Conceptos que hacen más fácil la vida en la planta de inyección
Canales y entradas
Canales de distribución
El cálculo correcto de las dimensiones de un canal de distribución se realiza partiendo de la dimensión del espesor de la pieza. Este es el punto de partida del cálculo. Seguidamente, se calculan los diferentes niveles del canal de distribución, esto es, en primer lugar el canal que ataca la entrada y seguidamente todos y cada uno de los canales que componen el sistema de llenado hasta llegar al bebedero.
Cada uno de los canales son los subcanales hasta llegar al que está en contacto con el bebedero. Este es el 'main runner' o canal principal.
Una de las características a tener en cuenta en el cálculo, es la viscosidad del material. No es lo mismo la sección necesaria para un material fluido que para un material con baja fluidez. El primer cálculo es el del canal que ataca la entrada. Éste debe ser de un espesor equivalente al espesor de la pieza más un valor de incremento que puede ser de 1 o 1,5 mm dependiendo de la viscosidad del material.
El siguiente canal que calcular es el siguiente subcanal. Éste debe ser de un espesor equivalente al espesor del canal anterior más un valor de incremento que puede ser de 1 o 1,5 mm dependiendo de la viscosidad del material.
Así sucesivamente en todos los niveles de subcanales que tenga el sistema de canales de distribución del llenado. Finalmente, después del cálculo del 'main runner' o canal principal se deben calcular los diámetros mayor y menor del bebedero cónico.
Para ello hay que tener en cuenta que el diámetro pequeño del bebedero debe ser mayor que el espesor de la pieza. Así aseguramos que el espesor de la pieza es la dimensión más pequeña de todo el sistema de llenado de la cavidad.
Realizando estos cambios de dimensiones en cada canal, aseguramos también la correcta presurización del sistema de llenado y no aplicar al material una cizalla excesiva.
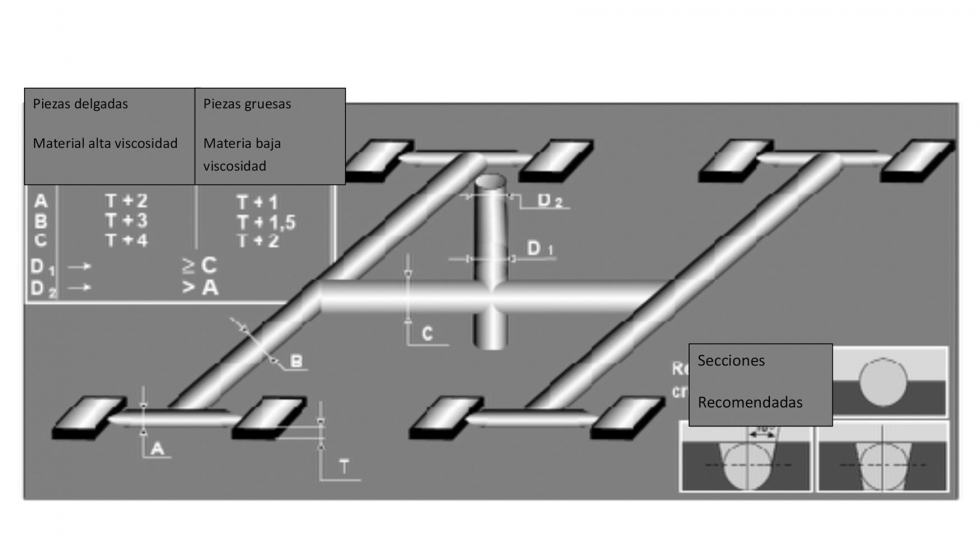
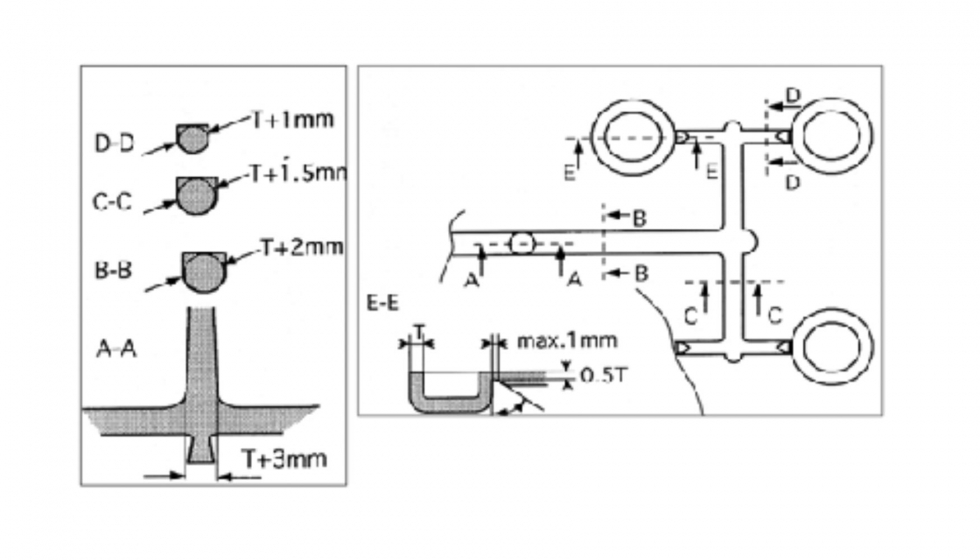
Esquema de dimensionamiento correcto de los canales de distribución a lo largo del recorrido del material. Estos incrementos permiten presurizar bien el sistema de canales.
