Manufactura aditiva en la industria aeroespacial
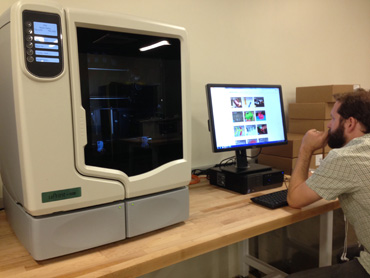
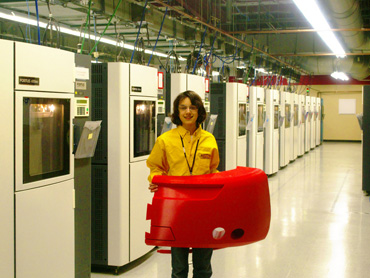
Una de sus principales aplicaciones se está dando en la industria aeroespacial, donde las nuevas tecnologías de manufactura digital aditiva están cambiando de manera acelerada el panorama presente y las previsiones de futuro en todo lo que rodea a este sector: Si hace veinte años la tecnología se caracterizaba por unas máquinas muy limitadas en sus prestaciones, unos materiales muy limitados en resistencia mecánica, y un casi absoluto desconocimiento de estas tecnologías, vemos que a medida que pasa el tiempo las máquinas van haciéndose cada vez más grandes y se están desarrollando nuevos materiales no ya para el simple prototipado rápido sino también para la fabricación directa de fijaciones y utillajes para la línea de montaje, e incluso para la fabricación directa de piezas de uso final.
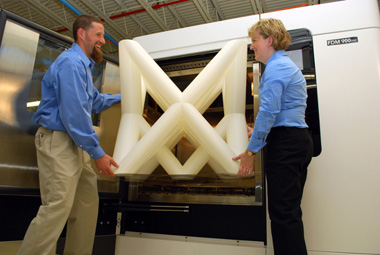
Por lo que respecta a la aviación civil, una exigente normativa de seguridad, combinada con los crecientes costes del combustible, han propiciado la salida a escena de un material revolucionario que goza de tres características clave para este sector: Es ignífugo, posee una baja densidad, y ofrece una incomparable resistencia mecánica. Estamos hablando del ULTEM 9085. Esta polieterimida —certificada para su uso por las normativas ABD0031, BSS7238, BSS7239, FAR-25.853, OSU 65/65 y UL94-V0— está siendo cada vez más utilizada en unos casos para la fabricación de piezas que no se detectan a simple vista —como pueden ser los conductos de aire y los paneles aislantes de nido de abeja— y en otros casos para la fabricación de piezas únicas tales como las toberas de regulación de climatización, las carcasas de aparatos electrónicos de ocio a bordo, y muchas otras piezas de objetos únicos ubicados en el interior de aeronaves exclusivas de alto standing, personalizados para cada cliente a fin de lograr su máximo confort.
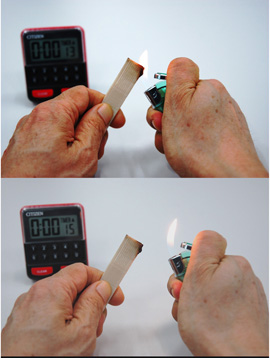
En lo que respecta al sector militar, su aplicación más frecuente se está dando hoy día en el desarrollo y fabricación de aviones no tripulados capaces de volar a mayores distancias o de transportar mayores cargas de pago, pero gastando menos combustible: En este caso la Manufactura Aditiva ha resultado clave al posibilitar la combinación de materiales ligeros e ignífugos como el ya mencionado Ultem 9085, con diseños de alto rendimiento aerodinámico, imposibles de obtener mediante manufactura tradicional. Pero sus aplicaciones no se limitan a las aeronaves no tripuladas: Llegados a este punto, merece la pena considerar el caso de KMC (Wichita, Kansas), principal fabricante mundial de instrumentación aeronáutica civil y militar. Antes de implementar la fabricación digital directa, KMC fabricaba piezas mediante inyección. Fabricar 500 carcasas ignífugas para transformadores toroidales mediante moldes de silicona le llevaba a KMC entre 3 y cuatro semanas desde el pedido hasta la entrega. Ahora, KMC produce esas 500 unidades en tan sólo una noche mediante fabricación aditiva.
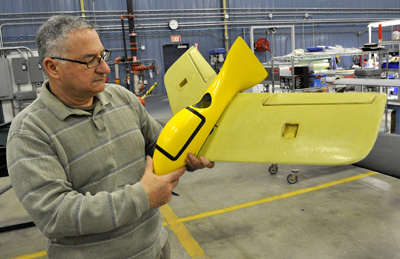
Y es que en un momento como el actual, caracterizado por los recortes de presupuesto, optar por la manufactura aditiva en todas las fases del proceso productivo puede resultar una buena alternativa gracias a la versatilidad de aplicaciones que ofrece y al considerable ahorro de costes y tiempos que puede reportar: Podemos usar la misma máquina durante una semana para fabricar prototipos funcionales, a la siguiente para fabricar una variedad de utillajes y a la siguiente para fabricar piezas de uso final, obteniendo siempre un ahorro de costes y tiempos imposible de obtener mediante la manufactura tradicional. En definitiva, parece cada vez más claro que la manufactura aditiva ha venido para quedarse, y está demostrando con creces que puede cambiar las reglas del juego: “La Impresión 3D posee el potencial para revolucionar el modo en que fabricamos casi todo. Si queremos fabricar mejores productos, tenemos que invertir en mejores ideas.” (Barack Obama, discurso ante el Congreso durante el Debate sobre el estado de la Unión. Enero de 2013).
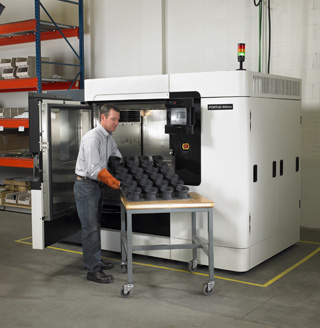
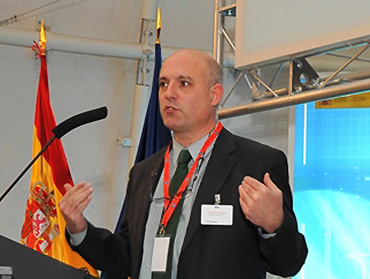