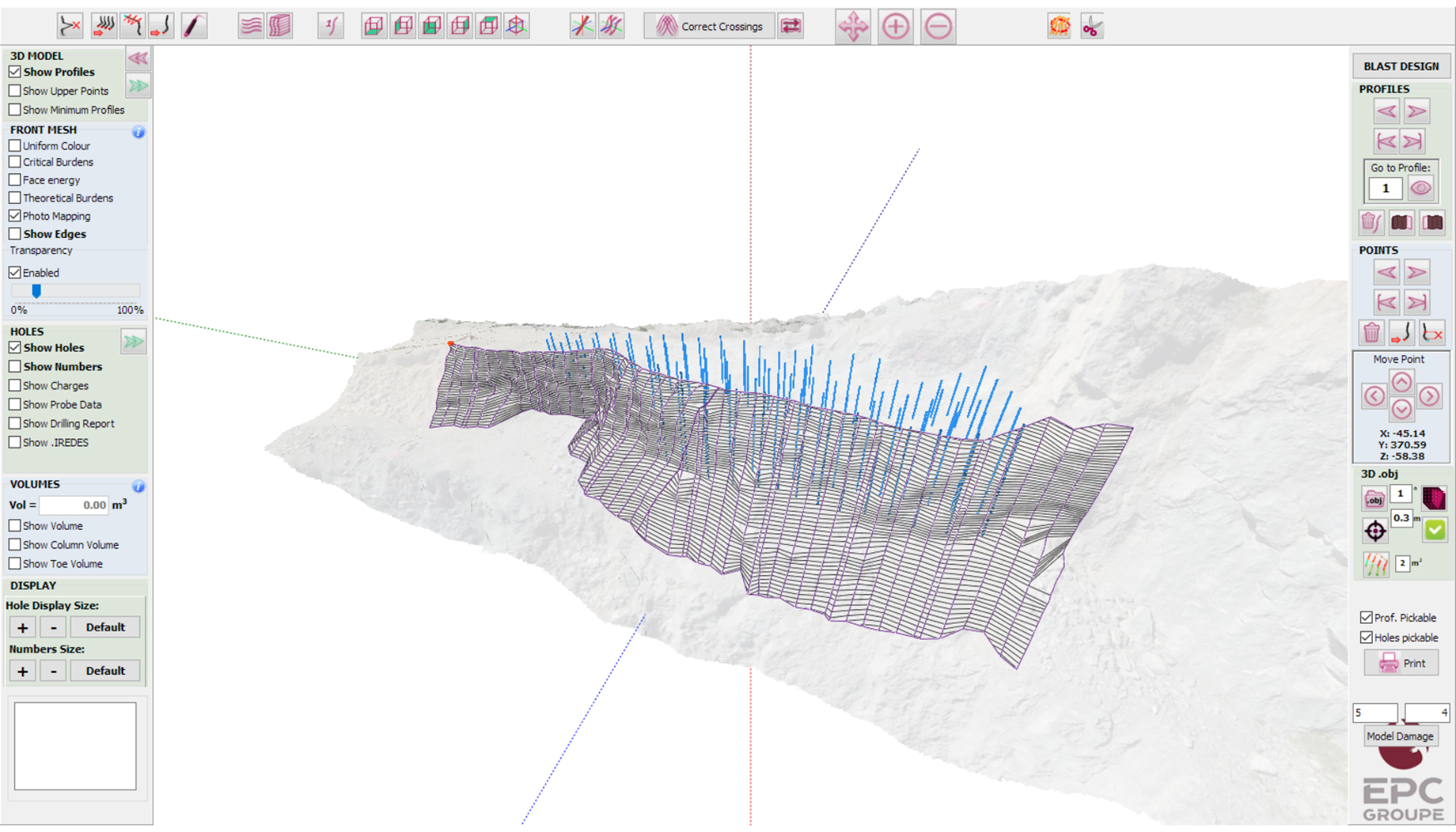
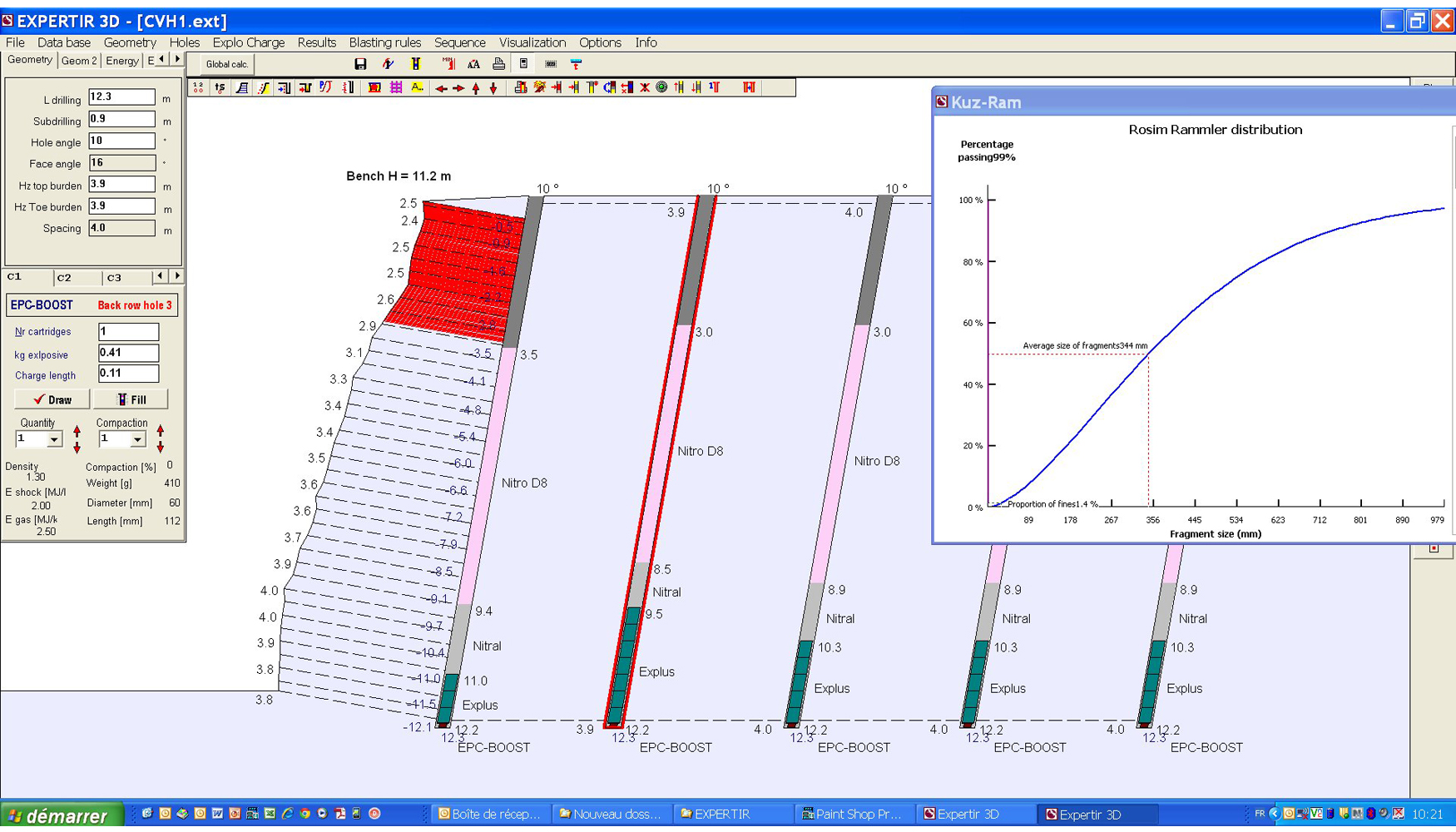
El coste de usar o no usar tecnología digital
El coste del uso de esta tecnología es muy sencillo de calcular; basta con pedir una oferta por la prestación externa del servicio o, si se va a llevar a cabo en la casa, presupuestar la compra de los equipos, las horas de formación técnica y de ingeniero para cada voladura; esta partida económica se divide entre las toneladas producidas y se obtiene el resultado.
