Acabado de superficies: sobre el acabado de la huella
La fabricación de moldes y matrices, tanto para la estampación y troquelado de chapa metálica, como para la inyección de piezas de plástico y aluminio, representa una parte importante dentro del sector de automoción. Considerando la estructura de costes asociada al proceso de producción, las operaciones de pulido en superficies complejas pueden llegar a suponer más de un 30% del tiempo total de fabricación. En la mayoría de los casos, salvo aplicaciones específicas, el pulido de moldes y matrices sigue siendo llevado a cabo por personal altamente especializado empleando técnicas abrasivas manuales.
1. El acabado de la huella, clave en moldes y matrices
Los productos y componentes que contienen superficies complejas han incrementado su importancia en la industria debido al aumento de la funcionalidad de este tipo de productos (características aerodinámicas, apariencia, optimización ergonómica y mejoras estéticas). Ejemplos se pueden encontrar fácilmente en el sector aeroespacial, del automóvil, y en la fabricación de moldes y matrices. En los componentes fabricados por mecanizado, uno de los principales indicadores de calidad es el grado de acabado superficial. Este depende directamente del tipo de proceso y de las condiciones empleadas para llevarlo a cabo. El acabado superficial es una parte importante de la integridad superficial y normalmente presenta gran importancia en el comportamiento funcional de las piezas. Muchas de las propiedades funcionales del componente dependen directamente de este factor, como por ejemplo la resistencia a fatiga, a desgaste, el comportamiento ante rozamiento, rodadura, lubricación, condiciones de estanqueidad, brillo y aspecto entre otros. En muchas ocasiones, para cumplir con los requisitos de rugosidad, dureza o integridad superficial en general, se llevan a cabo procesos adicionales de acabado. Por ejemplo, en el caso de grandes moldes y matrices de estampación con geometrías complejas, es normal realizar un pulido a mano como proceso de acabado, el cual puede representar un elevado porcentaje del total de tiempo de fabricación. A continuación se presenta el proceso de bruñido con bola para el acabado de este tipo de superficies.
2. El bruñido por deformación
El bruñido por deformación, o simplemente bruñido, se basa en generar pequeñas deformaciones plásticas en la superficie de la pieza tratada. Como elemento deformante se utilizan habitualmente herramientas en forma de bola o rodillo, fabricadas en materiales de elevada dureza, resistencia y límite elástico. El proceso consiste en presionar la herramienta de bruñido, o bruñidor, sobre las microirregularidades de la superficie y generar un deslizamiento y/o rodadura sobre la superficie a tratar para cubrir el área total de la pieza. De esta forma se consigue una capa de material endurecido por deformación que presenta mejores características tanto físicas como mecánicas respecto al material base. El aplastamiento genera efectos beneficiosos sobre la superficie, mejorando por una parte sus propiedades y como consecuencia el comportamiento funcional del componente. Los efectos del bruñido sobre la superficie son la mejora de la rugosidad final, el aumento de la dureza superficial y la introducción de tensiones residuales de compresión. Estos efectos a su vez hacen que el componente mejore sus propiedades en cuanto a vida a fatiga, corrosión y resistencia al desgaste. Son muchas las diferentes versiones de herramientas de bruñido que podemos encontrar en el mercado.
2.1. Bruñido con bola
El bruñido con bola es la configuración idónea para el acabado de superficies complejas. El principio de funcionamiento del bruñido hidrostático con bola, se basa en el concepto de muelle hidrostático. Se utiliza un fluido incompresible, normalmente taladrina, para generar la fuerza necesaria sobre la superficie. En comparación con el bruñido mecánico (utilizando un muelle calibrado), el bruñido hidrostático permite generar presiones controladas más elevadas sobre la superficie de la pieza, además de mantener una fuerza constante en todo el recorrido del muelle hidrostático. La fuerza normal generada sobre la superficie solamente depende de la presión de la bomba de bruñido y la geometría interior de la herramienta, la cual será constante para cada diámetro de bola. La presión es suministrada por una bomba hidráulica, la cual puede estar equipada con su propio depósito de taladrina o puede alimentarse directamente del depósito de la máquina donde se monte el equipo. Normalmente las bombas de bruñido alcanzan los 40 MPa de presión y suelen colocarse junto a la máquina donde se montará el sistema de bruñido. El elemento clave es la bola, que soportada hidrostáticamente, gracias a la presión de la bomba, presiona las crestas de mecanizado aplastándolas y logrando la mejora en la rugosidad. Gracias al muelle hidrostático, la bola tiene un movimiento libre de 6 mm donde mantiene constante la fuerza de bruñido. Este rango ayuda a absorber errores en las piezas, y facilita asimismo la programación del proceso de acabado. La técnica de bruñido hidrostático puede emplearse en superficies cilíndricas, superficies frontales planas, superficies de forma o perfiladas, superficies cónicas, biseles, respaldos, cambios de sección, etc.
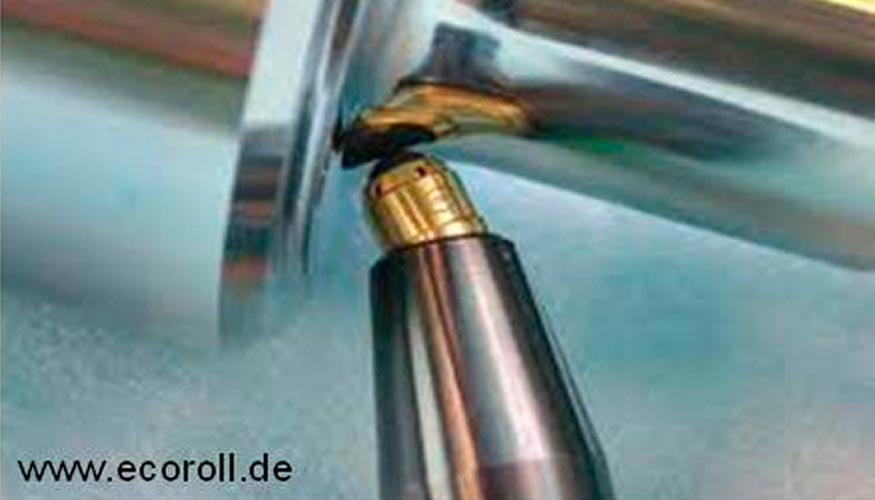
Herramienta de bruñido con bola de Ecoroll.
2.2. Beneficios y limitaciones del bruñido
Las técnicas de bruñido se caracterizan por ser procesos que no requieren grandes inversiones, con tiempos de ciclo relativamente cortos al poder trabajar a velocidades elevadas, y que generan una superficie final de gran calidad, tanto en aspectos de acabado superficial como en mejora de las características mecánicas del componente. En esta línea, a continuación se resumen los principales beneficios y limitaciones del proceso.
a) Beneficios técnicos y económicos
El mercado necesita soluciones avanzadas para realizar mecanizados completos en una atada, obtener un acabado superficial adecuado, en el menor tiempo posible, al mínimo coste y garantizando la seguridad y fiabilidad del proceso. El bruñido es un proceso que cumple estos requisitos. Además, este proceso mejora las propiedades mecánicas superficiales del componente. Los principales beneficios del proceso se citan a continuación:
b) Equipamiento necesario: Montaje y puesta a punto
El coste de un equipo de bruñido puede oscilar desde los 500 € cuando se trata de herramientas de bruñido mecánico hasta los 8.000 € cuando se trata de equipos de bruñido hidrostático donde es necesario la adquisición de un equipo de bombeo a alta presión. La inversión en equipamiento en estos casos es notablemente inferior a la inversión necesaria en cualquiera de los procesos de acabado y tratamientos superficiales normalmente utilizados. Además, el bruñido cuenta con la ventaja de poder utilizarse en la misma máquina donde se realiza el mecanizado previo, evitando grandes inversiones en maquinaria y evitando también el traslado de piezas de una máquina a otra.
