Conceptos que hacen más fácil la vida en la planta de inyección
La descompresión o succión, su función y su relación con la punta del husillo
¿Cuál es su función?
A medida que los materiales se fueron sofisticando y teniendo más complejidad en su proceso apareció la necesidad de descomprimir el material que había sido dosificado con una descompresión o succión después de la dosificación.
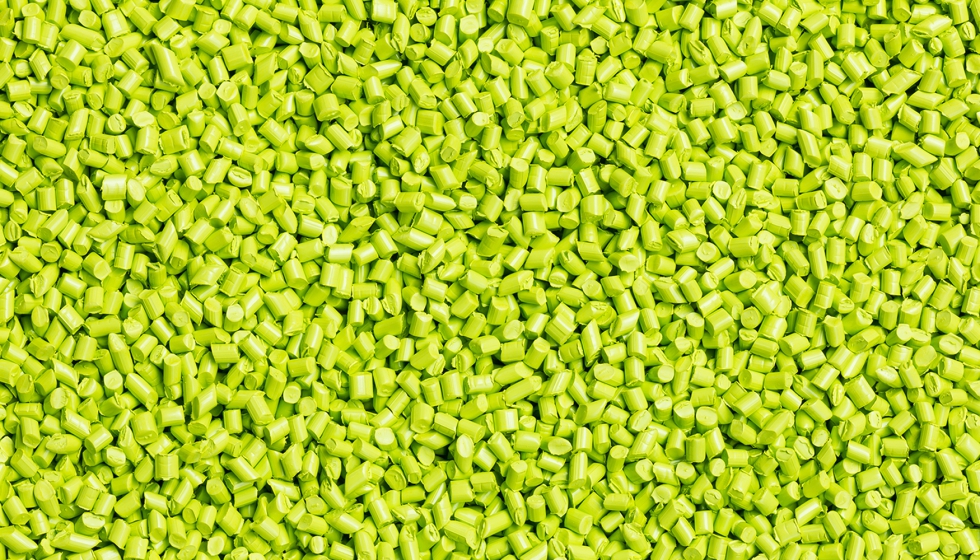
¿Por qué esta necesidad?
La utilización de boquillas de la unidad de inyección directas y sobre todo la fabricación con materiales semicristalinos hacía que al retirar la unidad de inyección después de la fase de dosificación, se produjera una pérdida de material desde la unidad de inyección. Hay que tener en cuenta que el material dosificado se encuentra bajo la presión aplicada en la regulación de la contrapresión durante la carga. Esta presión aplicada en el material fundido en la zona delantera de la unidad de inyección listo para ser inyectado, junto con una boquilla de máquina caliente y abierta, hace que se produzca esta fuga de material también llamado “babeo” que hace que perdamos, de modo descontrolado, parte del material fundido dosificado para la siguiente inyectada.
Entonces, ¿por qué no eliminamos esta presión sobre el material dosificado llamada contrapresión? Esta presión es indispensable para homogeneizar el material durante la dosificación. Sin ella no se produce el funcionamiento correcto del husillo (ver artículo publicado en Interempresas llamado “husillos”).
Por tanto, necesitamos que durante la dosificación exista una presión en el material dosificado en la zona delantera del husillo. Esto no es problema mientras estamos dosificando pues la unidad de inyección está apoyada contra el molde y el material fundido, aunque sometido a presión, no tiene por donde escapar fuera de la unidad de inyección.
El problema aparece cuando retiramos la unidad de inyección y la separamos del molde. En ese momento, es cuando se puede producir la fuga de material o babeo desde la unidad de inyección hacia el exterior perdiendo parte de la dosificación. Es de reseñar que si perdemos parte de la dosificación de manera descontrolada e irregular no podremos tener precisión en la inyección.
Como comentado al inicio de este artículo, esta es la situación más frecuente cuando se utilizan materiales semicristalinos. Este tipo de materiales tiene una temperatura de fusión muy definida por encima de la cual, el material está fundido y su viscosidad es baja, por tanto puede fluir fácilmente. Sin embargo, si el material semicristalino se encuentra por debajo de la temperatura de fusión, el material es sólido e imposible de hacerlo fluir. El gradiente entre el material semicristalino en estado fundido y en estado sólido es de unos pocos grados, de ahí la dificultad para controlar la pérdida o babeo a través de la temperatura del material en la boquilla de la inyectora.
Por ello, con materiales semicristalinos hay que asegurar que la temperatura del material en la boquilla de la unidad de inyección está por encima de la temperatura critica de fusión, y por tanto, el material estará fundido y con baja viscosidad, lo que facilita enormemente que pueda producirse la pérdida o babeo.