Tradicionalmente, lo que no se ha podido calcular de manera tan sencilla es el coste de no utilizar esta tecnología. Por una parte, en este cálculo entran conceptos a priori difíciles de cuantificar económicamente como la seguridad o el control de efectos ambientales de la voladura; además, la estimación económica de los beneficios a obtener como consecuencia de una fragmentación y arranque óptimos se centran en una posible reducción de costes aguas abajo de la voladura: fragmentación secundaria, carga, transporte, energía en machacadora, paradas en la planta, producción horaria; esto se conoce como concepto Mine to Mill. Lo más normal es que, tras cierto debate y, ante la imposibilidad de estimar con precisión una cifra concreta de beneficio final, la decisión suele ser siempre la misma: mientras no haya problemas evidentes de seguridad no se implementa nada.
Los beneficios del concepto Mine to Mill son conocidos y se han demostrado en diferentes casos reales durante las últimas dos décadas; siendo objeto de conferencias y publicaciones técnicas extensas, tanto en minería como en cantera. Si bien, como se ha mencionado antes, los beneficios finales para cada caso concreto son muy difíciles de estimar a priori sobre el papel y se pueden determinar de manera precisa únicamente con la práctica: poniendo en marcha un proyecto de mejora continua de resultados.
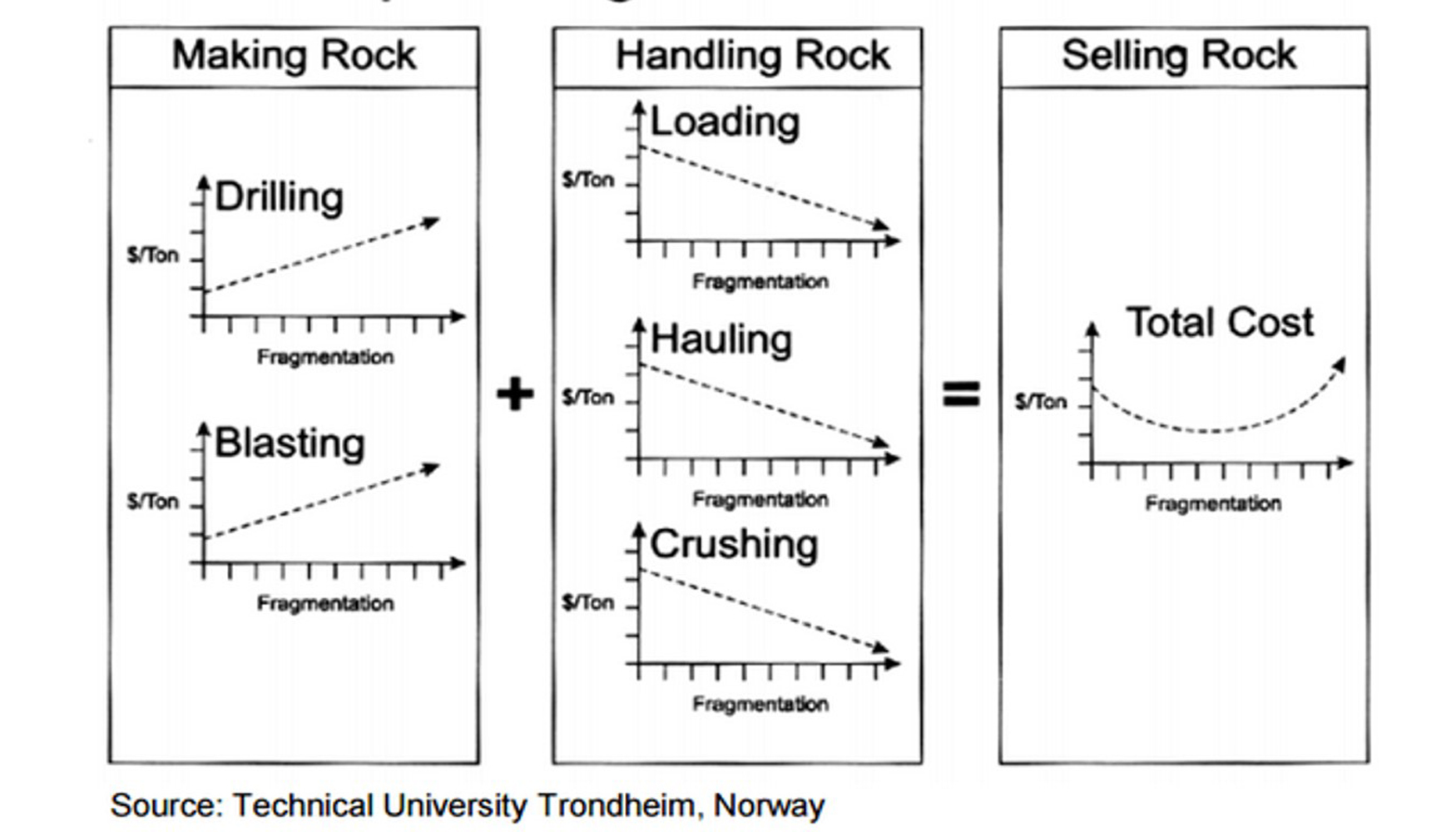
¿Existen beneficios inmediatos en el uso de la tecnología digital?