c) Acabado superficial y tolerancias dimensionales
El bruñido genera superficies de gran calidad con rugosidades superficiales pequeñas, del orden del rectificado, con valores entre 0,05 µm y 0,5 µm de rugosidad media. El proceso de bruñido permite mantener o incluso mejorar las tolerancias dimensionales previas del mecanizado. Además, el bruñido se puede realizar a velocidades elevadas, minimizando tiempos de proceso.
d) Propiedades mecánicas
Una de las principales ventajas respecto de otras técnicas de acabado superficial es que el bruñido mejora las propiedades mecánicas de los componentes. De esta forma, el proceso introduce tensiones residuales de compresión, aumenta la dureza superficial y en general mejora la integridad superficial del componente, consiguiendo de esta forma un aumento de la vida a fatiga y un aumento de la resistencia a desgaste y corrosión. A diferencia de otros tratamientos mecánicos que mejoran las propiedades de los componentes, el bruñido no empeora la calidad superficial y no genera elevadas temperaturas durante su aplicación.
e) Vida de herramienta
Las herramientas de bruñido pueden ser de metal duro, cerámica o incluso diamante. Se trata de materiales de elevada dureza y que debido a la naturaleza del proceso no tienden a sufrir desgastes excesivos.
f) Facilidad de programación y uso
Tanto cuando se aplica el proceso a pieza de revolución como a superficies complejas, la programación de las trayectorias se realiza igual que un proceso de mecanizado de acabado. Además, en herramientas hidrostáticas, la cabeza de bruñido tiene un movimiento libre de varios milímetros que favorece la absorción de pequeños defectos superficiales y facilita la programación. El proceso necesita poca intervención del operario, minimizando así los posibles errores humanos.
g) Bajos requisitos de par y potencia
Las máquinas necesarias para la aplicación del bruñido no necesitan grandes requisitos de par y potencia. Las fuerzas generadas durante el proceso son normalmente inferiores a las fuerzas generadas en un proceso de mecanizado. Por este motivo se puede aplicar el proceso en la misma máquina donde se mecaniza, sin necesidad de acoplamientos extremadamente rígidos o máquinas de grandes prestaciones. Recientemente se han publicado trabajos de aplicación del bruñido utilizando robots serie.
h) No generación de desperdicios
Es un proceso ecológicamente más limpio en comparación con otros similares de acabado, pues no se generan desperdicios al no haber arranque de viruta. También permite prescindir en determinados casos de tratamientos térmicos y/o termoquímicos, además de disminuir también el nivel de ruido, por lo que permite a los operarios mejores condiciones de trabajo y una disminución de la contaminación del medio ambiente.
2.3. Problemas y limitaciones
La mayor limitación del proceso es geométrica. Al igual que cualquier otro proceso de mecanizado, la geometría de la herramienta limita la geometría final de la pieza a fabricar. En el caso del bruñido la restricción está marcada principalmente por el radio de la bola o rodillo de la herramienta. Existen diferentes configuraciones y tamaños de herramientas de bruñido en el mercado, las cuales posibilitan cubrir un amplio rango de aplicaciones. Siempre que sea posible se recomienda trabajar con el eje de la herramienta en dirección normal a la superficie.
Un problema grave que se puede dar en la aplicación de esta técnica, es la existencia de poros, intersticios y demás fracturas justo debajo de la superficie mecanizada, como en el caso de algunas fundiciones. Al aplicar una presión puntual muy elevada en la zona dañada, internamente se puede producir una rotura o agrietamiento de la superficie acabada. Dado que se trata de pieza acabada, este tipo de problema es el más grave que se puede presentar.
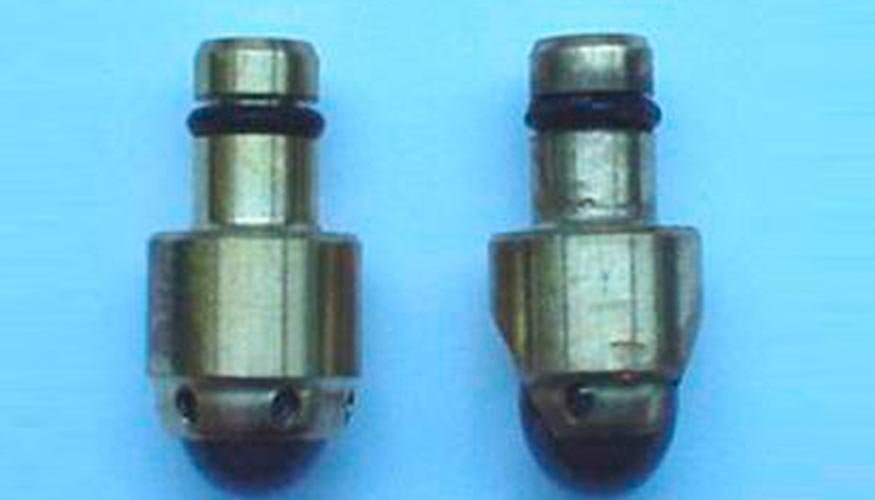
3. El análisis de la huella
El grado de acabado superficial se cuantifica en base al análisis del perfil geométrico de la superficie. Normalmente se trata de un perfil plano de la superficie, obtenido mediante el corte con un plano perpendicular a la superficie teórica y en la dirección de mayor desviación entre la superficie real y la teórica. La información recogida en el perfil filtrado de la superficie sirve para evaluar los diferentes parámetros de rugosidad, todos ellos recogidos en la norma ISO 4287. Los parámetros más empleados para caracterizar la textura superficial son Ra y Rz. La rugosidad media (Ra) se define como la media aritmética de los valores absolutos de las ordenadas del perfil de rugosidad. La altura de perfil máxima en una longitud de muestreo (Rzi), se define como la máxima distancia pico-valle dentro de la longitud de muestreo. Considerando las alturas máximas en las distintas longitudes de muestreo del perfil, se obtiene la altura media de perfil (Rz), que se define como la media aritmética de alturas máximas Rzi de las distintas longitudes de muestreo.