En el caso de los materiales amorfos, su comportamiento permite la regulación de la temperatura de la boquilla de la inyectora de modo que el material esté semi sólido y haga de obturación de la posible pérdida de material por la boquilla pero no esté lo suficientemente sólido para taponar u obturar el paso de material durante la inyección consiguiente.
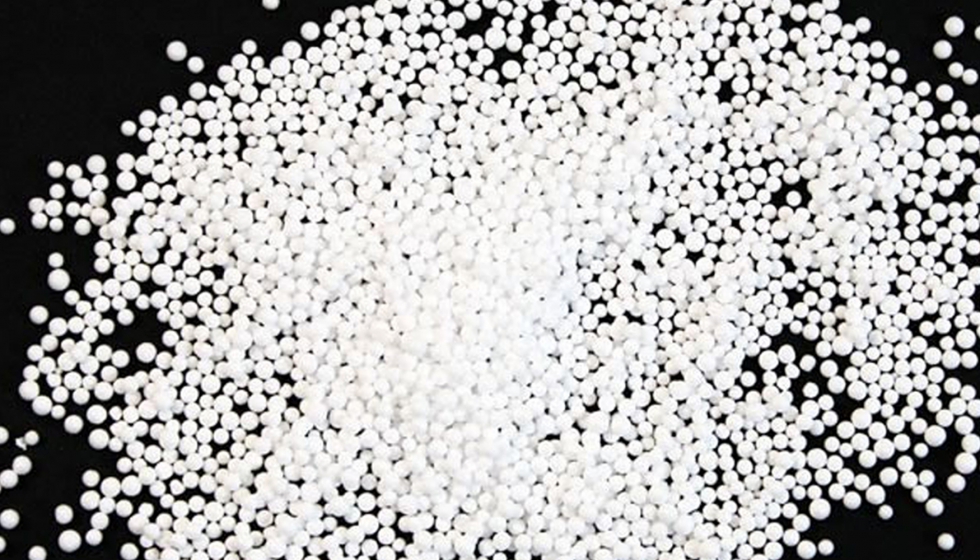
Para que se produzca esta indeseable pérdida incontrolada de material por la boquilla se tienen que dar dos factores: uno, que el material esté fundido y por tanto su viscosidad sea baja, y el otro, es que el material se encuentre a una presión mayor que la presión exterior o atmosférica.
Si al terminar la dosificación con la contrapresión requerida para una buena homogeneización de la masa y un buen funcionamiento del husillo, desplazamos hacia atrás el husillo en un movimiento lineal amplio, se produce un aumento del volumen disponible para contener el material dosificado. Con ello, la presión del material en la zona delantera del husillo disminuye drásticamente eliminando en gran manera la posibilidad de fuga de material.
Hoy en día, este movimiento opcional denominado “Descompresión después de la dosificación" lo tienen en su programación todas las inyectoras disponibles en el mercado.
Descompresión antes de la dosificación
Este movimiento, como su nombre indica, realiza un movimiento rectilíneo del husillo, sin que este gire, en una distancia y una velocidad programada por el técnico de inyección justo antes de realizar el giro del husillo para la dosificación.
¿Cuál es una de sus funciones?
Hay un momento en todos los procesos de inyección sea cual sea la máquina, molde o material donde podemos reducir el desgaste y aumentar la vida del husillo, de la válvula de la punta del husillo e incluso del motor del husillo. Especialmente importante es el desgaste de la válvula de la punta del husillo al ser este un elemento crítico en la repetibilidad y consistencia del proceso.
Si nos fijamos en detalle al final de la fase de compactación, después de las fases de pack and hold (ver artículo publicado en Interempresas llamado, “pack and hold, dos fases de la misma etapa”), la punta del husillo se encuentra en la posición avanzada, con el anillo flotante de cierre de la válvula antirretorno apoyado contra el anillo fijo. De esta manera hacen una unión estanca.
En ese momento, la presión entre estos dos anillos es altísima, de unos cuantos cientos de bares al menos, debido a que el plástico que hay en la zona delantera del husillo está presurizado al nivel de la presión de compactación y este plástico está presionando en anillo flotante de la válvula contra el anillo fijo con ese mismo nivel de alta presión.
En ese momento, al finalizar el tiempo de compactación o de aplicación de la fase de postpresión, en un instante y súbitamente, la máquina arranca directamente con la fase de dosificación, es decir, el husillo comienza a girar.
