Two technologies to choose in implantología: additive or sustractiva
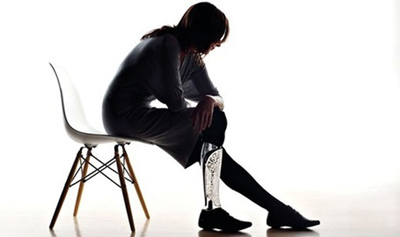
The possibility to obtain a three-dimensional digital model of the piece to substitute or of the zone to repair through different systems, joined to the new productive technicians, allows the realisation of an only unit perfectly ‘customizada' to each patient in some hours.
The advantages are many, in the first place the implant adapts to the patient requiring less hours of operating theatre put that the solutions of fixation of the same resolve before taking part, for example, in case of an articulation, the patient can recobrar before the mobility, the patient suffers lower pains, the period of hospitalisation is lower, etc.
The new technologies
The new productive technologies can divide in two big groups, the most modern additive technologies and the traditional technologies substractivas. The necessary investigation and apparition of new material biocompatibles also has gone tied to this revolution.
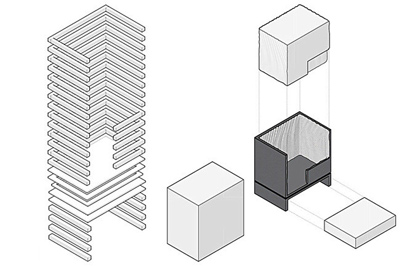
1. Additive technologies
The additive technologies or of prototyping fast, developed does few decades, contrived , initially, for the sector of development of product. The additive technologies work by the principle of addition of layers of material until forming a solid.
The materials were not definite, neither the finishings the necessary for a final product but the possibility to have a volumetric model in some hours, more or less functional, allowed to take out the product of the screen of the computer and accelerate the taking of decisions with the consistent reduction of the ‘Time to Market'.
However the advantage to obtain a piece without moulds, only and personalised, opened a window to the medicine. They did not take in appearing material biocompatibles and osteificables and the resolution of the machines —the height of the layers— happened of the 0,2 mm to the current 0,020 mm or lower.
The greater advantage of this technical is that it allows the creation of complex geometries, with inaccessible zones, as for example the possibility to build a hollow sphere, of this way can build structures lightened internally, with the same resistance but less weight, similar to the internal construction of the bones, so that the osteointegración was greater, geometries that would be impossible to achieve by technical substractivas.
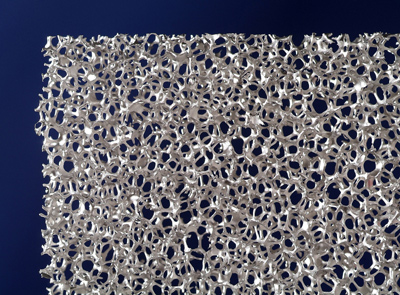
Inside the most known and used find the estereolitografía (SLA) and the sinterizado selective by laser (SLS).
SLA: In the first solidifies a resin through a laser that cataliza said resin.
SLS: The sinterizado selective by laser consists in agglutinating particles of material by means of a laser that goes melting these particles and soldering them until forming a solid. In both cases the process goes doing by layers, that is to say, the do of light amplified incide on a platform that displaces in the axis Z some micras once the layer or ‘slice' corresponding is list to happen to print the following.
The technology of sinterizado selective by laser more remarkable by his application medica is the, each more advanced day, system MLS or sinterizado of metals by laser and the sinterizado of plastics. The sinterizado of metals by laser supposes one of the greater industrial revolutions to productive level of the last years put that allows the construction of metallic pieces with geometries very optimised and in metallic material, from light metals until stainless steel and superaleaciones like IN718, IN625, ALSi10Mg, You6To the7Nb, ...
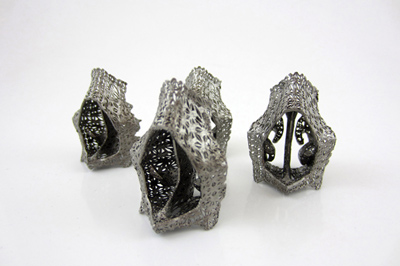
The medical application of this system could see it in Holland in June of 2011, the replacement of the complete bone of the jaw of a patient of 83 years by another produced by LAYERWISE in titanium, built in layers 33 micras (33 layers by each millimetre of height).
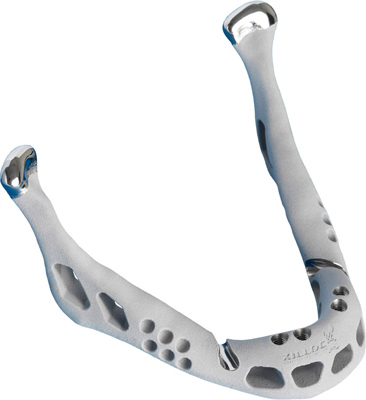
Inside the sinterizado of plastics, fits to stand out the sinterizado in plastic of type PEEK. The PEEK is a lighter alternative to the use of titanium in some cases and with a big osteointegración and whose main application are the cranial implants.