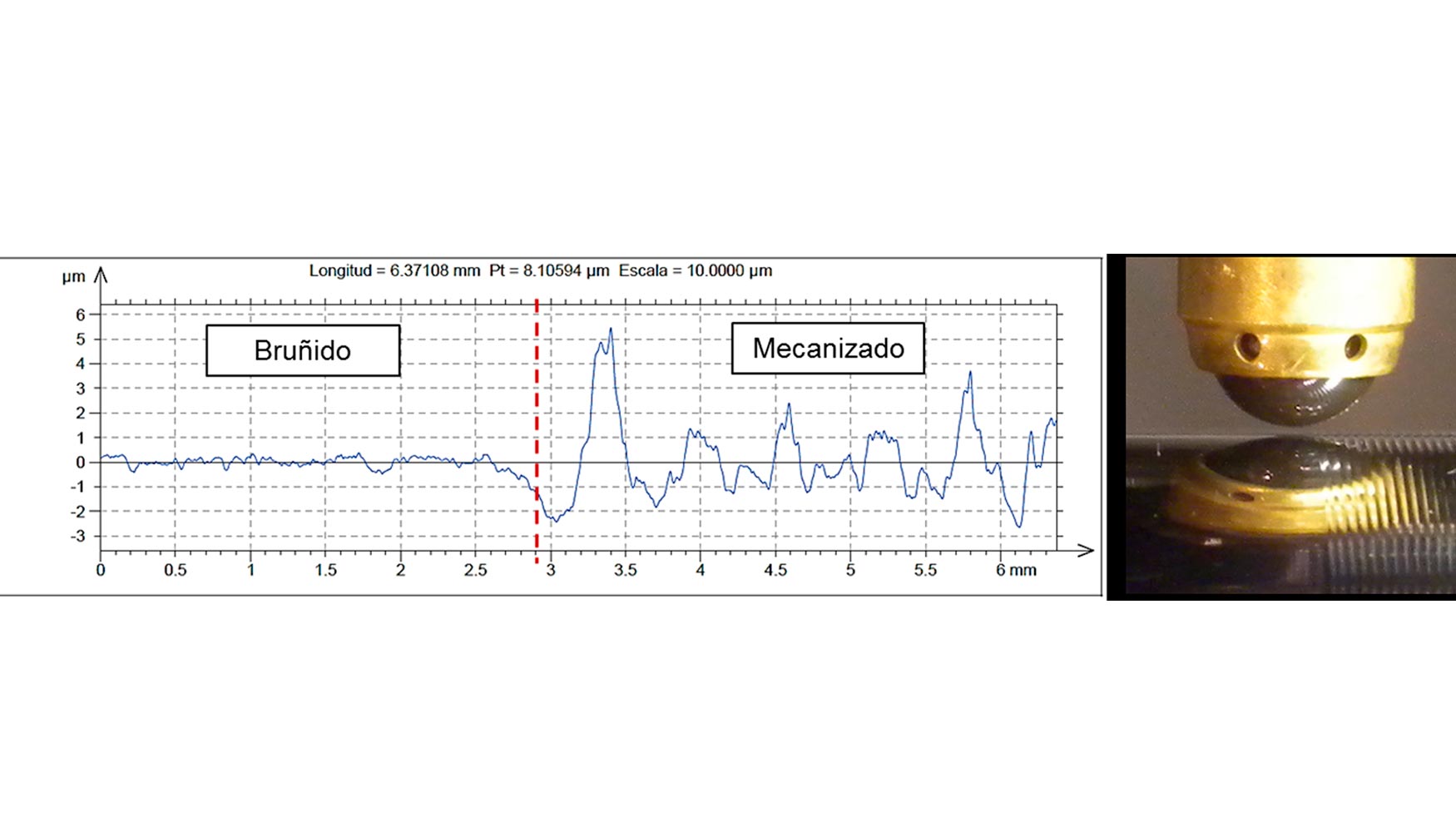
En los últimos años y debido en gran medida a los avances generados en microscopia óptica que permiten reducir notablemente los tiempos de medida, se tiende a capturar el perfil completo en 3D de la superficie y analizar directamente los parámetros superficiales de acuerdo a la norma ISO 25178-2. Esta representación tridimensional de la superficie permite analizar con detalle aspectos superficiales complicados de representar en 2D. En la figura se muestra un ejemplo de topografía tridimensional de una superficie mecanizada donde en el cuarto superior izquierdo se le ha aplicado una operación de bruñido a elevada presión, muy por encima de la presión óptima para ese material. Se aprecia la deformación producida así como la prominencia generada en la frontera entre la zona bruñida y la zona mecanizada.
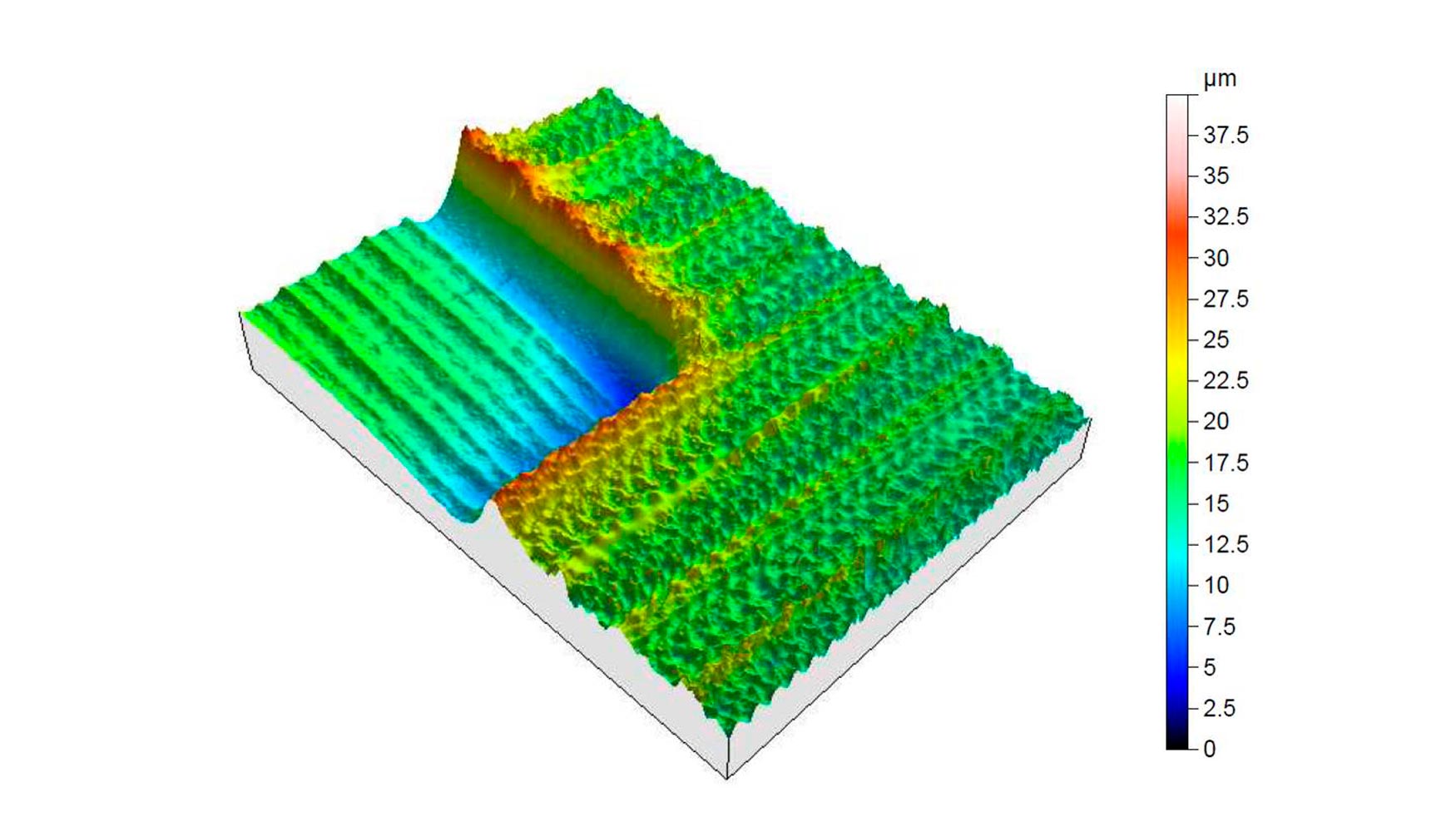
4. Casos de éxito en el acabado de superficies mecanizadas
A continuación se presentan a modo de ejemplo algunos de los resultados en ensayos demostrativos y casos de éxito obtenidos por el Grupo de Fabricación de la Escuela de Ingenieros de Bilbao. En todos los casos se ha empleado un sistema de bruñido hidrostático con bola de la marca Ecoroll.
