Nuevas tecnologías aplicadas al proceso de acabado de moldes
El presente artículo expone la investigación enmarcada en los proyectos Autopul y Sinde, correspondientes a convocatorias del Ministerio de Ciencia e Innovación del Gobierno de España (Sinide: IPT-020000-2010-34; Autopul: PID-560100-2009-4). El objetivo es desarrollar un sistema inteligente de acabado de piezas y utillajes para sectores del metal y el plástico, en especial automoción y aeronáutico, mediante sistemas de pulido y desbarbado, basados en robótica e inteligencia artificial y aplicable a materiales altamente tecnificados tanto metálicos como composites. Como principal objetivo estratégico se plantea la mejora de la competitividad de empresas de estos sectores y, por extensión, a proveedores de las mismas que se dedican a la fabricación de utillajes, mediante la incorporación de nuevos desarrollos experimentales que permitan optimizar, tecnificar y automatizar los procesos de acabado de piezas y utillajes en los sectores anteriormente mencionados que actualmente se realizan de forma manual.
El desarrollo realizado permite el lijado y pulido de piezas de superficies de forma libre, consiguiendo un acabado de alta calidad, teniendo un mayor control del proceso, controlando la cantidad de material eliminado, dando sentido a lo que se puede llamar ‘Conformal grinding / Conformal polishing’.
Para ello se integran tecnologías de alto nivel como sistemas CAM en un robot antropomórfico de 6 ejes, consiguiendo así un sistema altamente flexible, y adaptable y que además reduce el tiempo y coste del proceso.
Metodología
La investigación tiene unos puntos de desarrollo básicos comunes como son:
- Desarrollo de herramienta para pulido automatizado de superficies de forma libre.
- Adaptación de metodología CAM 5 ejes al proceso de pulido.[1]
- Automatización del sistema de pulido mediante robot antropomórfico.
A partir de estos puntos comunes la investigación se disgrega en 2 líneas principales.
- Desarrollo de la metodología que permita la reducción de la rugosidad superficial, y por tanto la mejora de la calidad final de la pieza.
- Caracterización de la metodología de pulido que permita controlar la cantidad de material que se quita, y por tanto permita desarrollar el concepto de ‘conformal polishing’.
Infraestructura
Durante esta investigación, diferentes configuraciones de herramienta de acabado fueron diseñadas y testadas con el objetivo de implementar el proceso automático de acabado. Sin embargo, el objetivo final de conseguir el acabado de superficies de forma libre condicionó el desarrollo. Estudios precedentes han desarrollado a tal efecto, herramientas rígidas controladas por un sensor de fuerza [2], obteniendo buenos resultados en superficies planas [3], sin embargo en el caso de superficies libres, las variaciones de curvatura que presentan, hacen que no haya una relación lineal entre la fuerza y la presión ejercida. Por ello la filosofía de la herramienta desarrollada basa su concepto en el control de presión mediante el control de la interferencia entre herramienta y superficie.
La configuración final se compone de un sistema multicapa que integra un elemento rígido, una capa reguladora de la presión, y una capa abrasiva. [4]
![Figura 1. Herramienta Desarrollada. [A] Capa rígida [B] Capa reguladora de presión [C] Capa Abrasiva Figura 1. Herramienta Desarrollada. [A] Capa rígida [B] Capa reguladora de presión [C] Capa Abrasiva](https://img.interempresas.net/fotos/908099.jpeg)
Figura 1. Herramienta Desarrollada. [A] Capa rígida [B] Capa reguladora de presión [C] Capa Abrasiva.
Para la automatización del sistema, en un momento inicial se realizó en una fresadora, sin embargo, el alcance del proyecto que implica el pulido de superficies de forma libre, conlleva que es necesario un sistema que permita la orientación del vector de la herramienta en función de la normal de la superficie a pulir.
Por esta razón, la máquina finalmente utilizada para la ejecución de este proyecto es un robot antropomórfico de 6 ejes, ya que dicho sistema permite la orientación de la herramienta en cualquier dirección dentro de las limitaciones del campo de trabajo.
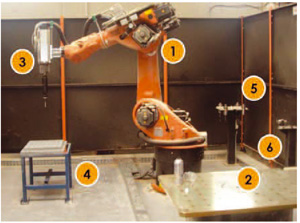
Figura 2. Celda de pulido automático [1] Robot [2] Eje externo (mesa giratoria) [3] Motor eléctrico [4] Intercambiador de herramientas de pulido [5] Intercambiador de portaherramientas [6] Sonda de medición de herramientas
La programación del robot se realiza mediante un sistema offline que permite la comunicación con un sistema CAM.
