Electroerosión por hilo para el mecanizado de perfiles firtree de discos de turbina
ONA ha realizado un estudio para analizar un proceso de electroerosión por hilo (WEDM) como alternativa al mecanizado convencional (brochado) de perfiles de abeto en discos para el sector aeronáutico. De hecho, el WEDM de ranuras de abeto podría convertirse en una opción industrial viable y sustituir al brochado en el futuro.
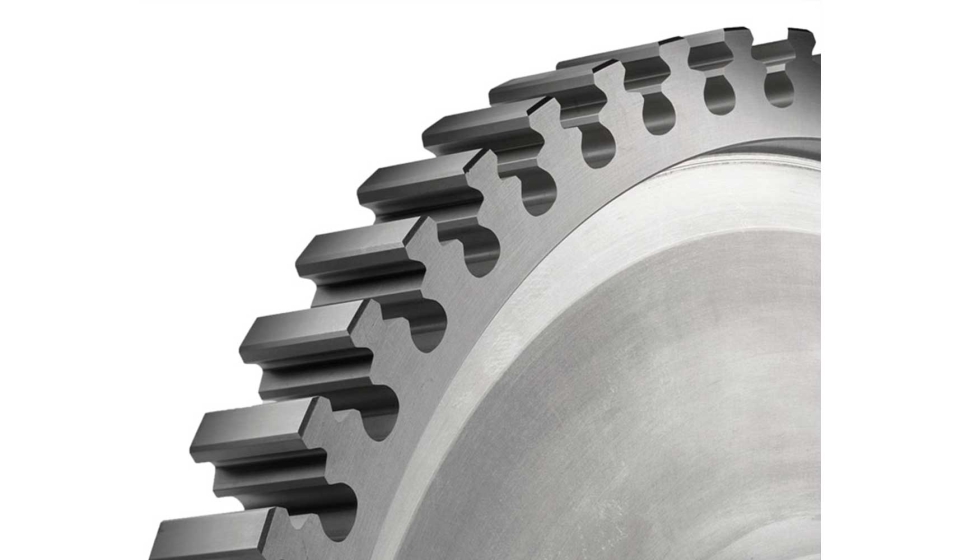
En su investigación, ONA comparó el proceso de electroerosión con otros mecanizados más convencionales como el brochado y el fresado. Como puntos clave de la investigación, ONA comparó parámetros como los requisitos de integridad de la superficie, la precisión y el tiempo de procesamiento del mecanizado de firtrees.
La prueba consistió en cortar un disco de turbina con las siguientes características:
- Material: Inconel 718.
- Diámetro exterior: 350 mm.
- 28 perfiles de ranura de abeto.
- Perfiles de ranura con un ángulo de 30 grados.
- 82 mm de espesor.
- Tolerancia del perfil 0,01 mm.
- Tolerancia de posicionamiento radial y angular de firtree 0,08 mm.
El objetivo de la investigación era cortar los dientes de ‘firtree’ de la turbina mediante WEDM cumpliendo los requisitos de tolerancia para analizar la siguiente información:
- Tiempo de desbaste de todo el perfil.
- Tiempo de acabado de todo el perfil.
- Tiempo total de erosión de todo el perfil.
- Tiempo total de desbaste del disco de turbina (incluido el tiempo de preparación).
- Tiempo total de acabado del disco de turbina (incluido el tiempo de preparación).
- Tiempo total de mecanizado (incluido el tiempo de configuración).
- Tasa de arranque de material MRR (mm2/min).
- Espesor de la capa refundida.