4.1. Pruebas puntuales en piezas test
Se realizaron ensayos en un acero aleado (AISI P20) con dureza 290-335 HB (31-37 HRC, 980-1130 MPa). Este acero es muy utilizado en moldes de inyección de aluminio. Se realizaron estudios con diferentes presiones de bruñido y diferentes superficies iniciales. El bruñido se realizó siempre con un paso de 0,1 mm y un avance de 15 m/min.
|
Superficie mecanizada, paso radial |
||||
Presión de Bruñido |
Parámetros de rugosidad mm |
ae=0,2mm |
ae=0,3mm |
ae=0,4mm |
ae=0,6mm |
Antes del bruñido |
Ra |
1,04 |
1,65 |
1,83 |
2,43 |
Rz |
8,38 |
12,05 |
16,42 |
14,44 |
|
10 MPa |
Ra |
0,17 |
0,16 |
0,12 |
0,27 |
Rz |
2,68 |
1,64 |
1,45 |
1,9 |
|
15 MPa |
Ra |
0,11 |
0,11 |
0,12 |
0,17 |
Rz |
1,58 |
1,32 |
1,26 |
1,12 |
|
20 MPa |
Ra |
0,13 |
0,07 |
0,10 |
0,13 |
Rz |
2,33 |
1,15 |
0,96 |
1,008 |
A la vista de los resultados de la tabla la primera conclusión es que a mayor presión de bruñido, el acabado final es mejor. Asimismo se ha observado que no es necesario copiar la superficie mecanizada con pasos muy pequeños para lograr la misma calidad después del bruñido. De este modo se puede ahorrar tiempo en los copiados para después pulir con el bruñidor de punta esférica.
Como se puede ver en las siguientes figuras se observan las topografías antes y después del bruñido. Se observa que en el caso del mecanizado la topografía presenta el típico aspecto de valles y picos del mecanizado de la bola y después del bruñido se observa que esas crestas han sido aplastadas, mejorando así la calidad superficial de la pieza.
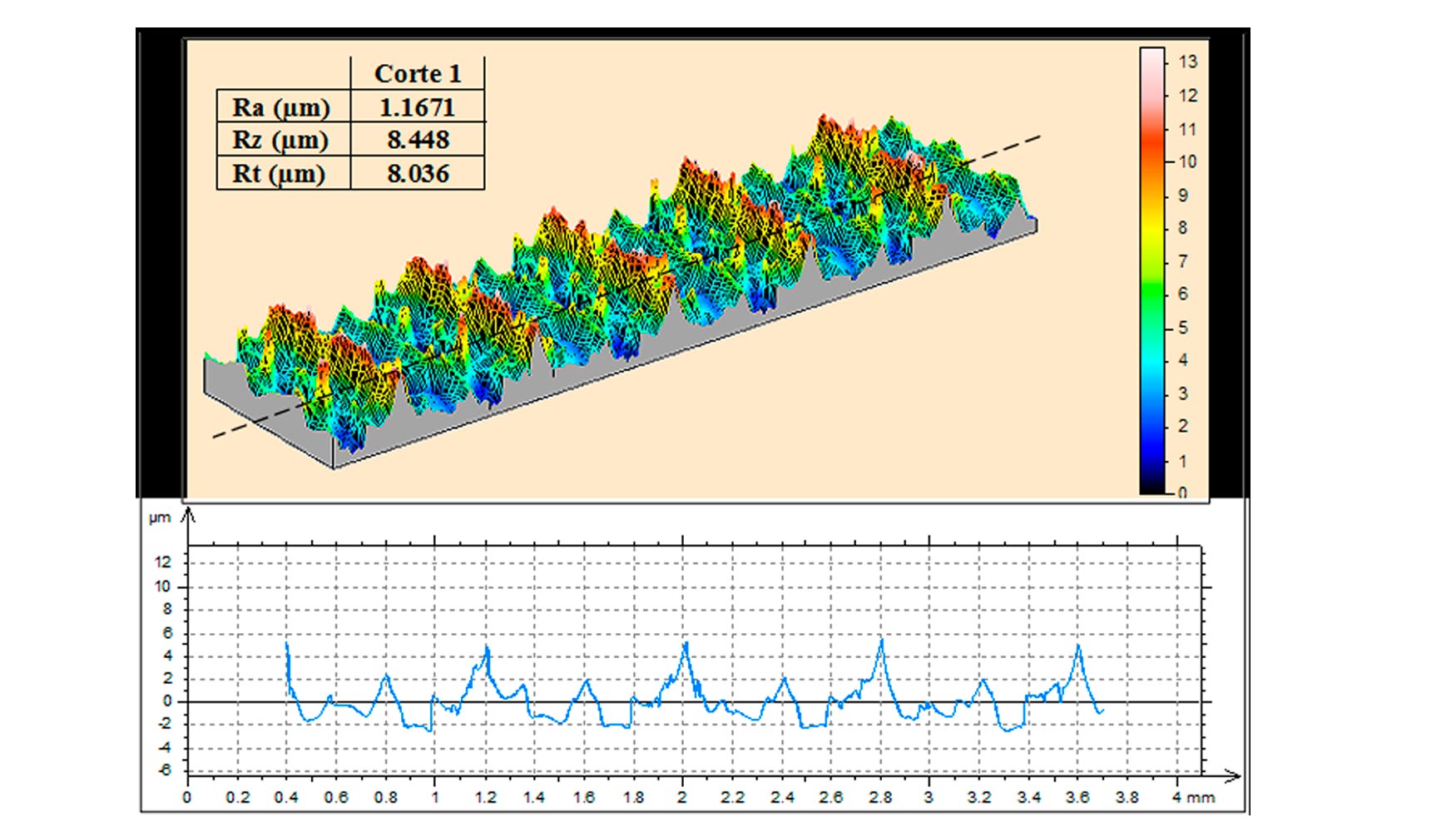

Además, las piezas han sido cortadas y analizadas en un microscopio para su inspección metalúrgica y medición de la dureza superficial. Se observa que la penetración de la capa aplastada puede llegar a ser 14 µm para la presión máxima. Este efecto es debido al trabajo en frío que realiza la bola sobre la superficie, alterando la orientación de las fibras y comprimiéndolas en la superficie. Además, las tensiones son de compresión por lo que, desde el punto de vista de vida a fatiga, el material después del bruñido se comportará mejor.
