Ingeniería inversa para un molde de una plantilla de silicona
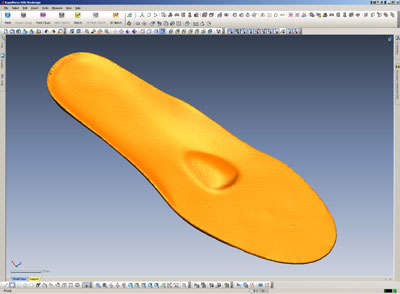
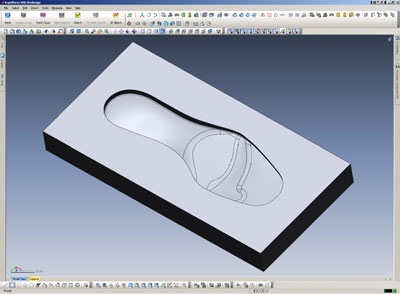
Sin embargo este modelo CAD no existía, ya para el desarrollo de las plantillas se había contado con la experiencia de un modelista (ya jubilado) que manualmente trabajo cada cavidad directamente en el molde, necesitando en torno a 6 meses para desarrollar su labor. A este problema se añadió la necesidad de modificar la geometría de las plantillas, conforme al retorno de experiencias de su clientela y las indicaciones de los podólogos de la empresa.
Primeramente se digitalizaron con un potente escáner 3D de Konica Minolta los diferentes modelos de plantillas elegidas (las piezas derechas únicamente; las izquierdas serian una simetría perfecta).
Una vez tratada la nube de puntos en el ordenador mediante el software Rapidform XOS/XOR se crearon las superficies, y el sólido resultante sirvió como base para definir las diferentes tallas de pie necesarias. Esta fase se realizo en 1 semana.
Seguidamente se introdujeron en el ordenador las modificaciones pedidas por los podólogos y clientes. Se variaron las formas de los talones y las alturas y formas de los arcos.
Para validar cada modificación se lanzaron moldes prototipos en estereolitografía (tres días de plazo) con lo que se fabricaron plantillas con la misma silicona que la producción serie. En total se realizaron tres moldes prototipos. La fase de validación se realizo en aproximadamente un mes.
Una vez validados los diseños de las plantillas, se diseñaron en 3D los moldes correspondientes y se mecanizaron en aluminio durante un mes de trabajo; de esta forma todas las cavidades eran iguales.
Actualmente, estos moldes están en producción, habiendo conseguido una reducción de costes conforme a los objetivos marcados, con un plazo aproximado de nueve semanas de desarrollo.
Trazza Soluciones de Ingenieria es pionera y experta en la ingenieria inversa de todo tipo de piezas y sectores. Dispone de un escáner 3D de Konica Minolta, con una tolerancia de trabajo de 0,05 mm y con Rapidform XOS/XOR, el mejor software del mercado para el tratamiento de nubes de puntos e ingenieria inversa, y todo ello sobre estaciones de trabajo gráficas, capaces de manejar más de 50 millones de puntos.
La digitalización se realiza en sus instalaciones o en casa del cliente si es necesario, y trabajan para diferentes sectores: automóvil, aeronáutica, arte, arquitectura, medicina, ortopedia, etc.
Igualmente realizan funciones de desarrollo de pieza, así como la fabricación de prototipos en diferentes tecnologías, según la finalidad de los mismos.
Recientemente, Trazza Soluciones de Ingeniería ha firmado acuerdos de distribución con Konica Minolta y Rapidform.
Más información: http://www.trazzasoluciones.es
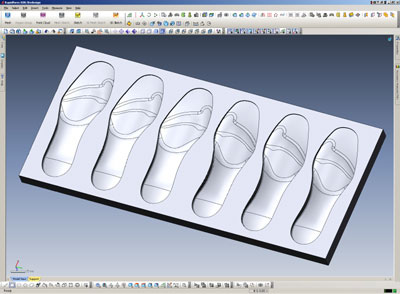
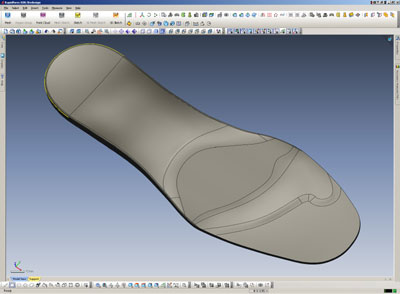