El micromecanizado tendrá una expansión máxima para fabricación de microcomponentes
Mecanizado por electroerosión
La tecnología láser en procesos de microfabricación se encuentra en una posición intermedia, útil como herramienta en procesos como corte, soldadura, taladrado, marcado, etc. Pero hay trabajos de micromecanizado que exigen una precisión que el láser excímer, o Nd-Yag, no pueden dar.
El mecanizado por descarga eléctrica
El proceso de la electroerosión consiste en la generación de un arco eléctrico entre una pieza metálica y un electrodo de grafito. Separando a ambos hay un medio dieléctrico, eléctricamente aislante. La intensidad del campo eléctrico es mayor que la resistencia del dieléctrico, al menos en algún punto, y la corriente rompe, permitiendo el flujo eléctrico entre los electrodos. Es el mismo efecto que la ruptura de un condensador eléctrico. La chispa calentará la superficie de la pieza hasta una temperatura en que volatiliza el metal, arrancará partículas de la pieza, y logrará finalmente reproducir en la pieza las formas del electrodo. La geometría típica es tridimensional formada por varios ángulos. Las máquina de electroerosión ofrece variedad de ciclos: vertical, orbital, vectorial, direccional, helicoidal, cónico, rotacional, etc. El mecanismo de arranque de metal es un proceso igual térmico que mecánico, provocado por la presencia de una fuerza eléctrica en la superficie del electrodo, que puede mecánicamente arrancar la viruta y crear un cráter. Este también sufre erosión. Básicamente se trata de una serie de rupturas y restauraciones del líquido dieléctrico entre electrodos siguiendo un modelo, producción de miles de chispas. La profundidad del cráter creado depende de la longitud del pulso, a más longitud la superficie de acabado será más rugosa. El pulso muy corto dará un acabado más fino. Durante el intervalo entre pulsos se renueva el líquido dieléctrico, a mayor intervalo más líquido se renueva en microsegundos, y más partículas de metal serán lanzadas fuera; con ello se aleja el peligro del cortocircuito, causado por las partículas.
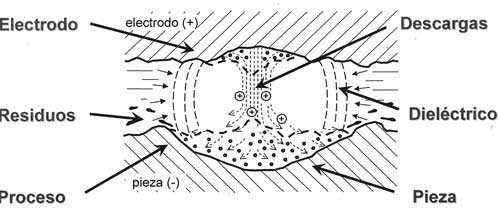
La intensidad de la corriente de la chispa depende de la capacitancia del condensador en el circuito RC, una intensidad, que depende de la carga acumulada en el condensador en un momento dado, y también del voltaje normal, constante, del circuito RC. En vez del generador RC se puede usar un generador de pulso controlado, ahora mejorado con nuevos componentes electrónicos. El generador, basado en un transistor que lo controla, modela el pulso de forma cuasi rectangular y el tiempo entre dos pulsos consecutivos.
En la pieza las descargas producen cráteres microscópicos, de un tamaño que depende del tipo de máquina. Tanto la pieza como el electrodo deben ser materiales conductores, para que pueda establecerse el arco eléctrico para el arranque de metal. Cuando cesa el pulso eléctrico, se inyecta nuevo líquido dieléctrico en el espacio entre electrodos, y las partículas metálicas de la pieza, que han sido arrancadas, son expulsadas, pero sólo parcialmente. Esas partículas pueden cambiar las características dieléctricas del líquido, e incluso producir un cortocircuito. Es un problema no resuelto. La distancia entre ambos electrodos, el espacio de chispa, depende de la máquina usada, es un factor lógicamente central en el proceso. Intolerable que ambos electrodos entren en contacto.
De nuevo se inicia otra descarga eléctrica. Se trata de metales duros, y no hace falta calentarlos para disminuir su dureza, para hacer más fácil el mecanizado. El método también sirve para metales no férreos, como titanio, Hastelloy, Kovar e Inconel y para dar forma a herramientas semicristalinas de diamante. Es posible incrementar su conductividad.
