Conceptos que hacen más fácil la vida en la planta de inyección
El tamaño de la unidad de inyección sí importa. Primera Parte
José Ramón Lerma, dpto. técnico de Biesterfeld Ibérica
28/09/2020No hay peor sorpresa que poner un nuevo molde en la máquina y descubrir justo cuando empiezas a inyectar piezas, que la unidad de inyección no tiene la suficiente capacidad para inyectar el molde en cuestión. Es probable que no lo reconozcamos ni en presencia de nuestro abogado, pero algunos de nosotros nos hemos visto en esta situación alguna vez.
Dicho sea de paso, en esta situación es cuando desesperadamente haces tus primeras pruebas de la denominada "intrusión", que es una función disponible en la mayoría de las inyectoras donde la máquina hace una extrusión con alta contrapresión durante un tiempo determinado y programable antes de hacer la inyección de toda la capacidad disponible de la unidad de inyección.
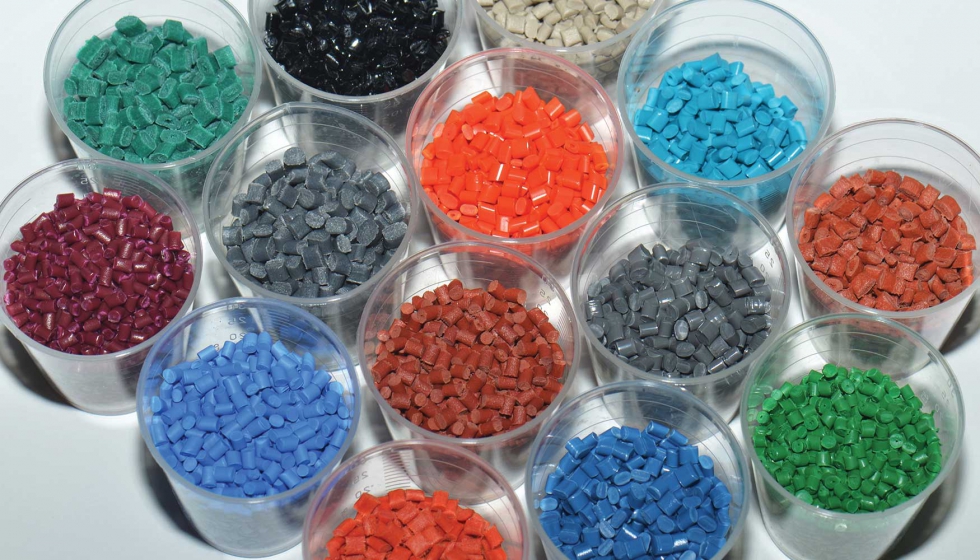
Pueden imaginarse las contrapartidas desde el punto de vista reológico del material de una intrusión o extrusión-inyección de polímero fundido dentro del molde, por ejemplo, factores tales como las homogeneidades de la masa, la cizalla, la velocidad de llenado, etcétera, en esta situación están fuera de todo control. Pero es una opción si disponemos de ella, como lo es una salida de emergencia para una situación provisional y excepcional. Nunca para una producción normal continuada.
En la otra cara de la moneda estaría la situación donde asignamos un molde a una inyectora con la unidad de inyección excesivamente grande. Esto quiere decir que nuestra dosis o utilización de la capacidad de la unidad de inyección será muy baja.
Aquí, en esta situación tendremos varios problemas. Por un lado, si pensamos en la precisión de la dosis obtenida al finalizar la etapa de dosificación y la dosis introducida en el molde en cada ciclo de inyección e imaginamos la punta del husillo con el anillo de cierre desplazándose en su recorrido para abrir y cerra el paso de material fundido.
Imaginemos una inyectora con un husillo de diámetro 50 mm realizando inyectadas con una dosis de 30 mm. Nuestro ratio de dosificación utilizada/ diámetro de husillo sería de 0,6, inferior al mínimo recomendado, que es un ratio de 1.
Si tenemos en cuenta que parte del recorrido de dosificación del husillo –en el ejemplo serían 30 mm–, va a ser el recorrido necesario para abrir y cerrar el anillo de cierre de la punta del husillo, podemos imaginar que nuestro proceso no tendrá robustez ni repetibilidad en la dosis obtenida real y en la dosis real introducida en el molde.
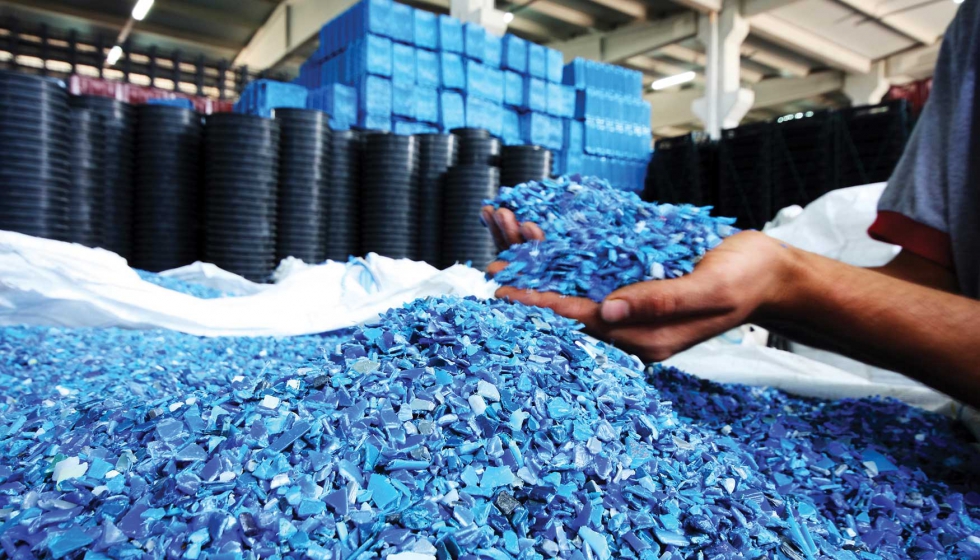
Otro problema añadido a un recorrido tan corto con un husillo grande es la precisión de ejecución de los perfiles de inyección programados si los hay por parte de la inyectora. Si en el ejemplo anterior definimos un perfil, lento-rápido-lento, que actúa con diferentes velocidades en diferentes cotas, en un recorrido de 30 mm de recorrido de husillo, en una inyectora de 50 mm de diámetro de husillo, nuestra precisión de movimientos será baja. Es como matar moscas a cañonazos, con una unidad de inyección con poca precisión para el volumen inyectado cada ciclo.
