Composites: Useful but difficult properties to mechanise
The aeronautical sector component manufacturing sector component manufacturing construction would be impossible without the compounds and also in the industry of the car have an increasingly important paper. Nevertheless, his processing and mechanised result difficult. For the machine of mechanised and the tools are extremely demanding especially the plastics reinforced with fibre of carbon in which the fibre is inserted in a matrix, as well as the compounds of materials with a structure by layers. The manufacturers expose the possible solutions in the next
The environingingment of the sector of compounds is extremely positive. Around the middle of year jointed the four technical organisations, that is to say, the Industrial Association for plastics Reinforced (AVK), Carbon Composites, plastics Reinforced with Carbon (CFK) - Valley Stade and the Forum Composite Technology in the VDMA to form the Professional Association Composite Germany and one of his first conjoint actions was the realisation of a survey on the economic situation. The greater part of the companies associated describe it as “extremely positive or very positive", as it ascertains Walter Begemann, director of the project of the Forum of the VDMA. What results especially satisfactory for the manufacturers of machines-tool and tools of precision is that two third parts schedule a still greater commitment. The impulses of growth more important proceed of the German industries and Asian of the car and of the aeronautical sector component manufacturing sector component manufacturing. It is thus that Michael Effing, president of the association, describes the compounds like “a key technology for the emplazamiento industrial in Germany”.
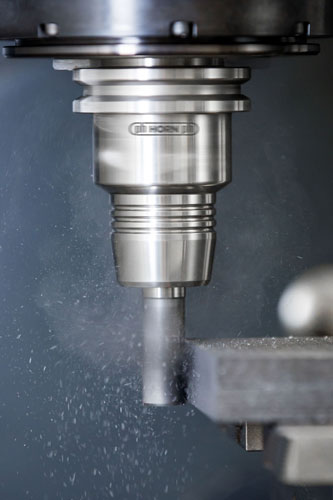
The same thinks the chair Frank Barthelmä, general director of the Society for Technology of Production and Development (GFE) and.V., Schmalkalden. Nevertheless, it warns about some of the central challenges: the danger of the deslaminaciones, insufficient useful lives of the tools and the aspiration of the particles of dust generated. “To the hour to design solutions for problems of this type, results indispensable to contemplate all the chain of process for the mechanised of the compounds, beginning with the concept of machine, the parameters of the process, the quality of the components and, of course, also the tools”. The GFE has achieved to adapt perfectly the tools in an iterative process to the task of mechanised. In concrete: “Thanks to some technologies of mechanised adapted like the polishing by brushed, the micro-finished by means of rectified of drag or the micro-granallado, has been possible to manufacture of reproducible form some radii of edges of cutting perfectly defined of some micrometers, all this along all the edge of cut of the tool”. These appearances are especially important in case of combined or staggered tools to be able to avoid the deslaminaciones, as it comments Barthelmä. Another step is the coating. In this sense, the layers of oxinitruro with oxygen inserted have resulted especially apt, improving the useful lives in more than the double in comparison with the conventional tools of hard metal macizo. The experts of mechanised of Schmalkalden expect some still better results of similar layers to diamonds (DLC: carbon type diamond) that they can turn into an economic alternative for the polycrystalline diamonds (PKD) or the tools of diamond CVD (CVD: deposition in phase of steam) whose cost is very high.
Also the manufacturers of machines-tool have to realizar his contribution. Barthelmä Exposes that “high speeds with new husillos encapsulados are one of the conditions for the mechanised of compounds. To all this add the maximum dynamics of the machine and the possibility of the milling of several axles, as it occurs in the mechanised lateral or simultaneous of five axles”. Besides, big sample hope in the mechanised with methods of hybrid production, like the milling aided by ultrasound.
