Validación de canales fríos con simulación
Katharina Aschhoff, directora de Marketing, Sigma Engineering GmbH y Matthias Tanzer, jefe de Ingeniería de Proyectos, Aplicaciones y Automatización, Maplan GmbH
21/02/2023Desarrollar internamente la tecnología de canal frío es costoso y a menudo no merece la pena, sobre todo para pequeñas cantidades y moldes individuales. Por eso es bueno que existan en el mercado sistemas normalizados para diversas aplicaciones individuales. Un proveedor muy conocido en este ámbito es la empresa austriaca Maplan, que ofrece tecnología de canal frío especialmente adaptada, además de sus propios sistemas de moldeo por inyección.
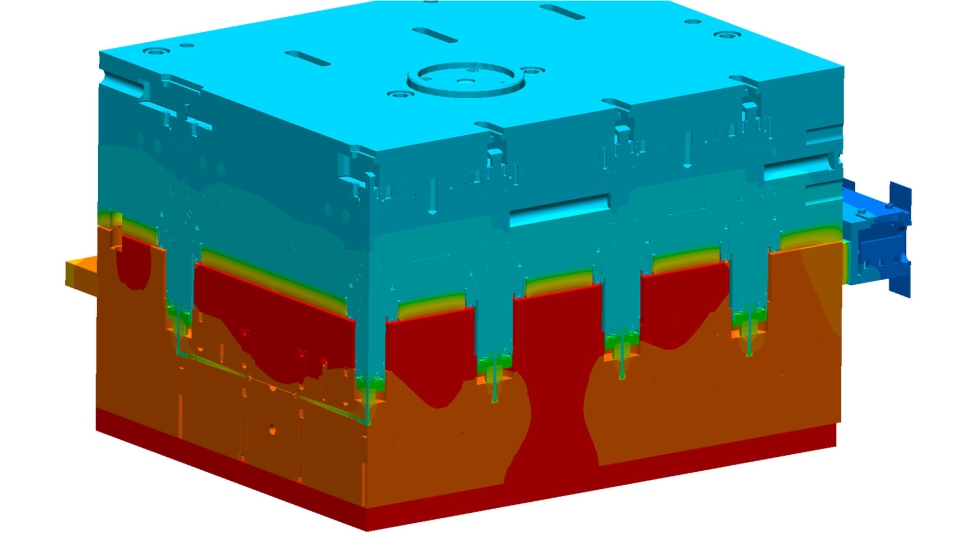
Para la validación de canales fríos, la simulación de toda la herramienta es relevante, ya que sólo se generan resultados realistas incluyendo todas las influencias sobre el canal frío.
Este artículo muestra cómo la moderna simulación de procesos con Sigmasoft Virtual Molding ayuda en el desarrollo, optimización y validación de estos complejos sistemas.
En función del uso y la aplicación previstos, Maplan ofrece distintos diseños de canal frío:
- MAP.crb slim: Sistema de canal frío muy delgado y fácil de reequipar sin placa calefactora separada.
- MAP.crb sólido o sólido+: El clásico canal frío perforado con colector en ángulo recto especial para altas presiones de inyección. La MAP.crb solid+ también se suministra con caudal volumétrico ajustable mecánicamente.
- MAP.crb split: El canal frío separable cuyo diseño tiene transiciones curvas y permite una limpieza eficaz.
- MAP.crb pinpoint: Compuerta lo más cerca posible del componente - con tecnología de compuerta de válvula hidráulica.
Para una mejor comprensión, las variantes solid+ y split deben ser investigadas y comparadas mediante simulación de procesos en el caso de aplicación concreta incluyendo el molde calentado. El molde de prueba utilizado aquí del Centro Técnico Maplan tiene 8 cavidades con un peso total de disparo de aprox. 288 g. El molde se fabricó en EPDM con 60 Shore A. El molde se calentó. Un EPDM con 60 Shore A sirvió de base para la prueba.