Imaginemos el esfuerzo de desgaste entre los dos anillos de ajuste de estanqueidad (que están fuertemente presurizados uno contra otro) cuando inmediatamente entra el par de giro del husillo y les hace girar.
Por ejemplo, si estamos compactando el material con una postpresión de 90 bares hidráulicos, (habría que multiplicar por el factor de intensificación de la inyectora para conocer los bares específicos) que podrían ser 900 bares de presión de inyección específica, esta presión está siendo aplicada directamente sobre el material fundido en la zona delantera del husillo. El elemento que está asegurando esta presión es la válvula de la punta del husillo y dentro de los elementos de la válvula, concretamente el anillo fijo y el casquillo o anillo flotante son los que sellan y hacen estanca la presión aguas arriba.
Imaginemos que el par de giro, en el primer instante, hace girar el husillo con una presión de empuje de 900 bares en el ejemplo comentado, a veces en nuestros procesos puede ser mucho mayor.
Hay que tener en cuenta que el anillo fijo de la válvula de la punta del husillo es un anillo fijo respecto al husillo (es decir, girará a la vez que el husillo) sin embargo el anillo flotante de cierre de la válvula es un anillo flotante e independiente del giro del husillo, aunque este giro le afecta irremediablemente.
Todos sabemos que estos dos elementos, anillo o casquillo flotante de la punta del husillo y el anillo fijo o de sellado son elementos que sufren desgaste debido a su función. También sabemos de la importancia de que este desgaste no sea excesivo o todo nuestro proceso será irregular, pero podemos mejorar su vida útil y minimizar parte del desgaste al que están sometidas estas piezas críticas.
Muchos inyectadores no ponen atención en este instante de cambio, a ese paso de presión de inyección alta para compactar al hacer girar el husillo para dosificar. Aquí es donde por unos instantes se produce un altísima fricción entre estos dos elementos. Posteriormente la presión caerá rápidamente y el plástico fundido que el husillo hace avanzar durante su movimiento de giro hará que el casquillo flotante se separe del anillo de cierre y por tanto, ya no habrá fricción entre ellos. Aunque se producen también otro tipo de fricciones y desgastes que comentaremos en próximos artículos.
Tabla.
¿Cómo podemos minimizar este momento de alta fricción y desgaste?
Una opción es programar en el mando de la inyectora, un tiempo de retardo al movimiento de dosificación. De este modo permitimos que la presión de compactación se reduzca y no haya tanto contacto con presión entre ambos elementos de cierre.
Es suficiente normalmente con un retardo de 0,3 a 0,5 segundos antes de pasar a dosificar. Es cierto que para algunos inyectadores esta acción es alargar el ciclo, pero aumentaremos la vida útil de estos elementos de estanqueidad que nos dan repetibilidad y consistencia al proceso.
Otra opción es utilizar el movimiento llamado 'Descompresión o succión antes de dosificar'. Este es un movimiento rectilíneo hacia atrás del husillo, sin realizar giro alguno, controlado por el técnico de inyección en los parámetros de carrera o distancia a desplazar y velocidad de desplazamiento.
La programación de un movimiento hacia atrás de este tipo hace que la presión sobre los elementos de sellado, anillo fijo y casquillo flotante caiga drásticamente y estos se separen para no friccionar entre ellos. Después, al alcanzar la carrera programada de descompresión, el husillo realizará la dosificación girando normalmente. De este modo no hay desgaste en este movimiento inicial de giro al no estar estos elementos en contacto ni bajo presión.
Con estas opciones, retardo en la dosificación y descompresión antes de la dosificación, obtenemos un menor par de giro en el inicio del movimiento de giro del husillo, lo que es una mayor durabilidad del motor de giro del husillo. Obtenemos un menor desgaste de los elementos de sellado, casquillo y anillo de cierre y por tanto, mayor durabilidad también de estos elementos además de una mayor estanqueidad de la válvula de cierre de la punta del husillo que nos va a beneficiar en un proceso más repetitivo y consistente.
Otras ventajas de la descompresión
Si nos fijamos en el movimiento de sellado y dosificación de la válvula de la punta del husillo, tenemos un movimiento de un casquillo flotante que no controlamos 100%.
Durante la inyección, este casquillo flotante se desplaza hasta apoyar con el anillo de cierre haciendo estanca la válvula durante el movimiento de inyección. Pero cuando empieza la dosificación, este casquillo es empujado por el material que el husillo está dosificando y empujando hacia adelante, de modo que se separa de su posición de sellado y se desplaza hacia adelante. Este desplazamiento no es 100% controlado por el técnico de inyección.