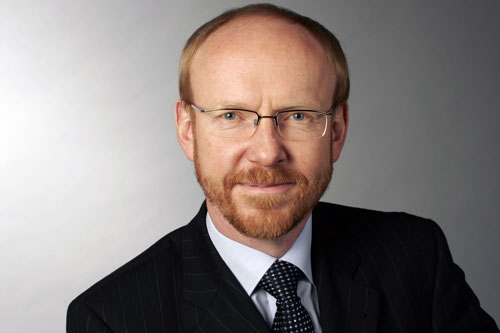
Reduction of costs in spite of some personalised solutions
Peter Büttler, responsible of activities of light construction of Komet Group, assumes that the requirements are heterogeneous: “On the one hand, the fibres differentiate by his material, length, thickness and sense of fibre. By the another side, the market offers at present more than 100 different resins for the matrix: duroplásticos and thermoplastic that they have to be mechanised in cold, and elastomers that require a high speed of cut, having to keep under the heat of friction in the slot of shaving to high speeds”. Appropriately, it is very important to keep a narrow collaboration between the user and the manufacturer of tools. “We check from the previous phase all the notable factors, like the material to mechanise, but also the technology of mechanised”. The work is different depending if it realizar in a centre of mechanised, with a robot or with machines of mechanised manual. To all this has to add the subjection of the piece of work and the corresponding risks of vibrations. Other factors: the refrigeration, the numbers of revolutions, the task of mechanised properly said and the aspiration.
The ideal would be a universal tool for a greater number of applications, “but for this at present does not exist any economic solution, since the compounds of materials extremely inhomogéneos establish some very miscellaneous requirements”, explains also the chair Diethard Thomas, director of the LMT Group Academy. Generally it is necessary to adapt the tool of personalised form to the compound materials. However, in case of compounds of materials in base to different materials assembled by layers, a solution to guarantee the profitability could be “orient the values of cutting to the partner of materials more difficult, for example, in case of compounds of CFK/aluminium or CFK/titanium”. Thomas perceives a need of permanent improvement since the materials are modifying and optimising constantly, especially by his high cost (suppose roughly the 50 percent of the cost): “In consequence also arise constantly new requirements regarding the design of the tools to follow optimising the process of mechanised, that is to say, the versions of tools and the recommendations of values of cut are subjected to constant changes”.
Aribert Schroth, specialist of product for materials of cutting ultraduros of the manufacturer of tools Paul Horn, desaconseja compare always the compounds only with plastics reinforced with fibre of carbon. “It is possible to mechanise the contiguous groups with the same tools but with different parameters of mechanised”. This starting point is similar to the that pursues the manufacturer of tools Mapal. According to Peter Müller-Hummel, boss of the unit of Aerospace and Compound business: “Like the requirements are used to to be identical, select always the most critical case what allows us cover a big number of the less critical applications”. Nevertheless, the intention of Mapal is to help to the customer to save costs also by other roads, as it explains it Müller-Hummel: “At present, the realisation of the mechanised in an alone operation of work, in place from among three and five steps of the process, has the potential maximum”. Besides, the special coatings for tools provide some useful lives longer reducing, for example, the cost by taladro.
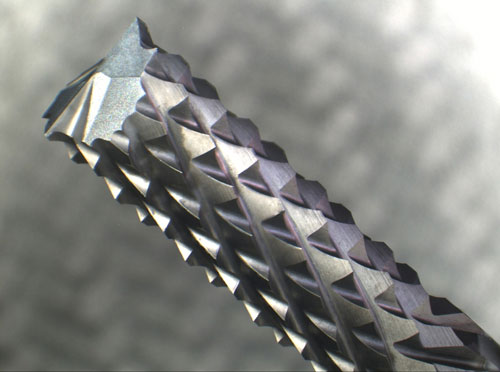
Generally, in what to the wear of the tools refers , still exists a lot of potential to increase clearly the profitability, as it reflects Schroth of Paul-Horn: “In what to the investigation and understanding of the processes that cause the wear of the edge refers , still remains a lot of way for visiting”. He centres the attention on another appearance, together with the requirement to the manufacturers of materials: “The prevention would result more effective from the phase of development of the material. Likewise, some narrower specifications and clear in the production repercutirían of positive form on the profitability”. In this sense, the current tendency to a lower percentage of resin and a strictly unisteeringal orientation of the fibres results advantageous, doing that the material was more predictable and calculable. This under construction light expert thinks that the corresponding elder deslaminación can be controlled: “What matters is that the edge of the tool was sharp and follow being it, for which comes us well practically any help”. The sensors can serve for this. Schroth: “In addition to the detection of the wear that contributes maximum utility, the behaviour of swing of the component results fundamental for the operation and the useful life of the tool used”.