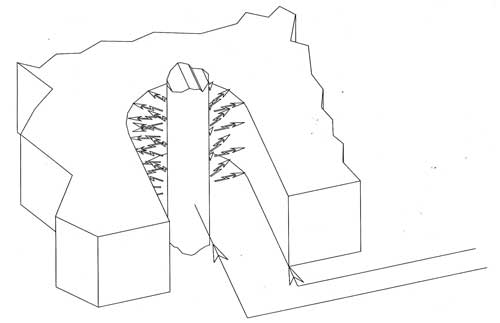
La descarga eléctrica es un proceso lento, que se emplea en geometrías no convencionales de metales duros y frágiles. Básicamente hay dos variantes: El electrodo de forma y el Hilo metálico. El primero logra arrancar 2 cm³/hora, de material, por lo que apareció la nueva variante, mucho más rápida, la del hilo. La investigación comenzó en 1770 con el físico inglés Joseph Priestley, el cual estudió el efecto erosivo de la descarga eléctrica. En 1943 dos científicos rusos, Dr.B.R.Lazarenko y Dr. N.I.Lazarenko adaptaron la descarga eléctrica al mecanizado de metales. Como el método tenía éxito, en 1952 el fabricante Charmilles creó la primera máquina de electroerosión, y fue exhibida en la Expo Europea de Máquina Herramienta en 1955. Debido a que el arranque de metal era lento, en 1969 Agie lanzó la erosión por electrodo de hilo, controlada por ordenador.
Electrodo de forma
Es comúnmente hecho de grafito, pues éste, por tener una elevada temperatura de vaporización, es más resistente al desgaste. Puede ser trabajado con una fresadora con el fin de crear, ya sea un electrodo macho u hembra. Esto significa que el electrodo tendrá la forma opuesta a la forma deseada en la pieza de trabajo. Es útil disponer de dos electrodos-forma, uno para erosión en bruto, y el otro para lograr el acabado final perfecto. El cobre también puede servir como electrodo, aunque su desgaste es más rápido. El electrodo de cobre es ideal para la perforación de hoyos, o agujeros redondos y profundos. El diámetro de estos electrodos no pasa de algunos milímetros y longitudes variadas, y prepara la pieza metálica para la posterior electroerosión por hilo. Se trata de agujeros que el taladro convencional no puede realizar.
Para la electroerosión la pieza y el electrodo se sitúan muy cercanos entre sí, dejando un espacio que oscila entre 0,01 y 0,05mm, por el que circula un líquido dieléctrico, normalmente aceite de baja conductividad, en que está sumergida la pieza. Un generador de corriente continua y pulsante crea un campo eléctrico intenso entre electrodo y pieza, que provoca el paulatino aumento de temperatura, hasta que el dieléctrico se vaporiza. Al desaparecer el aislamiento del dieléctrico salta la chispa, y se incrementa la temperatura, hasta extremos de 20.000 °C, se vaporiza un pequeño material de la pieza y del electrodo; se forma una burbuja que actúa de puente. Al cesar el pulso eléctrico, el puente-burbuja se rompe, y se alejan las partículas-gas del metal arrancado. Ese gas se solidifica al contacto con el dieléctrico, y es finalmente arrastrado. Ese ciclo completo se repite miles de veces por segundo, según la máquina. También se puede cambiar la polaridad electrodo-pieza. La erosión uniforme de la pieza reproduce las formas del electrodo. A medida que el electrodo se desgasta hay que ir acercándolo la pieza, para mantener el hueco constante. Los pequeños cráteres de la herramienta erosionan gradualmente el electrodo.
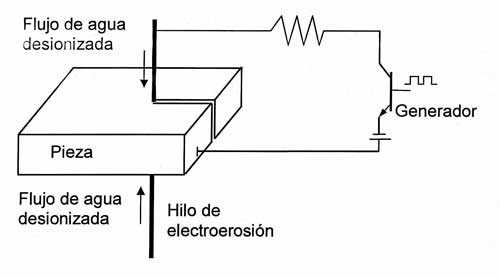
Hay que contrarrestar ese desgaste de la geometría del electrodo: una posibilidad es ir remplazándolo durante la operación, algo fácil si usamos la electroerosión por hilo, empujarlo cuidadosamente hacia abajo. Como es obvio, cuando el desgaste es severo el electrodo es remplazado. Si es de grafito, se corrige el desgaste con un generador digital, controlable al milisegundo, que invierte la polaridad mientras actúa la electroerosión. Es un efecto similar al recubrimiento de la plata, que continuamente deposita partículas de grafito hacia atrás, hacia el electrodo, hasta lograr el desgaste cero.