El molde no muestra diferencias de rendimiento térmico cuando se ensambla con ambas variantes de canal frío. La imagen de portada muestra el molde calentado por la placa de sujeción inferior al final de la fase de calentamiento. Esta vista se corta a través de las boquillas del canal frío. La separación térmica entre la platina de calentamiento del canal frío y el bloque de canal frío funciona de forma excelente y puede verse bien aquí.
Diferencias en detalle
A continuación, se comparan los dos bloques de canal frío entre sí y se muestran las diferencias en relación con el diseño respectivo. El canal frío MAP.crb solid+ tiene orificios rectos con un colector en ángulo recto y es adecuado para altas presiones de inyección. Por otro lado, el colector frío dividido MAP.crb tiene un diseño separable que permite acceder al colector frío. Además de facilitar la limpieza, este acceso también permite transiciones curvas de flujo optimizado.
Con la simulación, es fácil observar con más detalle las boquillas del canal frío. De especial importancia es el perfil de temperatura en el proceso. Se utilizan boquillas diferentes para los dos canales fríos. La velocidad del flujo en la variante dividida es mayor (derecha) que en el canal sólido+frío (izquierda) porque los canales tienen diámetros diferentes, véase la figura 1.
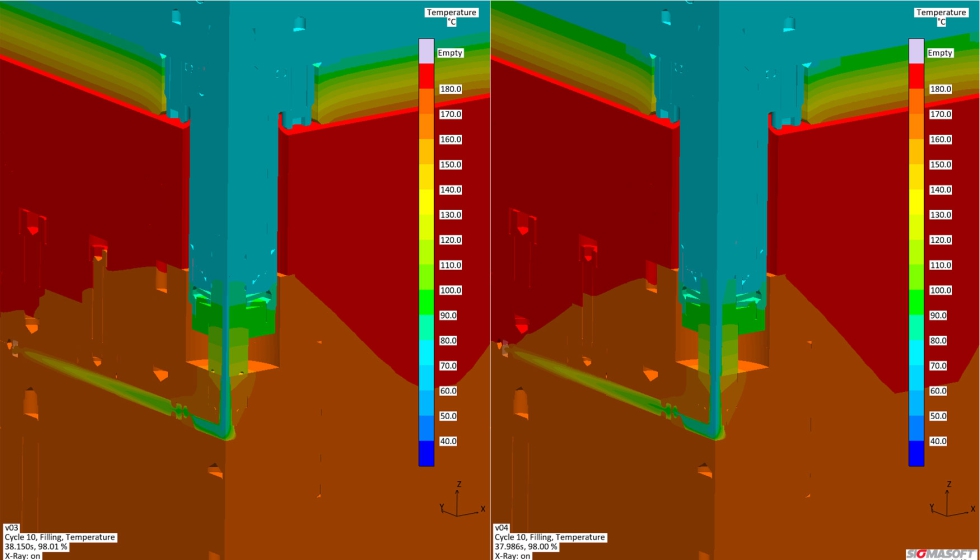
Figura 1: Sección de las boquillas de canal frío en el molde en comparación detallada (izquierda: Sólido+ y derecha: Dividido).