Pocas veces se cuestiona lo más evidente: ¿obtenemos algún beneficio cuantificable de manera inmediata al implementar la tecnología en el diseño de voladuras?. Recordemos ahora la cita de William Thomson Kelvin: “Lo que no se define no se puede medir. Lo que no se mide, no se puede mejorar. Lo que no se mejora, se degrada siempre.”.
Lo cierto es que en el diseño tradicional de voladuras en banco no se mide gran cosa, aparte del diámetro y la malla de perforación. Se usa como modelo de diseño un paralelepípedo perfecto definido por la piedra, el espaciamiento y la altura (estimada) del banco inclinado conforme al ángulo de la perforación de un barreno rectilíneo perfecto tirado con regla.
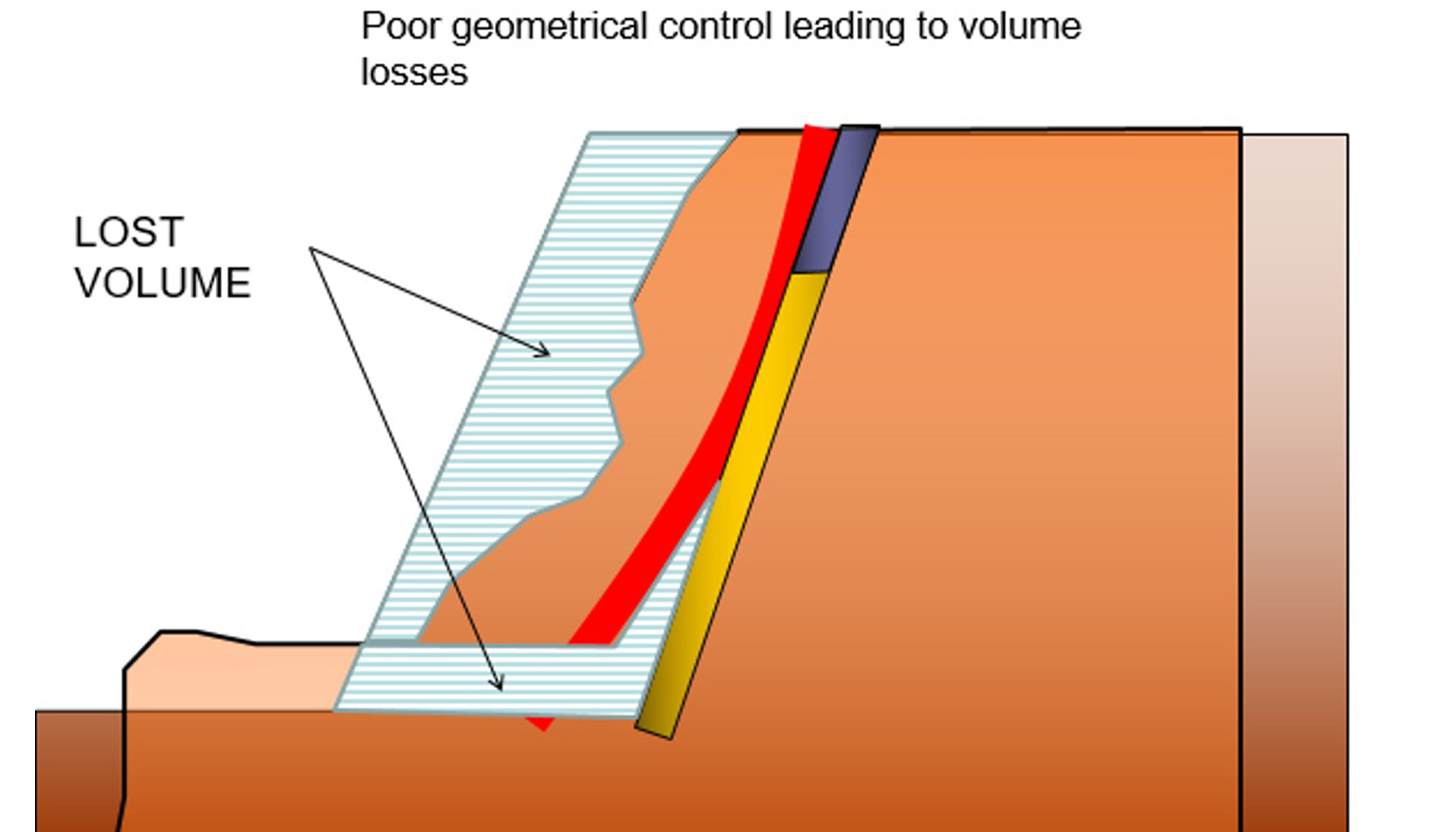
Este modelo ideal sirve de base de cálculo para las cargas por barreno, la sobreperforación, la longitud de retacado y para la obtención de la producción en toneladas de cada voladura. Se obtiene a partir de él muy fácilmente el consumo específico (en kg de explosivo por metro cúbico) y la perforación específica (en metros lineales por metro cúbico). Ese paralelepípedo es, en resumen, la base de cálculo de los costes directos en perforación y voladura. El problema es que este modelo ideal suele parecerse muy poco a la realidad debido a las irregularidades del frente y conduce a errores importantes.
