Influence of the aeronautical sector component manufacturing sector component manufacturing materials in the selection of the tools of cut for his mechanised
To finals of the 19th century the aluminium began to use for the manufacture of airships. The brothers Wright, to which attributes them , in 1903, the invention of the first self-propelled aeroplane, already used aluminium for his manufacture. Since until our days the aluminium has followed perfecting by means of new alloys increasingly resistant (like the 7075 T6) and that keep on being widely used in the industry of the aviation, supposing between 20% to 60% (depending of the model of aeroplane) of the materials used in the manufacture of the aircraft. His main application is in primary structures (fuselajes).
At the beginning of the years 40, began to manufacture the first aeroplanes promoted by turborreactores (motors of reaction) conceived to replace to the ones of pistones. This milestone marked also an important development of new alloys that went resistant to high temperatures and to his time that had a high resistance to the oxidation, can say that it was the principle of which today know like superaleaciones or resistant alloys to the heat. The main components of these alloys are the nickel, cobalt, chromium, molybdenum and ironinging (examples of resistant alloys to the heat used nowadays are; Inconel (718, 625, etc.), Hastelloy, Invar, Monel, etc. His main application in the aeronautical sector component manufacturing sector component manufacturing, are the motors of the aeroplanes. Some 10 years later begins the commercial use of the titanium and his alloys (the most common alloy nowadays is the You6To the4V), incorporating also to critical pieces of the structures and of the aeronautical sector component manufacturing sector component manufacturing motors.
At the beginning of the years 60 began to enter the fibre of boron for the use of compound materials, a costly fibre to produce and of applications quite reduced. But to finals of the 60 initiated the production of fibre of carbon and of aramidas, what supposed a big jump in the variety of applications and a very important reduction of the costs of production. The demand by part of the manufacturers of aircraft of materials lighter, joined to the increase of the price of the fuel by the crisis of the oil of 1973, did that every time they had more in account these light and resistant materials, using at the beginning in structures that did not have to bear big loads.
Nowadays, thanks to the big developments that have experienced these materials and the need of saving in consumption of fuel (less weight, less cost), greater environingingmental protection and saving of operations, the composites represent until 50% of the materials in the total of some models of aeroplanes, using for the primary and secondary structures. Some examples of composites are plastic reinforced with fibres of carbon (CFRP), of glass (GFRP), Aramida (Kevlar), PEEK, etc.
Materials more common to mechanise in the aeronautical sector component manufacturing sector component manufacturing industry
- Alloys of aluminium; 2011 (to the Cu), 6061 (to the Mg), 7075 T6 (to the Zn), etc.
- stainless Steels:
or PH's 13/8 PH, 15/5 PH, 17/4 PH, etc.)
or Dúplex and superdúplex (2205, 2304, 2507, etc.)
or Austeníticos (304, 316, 316L, 310, etc.)
or Martensíticos (420, etc.)
- Titaniums and alloys of titanium (You6To the4V, You5553, You 6246, etc.)
- Super alloys or resistant alloys to the heat (Inconel 718, Hastelloy, etc.)
- Composites (CFRP, GFRP, etc.)
Maquinabilidad Of the aeronautical sector component manufacturing sector component manufacturing materials
The term maquinabilidad could define it like the effect that have the properties of the materials, on the ease or difficulty to be mechanised by start of shaving.
The materials that have better maquinabilidad, generally, can consider that they mechanise with parameters of cutting higher (Speed of cut Vc, Advance F, depth of past Ap, lateral load Ae, ) and that precise less power and less strength of cut to realise it and all this with a life of greater tool and obtaining better finishings.
The material that usually takes like reference is the steel AISI 1112, to the that attributes him a maquinabilidad of 100. The chemical composition of this steel is:
- C => 0,13% máx.
- Mn => 0,7% mín. To 1% máx.
- P => 0,07% mín. To 0,12% máx.
- S => 0,16% mín. To 0,23% máx.
The materials with a value of maquinabilidad above 100, means that they are easier to mechanise and what lower was the value, means that more difficult to mechanise are.