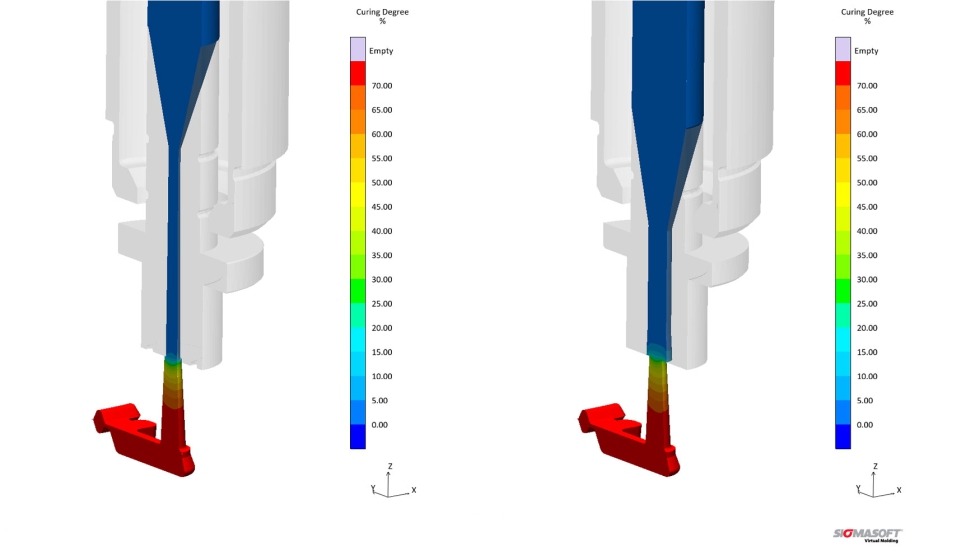
Al analizar los canales fríos, siempre es importante comprobar que no haya posibles perturbaciones del flujo ni ángulos muertos. Con Sigmasoft Virtual Molding, es posible hacerse una idea de los canales de flujo por los que se ha pasado y esto revela posibles ubicaciones en las que se puede estar acumulando material más antiguo. La figura 3 muestra una comparación de la edad del material de ambas disposiciones de canal frío, es decir, el tiempo que ha transcurrido desde que el material sale de la boquilla de la máquina. En comparación, los agujeros rectos del sólido+ pueden verse muy claramente en contraste con las transiciones curvas de la división. También es visible que no ofrecen zonas para posibles ángulos muertos (véase la figura 3).
Un método de representación aún mejor es el uso de trazadores de flujo en la simulación (no mostrados aquí). Esto permite representar con precisión el flujo en el vídeo siguiendo un gran número de partículas individuales de material.
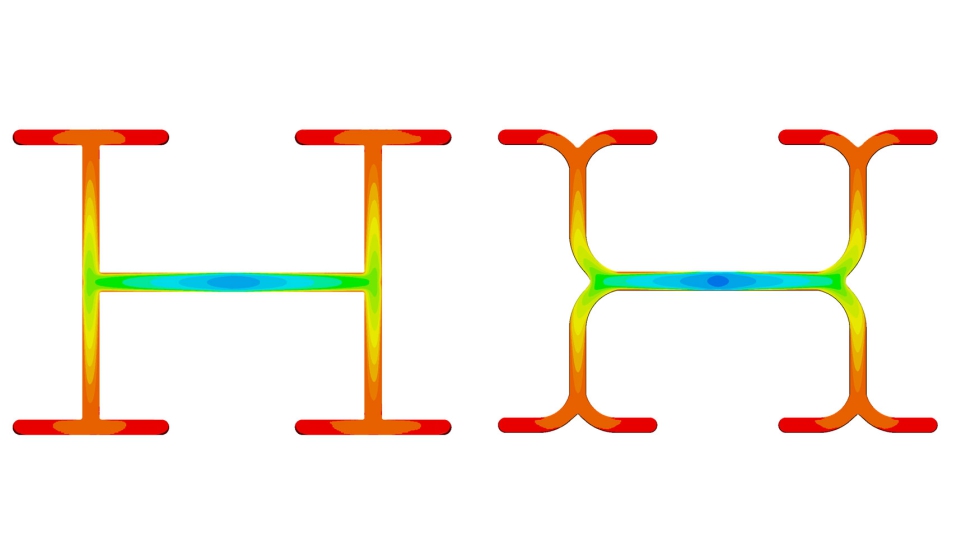
En esta comparación, las escalas se normalizaron al bebedero de la cavidad para una mejor comparabilidad de las relaciones de presión. El MAP.crb solid+ tiene una mayor pérdida de presión en el colector en comparación con los canales de flujo optimizado del MAP.crb split. El diámetro considerablemente menor en la punta de la tobera (visible en la figura 2) aumenta aún más la presión necesaria. En general, el diseño solid+ da lugar a una mayor necesidad de presión, lo que no supone un verdadero problema para las unidades típicas de este tamaño de máquina. Esto se debe en gran medida a la posibilidad del caudal volumétrico ajustable mecánicamente.