En el momento en que se produce esta separación del casquillo flotante, el material fundido que proviene del husillo puede avanzar hacia adelante a través del espacio que ha liberado el casquillo flotante, pero el empuje y la distancia que recorrerá dependerá de varios factores tales como, caudal de material empujado por el husillo (esto a su vez depende de las revoluciones de husillo), de la viscosidad del material, del diámetro de husillo empleado, etc.
Está demostrado, sobre todo cuando utilizamos diámetros de husillo grandes (mayores de 60 mm) junto con materiales de baja viscosidad, que este recorrido del casquillo flotante durante la dosificación no es un movimiento fijo y repetitivo, es un punto débil, en mi opinión, del proceso de inyección al ser un elemento importante que no controlamos al 100%.
Imagínense el peso de un casquillo flotante de un husillo de diámetro 100 mm combinado con un material de baja viscosidad. El empuje del material al pasar hacia la zona delantera del husillo a través de la válvula apenas podrá desplazar este pesado casquillo flotante hacia el tope delantero de una manera regular y repetitiva durante todos los ciclos.
Si este casquillo flotante no se desplaza hasta el tope del recorrido que ejerce el asiento frontal, y queda en diferentes posiciones del recorrido en cada inyectada, cuando se produce el empuje del husillo en el momento del recorrido del movimiento de inyección, el sellado de las dos piezas, anillo de cierre fijo y casquillo flotante, se producirá en diferentes posiciones del husillo y con diferentes volúmenes desplazados hacia el molde. Es decir, inconsistencia en el volumen inyectado entre ciclo y ciclo. Hay que tener en cuenta el detalle de que cuando el husillo avanza durante el inicio del recorrido de inyección, hay una pequeña parte del recorrido del husillo en el que no empujamos material hacia el molde de modo consistente, pues el casquillo de la válvula de la punta del husillo se encuentra separado del anillo de cierre y hasta que no entren en contacto durante el avance del husillo no tendremos estanqueidad.
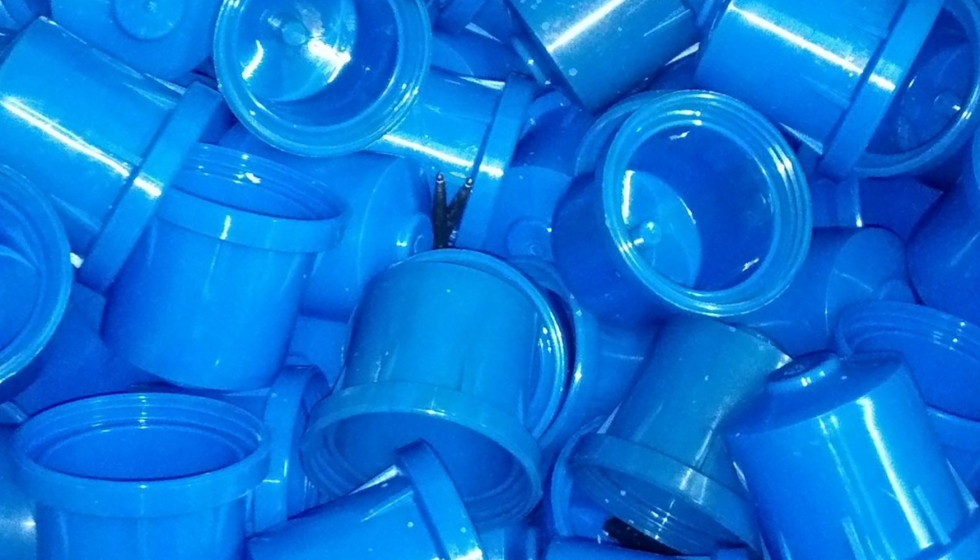
Dependiendo de la viscosidad del material, del caudal aportado por el husillo y del diámetro del husillo este recorrido del husillo hasta que el empuje de material sea estanco puede ser diferente.
He visto múltiples casos con esta combinación de máquina de husillos de grandes diámetros con materiales de baja viscosidad donde las piezas de repente salen faltadas y después vuelven a salir correctas sin existir variación en los parámetros ni desgaste en la válvula de la punta del husillo.
Ante estas situaciones es donde podemos aplicar la descompresión, tanto antes de la dosificación como después de la dosificación, ambas o por separado.
Con este movimiento vamos a desplazar a través del movimiento del husillo, el casquillo flotante a su posición de máxima abertura de paso de material a través de la válvula pero de manera controlada no en función del caudal, diámetro y viscosidad del material y cuando se produzca después de la dosificación el movimiento de inyección, el recorrido para cerrar la estanqueidad de la válvula será repetitivo y constante.