La erosión de la pieza varía desde nanómetros hasta centenares de micras en superficies rugosas. Para un acabado preciso, ±0,05 mm, son necesarios 2 electrodos, o más, una práctica común, cuando la herramienta reproduce en negativo la forma deseada. La herramienta avanza en dirección única hacia abajo, el eje Z. Cuando utilizamos un solo electrodo de forma simple, hay que moverlo en diversas direcciones, e incluso usar su rotación para moler. El desgaste logrado depende de la polaridad, corriente máxima y voltaje aplicado. La rugosidad superficial (RS) puede variar entre 48 RS (acabado muy rugoso) y 26 RS (acabado casi perfecto). 0 RS es un acabado sin rugosidad, casi imposible de conseguir.
Con el electrodo de forma no se generan fuerzas de corte, como en los procesos de mecanizado, torneado y taladrado. Por ello resulta aplicable a metales frágiles. Se pueden producir agujeros muy inclinados en superficies curvas, sin problemas de deslizamiento; así como de elevada relación: cociente entre la longitud y el diámetro. El pequeño diámetro y gran profundidad no son posibles con un taladro convencional. Las tolerancias que se obtienen son muy ajustadas: desde ±0,025 hasta ±0,127 mm, y se logran complejas configuraciones, antes imposibles. No hace falta un ataque de ácido, para lograr un acabado rugoso. Con el ácido el acabado es perfecto, disminuyen los costes y el tiempo de mecanizado, satisfactorio en la mayoría de ocasiones. Como la geometría de algunas piezas es compleja y el trabajo de corte necesario es difícil de posicionar, se usan artefactos específicos de acero inoxidable con el fin de sujetar la pieza durante el proceso. Se procura que el ciclo de manufactura sea lo más breve posible, el acabado de la pieza tenga la aspereza y calidad deseada y que la precisión en dimensiones y tolerancias geométricas sean las planeadas. Las piezas que hay que trabajar han de estar ordenadas con el fin de que durante la mecanización requieran una atención mínima. Como no hay contacto directo entre herramienta y pieza, se pueden mecanizar metales blandos, sin causar ninguna distorsión. Obviamente la protección y seguridad del operador es importante, pues las chispas pueden saltar fuera del contenedor y el uso de corriente eléctrica de alto voltaje presenta un peligro de electrocución.
No todo son ventajas, pues tiene más resistencia a la fatiga una pieza acabada por arranque de viruta (fresadora, torno, planificadora) que una pieza acabada por penetración eléctrica, electroerosión. La energía consumida es alta.
Electroerosión con hilo
La lentitud del electrodo de forma ha traído el proceso de electrodo por hilo, nacido en los años de la década de los setenta, con una capacidad de arranque de metal de unos 350 cm³/hora. La velocidad depende de muchos factores, como el diámetro del hilo, el voltaje y amperaje aplicados, el grosor y metal de la pieza. El acabado deseado afecta al tiempo del ciclo de manufactura, pues posteriormente será mejorado con pases semirepetitivos de corte. El hilo puede ser de latón o de zinc (y molibdeno en máquinas de hilo recirculante), y puede ser reciclado. Procede de una bobina, y funciona por control numérico. Una bobina de 8 kg de peso, de un hilo de 0,25 mm de diámetro tiene una longitud de 19 km. El diámetro puede ser de sólo 20 micras para trabajos de precisión geométrica de ±1 micra. Existen diámetros de 0,25 y 0,3 mm. El electrodo-hilo está sumergido en el líquido dieléctrico, el cual suele ser agua desionizada, de resistividad eléctrica controlada. El agua arrastra el metal arrancado, su caudal es proporcional al espesor de la chapa que se perfora. Las guías del hilo tienen una precisión de 0,004 mm. El hilo puede cortar un agujero de un diámetro de 0,12 mm, aunque el diámetro del hilo electrodo es de 0,1 mm. Cortar un diámetro mayor que el del hilo se explica, porque saltan chispas laterales del hilo, que causan erosión en la pieza. El hilo se adquiere en rollos y a peso. La tensión mecánica exacta del hilo es importante para lograr un corte efectivo. Si nos excedemos, sobretensión del hilo, acabará en ruptura, algo bastante común, y a veces necesaria. Con un encendedor vulgar se puede romper el hilo. La posición de una cabeza superior y otra inferior, por las cuales pasa el hilo, requiere un alineamiento vertical concéntrico.