Canales Calientes
Aislamiento del torpedo y el molde
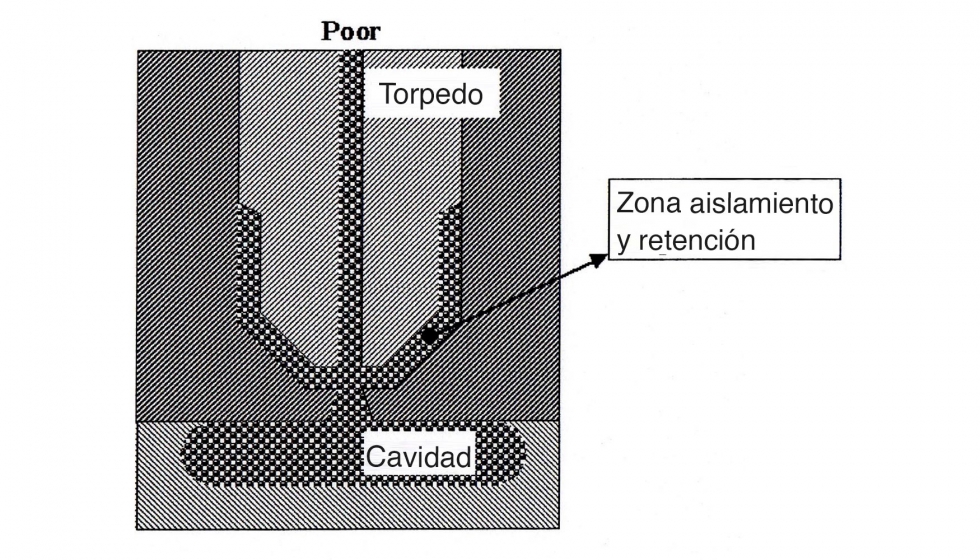
En este caso el torpedo está aislado térmicamente del molde a través del polímero. Posibles degradaciones del polímero pueden causar, gases, ráfagas y puntos negros.
Alternativa: colocar pieza de Vespel de Dupont para aislar esta zona para evitar retenciones en materiales térmicamente sensibles, transparentes, cambios de color, etc.
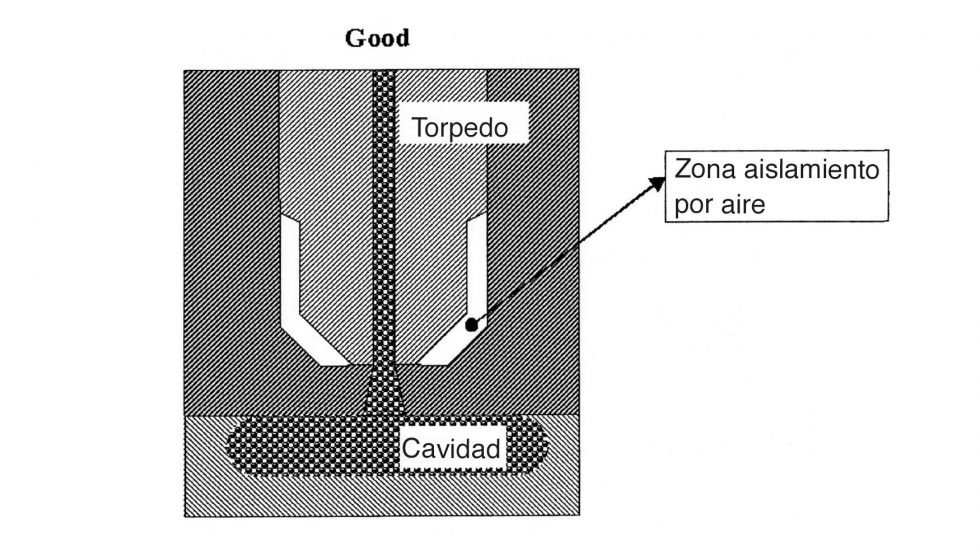
Entradas
Las entradas son la mayor restricción de todo el sistema de llenado. El paso del material fundido a través de esta super restricción supone un punto crítico del proceso ya que se genera una gran fricción del material fundido al pasar. Tanto, que podemos generar degradaciones moleculares o del paquete de aditivos del polímero con lo que puede aparecer pérdida de propiedades del material o defectos estéticos en las piezas producidas.