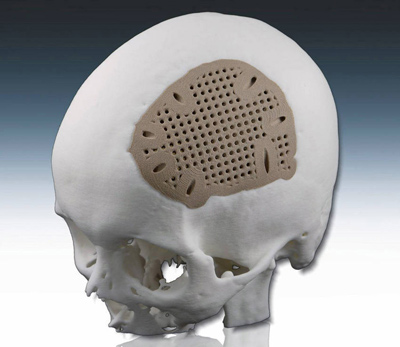
2. Technologies substractivas
The technologies substractivas are those that go deleting material from a metallic block or of other materials, until achieving the geometry wished, being the most known the mechanised. The main advantage of the systems of mechanised is his speed. The mechanised allows to obtain pieces with final finishings in terms very short, of some hours. The increase of the competitiveness and the proliferation of this type of machines have favoured his development and cheapening.
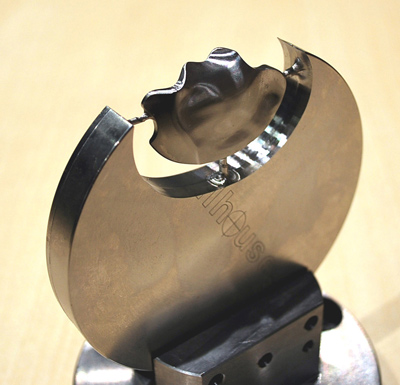
This has allowed ‘humanizar' the industrial machinery until the extreme to find integral solutions for ‘office', like the Datron D5, a system oriented to the dental prothetic sector that integrates a ‘interface' attractor trucks, a simple software and an advanced team of mechanised of 5 axles.
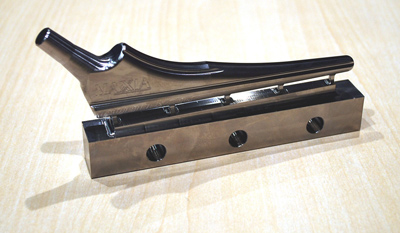
The precision and high quality of these systems does that they can produce pieces of implantología dental practically finished, produced in time record and with a big aprovechamiento of the materials, already are metallic (CrCo) or no metallic (Oxides of Zirconio, Waxles, PEEK, etc.)
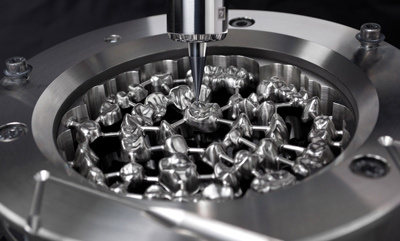
Twins twin of the previous, the Datron C5, with structures almost designed for the operating theatre and others scheme more'conventional' but endowed of elements like linear motorisations, which reach speeds until 90 m/min, allows to mechanise greater pieces of prothetic type for entitle, hips or vertebrae, mandibular arches, etc., reducing likewise the times of manufacture and improving increasingly the quality of the pieces produced. Another example is the new family L 160 of Matsuura in which, in function of the application, can select configurations in 3 and 5 axles and with different ranks of husillos, precisions and speeds. Diverse manufacturers have of scheme of this type, Matsuura, DMG, Hermle, Rodent, etc.
But definitely, and with the sight put en el futuro, one of the technologies more visionarias is the designated hybrid. Inside the sinterizado selective by laser of metallic pieces find us with a phase almost insalvable, the pieces are used to to need some type of back process of finishing, zones more pulidas, better superficial finishing, threads…
For this the Japanese company Matsuura developed his Lumex Advance 25, a hybrid machine that combines a system SLS of metal inside a machine of mechanised, allowing the construction of pieces with own geometry of a printer 3D but with the finishings and the speed of a machine of mechanised.
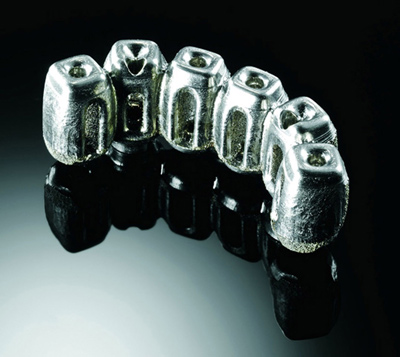
Present and future
At present already are developing a lot of systems inside the two constructive technicians that have quoted.
This is the present.
The future of the implants happens also by the materials. At present already it is investigating, no already in new materials biocompatibles, but in new biomateriales.
The University of of Washington carries a pair of years investigating in a three-dimensional printer of bones, whose material base is a compound of phosphate of calcium with silica and zinc and is able to realise pieces in layers of 0,020 mm.

Another of the pioneering investigations is the llevar by Yong Huang, of the University of Clemson, that has developed a system to print plates of cells, what soon could convert, no already in the impressesion of prosthesis, but of bones and even complete organs.
The technician already exists, will improve his precision, the finishing of the pieces and his resolution, the standardisation of this type of systems abaratará increasingly the costs and will find us with a lower number of rejections and problems postoperatorios, the life of the implants will be greater and the time of minimum adaptation.
Will arrive to the operating theatre, will do us a scanner, manufactured us the piece exactly to our measure, implanted it to us and will go out walking?
That is the future.
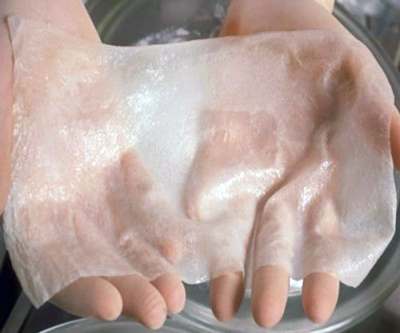
Sources:
Rapid Ready Technology, MedCity News, Zach Hines, EOS, LayerWise, Datron, Matsuura, University of Washington, University of Clemson.