Desarrollan una resina termoestable para la fabricación de moldes de inyección de termoplásticos
Las primeras pruebas de ADDSET, un proyecto de I+D liderado por CT, en colaboración con el centro Eurecat, y financiado por ACCIÓ a través de su programa Nuclis Internacionals, han finalizado con éxito. Acrónimo de Aplicación, Desarrollo y Demostración de resina Termoestable (ThermoSET) y orientado a moldes fabricados aditivamente para inyección de termoplásticos, ADDSET es un proyecto en el que CT ha logrado dar un paso más en el desarrollo de la tecnología de fabricación bajo demanda mediante el desarrollo de una resina termoestable de suficiente temperatura de transición vítrea capaz de ser utilizada como resina en la fabricación de moldes de inyección de termoplásticos.
Tras más de un año de desarrollo, el proyecto de I+D ADDSET se acerca a su objetivo de mejorar la tecnología de fabricación bajo demanda mediante la formulación de una resina termoestable capaz de ser utilizada como resina en la fabricación de moldes de inyección de termoplásticos. A través de este desarrollo, CT plantea además la demostración del nuevo material mediante la aplicación de la fabricación del molde a un caso de uso dentro del sector del transporte, en particular aeronáutica o automoción.
El objetivo del proyecto se ha materializado a través de la aplicación de esta tecnología en un caso de uso para Airbus en las instalaciones del instituto de investigación Fraunhofer IFAM en Alemania y con la colaboración de Eurecat.
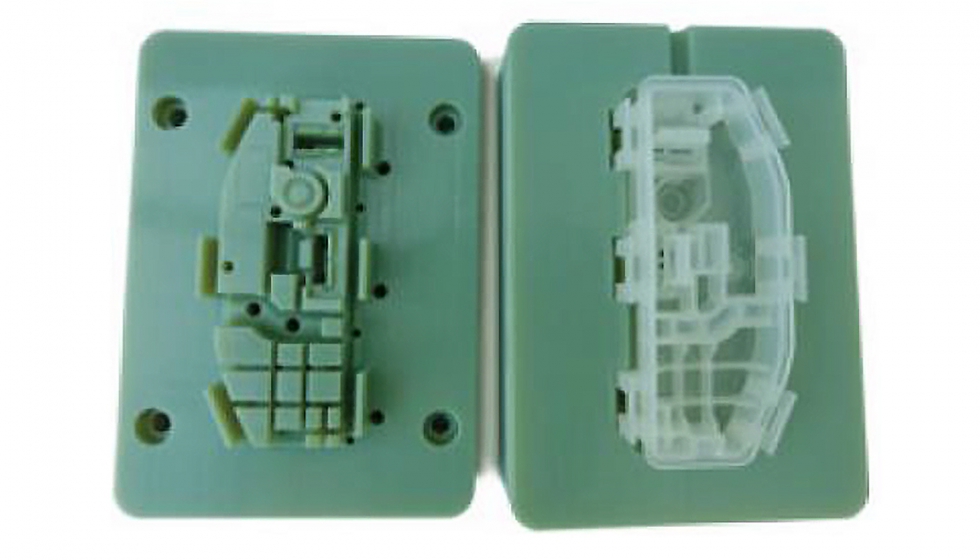
Esta tecnología ofrece una mayor y rápida adaptabilidad a los cambios en el diseño de piezas, que junto con la optimización y el diseño adaptado a la tecnología de impresión 3D, pueden conducir a un menor coste total de fabricación. De esta manera, se convierte en una opción muy atractiva en el ámbito de la fabricación de moldes, utillaje de fabricación y montaje y herramientas.
Por tanto, las tecnologías de impresión 3D, convenientemente aplicadas a moldes, utillajes de fabricación y montaje y herramientas, pueden convertirse de forma clara en un elemento de mayor competitividad para las empresas que lo implementen de forma usual.
