High application of composites in construction
Another work is also a reference because it represents the consecration of the composites as structural materials, in direct competition with the steel and reinforced concrete. In addition, is located in Valencia, city that welcomes us for the first time in these 17 Conference on composite materials and in case outside little, us Chairman, because it is located a few metres from the magnificent Auditorium of the Universidad Politécnica de Valencia. It is the Tower of the UPV.
Both achievements, distinct but at which more interesting will be leaven of new works that expand the horizon of the composites in this early twenty-first century: are only in the home.
Reason and be of the composites in two singular achievements
In the end, composites have been elected and have been because in addition to some notable qualities, they have been reliable and found fit through numerous trials and tests, and finally, it is very important, because at a very competitive price.
In both implementations, and this is something to note, he has been with a team of professionals with high technical preparation, with great enthusiasm and determination, and what is very important, a great imagination. When he goes in cutting edge, as in these cases, arising from continuous amount of new problems you need to know weigh and solve and here the imagination is key, because the traditional does not work.
The singular points which provide the composites, include: a great lightness and resistance, excellent surface finish, lack of maintenance, fatigue strength, handling them at work and maximum design freedom.
An architect, engineer, designer, Builder, or technician in general, has never had in his hand a material with so many possibilities as the accompanying composite materials, therefore, give you a freedom and ability to design unique.
Extension of the Museo Nacional Centro de Arte Reina Sofía
There are a lot annex to the Museum, adjacent to three streets, round Atocha, calle Argumosa and Street Hospital. The fourth façade is bordered by the Museum Reina Sofia, Madrid classical construction with no less than two centuries of history, the former Faculty of Medicine of Madrid.
The new building should be library, room for temporary exhibitions, a large auditorium, workshops, as well as cafeteria and services two sotar us. This project there are many architects from around the world, becoming the winner of the prestigious architect Nouvel francésJean, author of emblematic works around the world.
The winning project presents a remarkable feature: the concatenation of its surfaces, extending without solution of continuity, from the deck, the four facades, the bottom (which constitutes the ceiling of the ground floor) two large screens supportreferred to by way of two huge keels and the ceilings of the slabs.
I confess that the first time I visited the work, I felt the feeling of being lost, because it gives the impression of being before a giant maze, with 5,000 square meters of surface.
There are virtually no flat areas. This is the great novelty and the difficulty that involves getting the agreement of all its parts, defined by successive and different radii of curvature. Suffice it to say that the regulated areas, with double curvature, reach 80% of the total.
This means that final cutting has generated more than 600 types other than a total of 1,200 pieces of cladding panels, all them in composite whose details we will look at later.
This was the challenge of Jean Nouvel, and he attended various materials, like forming brick, panels of parent cementicias, reinforced with glass (GRC), etc., but for aesthetic reasons or for technical challenges, they were repulsed by the architect.
The ground floor of the building consists of enclosures of curtain wall glass with a core of stairs of steel and glass located on the main façade of the round of Atocha Street.
The Auditorium, boast of composites of a great attraction stands out from the building in its 4/5 parts through openings in the upper floor, also glass, and is supported by two curved screens above, by way of two keels.
Glass surfaces on the one hand allow enter and lead the visitor to the interior of the building and at the same time allow you to see the entire set, with access to all of its parts.
Composite solution
And in our case, exclusive of the composite, acts as a mirror, reflecting figures, adjacent building, the movement of the street, and so on.
Personally I have been fascinated by the play of lights and shadows, colours and figures that is capable of reflecting the composite material, working here has become, with high technology and to have greatly contributed two people, the technical manager of the composite solutionEnrique Márquez González of DYC-ACS, and the manufacturer of the panels, Pedro Guijarro of Composite Guimar, company located in Manzanares 100 km from Madrid.
Computer design
This program defines a virtual model that moved to a language of numerical control, allow the carving to scale on a block of wood, of the surround solid of the Auditorium, in other words, our shells in composite. On it, the design team, check the
surfaces and resulting encounters, makes corrections estimated appropriate and points out the general criteria of butchering.
With these changes is a new virtual model - final principle. In the outlining all the lines of tangency of the different surfaces, optimizing the cutting of the resulting levels to get models more repetitive and relatively simple, in the enormous complexity of the set.
