“En Portugal tenemos un conocimiento al nivel del mejor fabricante de moldes del mundo”
Entrevista a João Faustino, presidente de Cefamol, Associação Nacional da Indústria de Moldes
João Faustino asume la presidencia de la asociación portuguesa Cefamol. Este año fue reelegido presidente por cuarta vez y el mandato concluirá en 2020. Es un gran conocedor del sector de la fabricación de moldes, con la experiencia y el conocimiento que tiene además por ejercer como máximo responsable de su empresa TJ Moldes. Dinamización del conocimiento y cooperación son claves para el reconocimiento de esta industria por la que la asociación vela. Aprovechamos nuestra asistencia a la Semana de los Moldes para hablar con él y que nos desvele los entresijos de la industria que representa.
¿Cómo comenzó la industria de moldes portugesa?
Hace 270 años aproximadamente Portugal fundó su primera fábrica de moldes para vidrio. En aquella época los moldes eran de madera y después, de hierro fundido. No fue hasta después de la Primera Guerra Mundial –antes no existían los plásticos– cuando se creara la primera empresa dedicada a la fabricación de moldes para la inyección de plástico, Anibal H. Abrantes. A partir de aquí muchos profesionales que salieron esta pionera empresa fundaron las suyas y así comenzó la expansión de esta industria. Hoy contamos con 10.000 personas trabajando en el segmento de los moldes de plástico y más de 500 empresas, grandes, medianas y pequeñas dedicadas a su fabricación.
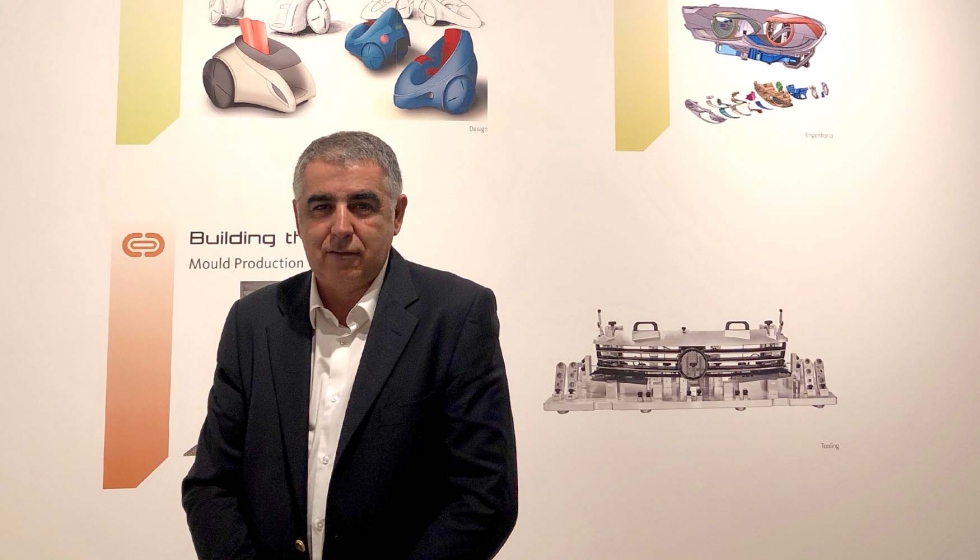
¿Cómo ha cambiado el mercado en los últimos años?
Podemos decir que hemos pasado de un tipo de tecnología más manual a otras centradas en la electrónica. Al inicio exportábamos a Estados Unidos muchos moldes para la industria del juguete, sin embargo, con la apertura de mercados asiáticos la exportación allí paró. Fue en este momento cuando comenzamos a centrarnos más en la industria automovilística, en la automatización, la electrónica o los bienes de hogar, entre otros sectores.
Desde hace quince años mucha producción de empresas en Europa ha acabado en Asia y muchos de esos moldes se han dejado de fabricar. Actualmente Portugal destina a la industria del automóvil un 90% de su producción.
Hace años en la Semana de los Moldes se hablaba del molde procedente de China. Muchas empresas que compraron allí dejaron de hacerlo por su calidad. Sin embargo, vemos como en los últimos 4 años ha crecido su consumo en Portugal y en España, ¿por qué?
Continuamos compitiendo con China. Tiene unos precios atractivos y ya no hay tanta diferencia entre las calidades de los moldes. No podemos competir en precio.
Pero tal vez sí en otros factores.
Es evidente que nosotros nos desmarcamos de los moldes chinos y de otros países dando un servicio técnico impecable y acompañando al cliente. Ayudamos a desarrollar las piezas, colaboramos en todo el proceso, en los montajes... en definitiva, damos un servicio completo. No competiremos por precios pero sí por procesos haciendo más en menos tiempo.