En el entorno CAM se desarrolla la metodología para el pulido automático de tal forma que se desarrollan bases de datos de herramientas, macros y rutinas de parámetros que han sido optimizados mediante una exhaustiva investigación basada en ensayos sobre probetas de aluminio que posteriormente han sido topografiadas y analizadas mediante un sistema de microscopía confocal.
Rugosidad y calidad de las superficies
Uno de los objetivos del proyecto es la optimización de la metodología de pulido para conseguir superficies de alta calidad, lo cual implica una reducción de la rugosidad de las superficies pulidas.
Se ha realizado la optimización de los parámetros relacionados con el pulido:
- Granulometría de los abrasivos.
- Velocidad de rotación de la herramienta.
- Velocidad de avance de la herramienta.
- Distancia entre pasadas
- Presión sobre la superficie.
Tras este trabajo de ensayos y optimización se describe una secuencia que es capaz de progresivamente, en fases sucesivas, ir reduciendo la rugosidad de la pieza y, por lo tanto, de mejorar su aspecto y calidad superficial.
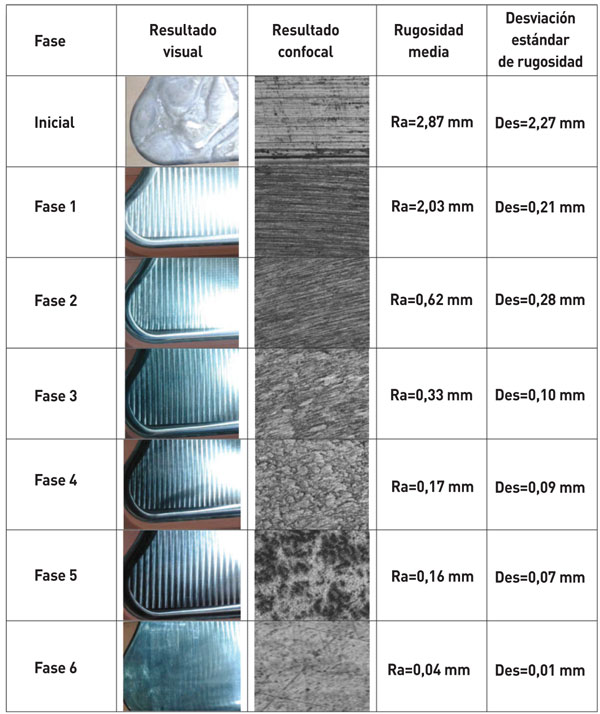
Figura 3. Evolución de parámetros de rugosidad durante la ejecución de la metodología desarrollada.
En la figura anterior se puede observar cómo evoluciona la superficie aplicando las sucesivas secuencias de pulido. Se observa que no solo mejora la rugosidad, sino que la desviación baja de la misma forma, lo que conlleva una homogeneización de la superficie procesada que es otro de los objetivos del proceso de acabado.
‘Conformal Polishing’
Durante el proceso de acabado de piezas de alto nivel, tan importante como la obtención de la rugosidad deseada es conservar la geometría original o teórica de la superficie. En el caso de superficies de forma libre, el proceso de pulido actualmente se sigue realizando de forma manual, con lo que no existe ningún control sobre la cantidad de material que se elimina, y tampoco existe ningún método para evitar la generación de ondulaciones en la superficie. El desarrollo de esta investigación ha conseguido la implementación de un simulador matemático que permite simular la cantidad de material eliminado y el aspecto de la superficie de forma previa a la realización del pulido.
En la metodología desarrollada, el 75% del material se elimina durante la primera fase.
![Figura 4. [A] Huella teórica obtenida con el simulador de pulido. [B] Simulación de superficie en Fase 1 de la metodología desarrollada... Figura 4. [A] Huella teórica obtenida con el simulador de pulido. [B] Simulación de superficie en Fase 1 de la metodología desarrollada...](https://img.interempresas.net/fotos/908102.jpeg)
Figura 4. [A] Huella teórica obtenida con el simulador de pulido. [B] Simulación de superficie en Fase 1 de la metodología desarrollada.