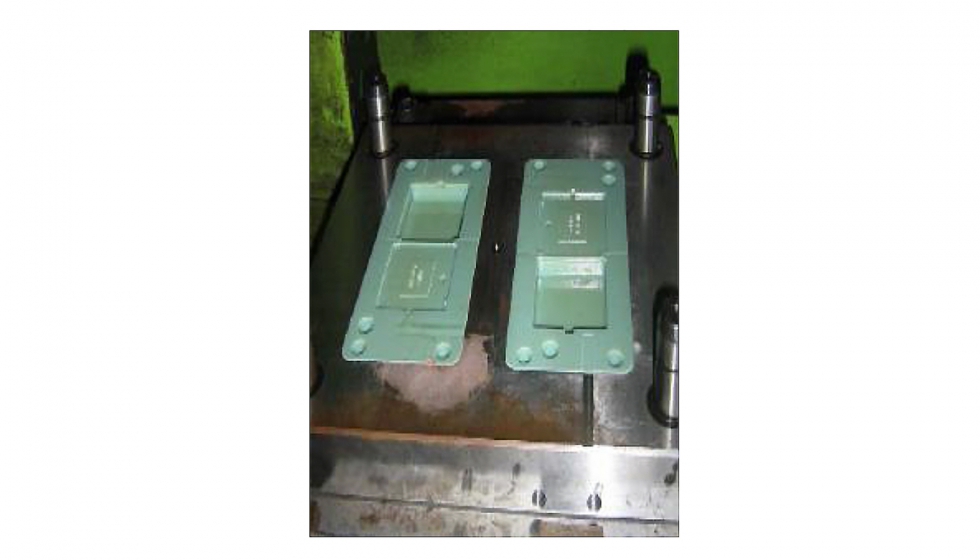
La reducción potencial de costes de las tecnologías de fabricación aditiva se puede asociar a la fabricación de piezas únicas o lotes pequeños, gracias a la disminución de las mermas de materia prima, que permite, por tanto, un máximo aprovechamiento del material y una reducción en el uso de mano de obra al ser un proceso automatizado. Igualmente, se le pueden atribuir otras ventajas tales como un menor tiempo de entrega y una mejora de la funcionalidad, así como una mayor posibilidad de personalización.
Es sabido que el proceso de inyección es un proceso rápido, automatizado, flexible y que puede fabricar piezas geométricamente muy complejas con una elevada precisión dimensional, piezas de algunos gramos, hasta más de 100 kg de peso. El proceso no obstante permite generalmente casos de negocio viables a partir de más 10.000 piezas a fabricar, siendo difícilmente viable para series cortas. Para este proceso, la fabricación del molde conlleva usualmente desde un mínimo de 6 hasta más de 16 semanas para tenerlo finalizado para fabricación de piezas. No obstante, son necesarios ajustes posteriores que alargan el plazo para comenzar la fabricación de serie. Todo esto incrementa el coste del molde de inyección y el coste de oportunidad del producto al mercado.
El caso es como poder aprovechar la inyección de termoplásticos en sectores donde las series cortas lo hacen inviable, por ejemplo, en aquellos donde solo se necesitan 100 piezas o donde las piezas se necesitan de forma urgente, por ejemplo, en un par de días. Un ejemplo de sector de baja cadencia que actualmente no puede utilizar las ventajas de la inyección de termoplásticos es el sector aeronáutico; otro puede ser el sector de vehículos de carretera especiales.
En el sector aeronáutico surgen piezas con geometrías complejas, que quizás en otros sectores no existirían, por la inmensa necesidad de optimizar el peso. En definitiva, el sector requiere una mayor complejidad de la pieza y un cambio de materiales de la pieza de metal a polímero. En muchos casos, esta necesidad no puede resolverse con la impresión 3D directa de la pieza, ya sea por falta de material específico para hacerla (la gama de materiales de impresión 3D está a día de hoy marcada por los fabricantes de equipo, y es una gama cerrada) o por otros condicionantes técnicos de variabilidad del proceso.
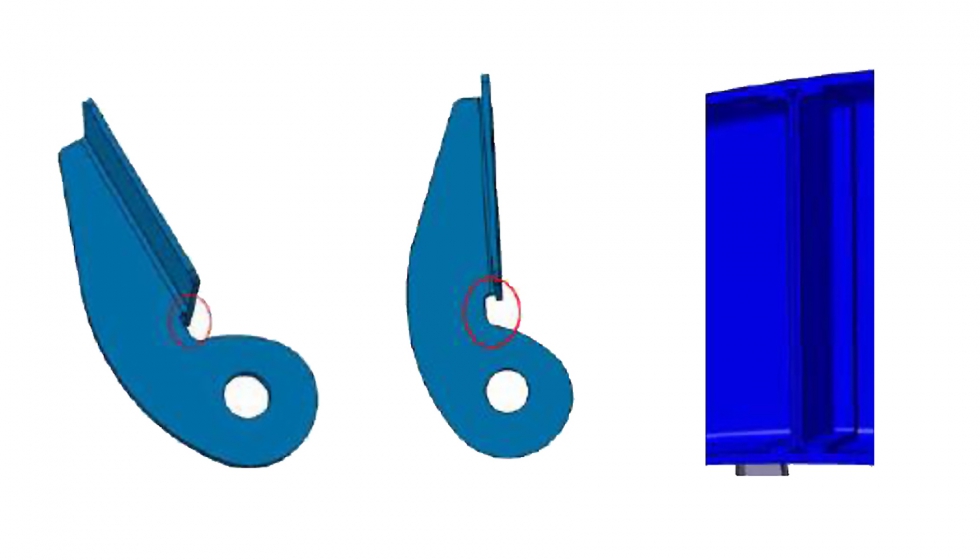
En general, la implementación de las cavidades específicas para un molde es una de las tareas más caras del proceso de fabricación., Además de resultar generalmente cara, es la parte que del molde que más tiempo conlleva en su fabricación, ya que se trata de la zona del molde con mayor desafío técnico. La fabricación de moldes de inyección por impresión 3D, ya sea para prototipos o para un número reducido de unidades, es algo que se está utilizando actualmente. Sin embargo, la vida del molde es bastante corta debido principalmente a la pobre conductividad y a la baja estabilidad térmica de los materiales poliméricos utilizados. Lo más frecuentes es que esos moldes solo puedan resistir la fabricación de 1 a 50 unidades máximo.