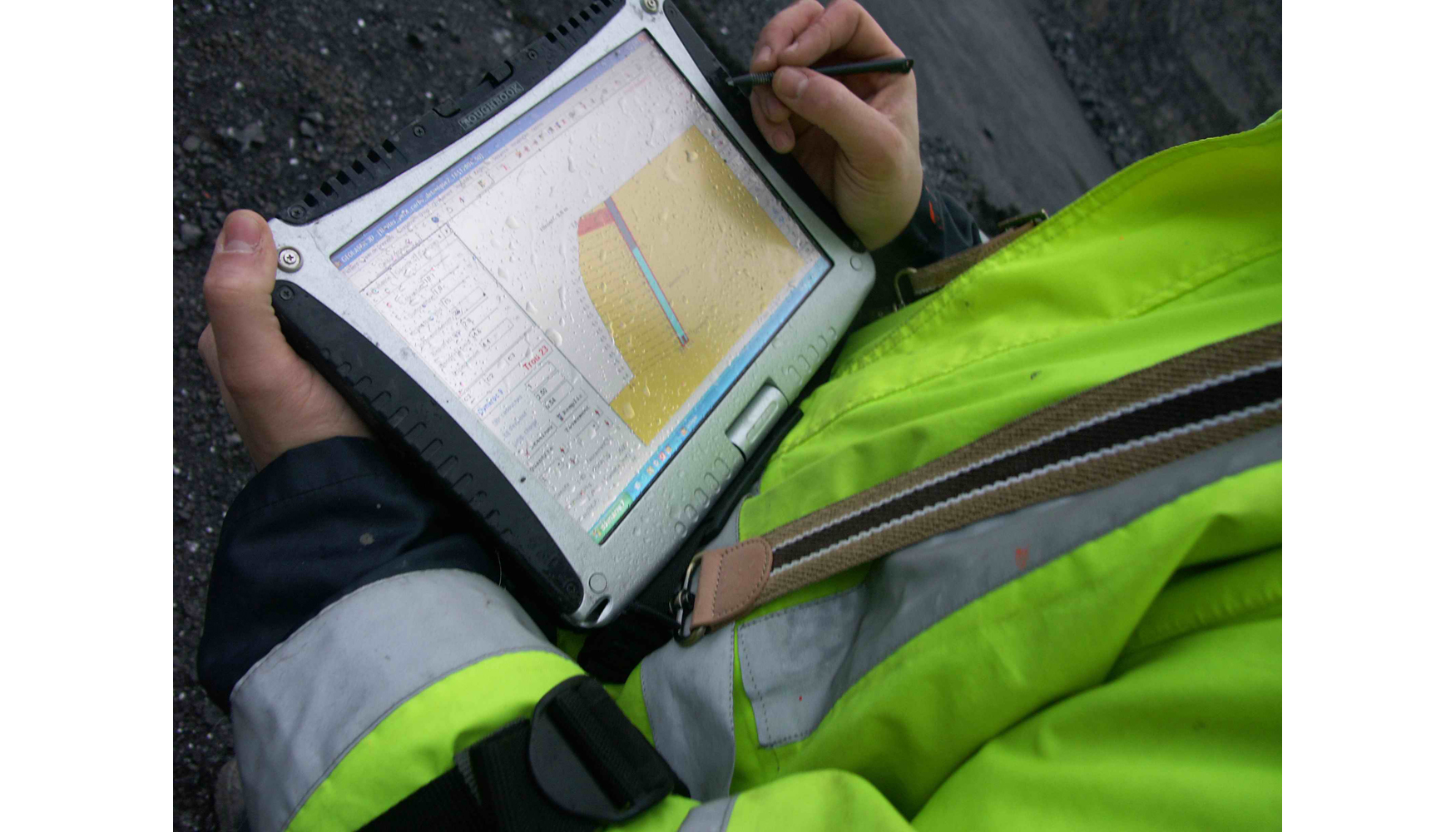
Beneficios reales
El Grupo EPC realizó recientemente una auditoría en un grupo de 8 canteras con el objeto de estudiar el estado general de los frentes y de la perforación; además de identificar posibles mejoras técnicas a partir de diseños más eficientes que pretenden un reparto uniforme de la energía del explosivo por barreno. El objetivo era identificar los errores en origen que causan los problemas tradicionales en voladura: repiés, fragmentación poco uniforme, horas excesivas de fragmentación secundaria, etc.
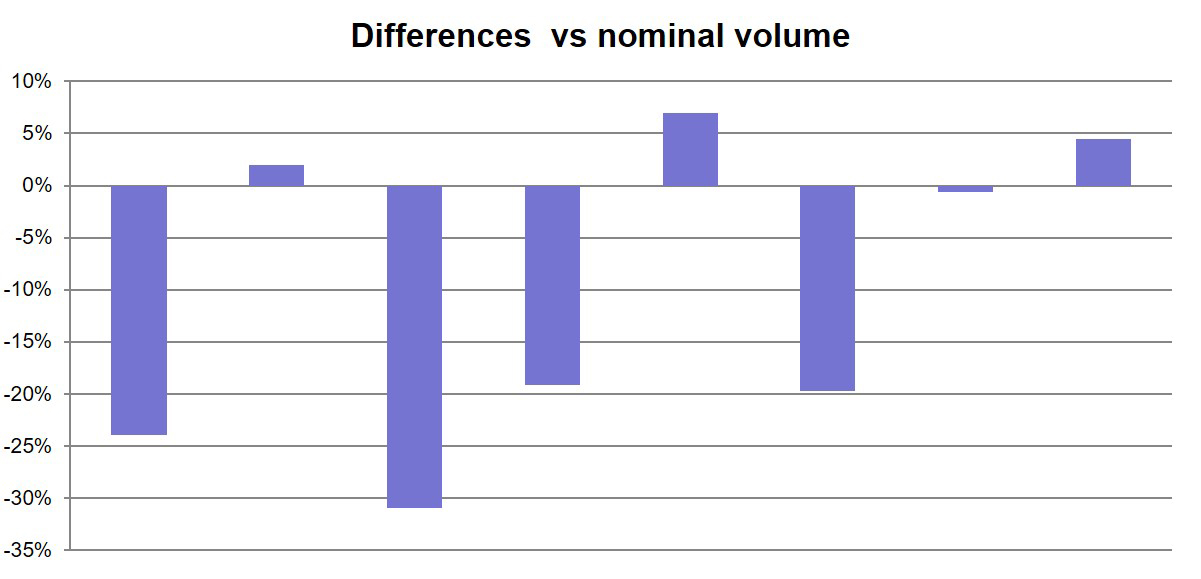
Tras la campaña inicial de medición de los frentes en las voladuras, la primera y más demoledora conclusión que se obtuvo fue que, de media en el conjunto de las 8 canteras, el error geométrico en el diseño conducía a sobrestimar el volumen a volar en más de un 20%; es decir, que los recursos materiales y humanos empleados en perforación y voladura producían en realidad menos de un 80% de las toneladas de roca a volar sobre el papel. Esto, con los costes normales de perforación y voladura, se