As reference we would say that the number of square metres of mold exceed 200 and precisely because of this formidable tool which is the Catia, each mold can work several panels "different but the family". It is the only solution to make economically viable production and thus this solution of "family mould", has conditioned the manufacture itself as we discuss later.
Panels surface of generating curve and straight guideline or simple curves, templates in one or two senses are made with Autocad 3D and hence models by specialized cabinet makers.
The panels of more complication, the Catia, as we have said, will go it down in lathes of numerical control that will act on the billets of wood. After turning the model, it enmasilla, polishes and protects and is ready to make the mold.
Mold
As we know, the modelo-molde relationship is total. All levels of Assembly and workshop are obtained from the second virtual model. The contribution of the Catia tool in the manufacture of the modelo-molde has been a key, because it allows us to make sections of the
solid generated with any type of surface, by way of tomography, obtaining the outside line of every intersection in their true magnitude although undefined thicknesses or relations with adjacent levels. These lines are passed to Autocad 3D and on them were
Add the thickness of panel, shells, insulation, etc., allowing the development of plans on plant, elevation and section.
About the elaborate plans the strings and arches of its perimeter, the orthogonal situation of their cajeados, metal anchors, i.e., to define everything that goes with a panel are measured. This gives clear references to the layout of the side edges on the molds as well as the precise situation of the points of anchoring both the panels work.
This development allows the combination of CAD-CAM techniques of the aviation industry, without having to make them extend to each and every one of the panels, which would have been impossible take deadlines and costs.
It should be recalled that the series of industrial manufacturing range from antennas of identical units, in aviation for example, to hundreds of thousands in automotive, and singular, as in our case buildings, pieces unique and unrepeatable.
Manufacture of composite panel
They have been chosen a resin polyester self-extinguishing ortoftálica that meets the conditions of necessary protection to the fire.
On resin cast phenolic - fiberglass perfectly prepared, is rusting and later a first layer of MAT resin ortoftálica that will be left to heal. Then is postcura in furnace and turns to laminar repeating the operation a third time. It's that I monitor to maximize the contractions of the laminate, looking back on it if it is necessary to achieve a completely smooth surface.
Once built the outer skin of the panel, is given a coat of resin and is superimposed a 45 mm panel thickness of foam panels with a layer of fiberglass reinforcement, closing the set with a vacuum bagabsorbent, sealants, etc., in the aeronautical style. Once polymerized as a whole, are anchors at certain points and are laminarán other two layers of reinforcement.
We have structurally the panel, which will be in greatest dimension up to 3.60 x 1.60 m without presenting any problems of deformation.
Completion of the panel
The way to be followed it is another that consists in applying a similar method to the developed for panels with matrices of hydraulics conglomerate, consistent in successive imprimaciones, lijados, layers of nacreous painting and varnish shine anti-painted, applied in cabin of painting.
Following some rigorous protocols of work, controls the ventilation, temperature and time of wait, precalentamiento and cured of each layer.
This finishing allows, as they can you check, the modification of the familiar moulds to realizar in them different pieces.
The resultant marks in the surface of the panels, consequence of the successive cuttings and splice of models and moulds, can repair in the previous operations to the painted, repairs these, impossible to carry out in the gel-coat tintado usual.
Like summary of this realisation, will say that it could establish perfectly this trilogy:
Jean Nouvel Panels composite enlargement Museum Queen Sofia.
In our opinion, had not been able to reach the realisation of the work of the genial architect, without having the composites.
The design of Jean Nouvel, is tied with them.
Tower UPV (Valencia)
Professor D. Juan Antonio Rovira-Soler
This marks it so that in the 1980s and 1990s, it delves into his contacts and experience with these new materials.
Finally in 2003 and by the Rector of the UPV, get commissioned to raise an innovative and emblematic Tower of what is new and vigorous UPV from Valencia, Tower to see and check the situation from afaras a faro-guía and at the same time innovative, testimony knowledge and knowledge of the University.
The occasion is unique and choose composite materials, and as a good engineer, think that we need to dispose of composites with the module of young or possible maximum stiffness and at the same time a fact process, because this will take you to the best possible price.