A diferencia de las máquinas de electrodo de forma en las que la polaridad aplicada puede ser invertida, el electrodo hilo no lo permite, es constante: la mesa donde la pieza es mecanizada es tierra; o sea, es de polaridad negativa.
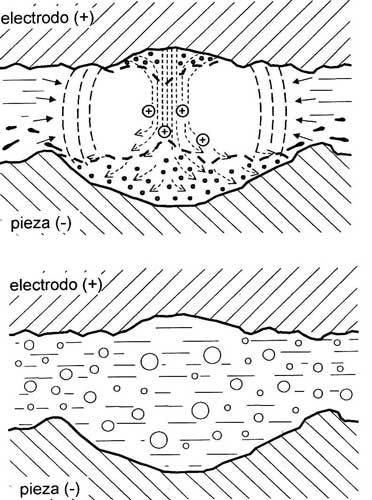
Abajo: El material fundido es arrastrado en forma de bolas por el líquido dieléctrico a derecha e izquierda. Las virutas de la electroerosión.
El hilo, por consiguiente, es positivo. En la máquina el hilo es tensionado en forma vertical (Z) para producir cortes y movimientos en axiales X e Y. La mayoría de las máquinas ‘por hilo’ tienen capacidad de mover sus componentes, para ajustar el hilo vertical, y producir cortes con un ángulo limitado (axiales U y V). Dos cabezales de diamante sujetan al hilo. Puede producir en una chapa un orificio que es, por ej. cuadrado por arriba y circular por abajo. El corte interno de la pieza presupone un agujero previamente taladrado. El electrodo hilo está sujeto por los extremos y realiza un movimiento de vaivén, como el de una sierra, y va socavando la pieza hasta lograr la forma geométrica deseada. Si el corte es en el exterior de la pieza, el hilo empieza el movimiento desde el perímetro exterior hasta provocar el arco. Continúa su movimiento hasta conseguir la periferia deseada.
El hilo tiene sus ventajas, pues, no precisa el mecanizado previo del electrodo, es de alta precisión para formas complejas, y el resultado es constante. Según la capacidad de la máquina, el trabajo con alambre puede incluir angularidad variable controlada, o geometría independiente (4º eje). Se pueden mecanizar placas hasta 30 cm de espesor, metales previamente templados, y así evitar las deformaciones producidas por un tratamiento térmico, después de terminada la pieza. El arrastre de partículas de metal por agua desionizada requiere poca energía.
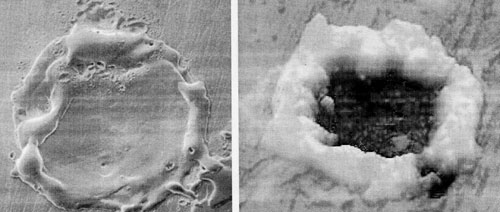
Sus aplicaciones más importantes las encontramos en la fabricación de moldes, master, para la estampación de joyas, plata, monedas, etc. Producción rápida, en menos de 10 segundos, de prototipos de componentes en la industria del automóvil, aeroespacial, electrónica. Las hileras de agujeros microscópicos en el borde de salida de los álabes de turbinas de aviación, para inyectar gas en el motor, permiten el funcionamiento a muy alta temperatura. La alta relación diámetro-longitud del agujero no es posible con la tecnología convencional de perforación.
