Entrevista a Josep Mª Vall, presidente del CIAC
Josep Mª Vall es presidente del CIAC —Clúster de la Indústria d'Automoció de Catalunya— desde finales de 2017. Doctor en Ingeniería Industrial por la Escuela Técnica Superior de Ingeniería Industrial de Barcelona (ETSEIB), ocupa el cargo de consejero en Comforsa. Atrás queda una larga trayectoria profesional en el ámbito de la automoción, sector en el que ha ocupado posiciones de responsabilidad en compañías como Gedia España, Ficosa y Yamaha Motor España. Este bagaje lo capacita para valorar la situación del sector automovilístico hoy y prever los retos que deberán afrontar tanto los fabricantes como sus proveedores. Tomen nota.
Para empezar, me gustaría que pudiera hacer un balance del tiempo que lleva al frente del CIAC y los pasos a seguir bajo su batuta.
Trascurridos los primeros 100 días, y un poco más…, puedo decir que me llevo una grata sorpresa con el gran interés de las empresas en participar: llevamos unos 32 proyectos en marcha y, habiendo estado en gran parte de las comisiones, lo cierto es que hay una gran actividad tanto por número de participantes como por el trabajo que llevan a cabo, con mucha innovación, creatividad y empresas detrás interesadas. Y es que me he encontrado con un grupo de personas con ganas de trabajar y desde el CIAC lo que hacemos es crear el camino, facilitamos el camino para que las empresas puedan seguir adelante.
En segundo lugar, hemos puesto en marcha los grados de ingeniería del automóvil, con la UPC de Manresa y UVic-UCC, con más de un centenar de alumnos formándose, algo excepcionalmente positivo porque significa que hay gente interesada en trabajar en este sector y que las empresas encontrarán personal formado dentro de cuatro años. Por otra parte, también hemos firmado un acuerdo con la Universidad de Girona para realizar un Máster de Logística, que empezará el próximo curso, y que ha generado mucho interés también, lo que me satisface personalmente.
Otro proyecto interesante es el que se está llevando a cabo desde MotorSport2020.cat: el Kart Academy. Implica unos 12-14 centros de formación profesional cuyos alumnos presentarán un kart con todo lo que ello implica; desde el diseño a la compra de piezas y materiales…Y competirán a finales de junio en Montmeló.
Asimismo, también he detectado el gran interés que genera el clúster no sólo entre empresas del sector del automóvil sino de otras disciplinas, que vienen a participar en los eventos organizados, que ponen sobre la mesa diferentes temas de debate. Uno de los últimos, por ejemplo, sobre los retos del coche eléctrico. Charlas que permiten realizar networking y crear redes de conocimiento.
Y durante estos 100 días también me he dedicado a conocer y darme a conocer entre todos los implicados.
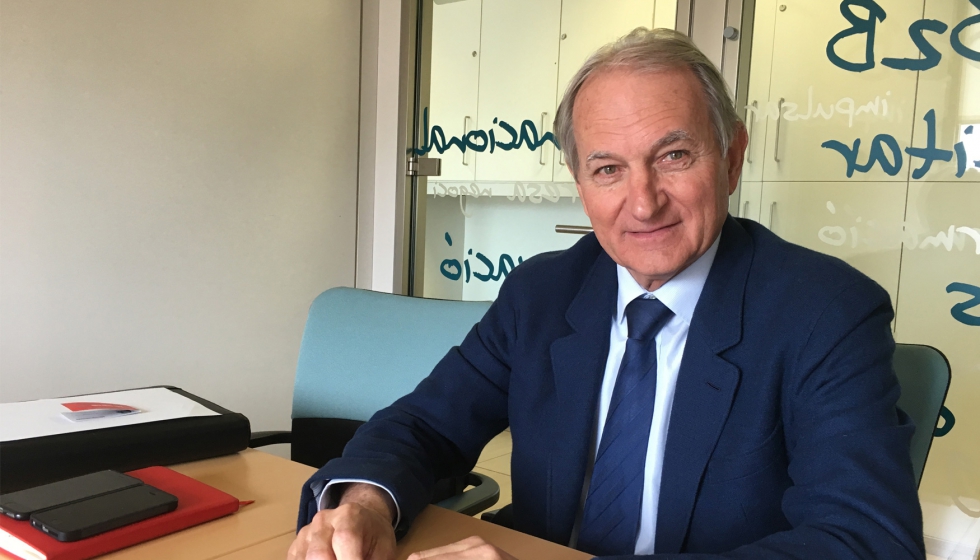
Josep Mª Vall está orgulloso de la preparación de las empresas pero demanda potenciar la formación de calidad y más colaboración de las Administraciones para facilitar el cambio tecnológico.
Ha mencionado dos de los caballos de batalla del clúster desde su gestación… La relación empresa-universidad y la falta de colaboración entre empresas… ¿Parece que vamos por buen camino?
Lo cierto es que las empresas, inmersas en su día a día, tienen poco tiempo para salir… hay que facilitarles reunirse, conocerse, compartir experiencias… y esto es lo que genera el CIAC. Y responden. Tienen mucho interés y participan con representantes que aportan valor y know-how.
Por otra parte, sí es cierto que se requiere de personal cualificado. Hoy el sector de la automoción puedo decir que está en uno de sus mejores momentos, eufórico, no sólo por cómo van las dos marcas instaladas en Catalunya, como son Nissan y Seat sino también por toda la industria auxiliar asociada. Empresas que además exportan en gran cantidad. Están en un momento muy bueno… pero les faltan técnicos, ingenieros y operarios de Formación Profesional hábiles también con las nuevas tecnologías. Y este en un hándicap. Por ello apostamos por una FP Dual, con relación entre las universidades, los centros de formación, los estudiantes y las empresas. Y eso requiere de un esfuerzo para las empresas… pero deben entender que no es tiempo perdido sino una inversión de futuro. Es un cambio de mentalidad que debe hacerse… estamos en ello.