puede estimar en un sobrecoste de unos 50.000€ por cada millón de toneladas. Es decir, la introducción de la tecnología digital en la medición de frentes y barrenos va a corregir esos posibles errores de diseño de manera inmediata y supone, por tanto, el ahorro automático de ese exceso de costes consecuencia de una medición geométrica deficiente.
Una parte importante de esta desviación en los volúmenes reales tenía como origen una estimación inadecuada de la altura de banco que llevaba a un exceso medio de la sobreperforación de 2m por barreno. Este problema de sobreperforación excesiva es muy común en las explotaciones donde no se mide el frente con tecnología digital; produce un piso triturado que dificulta la futura perforación del banco inferior, exceso de vibraciones y el evidente malgasto de explosivo (generalmente encartuchado de mayor precio que en la columna) y perforación inútil en el fondo del barreno. El resto de la desviación provenía de las diferencias geométricas normales entre un frente de voladura real y el modelo rectilíneo ideal.
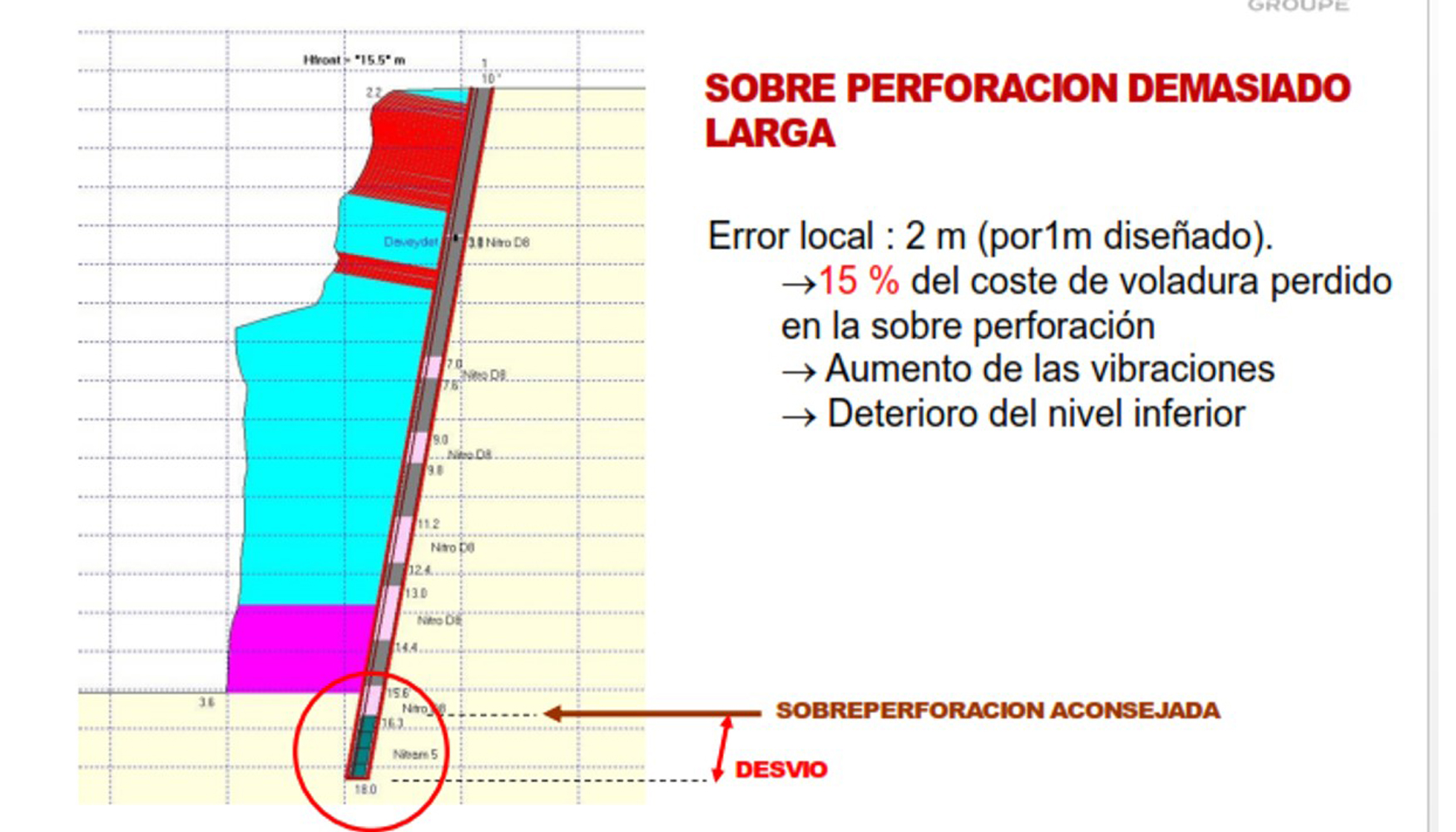