Si contrastamos los datos obtenidos con el simulador de pulido desarrollado con el caso de estudio presentado se observa que la altura cresta-valle en el simulador es de 1,64 mm, mientras que el resultado real es de 1,32 mm. Esto supone que se puede predecir la cantidad de material eliminado, y por tanto la geometría de superficie obtenida con un error inferior al 20%.
Aplicaciones del pulido automático
La metodología desarrollada ha sido aplicada con éxito a diferentes casos de estudio, en concreto a piezas de aluminio para piezas aeronáuticas y de automoción. A continuación se muestran algunas imágenes de los resultados obtenidos.
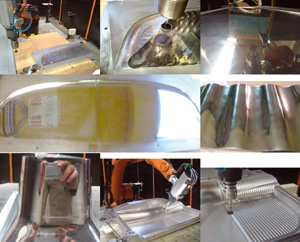
Figura 5. Imágenes del proceso y resultados del pulido automático de superficies de forma libre.
Conclusiones
Como se ha descrito, se ha conseguido realizar el pulido de superficies de forma libre de piezas de alto nivel en aluminio. Se ha desarrollado una metodología que permite por un lado controlar la rugosidad y la calidad de las superficies obtenidas, y de la misma forma prever de antemano la cantidad de material que se va a eliminar durante del proceso en cada zona de la pieza.
Como se ha descrito en el cuerpo del artículo, la metodología se basa en una serie de pasos sucesivos, cuyo resultado es una rugosidad determinada.
En función de los requerimientos de la pieza a procesar, sólo sería necesario aplicar las etapas necesarias para conseguir la rugosidad y por tanto la calidad superficial exigida en cada caso concreto, reduciendo por tanto el tiempo de procesado.
La aplicación del pulido automático con robot según la metodología descrita presenta las siguientes ventajas respecto al pulido manual que actualmente se aplica sobre todo a superficies de forma libre:
- Reducción del tiempo de proceso.
- Repetibilidad del proceso.
- Control de la geometría obtenida
Además la implementación del simulador de pulido desarrollado amplía la aplicabilidad de la tecnología, ya que a medio plazo hace posible la corrección geométrica de piezas defectuosas.
En casos críticos donde la tolerancia geométrica de la pieza es importante el pulido o acabado con la metodología descrita permite la corrección puntual de la geometría mediante un proceso que es capaz de eliminar muy poca cantidad de material, permitiendo así una corrección minuciosa de la geometría obtenida.
Se estima de especial importancia la aplicabilidad de este desarrollo en piezas del sector aeronáutico, concretamente en piezas estructurales, cuya geometría se caracteriza por tener una piel principal nervada en su parte trasera, que genera una serie de sectores, en los cuales el espesor de pieza resultante es especialmente riguroso.
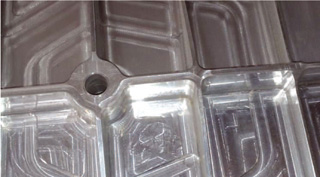
Figura 6. Pieza de aeroestructura. Zona Inferior resultado de proceso de fresado. Zona superior aplicando la Fase 1 descrita.
En estos casos muchas veces el proceso de corrección de los defectos de espesor, marcas de mecanizado u otros errores, puede resultar en ocasiones más largo y costoso que el propio proceso de arranque de viruta.
Así pues la aplicación de los resultados de esta investigación supondría un aumento en la calidad final de la pieza, y una reducción de los costes de proceso, al mismo tiempo que se asegura la homogeneidad y repetibilidad de los resultados.
Referencias
[1] Márquez, J.J.; Pérez, J.M.; Ríos, J.; Vizán, A. Process modelling for robotic polishing. Journal of Materials Processing Technology, 159 (2005), pp. 69-82.
[2] Nagata, F.; Kusumoto, Y.; Fujimoto, Y.; Watanabe, K. Robotic sanding system for new designed furniture with free-formed surface. Robotics and Computer-Integrated Manufacturing, 23 (2007), pp. 271-279.
[3] Li, Y.; Gracewski, S.M.; Funkebusch, P.D., Ruckman, J. Analysis of chatter in contour grinding of optical materials. International Journal of Machine Tools & Manufacture, 42 (2002), pp. 1095-1103.
[4] Dieste, J.A.; Fernández, A.; Roba, D. Rapid Finishing of Free Form Surfaces Using Milling Machine and Spherical Robot, Advanced Science Letters 19 (2013), pp. 849-852.