Handtmann inicia el moldeo a presión en su planta de Biberach
Hace dos años se dio inicio en Alemania al innovador proceso de moldeo a presión, en el que Handtmann ha invertido millones. Un año y medio después de la ceremonia, el 25 de octubre de 2024, se ha moldeado la primera pieza de serie en la nueva máquina de megafundición de la planta de Biberach.
Por megafundición se entiende la fundición de piezas metálicas de gran tamaño, cuya producción requiere técnicas y máquinas especiales. A escala internacional, la megafundición es ya una tecnología emergente, sobre todo en China y Estados Unidos. El proceso de fundición a presión tiene el potencial de revolucionar el proceso de fabricación de automóviles. Por ejemplo, pueden fabricarse en aluminio grandes carcasas de baterías o bastidores de hasta dos metros de longitud para vehículos eléctricos. Incluso pueden fundirse en una sola pieza secciones completas delanteras o traseras de un coche.
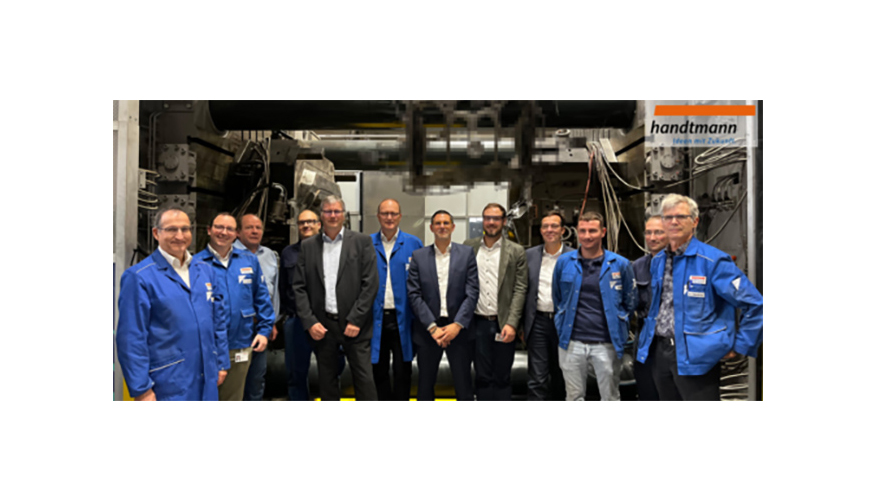
Handtmann ya ha puesto en marcha los primeros proyectos con fabricantes de automóviles alemanes: se adentra en la producción de grandes piezas estructurales con la exitosa puesta en servicio de una Carat 610 ampliada de Bühler AG con una fuerza de cierre de 61.000 kN y un peso de inyección de hasta 128 kg de aluminio.
La megafundición es un componente importante de la estrategia de Handtmann para apoyar a sus clientes en la transformación y se está estableciendo deliberadamente en la sede central de Biberach para reforzar la competitividad de la industria automovilística alemana. Las inversiones en nuevos procesos y tecnologías son la clave para garantizar el crecimiento, la innovación y la competitividad a largo plazo en Alemania y Europa.
Megacasting permitirá a Handtmann introducirse en nuevas áreas de producto. En línea con el lema ‘we deliver transformation’, Handtmann seguirá aumentando su competitividad y reposicionándose como una empresa de fundición a presión fiable y dispuesta a reinventarse continuamente con cerca de ciento cincuenta años de experiencia.
“La capacidad de producir componentes estructurales grandes y complejos en una sola colada nos permite acortar el tiempo de producción, mejorar la eficiencia de los materiales y aumentar la integridad estructural de los vehículos”, ha anunciado Heiko Pfeiffer, vicepresidente ejecutivo de producción de la división de fundición de metales ligeros.
Las ventajas de los grandes componentes fundidos en una sola pieza incluyen principalmente una menor complejidad de fabricación con menores costes de compra y logística. Se reducen los pasos del proceso de producción y se evitan pasos de unión y acabado que requieren mucha mano de obra, como la soldadura y el fresado. Se ahorra peso en la carrocería, lo que es especialmente relevante para los vehículos eléctricos. La megafundición también es interesante desde el punto de vista de la sostenibilidad, porque los componentes más grandes fabricados con un solo material ofrecen ventajas en términos de reciclaje de vehículos.