Erosión electroquímica
Es el método de mecanizar materiales no conductores, por ej., los polímeros. Es análogo a la electroerosión. Se trata de un proceso en que el material se elimina por disolución anódica del mismo en una corriente rápida de electrolito. Es básicamente un proceso en el que la herramienta es el cátodo y la pieza el ánodo. El cátodo podrá ser un electrodo de forma, o un electrodo de hilo. Al aplicar una corriente eléctrica se producen chispas en la superficie del cátodo, que llevarán a cabo la mecanización. Ambos electrodos han de ser conductores, y el electrolito arrastra los lodos hasta un filtro de decantación. La herramienta avanza hacia la pieza a una velocidad constante, adaptada a la velocidad de disolución de los electrodos, manteniendo entre ambos electrodos una distancia de 0,07-0,075 mm. El intersticio evita el cortocircuito entre electrodos. Mantener la distancia correcta entre ánodo y cátodo es fundamental. A través del intersticio circula la corriente del electrolito, que arrastra los residuos de la descomposición del metal de la pieza. El aumento de voltaje incrementa la energía de descarga, la formación de chispas y el desbaste. Para la herramienta se emplea cobre principalmente, pero también latón, acero inoxidable, grafito recubierto de cobre, para evitar su erosión, aleaciones de wolframio-cobre. La herramienta permanece inerte frente a las reacciones químicas primarias. De suyo no se desgasta, pero de hecho hay una lenta degradación de la misma.
El electrodo de forma se usa para realizar una cavidad, o un agujero. El electrodo-troquel tendrá la forma de la cavidad a realizar, y mediante un movimiento vertical entre la pieza y la herramienta se producirá el mecanizado. El electrodo de hilo realiza los cortes, y puede describir trayectorias complejas 3D. Los factores más decisivos son el diámetro del hilo, el voltaje y amperaje aplicados. La velocidad de mecanizado variará. Si la tensión del hilo es baja, producirá un mal acabado de la pieza, pero si hay sobretensión se puede romper el hilo.
El electrolito es agua con sales conductoras, como NaCl, KCl, NO3Na, a una temperatura de 30-50 °C, con velocidades de flujo de corriente de 15-60 m/s y con presiones de 15 bares. La pieza es metal de gran dureza, y no sufre alteración de su estructura cristalina. La pieza queda libre de rababas, por lo que no hace falta ninguna operación de acabado. La tensión es de corriente continua, de 6 a 35 V. La corriente muy intensa, entre 10 y 10.000 A. La densidad de corriente es de 2,3-3,1 A/mm². La velocidad del proceso es de 1,5-2,0 cm³/minuto/1.000 A. La velocidad de penetración es de 2,5 mm/minuto en aleaciones duras. Se consiguen tolerancias de ±0,025 mm de precisión dimensional.
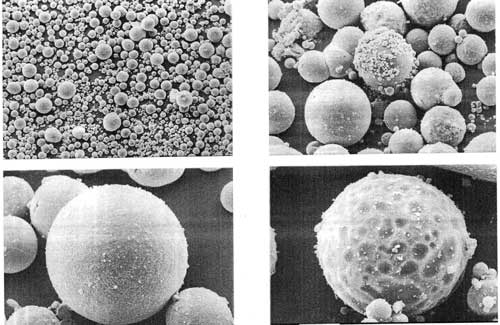
Existen variantes:
- Pulido electroquímico: es el mismo proceso, pero sin avance. Con velocidades de electrolito y densidades de corriente menores, con lo que se logran superficies de acabado muy fino, con valores del orden de 0,25-0,30 micras.
- Taladro electroquímico: Para agujeros de diámetro muy pequeño. Para ello se emplea un voltaje elevado y un electrolito ácido. La herramienta es una boquilla de vidrio estirado, con electrodo interior. El intersticio es de 0,03-0,06 mm. Presenta la ventaja de que se pueden mecanizar simultáneamente múltiples agujeros. En metales como el Ni y Co se obtienen agujeros de 0,1-0,75 mm de diámetro.
- Desbarbado electroquímico: La pieza a desbarbar se introduce en un tambor rotatorio, asilado eléctricamente, que contiene dos electrodos de corriente. Se añaden al electrolito unas esferas de grafito, que se cargan en los electrodos. Las esferas en el intersticio provocan el mecanizado electroquímico. Las rebabas desaparecen, y producen un pequeño cambio dimensional en la pieza.
Referencias
- Descoeudres, A. Electrical discharge machining plasmas. Thése EPFL, 2006.
- Derek, Pl. Industrial electrochemistry, Springer 2004.
- Dibitonto, D. Electrical discharge machining process. Journal of Applied Physics 66, 1989.
- McGeough, J. Advanced methods of machining. Springer 2007.
- Semon, G. A practical guide to electro-discharge machining. Atelier De Charmilles, Geneva 1975.