¿Qué tipo de moldes puede producir Portugal en cuanto a tamaño y complejidad?
Competimos con los ‘players’ números uno del mundo. Conseguimos fabricar moldes hasta 120 toneladas, moldes de alto rigor técnico, de una micra, moldes con inyección de agua, con tejido, con aire, con dos, tres y cuatro materiales, por ejemplo.
En cuanto al conocimiento existente, en Portugal lo tenemos al nivel del mejor que existe en el mundo.
Durante la Semana de Moldes se ha hablado de exportación y de nuevos mercados, como México.
Nuestros principales mercados son España, Alemania y Francia. Otros, como la República Checa y Holanda, son también importantes. México ha crecido mucho gracias a las nuevas plantas de automoción que se han instalado en este país. Así, muchas empresas que producen moldes para México tienen la necesidad de tener allí un pequeño taller de reparación o mantenimiento de moldes. Es algo que ya ocurrió hace muchos años y vuelve a suceder ahora. En este momento hay más empresas portuguesas que planean instalarse en México el año que viene.
¿A qué retos se enfrenta el sector del molde con el automóvil como principal destino de la producción?
A grandes retos. En la actualidad hay una gran número de automóviles que no han salido al mercado con normalidad porque los fabricantes dudan si serán productos eléctricos, híbridos u otros modelos. Todo esto está provocando retrasos en el lanzamiento de nuevos modelos.
Debemos estar en las mejores condiciones tecnológicas, de conocimiento y ‘know how’ para enfrentarnos a estos desafíos. Por eso en Portugal hay mucha inversión.
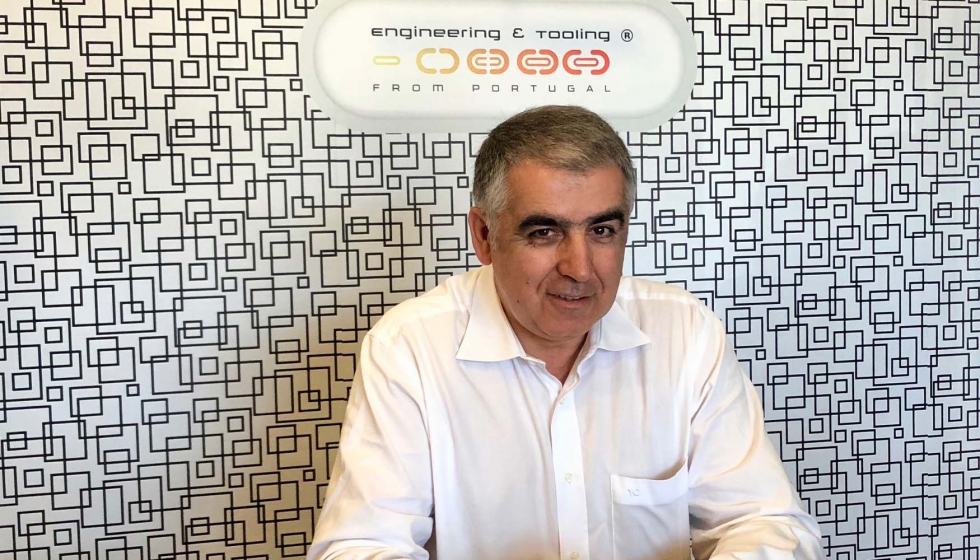
¿También la digitalización en los vehículos se presenta como una ventaja para los plásticos técnicos?
Totalmente. Lo cierto es que en la actualidad se están dando muchos cambios y nos estamos adaptando. Por ejemplo, cada vez más vemos en los talleres máquinas con paletización –algo que no existía hasta el momento–, máquinas que se comunican unas con otras, robots que dan información y trasladan piezas entre máquinas e incluso diversos tipos de acabados de moldes cada vez más finos y rigurosos, para disminuir el tiempo de montaje del molde final. Toda esta política que intentamos desarrollar se dirige a aumentar la productividad de las empresas.
¿Qué papel tiene Cefamol en el sector?
Actualmente tenemos cerca de 170 empresas asociadas, que corresponden más o menos a un 80% de la capacidad productiva instalada. Casi todos los meses llevamos a cabo misiones internacionales a posibles clientes, viajes de vigilancia tecnológica. Ahora en noviembre o diciembre iremos a Indonesia para ver qué sucede allí.
Debemos salir de los mercados habituales para dinamizar nuestra capacidad en los mercados más distantes. Para eso tenemos un plan de formación anual y permanente con temas como la productividad, finanzas, metrología, etc, y formación que realizamos para la empresas para que puedan tener más rendimiento.