An exact detection of the wear is also indispensable for the development in the wbk, Institute for the Technology of Production, in Karlsruhe. The scientific employee Stefan Klotz has analysed in more detail the damages of material produced by the wear of the tool during the taladrado. It has discovered that together with the wear of the tool “change the relations of mesh of the edge of tool, giving place to changes in the senses of strength of the process and an increase of the damages in the piece of work”. Klotz Proposes therefore a “dynamic adaptation of the parameters of process to the current state of wear of the tool“with the end to”reduce directly the damages produced in the layers of coverage”.
The machine-classical tool is used to to result too expensive
Whereas the manufacturers of tools follow investigating and developing for the attractor trucks market of the future of the mechanised of compounds, the manufacturers of machines-classical tool for the mechanised seems that have a general problem with the compounds: usually his machines are too small and too expensive. Ivica Kolaric, manager of the Department for Functional Materials in the Institute Fraunhofer for Technology of Production and Automation IPA explain the following: “For the mechanised of the compounds use frequently machines that have his origin in the sector of the mechanised wooden and plastic”. It is not of extrañar if they analyse the specific prices by surface. If in case of a machine-classical tool, the price by square metre of surface of mechanised can reach the 600.000 euros, the machines of mechanised wooden begin with some prices around the 10.000 euros by square metre, of course, with a clearly inferior precision. The situation could change modifying the requirements of the industry of the car. Whereas in the aeronautical sector component manufacturing sector component manufacturing industry and in the wind installations employ pieces very big, very fragile and of lower precision, the industry of the car requires pieces much smaller that they have to produce quickly in big quantities and with a high precision. The conclusion of Kolaric: “The offer of the manufacturers of machines has to be more economic and the manufacturers of machines of mechanised wooden have to improve the precision”.
This peculiarity also has detected in Mag Ias, as it explains it Matthias Meyer, vice-president of Composites: “The range of main pieces includes components lengthened of fine walls and, therefore, so much the area of work of the machine like the table of the machine have to dimensionarse appropriately. In spite of the fault of mechanised of free form, the geometries of pieces do necessary in the majority of the cases a mechanised in four or five axles to generate some edges of orthogonal cutting regarding the surface of the component”. Besides, the requirements regarding the husillo of tool are different to the ones of the mechanised of metals. Like technological competitor, Meyer has identified especially the cut by stream of water; although this method still litigates with disadvantages like damages in the components and big volumes of special rubbishes. “It is thus that in Mag has decided expand consistently the mechanised by milling of the compounds and resort to the knowledges of the automation and of the production in series”.
Another manufacturer of machines-classical tool that assumes the challenge is DMG Mori. “In addition to a concept of machine on a long-term basis and maximum dynamic, the machine has to be especially prepared for the mechanised of abrasive dusts”, explains Patrick Diederich, general director of the company Sauer GmbH in Pfronten, a subsidiary of DMG Mori. The range includes a hybrid concept in shape of ultrasonic machines, ideals precisely for the mechanised of difficult materials. In this process, a system inductivo of actuators flap the rotation of the tool with a cinematic of oscillating movement in longitudinal sense. “In this way we achieve a clear reduction of the strengths of process that are acting around 40%, obtain clean edges and avoid breaks of fibres, as well as the deslaminación at the same time that increase the advances”.
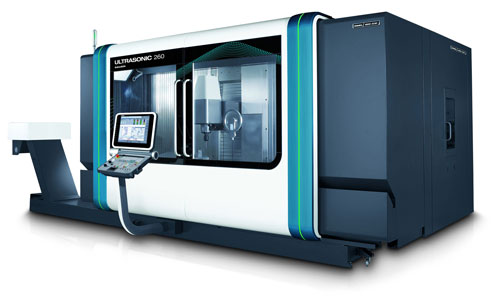
A big problem for the mechanised suppose it the abrasive dusts and of electrical conductivity. “The integration of a concept of integral aspiration that work perfectly is one of the most important factors. In addition to an aspiration of high performance with integrated surveillance of fine dust, as well as a recovery of heat in the optimum case, the machine has to have of an area of work closed with an integrated aspiration of the enclosure”. To avoid directly that the dusts can produce dangers, have situated the accionamientos and the guides out of the enclosure of machine. Besides, they have isolated the axles X and Z. A very serious council of Diederich: “Generally they have to protect all the electrical components. Besides, the husillo of mechanised has to be free of oil to avoid pollutions in the component”.