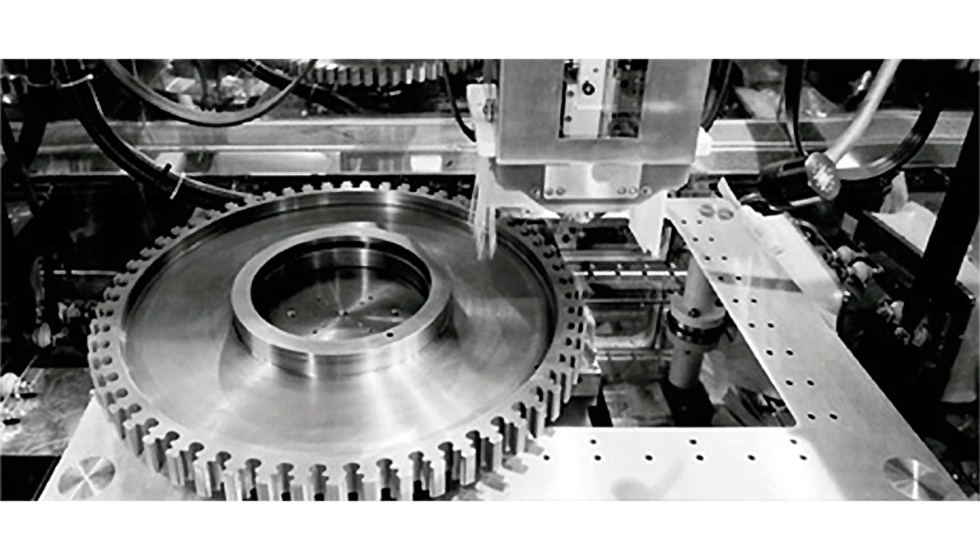
Configuración de electroerosión y condiciones de mecanizado
Para llevar a cabo el análisis, se utilizó la tecnología ONA estándar para aleación de níquel, una mesa giratoria de 2 ejes y dos condiciones de lavado diferentes. Por un lado, buenas condiciones de lavado (boquillas cerradas) y, por otro, peores condiciones de lavado (boquillas abiertas). Además, se utilizó alambre revestido de 0,25 para el corte de desbaste.
Estos dos escenarios diferentes elegidos para el estudio (boquillas abiertas y cerradas) nos permitieron realizar diferentes pruebas para evaluar adecuadamente el tiempo de erosión, ya que éste depende en gran medida de las condiciones de lavado. Es frecuente que, debido a las características geométricas de los discos de turbina, no puedan utilizarse toberas cerradas.
Resultados de la investigación
Al término de las pruebas, los resultados mostraron que se puede obtener un espesor de capa de refundición en el rango de micras necesario (alrededor de 5 µm) y con suficiente precisión en el perfil de abeto dentro de una tolerancia de 0,01 mm. utilizando la tecnología WEDM. Estos resultados se obtuvieron tras una pasada de desbaste y dos de acabado (estrategia de 3 cortes).
En peores condiciones de lavado (boquillas abiertas), la tasa de arranque de material para el desbaste fue de 110 mm2/ min. De hecho, para la estrategia utilizada en la investigación (una pasada de desbaste y dos de acabado), la tasa de arranque de material fue de 60 mm2/ min.
Por otra parte, en buenas condiciones de lavado (boquillas cerradas), se observó una ligera mejora de la tasa de arranque de material. Sólo en el proceso de desbaste, alcanzó más de 400 mm2/ min.
Conclusiones
Tras la investigación, podemos concluir que el mecanizado WEDM de perfiles de abeto de discos de turbina es una alternativa muy válida para competir con el brochado como solución industrial en el sector aeronáutico. Los generadores de última generación, cada vez más potentes, y los controles numéricos más avanzados permiten optimizar el tiempo de mecanizado y reducir el espesor de la capa blanca. Además, consiguen una precisión geométrica muy buena.
En el estudio realizado por ONA (estrategia de 3 cortes), el mecanizado de firtrees de discos de turbina cumple las tolerancias geométricas y obtiene una capa blanca inferior a 5 μm. Además, se obtiene información muy valiosa sobre la tasa de arranque de material y el tiempo de mecanizado.
Es cierto que la certificación del proceso completo de mecanizado mediante electroerosión según las normas aeroespaciales estándar puede ser un proceso largo y costoso. Por este motivo, la ONA concluye que una opción mejor sería combinar la electroerosión por hilo para el desbaste, ya que es más barata y rápida, junto con el brochado para el acabado final. Por consiguiente, no sería necesario volver a certificar el proceso.