Los polímeros utilizados son los facilitados por el fabricante de máquinas y algunos de estos son: Polietileno, Polipropileno, PLA, ABS, PETG. Otros ejemplos de los más técnicos que están en desarrollo serían: PEEK, PPSU o PPSF. Basados en las características del estado del arte observado, así como también en las limitaciones actuales, el proyecto ADDSET plantea como objetivos:
- Mejorar en la conductividad térmica, consiguiendo de esta forma una rápida uniformidad de temperatura de la parte del molde hecho en resina termoestable y evitando esfuerzos mecánicos generados por las solicitaciones térmicas. Todo ello permite alargar considerablemente la vida del molde.
- Mejorar en la estabilidad térmica, consiguiendo evitar deformaciones debidas a los ciclos térmicos del molde y por tanto manteniendo la estabilidad dimensional del mismo y por ende de la pieza a fabricar. Así mismo, se consiguen fabricar más piezas con el mismo molde.
Algunas de las características intrínsecas de los materiales, resinas, termoestables de las cuales se busca aprovechar en ADDSET son:
- Resistencia mecánica media superior a resinas termoplásticas
- Buena resistencia a la distorsión por temperatura
- Baja fluencia (menor coeficiente de deformación bajo la influencia de las solicitaciones mecánicas)
- Mayor adhesividad que permita imprimir directamente sobre un subcomponente
Desde un punto de vista cuantitativo, el objetivo planteado en ADDSET buscará obtener las siguientes cifras:
- Aumentar la vida de las piezas del molde hechas por impresión 3D, con la nueva resina termoestable, en un factor de 3: actualmente limitado, con un grado de calidad adecuado, al orden de 50 piezas inyectadas máximo.
- Reducir los costes de fabricación del molde, mediante el empleo de la nueva resina para la cavidad del mismo, en un factor de 2: tomando como base el mecanizado de una cavidad de acero para moldes
- Reducir el plazo de entrega del molde en un factor de 3: tomando como base un plazo de entrega medio de un molde producido por tecnología convencional de aproximadamente 10 semanas
- Optimizar al peso de la pieza, mediante la utilización de metodología de diseño innovadora (DIGIMAT), de forma tal de ahorrar peso en un factor de 1,4 => tomando como base una pieza fabricada en metal aluminio con una densidad de 2,78 g/cm3.
Tras los primeros resultados obtenidos en el proyecto se ha logrado formular una resina termoestable que permite la inyección de polímeros técnicos como PA66 (poliamida) reforzada con fibra de vidrio. Después de 100 inyecciones en las piezas apenas se aprecian rebabas y el molde no se descascarilla.
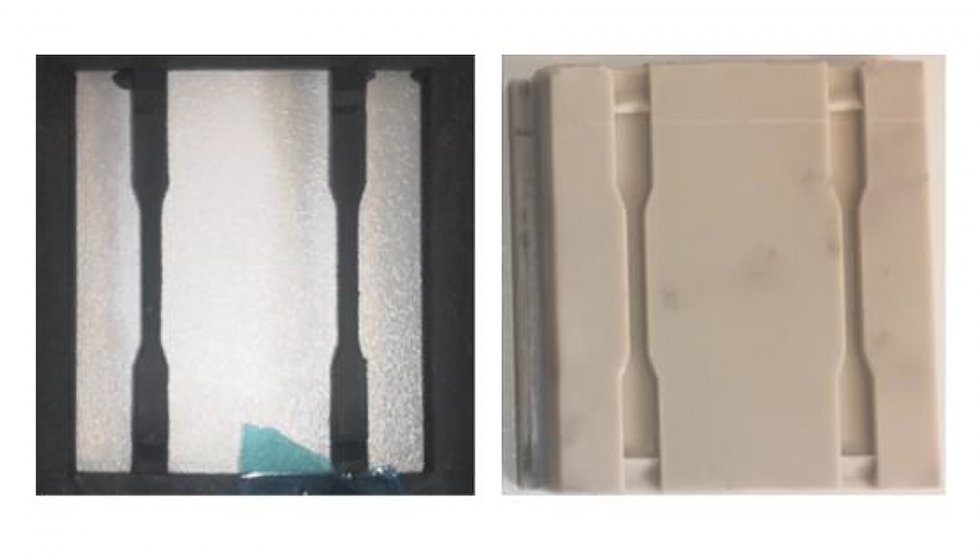