Although the factors that influence in the maquinabilidad of a material are many and complexes to determine, could enumerate like some of the most influential;
- the chemical composition
- the thermal sensors conductivity
- the micro structures
- the resistance to the traction
- the hardness and ductility
Even taking into account that they are many the variables and factors that influence in the maquinabilidad, and that do very difficult to obtain a precise table that relate material and maquinabilidad, have wanted to show one in which they appear some of the aeronautical sector component manufacturing sector component manufacturing materials more common to mechanise and his corresponding value of maquinabilidad.
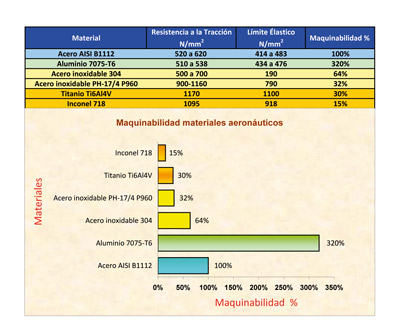
According to the chart of the figure 1, the mechanised of the Inconel 718 would be the one who more difficulty would present to the hour to be mechanised, since it presents the index of maquinabilidad lower and by the contrary the Aluminium 7075-T6, is the one who results easier to mechanise, since it is the one who presents an index of maquinabilidad greater.
Influence of the material in the selection of the tool of cutting (*):
The physical properties like thermal sensors conductivity and others and the mechanics like resistance to the traction, elastic limit, etc. of the materials, are those that determine his behaviour in front of the mechanised and therefore they go us to condition in the selection of the suitable tools and in his conditions of work.
Aluminium and alloys of aluminium
The aluminium is a metal of low density, soft compared with the steel, although aleado can arrive to reach resistances to the upper traction to 600 N/mm2, presents good thermal sensors conductivity, all this does that it was of easy mechanisation.
Milling and turning of aluminium
The most common characteristics of the milling cutters HM integral or plates for the milling and turning of aluminium are: Edges of cutting very sharp, angles of desprendimiento positive, channels of evacuation of shaving, wide (milling), surface of desprendimiento pulida (this is not necessary but favours the mechanised), channels of evacuation polishings, in the milling cutters of hard metal (no necessary but favours the mechanised).
The superficial coating of the tool, is not necessary for aluminiums with low content of silicon (If < 0,5%), although this, will give him greater length to the tool, especially in operations of desbaste. For aluminiums with high content in silicon (If > 10%) and especially for milling cutters of integral hard metal, the coating does almost forced if we want to have a life of greater tool, since the silicon is very abrasive. For the plates of milling and turning, the substrate of the material of cutting (HM) that is used to use, is of big hardness (inside the carbides of tungsten), what allows that they give good performance, even without additional coatings.
The speeds of cut in milling and turning of aluminium (p.And. 7075) with plaquitas of HM pulidas, can arrive to 3.000 m/min. What supposes some 15.165 rpm for a dish of Ø 63 mm or 9.554 rpm for the turning of a piece of Ø 100 mm. The advances also can be high, p.And. In milling with plaquitas, of fz = 0,6 mm (advance by tooth) or of F= 0,75 mm/rev in the case of the turning, all depending on the geometry of the plates, the stability, the past, etc.
For the mechanised of aluminiums with tools of hard metal is necessary to use oils of cut, as first option, or MQL.
The aeronautical sector component manufacturing sector component manufacturing pieces, in a lot of occasions require of some radii of particular ‘agreement' what does that the milling cutters and the plaquitas of milling have to have these radii. Some of the most common radii are: 0,5 - 1 - 1,6 - 2 - 3 - 3,2 - 4 - 5 mm.
Because of the particular geometries of the pieces for aeroplanes, in a lot of occasions requires that the milling cutters offer big variety of long and destalonados of neck, at the same time of a cut 'soft extra' to be able to realise pieces of walls very thin without that these suffer deformations by the strengths of cutting.
stainless Steels
The stainless steels are alloys of steel that contain more than 11% of chromium, that is the element that confers him the protection against the oxidation and the corrosion. Attending to the type of alloy of the stainless steel, can classify them in:
- Ferríticos (430) (hardly used in aeronautical sector component manufacturing sector component manufacturing, by not being so resistant to the oxidation and corrosion, like the rest)
- Austeníticos (304)
- Martensíticos (420)
- Dúplex (2205)
- Toughened by precipitation (PH-17/4)
The stainless as we saw in the figure 1 have greater or minor maquinabilidad depending of the type that are, but generally, mechanise worse that the common steels. The chromium together with other aleantes like the nickel, molybdenum, etc. increase the resistance to the traction, confer him lower thermal sensors conductivity, greater ductility and an endurecimiento by deformation, what translates in more difficulty to the hour to mechanise them.