Contrapartida o efecto indeseado
Como contrapartida, la utilización de la descompresión bien sea antes de la dosificación o después de esta dosificación, puede dar lugar a generar defectos estéticos en formas de ráfagas superficiales. Estos defectos se producen debido al aire.
El apoyo y contacto entre la unidad de inyección y el molde a través de la boquilla de inyección de la máquina, no es un apoyo estanco al aire como se podría suponer. Al realizar el movimiento de succión o descompresión, el aire puede entrar por esta descompresión en la zona delantera del husillo. Este aire acompañado de la humedad relativa contenida en el mismo genera, a temperaturas de inyección del plástico, vaporización de esta humedad en forma de ráfagas en superficie de las piezas.
Punta o válvula del husillo
El nivel de cumplimiento de esta función depende en gran medida de qué tipo de válvula, sus calidades en los materiales empleados y también de la geometría y diseño de la válvula.
Cada tipo de punta de husillo existente en el mercado tiene unas ventajas e inconvenientes desde el punto de vista de eficiencia y durabilidad.
Punta del husillo
Normalmente es un conjunto compuesto de tres elementos
- Anillo de cierre trasero
- Casquillo flotante
- Casquillo retenedor o casquillo frontal
Aunque también hay las de 4 elementos. Estas tienen el casquillo frontal montado como postizo realizado con otro material endurecido. Esto permite una mayor duración de este elemento de ajuste así como su sustitución más rápida y económica que el cambio alternativo que sería de toda la punta o válvula del husillo. Este elemento es tan importante en el proceso de inyección que lo analizaremos más en profundidad en próximos artículos.
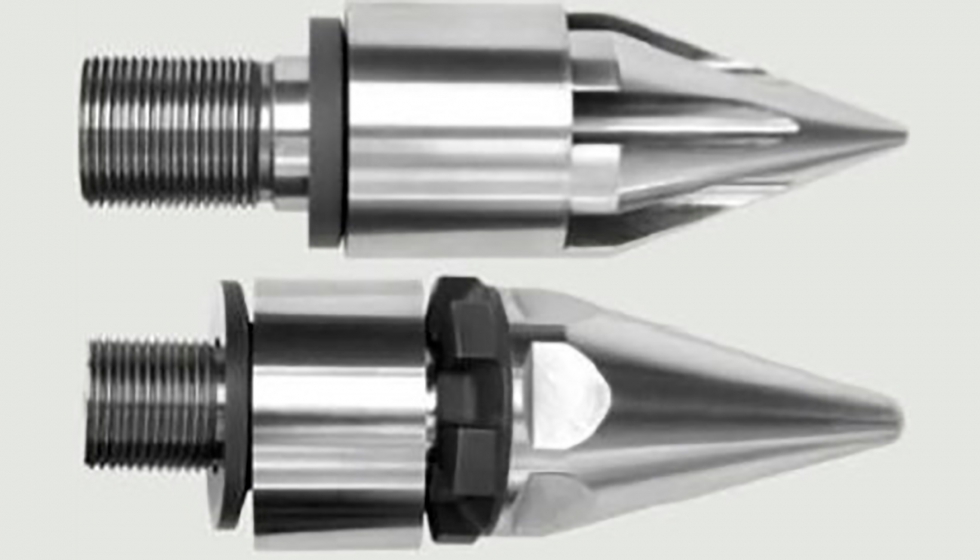
Si disponemos de las opciones de descompresión antes y después de la dosificación así como la posibilidad de retardar la dosis después de la compactación, pensemos en utilizarlas para una mayor durabilidad de la válvula de la punta del husillo y sus elementos y así obtener una mayor repetibilidad y consistencia en nuestro proceso.
José Ramón Lerma es autor de los libros: 'Libro Manual Avanzado de Inyección de Termoplástico', que tiene como objetivo ser, por un lado, una herramienta para la formación y, por otro, un manual de ayuda para todo el personal de una empresa de inyección de plásticos y, del recientemente editado, 'Scientific Injection Molding Tools. Productividad a través del dominio del proceso'. Ambas publicaciones, comercializadas por Plásticos Universales / Interempresas (libros@interempresas.net), consta de detallados casos prácticos, amplia información de moldeo científico y un ‘pendrive’ con 20 hojas de cálculo y herramientas de SC Molding o Scientific Injection Molding, además de optimización y definición de proceso, lo que lo hacen único en el mercado. Página web sobre Scientific Injection Molding: www.asimm.es