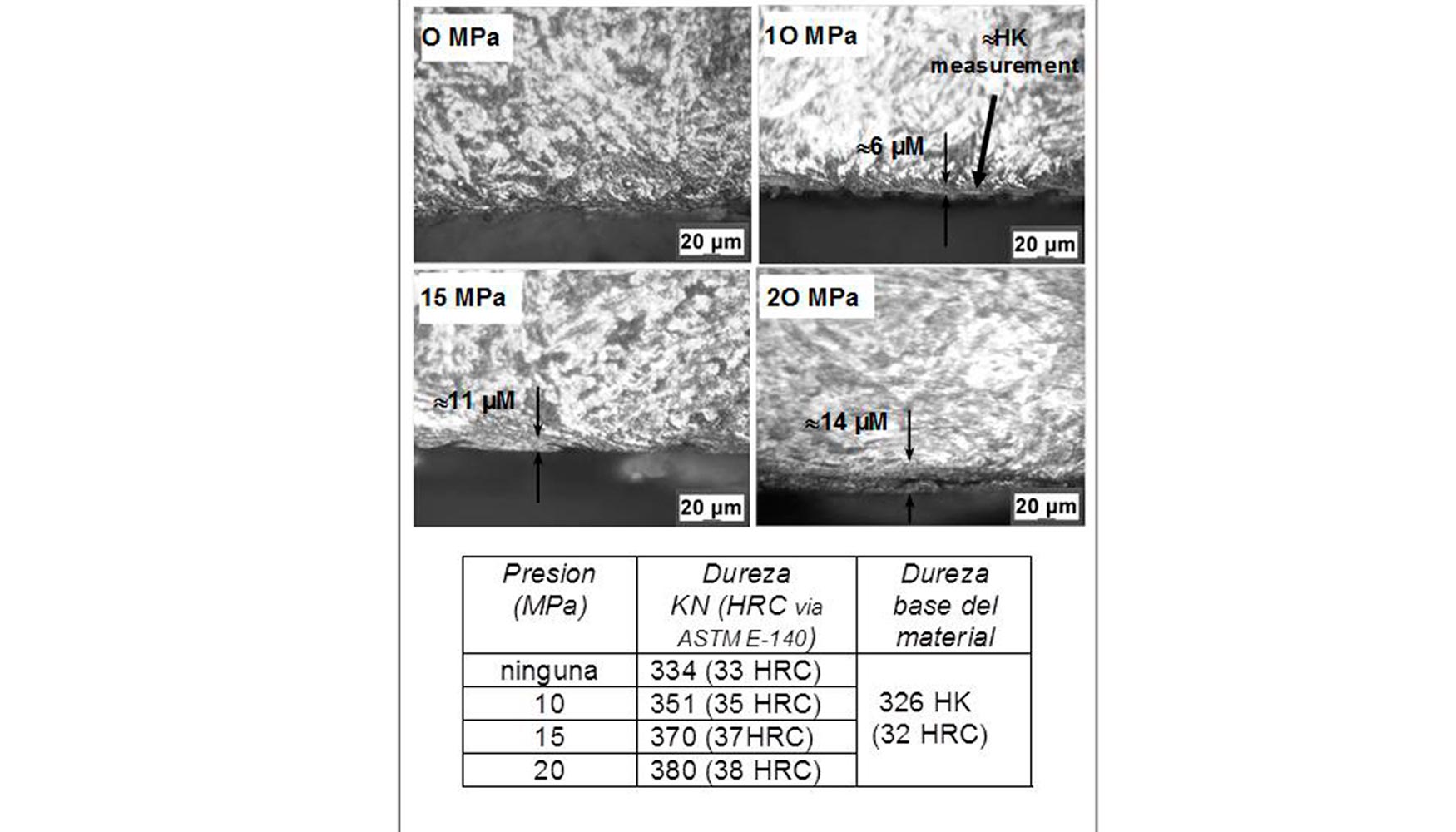
4.2. Acabado de un molde de inyección de aluminio
Tras el fresado de las superficies se ha procedido a bruñir las 4 secciones idénticas del molde. La velocidad de bruñido fue en todos los casos 15 m/min, utilizando diferentes pasos transversales de bruñido, ab de valor 0,05, 0,1 y 0,2 mm, y en dos direcciones de aplicación, esto es, perpendicular a la dirección de fresado y longitudinal en la misma dirección de fresado.
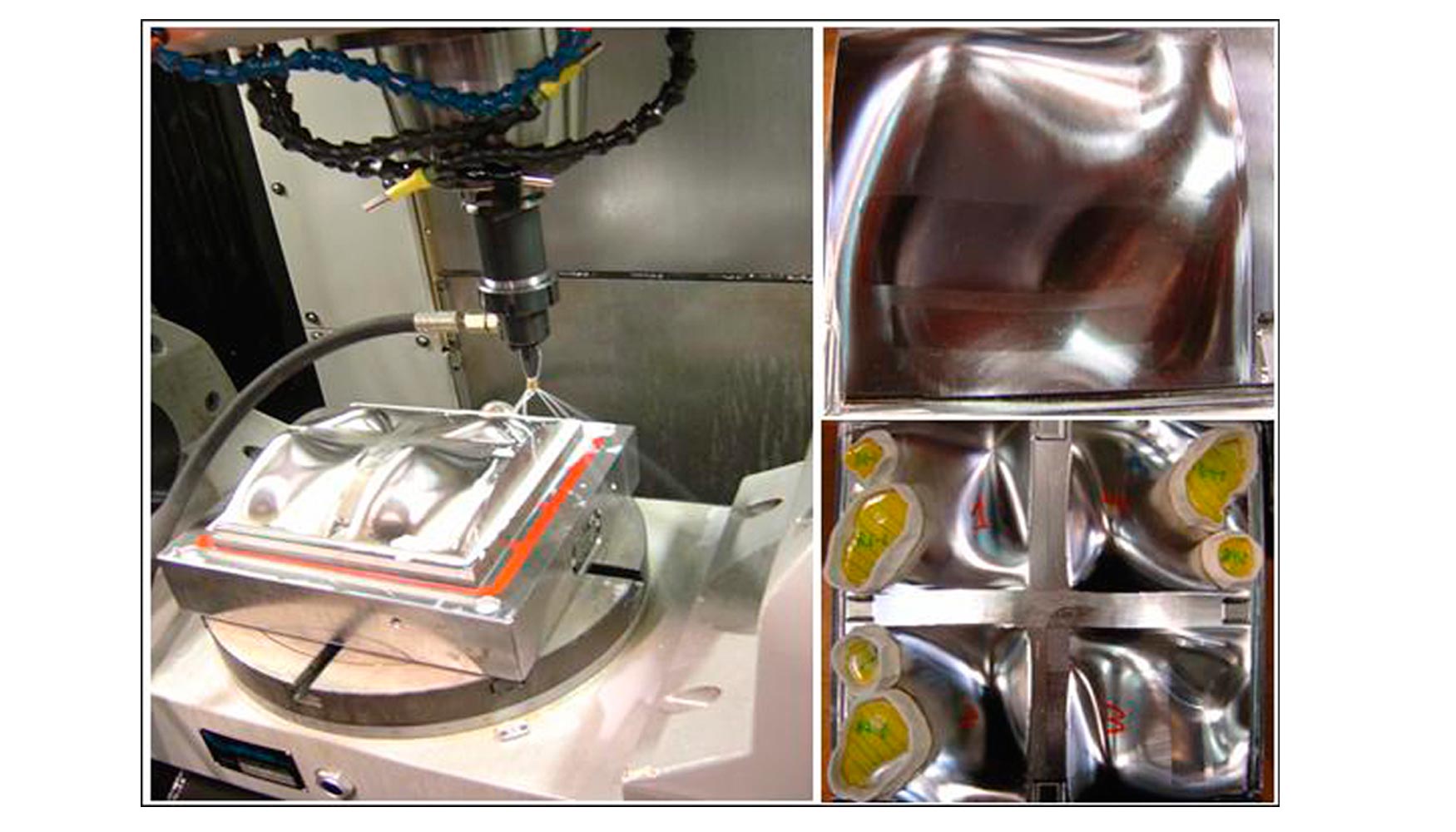
Se ha comprobado que la dureza superficial ha subido de los 52 HRC iniciales a 59 HRC, lo que es un efecto positivo adicional para el funcionamiento del utillaje que trabaja en ciclos de compresión, pues aumenta su resistencia a la fatiga.
Asimismo se comprueba que a peor calidad de la superficie inicial mecanizada el bruñido final también es de menor calidad. Este efecto es debido a que con pasos grandes de mecanizado las crestas resultantes son demasiado grandes para poder ser aplastadas por la bola del bruñidor. De esta manera hay que buscar un compromiso para el copiado para que la calidad final del bruñido sea la óptima. En nuestro caso un paso de mecanizado de 0,45 mm para la fresa de bola de 8 mm se ha mostrado aceptable para poder aplicar después el bruñido con éxito.