You can imagine that the result is none other than the pultrusion technology; It is the logical end and he will direct their efforts, ending by contact with the industrial Barcelona Jaume Tatjé Soler, Managing Director of Tadipol and Tecnipul, forming a duo of undoubted importance for the realization of this tower.
Design of the Tower
The Tower starts from the ground with a diameter at base of 8.5 m and ends with a diameter of 0.16 m.
The 31,2 metres from ground level starts as a Crown a conical poster of the UPV in composite which has a total height of 3.15 m diameter at base of 4.30 m; 7,70 m at the top and 6 mm thick. This poster, a challenge for the purposes of stability and behaviour with the wind, weighs 3 t.
On the poster and at an altitude of 37,35 m from the ground is the center of a sphere of fiberglass of 2 m diameter of 6 mm which together with the pinnacle that ends and you arriostres them corresponding, they throw a weight of 2 t, i.e. tapered poster more field with Pinnacle of Coronation with a total of 5 tonnes of weight, all of this starting at an elevation of 31.2 m. Well, the tower is designed and calculated to withstand winds of 115 km in base and 160 km at the level of the poster. In this case extreme, the deflection of the tower at tip, would be 0.90 m.
Construction of its elements
flexion and traction. They are made of fiberglass and resin vinylester.
These legs have a length of 10.90 m forming at the base diameter of 8.50 m and 2.40 m. completion
From this height, the legs become six, with the same composition as in the lower section, and maintain the curvature of the tower to 23.30 m with a diameter of the Tower of 1.25 m.
Finally and 23.30 m to 35,77 m the legs become 5 hollow tubes of 60 mm in outside diameter and 9 mm wall with the two solid lunettes of previous glass.
35.7 M to 42,35 Coronation m, it will be only hollow tubes of 60 mm in diameter that will make up an outside diameter of the Tower of 0.16 m, position in which anchor the lightning rod of 2 m in height.
Rings
The twelve main uprights are linked together by elements that we call "rings", each 2 m to a height of 10.90 m. These rings have a geometry of the truncated cone with a rectangular section of 400 x 200 x 8. The geometry of the Tower has 41 levels, while each level represented by these rings. Up to a height of 12 m there are outer and inner rings on the legs. From this height, the rings are only foreign except in the area of connection of the sphere and poster with the main structure.
All the rings of the structure are isophtalic manually stratified glass fibre reinforced polyester. In the future will be applied to a new technique that we are developing with a net improvement both in the technical aspect as economic.
Finally, among the 23,40 m and 35,77, each one of the "six faces" of the structure, is arriostrada through straps or solid profiles in fibreglass of 8 mm in diameter; These straps limit the inclination of the tower.
All the elements of the Tower, including screws, thread and washers to attach legs to rings, are made in fiberglass and resin polyester, as indicated in the table below:
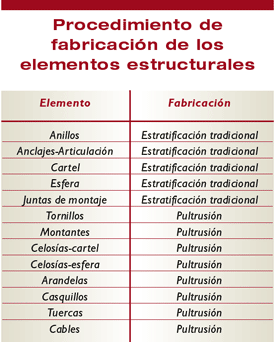
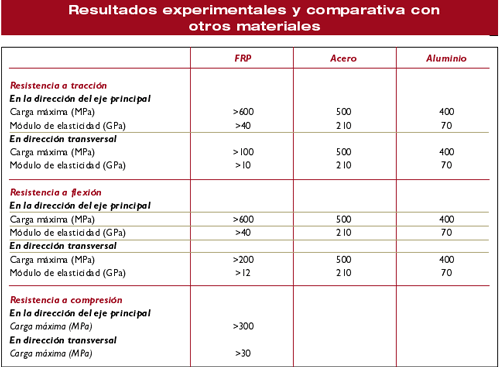
Trials
Transport and Assembly
The structures built with this material, weigh the same resistance, the fourth part of steel structures, which affects a greater economy and speed of Assembly, cheaper foundations and allowing its use in less consistent land, such as areas near the sea, although its properties would allow them to be anchored in the same sea. The pictures that we illustrate how much say, speak for themselves.