Además de esta diferencia de volúmenes, en todas las canteras se identificó una distribución muy heterogénea de la energía explosiva dentro de las voladuras, lo cual conducía a los clásicos problemas descritos anteriormente: fragmentación no uniforme, repiés, etc. Es decir, pese a que de manera general se usaba mucha más energía explosiva de la necesaria para el volumen real de roca a volar, ésta no se encontraba bien repartida y conducía a problemas reales de fragmentación y arranque deficientes. Este patrón es común en casi todas las explotaciones que no hacen uso de la tecnología digital en los diseños de voladuras en banco.
Como se puede apreciar en la figura, en 3 de las 8 canteras los volúmenes reales volados eran ligeramente superiores a los proyectados; lo cual, a priori puede parecer una fuente de ahorro. Esto es, sin embargo, una falsa economía de recursos tal y como se ha justificado antes. Este ahorro inicial en perforación y voladura se traduce siempre en una fragmentación y un arranque pobres; lo cual genera costes aguas abajo mucho mayores en saneo de frentes, fragmentación secundaria, transporte, paradas y consumos en machacadora, etc.
Tras hacer un seguimiento en la mayor de las 8 canteras, con una producción anual de 2,5 Mt; desde de la introducción de la tecnología digital 3D en el diseño de voladuras, la perforación se consiguió reducir en un 27% para mantener el mismo volumen de producción y el número de horas en fragmentación secundaria ha pasado a ser prácticamente nulo.
Conclusión
El uso de esta tecnología es desde hace tiempo obligatorio en varios países por ser la única forma eficaz de controlar el riesgo de producir peligrosas proyecciones de roca en las voladuras en banco. Sin entrar a valorar en detalle los beneficios evidentes en seguridad o reducción de vibraciones y las posibles mejoras en los costes globales de producción (Mine to Mill); el conocimiento exacto de la geometría del frente de voladura y de la perforación nos lleva de manera inmediata a poder medir de forma precisa el volumen de material en cada voladura y a proyectar con exactitud la posición de los barrenos, los metros de perforación y la cantidad y tipo de explosivo que se requieren para cada voladura. Esto tiene de por sí un efecto positivo inmediato en los costes directos en perforación y voladura; que se traducen en ahorros de caja diarios. Una simple y rápida auditoría técnica de la geometría de los frentes y de la perforación en su explotación es suficiente para saber cómo de cerca está de ese objetivo.