Los resultados de rugosidad se presentan en la siguiente tabla:
|
Bruñido perpendicular al fresado |
Bruñido en dirección al fresado |
||||
Pieza test |
Rugosidad (mm) |
Tras el fresado |
ab= 0,05mm |
ab= 0,1mm |
ab= 0,2mm |
ab=0,1mm |
Pieza 1 ae=1mm |
Ra |
2,78 |
1,18 |
1,24 |
1,45 |
1,16 |
Rz |
12,17 |
3,90 |
4,15 |
4,45 |
4,59 |
|
Pieza 2 ae =0,9mm |
Ra |
1,97 |
1,06 |
0,68 |
1,14 |
1,25 |
Rz |
7,31 |
3,74 |
2,96 |
3,93 |
4,27 |
|
Pieza 3 ae =0,45mm |
Ra |
1,72 |
0,20 |
0,28 |
0,30 |
0,14 |
Rz |
7,19 |
1,19 |
1,27 |
1,47 |
0,85 |
|
Pieza 4 ae =0,4mm |
Ra |
1,46 |
0,18 |
0,20 |
0,28 |
0,23 |
Rz |
6,29 |
1,26 |
1,28 |
1,47 |
1,14 |
4.3. Acabado de troqueles de estampación
Esta pieza es una pequeña parte de un gran troquel, compuesto por cuatro materiales, siendo su material base la fundición GGG70 (ASTM 100-70-03) a 280HBN. La parte marcada como A en la figura se ha templado a 60-62 HRC. Los dos insertos B son de acero templado DIN 1.2379 (AISI tipo D3) a 64HRC. La ranura marcada como C es Stellite Alloy 2 (28 HRC) depositado como un material de recargue, es decir, aquel que se añade para recuperar una forma mecanizada previamente con error o por necesidades de la definición del troquel en la fase final de pruebas. El problema que representa es la convivencia de cuatro niveles de dureza en una misma operación.
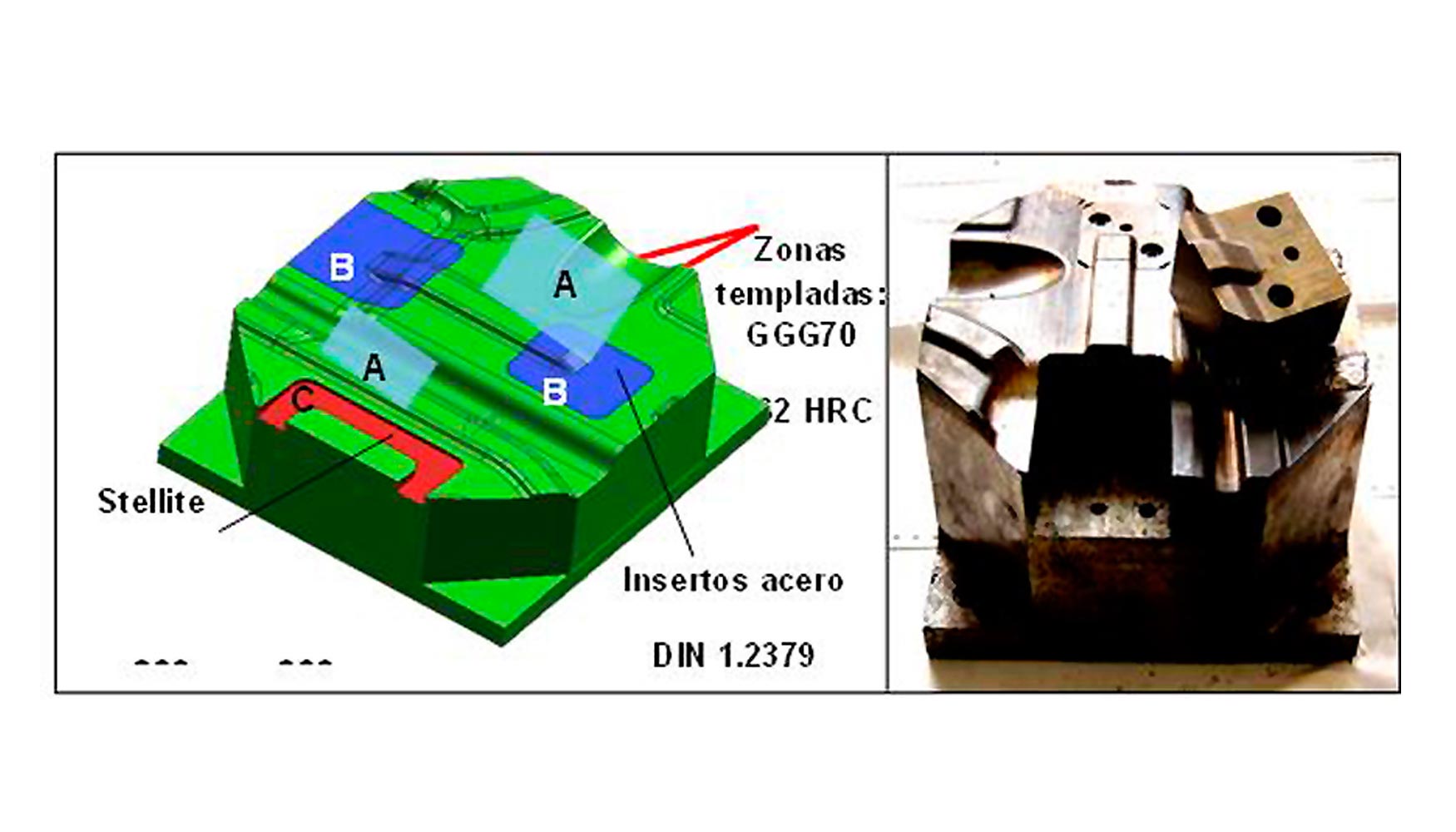
Los resultados obtenidos en los bruñidos se presentan en la siguiente tabla:
Zona |
Rugosidad tras el fresado (mm) |
Parámetros de BB |
Rugosidad tras el BB |
|||||
Ra |
Rt |
Rz |
dirección |
ab |
Ra |
Rt |
Rz |
|
A Fundición templada |
1,60 |
8,56 |
8,56 |
perpendicular |
0,1 mm |
1,23 |
6,97 |
5,83 |
45º |
0,39 |
5,12 |
3,71 |
|||||
B Insertos templados |
1,22 |
5,37 |
5,12 |
perpendicular |
0,1 mm |
1,08 |
5,79 |
5,396 |
45º |
0,29 |
2,10 |
1,64 |
|||||
C Zona recargada |
0,51 |
2,51 |
2,48 |
45º |
0,1 mm |
0,13 |
1,45 |
0,82 |
Fundición base |
1,45 |
8,25 |
8,25 |
45º |
0,1 mm |
0,27 |
4,38 |
2,79 |
perpendicular |
0,48 |
5,52 |
4,01 |
La principal conclusión es que en la zona blanda C y en la zona de fundición no templada, la rugosidad media cae de 0,51 a 0,13 µm y de 1,45 a 0,27 µm Ra respectivamente. Sin embargo en las zonas endurecidas, A y B (a más 60 HRC), el bruñido produce un efecto moderado, siendo muy sensible a la dirección de bruñido. Con un equipo de mayor presión como los disponibles comercialmente (los hay hasta 50 MPa), se hubieran obtenido mejores resultados. Respecto al cambio de dureza superficial, en la fundición base se pasa de 280 a 366 HB (de 29 a 39 HRC), en la fundición templada (zona A) de 62 a 65 HRC, en los insertos (zona B) de 63 a 66 HRC, y en la zona recargada (zona C) de 28 a 35 HRC.
4.4. Aplicación real en un punzonador
En este caso la pieza es una fundición GG25 mecanizada con una bola de 20 mm de diámetro con un paso radial 0,35 mm. Los parámetros de bruñido han sido los siguientes: Velocidad de bruñido 15 m/min, paso de bruñido 0,175 mm y la máxima presión de bruñido. La dirección de bruñido ha sido paralela a la dirección de acabado (las direcciones lógicas dado que la pieza era mucho más larga que ancha).