Volvamos por un momento al caso anterior de utilización excesiva de la unidad de inyección. Por ejemplo, una máquina de diámetro de husillo 50 mm y una dosificación utilizada 300 mm. El ratio de dosificación / diámetro es de 6, muy por encima del recomendado máximo que es 4.
En esta situación tenemos un problema añadido que hay que tener en cuenta.
La inmensa mayoría de husillos que funcionan en las inyectoras de las plantas de inyección son husillos denominados 'universal'. En estos husillos (ver esquema), la zona de dosificación inicial suele tener unos 10 diámetros de longitud, la zona de compresión que va a continuación tiene unos 5 diámetros de longitud y la zona de mezcla unos 5 diámetros de longitud.
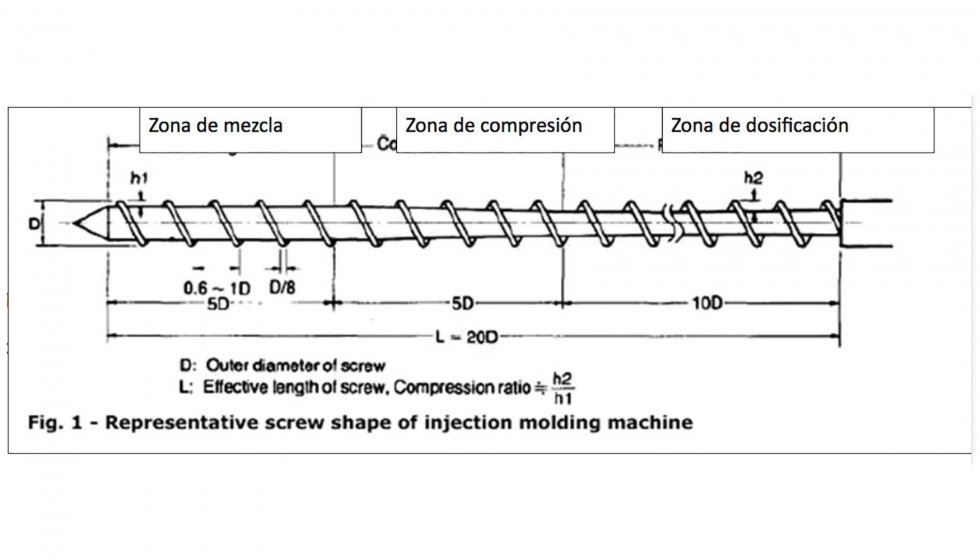
Si, como en el ejemplo comentado, estamos dosificando una dosis equivalente a 6 diámetros, los gránulos de polímero que entran en el husillo en los últimos milímetros de dosis, en las últimas vueltas del husillo, tendrán un “tratamiento” muy diferente a los gránulos de plástico que entraron en el husillo al principio de la dosis. Los gránulos que entraron en los primeros milímetros de dosis van a pasar por un recorrido dentro del husillo en la zona de dosificación mucho mas largo que los gránulos que empezarán este recorrido al final de la dosificación. Estos últimos entrarán (por efecto del retroceso del husillo durante la dosis) en contacto con el husillo en zonas mas delanteras del recorrido. Con esto, estos granos de material entrarán rápidamente en contacto con la zona de compresión del husillo que viene a continuación.
Estas diferencias pueden dar lugar a faltas de homogeneidad en la masa fundida, zonas con diferente estado térmico, etc.
Pero, ¿cómo definimos o determinamos un tamaño ideal de la unidad de inyección? ¿Cómo comprobamos que la unidad de inyección que pensamos utilizar es la adecuada?
Esto lo veremos en el siguiente artículo.
José Ramón Lerma es autor de los libros: 'Libro Manual Avanzado de Inyección de Termoplástico', que tiene como objetivo ser, por un lado, una herramienta para la formación y, por otro, un manual de ayuda para todo el personal de una empresa de inyección de plásticos y, del recientemente editado, 'Scientific Injection Molding Tools. Productividad a través del dominio del proceso'. Ambas publicaciones, comercializadas por Plásticos Universales / Interempresas (libros@interempresas.net), consta de detallados casos prácticos, amplia información de moldeo científico y un ‘pendrive’ con 20 hojas de cálculo y herramientas de SC Molding o Scientific Injection Molding, además de optimización y definición de proceso, lo que lo hacen único en el mercado. Página web sobre Scientific Injection Molding: www.asimm.es