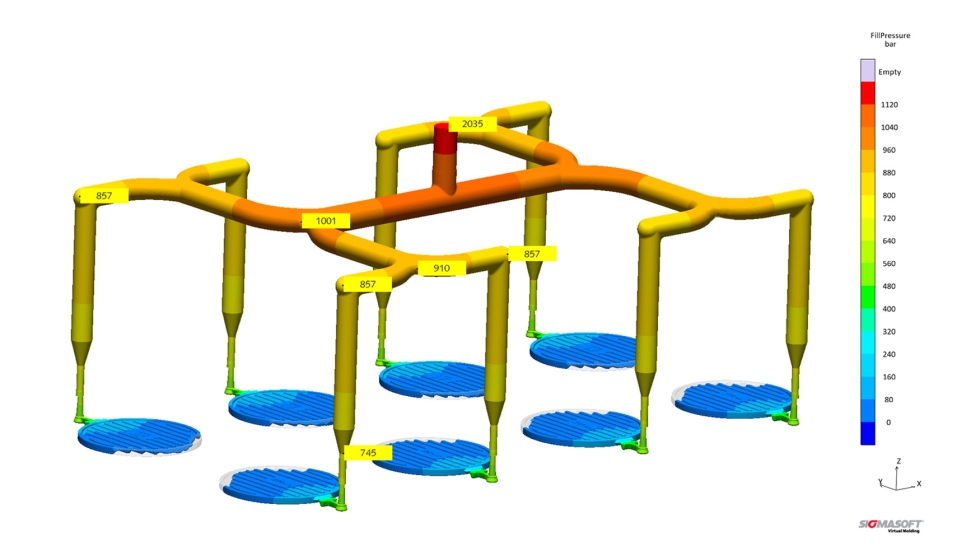
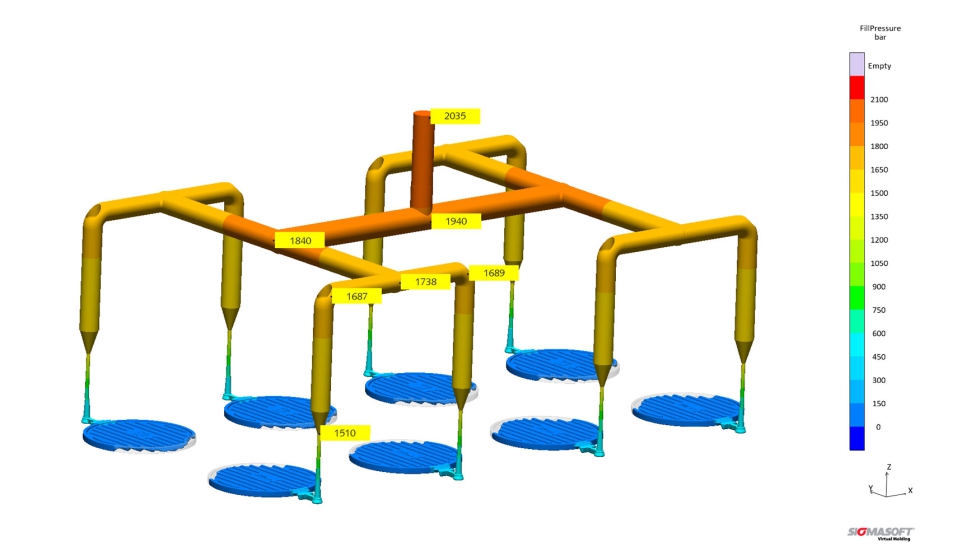