Milling and turning in to/stainless
The most common characteristics of the milling cutters of HM integral and plates for milling and turning of stainless steels are: edges of alive ‘cut', without arriving to the values for aluminium, angles of desprendimiento positive, but no as much as for aluminium. p.And. For milling cutters of HM integral; Aluminium => 15º To/inox. => 10º, channels of similar evacuation to the ones of common steels. The coatings of the type TIN, TICN, TIALN, CrN, etc. in the case of the tools for To/inox are very important. In these materials, not having coating is synonymous of drastic reduction of the life of the tool because of the high temperatures that generate in the cut of these materials. For the plates of milling and turning, the substrate of the material of cutting (HM) that is used to use is more tenaz that in the ones of aluminium.
The speeds of cut in milling and turning of stainless steel with plaquitas of HM can be between the 60 to 350 m/min depending mainly of the type of stainless. The advances, although they are lower to the used in the common steels, do not owe to be reduced of important form as to do it generates greater friction and more heat. For example: advance by tooth for a strawberry HPC of integral hard metal Ø 12 mm with coating; - in steel F-114 => fz = 0,075 mm - in to/ inox 304 => fz = 0,053 mm.
For the mechanised of stainless steels with tools of hard metal is necessary to use oils of cut like first option, or MQL, although in the case of milling with plaquitas fits the option to do it in dry, only with air, increasing the speed of cut, poe example milling of an AISI 304; - With taladrina Vc = 130 m/min. – In dry Vc = 220 m/min.
In the pieces for aeroplanes, in the To/inox, the same that in the aluminiums, is very common the use of radii of particular ‘agreement' and in occasions also require of milling cutters with long and destalonados of specific neck.
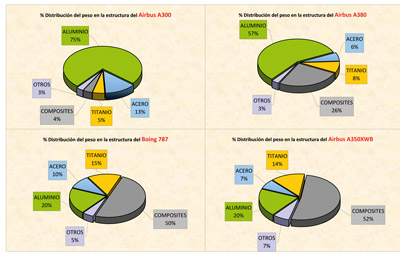
Titaniums and alloys of titanium
The alloys of titanium like the You6To the4V, possess a ratio resistance-weight, without the same, at the same time that a resistance to the greater corrosion that the stainless steels, is also ductile and have very low thermal sensors conductivity. Another property that have is a fast elastic recovery. All this does that the alloys of titanium are more difficult to mechanise.
Milling and turning of titanium and alloys of titanium
To the tools for titaniums can them confer characteristics very similar to the ones of stainless steels, mainly in what to geometry refers (edges of cutting and angles of desprendimiento). The coatings result indispensable of face to the life of tool. The heat generated in the cut of the alloys of titanium is very high, because of his low transmission of the heat, to his high resistance and to the effect of dock that produces the shaving and that does that it remain brushing on the surface of desprendimiento of the tool. The sustrato of the material of cut in the milling cutters of integral hard metal is used to to be equal that for the stainless, the plaquitas of milling slightly more tenaces and however, for the plates of turning are used to to have greater hardness.
The speeds of cut in titanium are quite lower that in the stainless steels, being values very common for example for milling cutters of integral hard metal recubiertas Vc = 60-80 m/min. Regarding the advances, are very similar to the ones of the to/inox austeníticos but with a sustacial reduction of the depth of past.
The use of oil of cut is indispensable, in the case of the titanium.
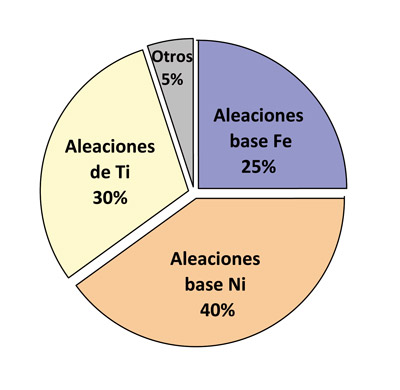
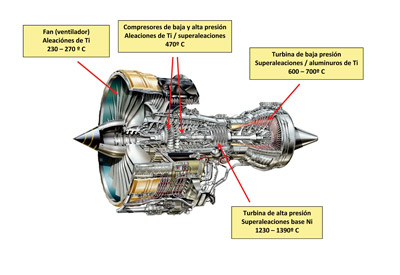
resistant Alloys to the heat or superaleaciones
The superaleaciones more used in the aeronautical sector component manufacturing sector component manufacturing industry are the ones of basic nickel or with high content of Neither, are alloys that keep his properties to high temperatures and that have a high resistance to the traction, to the corrosion, low thermal sensors conductivity, are abrasive and present endurecimiento by deformation. From here that some of them are really difficult to mechanise.