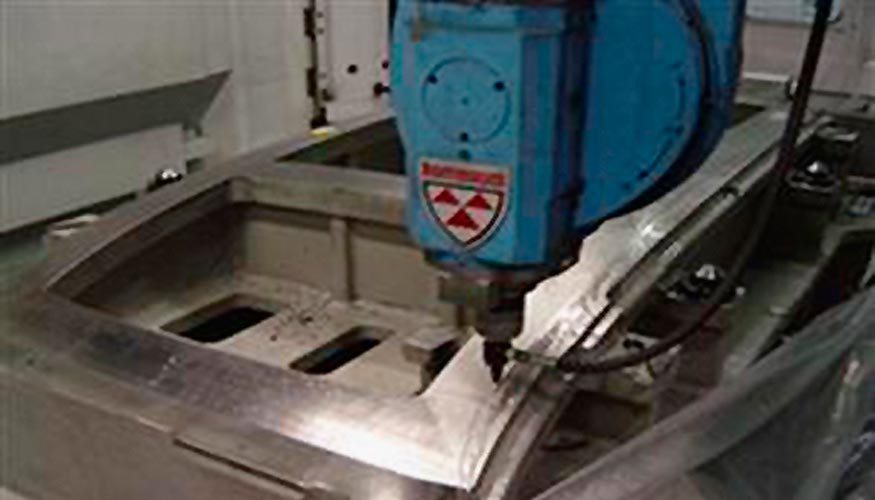
Se observó que el proceso de bruñido no ‘tapa’ posibles errores anteriores de mecanizado. Por lo tanto, para una correcta aplicación del bruñido con bola, la pieza tiene que estar copiada sin marcas ni grandes defectos superficiales como ondulaciones. A modo de ilustración se presenta en la figura los resultados de algunas mediciones de las probetas extraídas:
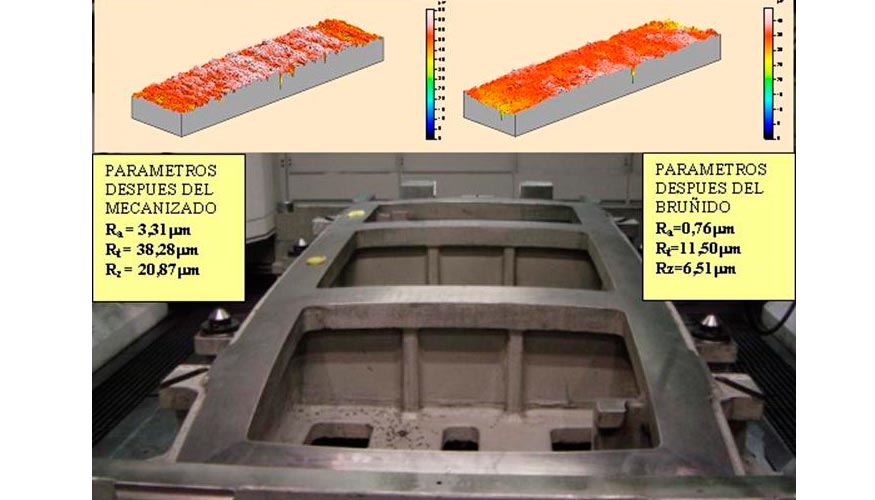
4.5. Aplicación en pieza test de matricería de elevada dureza
En este caso se ha utilizado una estrategia de 3+2 ejes para el bruñido de un molde previamente mecanizado de acero templado DIN 1.2379 (AISI type D3) de elevada dureza (64 HRC). Se trata de una pieza de matricería diseñada y fabricada años atrás como pieza test para estudiar el mecanizado a alta velocidad en aceros de elevada dureza. La geometría de la pieza se diseñó de forma que representase la gran variedad de posibles formas que se pueden dar en la fabricación de moldes y matrices. En este caso, el objetivo es aplicar el bruñido por parches en un material templado de elevada dureza y con diferentes dificultades geométricas de cara a estudiar la mejora de la calidad superficial después del proceso.
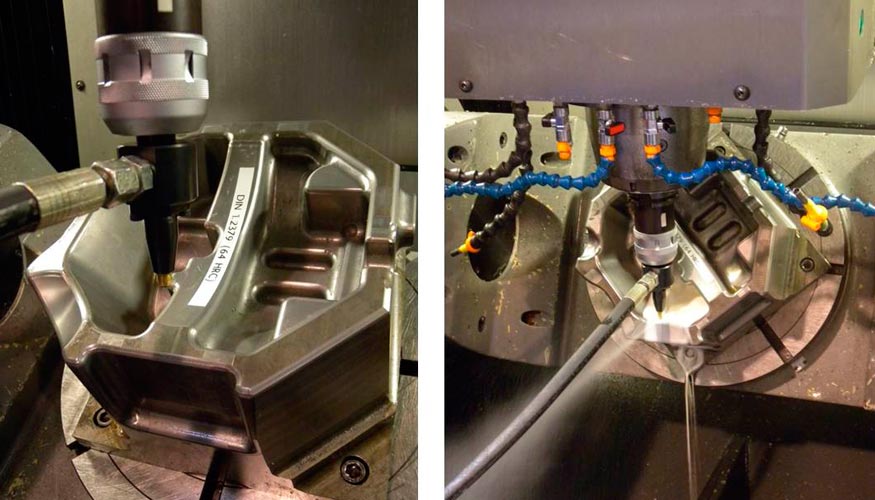
Se han bruñido varias zonas con diferente geometría. La siguiente tabla muestra los valores de rugosidad obtenidos en pruebas realizadas a diferentes presiones. Estas pruebas se han llevado a cabo para determinar cuál es la presión óptima de bruñido. En este caso, debido a la elevada dureza del material, la presión con la cual se consiguen los mejores resultados es 40 MPa, la máxima presión que es capaz de suministrar la bomba. Los resultados muestran que la mejora de los parámetros de rugosidad es aproximadamente de un 50%.
|
Fresado |
Bruñido |
|||
|
10 [MPa] |
20 [MPa] |
30 [MPa] |
40 [MPa] |
|
Ra [µm] |
0,765 |
0,63 |
0,47 |
0,43 |
0,43 |
Rz [µm] |
7,84 |
3,58 |
2,59 |
2,61 |
2,36 |
En conclusión, el bruñido con bola y accionamiento hidrostático es una opción real, madura en tecnología y rápida para su aplicación en moldes y matrices. Su grado de desarrollo ha sido analizado y mejorado por varios proyectos llevados a cabo los últimos años. De forma amigable podemos decir, “el que no bruñe es porque no quiere”.
Pulido láser, acabado de moldes y matrices
El pulido láser se plantea como una alternativa para la automatización de las operaciones de pulido. El proceso de pulido láser se basa en la fusión controlada de una capa superficial de material, de modo que el material fundido rellena los huecos de las irregularidades topográficas dando lugar a una superficie más homogénea. Se trata de un proceso que lleva más de 25 años siendo aplicado con éxito en el pulido de superficies de diamante depositado químicamente (CVD), en el acabado de lentes ópticas e incluso en la reducción de la rugosidad superficial en obleas de silicio, sin embargo, se trata de una tecnología poco extendida en la fabricación de componentes metálicos. Los pocos trabajos existentes muestran que es posible obtener reducciones de rugosidad de más del 80% en aceros de herramienta como el AISI H13, aceros inoxidables, Titanio o fundiciones como la GG25 o la GGG70L. Dado que el proceso implica la fusión de una capa superficial, para un resultado óptimo, resulta determinante la correcta selección de los parámetros, una densidad de energía por debajo de la necesaria da como resultado una topografía irregular, sin embargo, una densidad energética por encima de la óptima, además de una mayor afectación térmica, provoca la generación de un baño fundido de material y la aparición de ondulaciones en la superficie, dando lugar al régimen conocido como Surface Over Melt (SOM).