Además, las dimensiones de la entrada determinan el tiempo que éstas permanecerán abiertas para poder llenar y compactar el material dentro de la cavidad. Después del llenado volumétrico de la cavidad, se producirá una pérdida de volumen o contracción que debe ser compensada haciendo entrar más moléculas de polímero en la cavidad. Para ello es imprescindible que la entrada permanezca abierta el tiempo suficiente sin cerrarse y sellar la entrada.
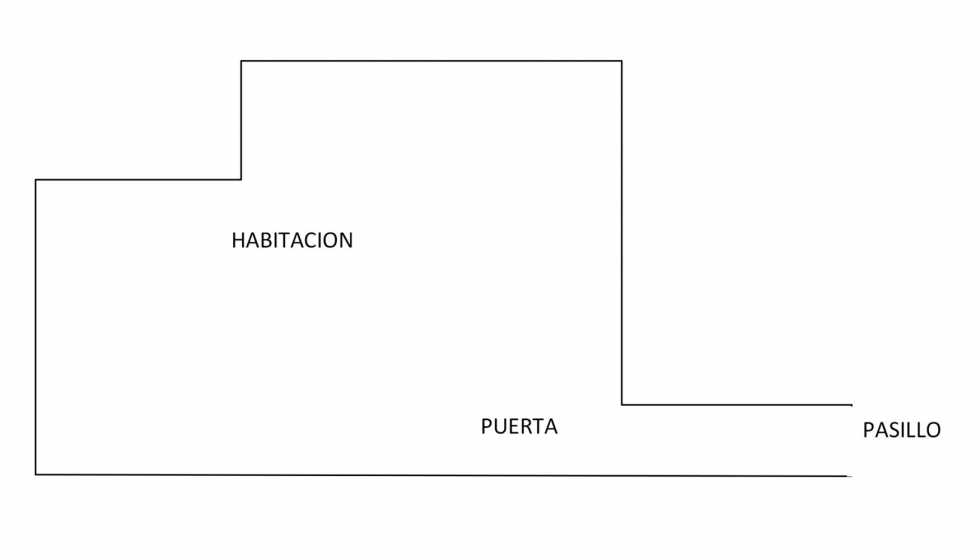
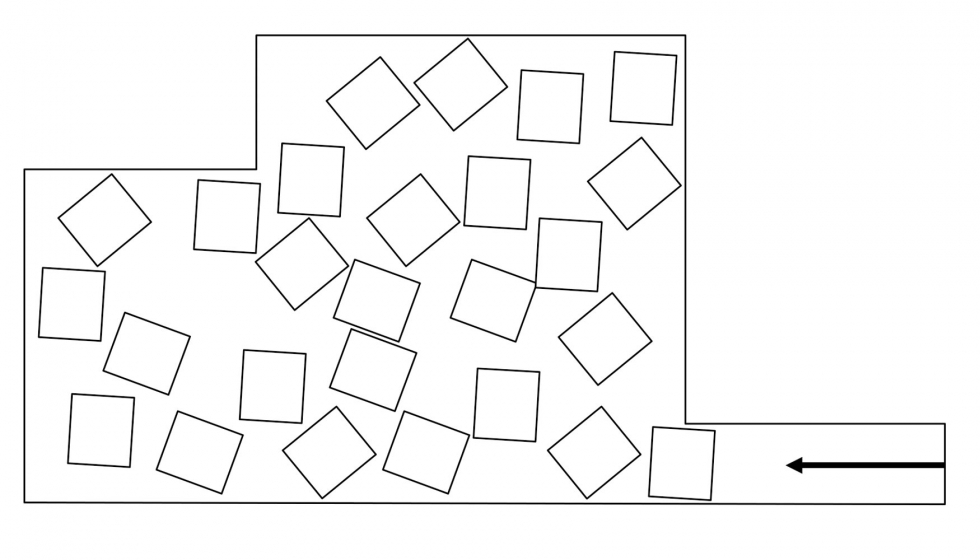
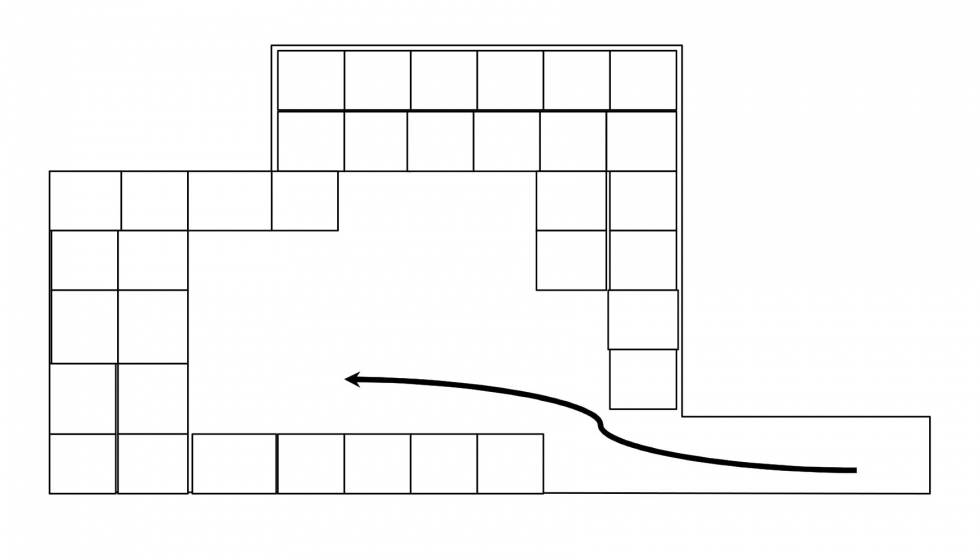
Las entradas son normalmente con secciones de forma redonda o rectangular. En ambos casos, para realizar el cálculo de las dimensiones correctas de la entrada se tiene en cuenta el espesor de la pieza.
Entradas redondas
El diámetro de la entrada en el caso de las entradas redondas se calcula en función de un porcentaje del espesor de la pieza. Para materiales de buena fluidez se puede aplicar un 50% del espesor de la pieza y para materiales viscosos se puede llegar a 80-90 e incluso 100% del espesor de la pieza.
Entradas rectangulares
En el caso de entradas rectangulares, estas tienen tres dimensiones:
- 'Deep' o profundidad: Esta característica de la entrada determina el tiempo de sellado de la misma. Aquí se pueden aplicar valores dependientes del espesor de la pieza. Para materiales de buena fluidez se puede aplicar un 50% del espesor de la pieza y para materiales viscosos se puede llegar a 80—90 % del espesor.