Milling and turning of resistant alloys to the heat
Although some of these materials has a resistance to the high traction, until 1.400 N/mm2, precise of positive edges so that when penetrating in the material, no shop to deform it (and therefore to toughen it) if no to cut it. All the said on the alloys of titanium, would be cost for these materials, except the speed of cutting that in the case of alloys like the Inconel 718, has to be a lot of minor, for example mills of HM integral recubierta; Vc = 30 m/min. The advances in general are slightly inferior to the used in the alloys of titanium (aprox. -20%) and to the equal that in the titaniums the depth of past, has to be reduced with regard to the stainless. Regarding the oil of cut, also is indispensable and has to to be optimised in his percentage to obtain good results.
Composites
The composites are material synthetic composed by two or more components and that characterise because the resultant material is of properties (physical and mechanical) upper to which formed them separately, have very good mechanical properties compared with the traditional metallic alloys, as they can be the derivatives of the aluminium, and besides the compound materials are less sensitive to the corrosion or to the fatigue. They are used to to be abrasive and his mechanised with an unsuitable tool can produce that the fibres separate of the matrix, producing what knows like delaminación. The generation of high temperatures in his mechanised, can cause burns that damage or deform the structure.
Mechanised of composites aeronautical sector component manufacturing sector component manufacturing
Usually consist in milling and taladrados, being much less common the turning.
For the milling of these materials with milling cutters of HM integral, employ milling cutters with geometries and specific angles not to produce the quoted damages in the material, for example exist milling cutters for composites of the type Honeycomb (panels sándwich) with edges of cut in propeller that by the part from above push the material downwards and by the part of down, push upwards, at the same time, to avoid damage the upper layer and the inferior. Generally the edges of cut are more positive that the employees for aluminium and depending of the type of composite, suits that they are protected by coatings that hardly round the edge, being very usual the coating of diamond or directly the milling cutters with insertos of diamond (PCD), although because of his extreme fragility, are used to to be used for operations of finishing or when it requires a good superficial finishing.
The milling of materials composed with plaquitas, employs in operations of desbaste or pieces of big dimensions and not to damage the material suits that they are with suitable edges for these materials (sometimes those that use for milling of aluminium are valid) and pulidas so that the cut was the softest possible and reduce the rozamiento.
The use of oils of cut for these materials can damage them, by what suits informed in the providers of these materials, if possible his use and what cuidar it is necessary to have of face to the protection of the machine, in the case to be able to use them or of face to the personal protection (vacuums of dust and smokes produced) in the case to have to do it in dry with air to pressesure.
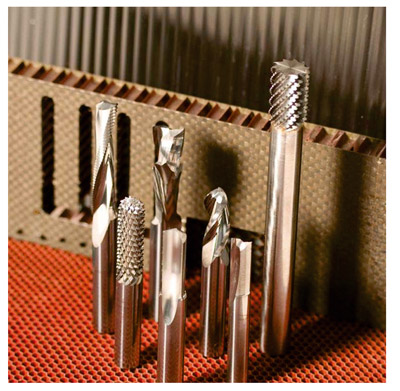

The aeronautical sector component manufacturing sector component manufacturing sector demand of the mechanised each day pieces more complex, of greater precision, with better finishings and in terms of delivery every time lower, this joined to the high cost of some of the materials employed (like titaniums and superaleaciones) and to the long of mechanised that carries to realise some of them, does that the election of the suitable tool, was key. Looking for by these reasons, in the mechanised of aeronautical sector component manufacturing sector component manufacturing pieces, tools that are very reliable, precise, productive and universal, this last characteristic, very important of face to achieve them in terms very short and prices more adjusted.