The dusts that go generating and his repercussions on the hygiene and the health are the main challenge for the employee of IPA Ivica Kolaric, in addition to the reduction of costs and the prolongation of the useful life of the tools. In his opinion, so much the people like the machines will be exposed to risks while they do not analyse thoroughly the concrete effects that have these dusts and define the best way to treat them: “The dusts no only can suppose a danger for the health, but they can fly through the ships of production to other machines and cause anomalies in them”. In the IPA a group of work in which it also participates the mutual professional is tackling these questions. The gentleman Meyer, employed of MAG, also confirms the problem to have to protect to the people and the machines: “The integration of the aspiration and the impermeabilización simultaneous of the components of the machines supposes in this sense a key appearance of the work. Nevertheless, no only they generate dusts, but also residual pieces very big that can not evacuate of the area of work of safe form, guaranteeing the hygiene of the process resorting to the conventional mechanisms like carriers sinfín”. Another central point is the manufacture of means of construction for a manipulation and safe subjection of structures of fine walls.
Generally, the mechanised of compounds establishes high requirements for the development of technology, as it explains it Patrick Diederich: “A combination of the most miscellaneous materials that gives place to a behaviour of material extremely anisotropic, requires to optimise all the data of the process, the tools, as well as the selection of the lubricantes refrigerantes”. In addition to the mechanised properly said, have to take into account also the following steps of the process, like the methods of hit, the painting or the back processing. Practically all the operations of rebordeado require a milling of several axles. “In this sense, precisely in the mechanised lateral and also in the simultaneous of five axles, especially the dynamics of the different axles has to synchronise perfectly between yes, since only like this is possible to guarantee a fast positioning or reposicionamiento during the demanding tasks of mechanised”, stands out Diederich.
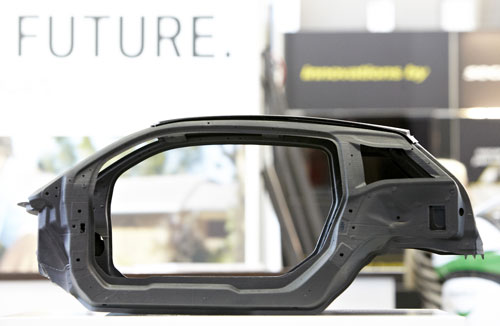
But even the machines-tool can benefit of the compounds. In this sense, in DMG Mori are analysing the sectors in which these materials can contribute advantages. Florian Feucht, director of the Department of Development of Composite Sauer in Stipshausen: “In a first phase centre us in the masses in movement and the increase of the energetic efficiency with the aim to achieve a maximum dynamics with the corresponding sustainability”. Instead, the possibility to compensate the travel induced térmicamente by means of the employment of fibre of carbon results less interesting. “This appearance already have it quite controlled with the current materials”. Also in the case of Mag are very important the compounds for the construction of machines-tool, especially when it treats of the dynamics, as it explains it Matthias Meyer: “they Are many the sectors in which ours machines have to accelerate the masses in little time”.
For the AMB 2014 that will organise between the 16 and on 20 September expect more than 90.000 professional visitors and roughly 1.300 display units that will show on a surface of 105.000 square metres gross his innovations and improvements of development in the sector of the technology of start of shaving and in the industry of tools of precision, as well as tools of subjection, CAD, CAM, FALLS, software, rectificadoras, systems of manipulation of pieces and tools, and technical of measurement. The AMB 2014 sees supported by the associations patrocinadoras VDMA skilled Association in tools of precision, VDMA skilled Association in software, as well as the VDW Association of German factories of machines-tool.