- 'Wide' o anchura: Esta característica se dimensiona en función del volumen de material que va a circular a través de la entrada. Se aplican valores de 2 veces la profundidad para piezas pequeñas y hasta 5 ó 6 veces la profundidad de la entrada para piezas de mayor volumen.
- 'Land' o longitud: Esta característica es el enlace entre el canal y la entrada. Aquí no debemos aplicar una longitud de este enlace mayor de 0,5 a 1 mm. Exceso de “land” provoca sobrecalentamiento del material.
José Ramón Lerma es autor del Libro Manual Avanzado de Inyección de Termoplástico, que tiene como objetivo ser, por un lado, una herramienta para la formación y, por otro, un manual de ayuda para todo el personal de una empresa de inyección de plásticos. El libro, comercializado por Plásticos Universales / Interempresas (libros@interempresas.net, consta de detallados casos prácticos, amplia información de moldeo científico y un ‘pendrive’ con 20 hojas de cálculo y herramientas de SC Molding o Scientific Injection Molding, además de optimización y definición de proceso, lo que lo hacen único en el mercado. Página web sobre Scientific Injection Molding: www.asimm.es
Más información sobre los cursos Scientific Molding online impartidos en Inefco, en los que José Ramón Lerma es tutor https://www.ieaula.com/home/31-procesos-avanzados-de-inyeccion-de-termoplasticos.html