A nivel comercial existen pocos desarrollos de máquinas centrados en aplicaciones de pulido láser. Equipos como la serie Laser de GF Machining solutions, o la serie Lasertec Shape de DMG MORI de máquinas híbridas de mecanizado y texturizado láser, están más orientadas a aplicaciones puramente centradas en texturizado, si bien, también tienen la capacidad de reducir la rugosidad superficial trabajando en condiciones de pulido láser, ya bien sea en régimen pulsado o en régimen continuo. La limitación de las mismas para operaciones de pulido suele estar asociada a una muy baja productividad, por debajo de los 10 cm2/min y una potencia máxima por debajo de los 100 W en continuo. Por otro lado, el prototipo de máquina desarrollada por la empresa Arnold en colaboración con el ILT como resultado del proyecto europeo Alpine es, sin duda, la más orientada a operaciones de pulido láser. A diferencia de las soluciones híbridas o de texturizado, ésta dispone de un láser de mayor potencia (750 o 1.000 W) y una cámara de atmósfera controlada que permite procesar materiales como el titanio o las fundiciones de alto contenido en carbono que precisan de una descarburización superficial para lograr un resultado adecuado con una productividad cercana a los 60 cm2/min.
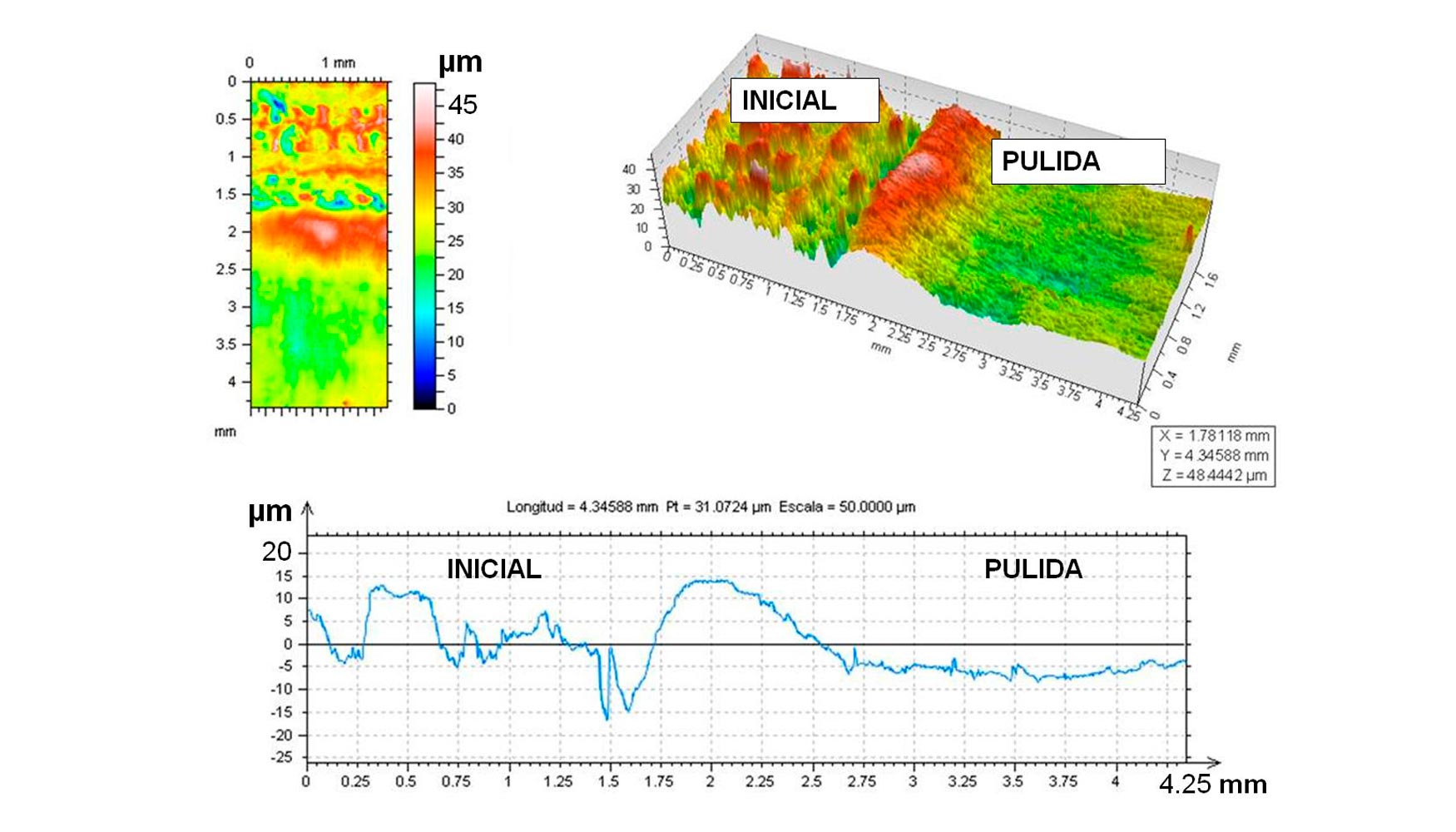
El impacto del bruñido en los últimos 4 años. Del MRL 5 AL 7, ejemplo de desarrollo
Sectores de gran importancia en Europa como el de automoción, el aeronáutico y el eólico están impulsando notablemente el I+D+i, focalizando gran parte de los recursos en procesos de fabricación y producción por mecanizado. En este contexto, la fabricación avanzada se perfila como concepto clave para las grandes empresas y grupos de investigación y se entiende como la generación y aplicación de conocimiento, experiencia y tecnología de vanguardia para la creación de productos, procesos de producción y servicios de alto valor añadido. En esta línea, el bruñido junto con otros tratamientos superficiales mecánicos se antojan imprescindibles para el acabado de componentes críticos con requisitos muy restrictivos en cuanto a integridad superficial. Por este motivo, la investigación básica pero orientada en torno a tratamientos superficiales y mejora de la integridad superficial es una línea clara sobre la que trabajar para sentar las bases de la investigación aplicada en este campo.
Claramente, los esfuerzos tienen que dirigirse hacia la idea de complementar los intereses científicos con la realidad industrial de nuestro entorno, o lo que es lo mismo, establecer Manufacturing Readiness Level MRL 7-8 como objetivos prioritarios. En los últimos años, los avances realizados en relación a operaciones de bruñido han pasado de centrarse exclusivamente en MRLs bajos para posicionarse en un contexto industrial de mayor relevancia, alcanzando en algunos casos MRL 6-7. De esta forma, se ha conseguido transferir conocimiento a procesos industriales reales, siempre desde una base científica consolidada. Por otra parte no hay duda de que la escala MRL se va a imponer como forma de definir el estado, madurez y alcance de los proyectos de I+D+i.
En el caso del bruñido, algunos centros y universidades (como la Escuela de Ingenieros de Bilbao) llevan muchos años estudiando los fundamentos científicos del proceso y aprendiendo desde ese punto de vista.
En los últimos años, el Grupo de la Escuela ha colaborado intensamente con la industria del entorno para difundir ese conocimiento y ponerlo a prueba en condiciones industriales reales, como por ejemplo acabando pisadores, punzonadores y troqueles de estampación, o componentes rotativos.