Comentaba el buen momento de las empresas proveedoras… ¿Cuál es la situación de los fabricantes de piezas, componentes e industria auxiliar?
La industria de nuestro país está muy bien preparada y muy bien considerada, también en el ámbito internacional, gracias a la capacidad de sus empleados y a que las empresas han sabido mostrar su potencial de trabajo y lo que son capaces de fabricar. En contra de algunas creencias, aquí no se ensambla, aquí se diseña y se fabrica y se desarrollan proyectos innovadores. Si sólo se apostara por el ensamblaje habría peligro de que la producción se fuera a otros países con mano de obra más barata. Pero no es el caso. Al revés, las empresas instaladas aquí no sólo producen y diseñan si no que, además, aportan a la empresa madre. La industria del automóvil de Catalunya diseña, hace prototipos, preseries… y fabrica.
La tendencia hacia el coche conectado y coche autónomo… implica al fabricante del automóvil, pero también al desarrollador de la tecnología a integrar. ¿Cómo está el segmento de la electrónica?
Hay empresas preparadas y muy bien preparadas para este cambio tecnológico. Incluso empresas que ya han cambiado su producto hacia este mercado. Como pasar de producir cable mecánico a convertirse en una empresa fabricante de producto tecnológico para el coche eléctrico. En el Clúster conocemos varios ejemplos. Sin embargo, hay que tener en cuenta que no será un cambio radical, sino que será evolutivo.
Se prevé que durante unos años coexistan diversos tipos de vehículos…
Por supuesto. Hablamos del coche eléctrico porque es una novedad y porque los fabricantes están apostando por él por cuestiones de regulaciones medioambientales… pero la previsión es que entre 2030-2040 el 30% de los vehículos del parque automovilístico sean eléctricos… ¿Qué será el otro 70%? En mi opinión, convivirán coches eléctricos, híbridos, de combustión y… aunque con menos cantidad, motores diésel. Así que está claro que la industria deberá adaptarse para fabricar piezas para el coche eléctrico, pero también hay que suministrar a los demás… Así que hay tiempo para adaptarse. Lo que sí es cierto es que las empresas deben asumir el cambio tecnológico, habrá cambios en el tipo de trabajo y habrá que adaptar toda la estructura humana a este cambio. Y la Administración debe ayudar a propiciar estos cambios, no mirarlo desde la barrera. Debe facilitar el camino para que las empresas hagan este cambio. No todo termina poniendo normas. Lo vemos en las grandes ciudades. Para reducir los efectos nocivos de la contaminación se están poniendo en marcha una serie de normas para regular el tráfico según el nivel de polución. ¿Eso es todo lo que pueden hacer? ¿Qué ocurre con quién tiene un coche que contamina? Hay que ayudarle a hacer el cambio hacia un vehículo de bajas emisiones. Y ocurre en toda Europa no sólo en España, aunque debemos tener en cuenta que el parque automovilístico español es de los más antiguos. ¿Qué hacer con estos vehículos? Es necesario entender que no basta con regular y aplicar normativas.
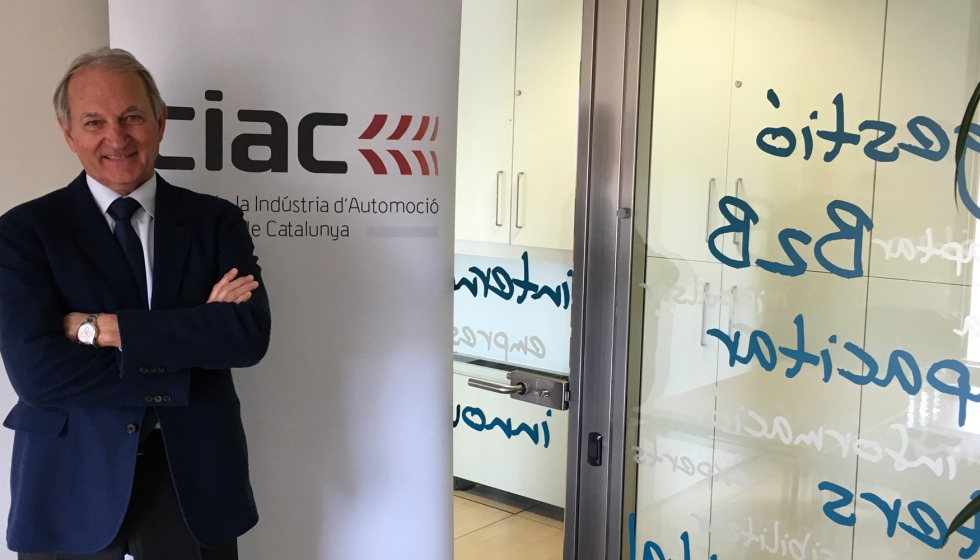
También se exigen cambios en la fabricación de vehículos; menos contaminación, menos pesos, nuevos materiales…
Evidente, y ello demanda de inversión. La industria debe invertir cada año. O muere. Una empresa que no invierte en dos años queda obsoleta. Y la inversión para nuevos materiales, nuevos sistemas… debe contar con la ayuda de la Administración. No es que no exista nada, pero hay que potenciarlo más. Aunque es cierto que la industria, con ayuda o sin ella, tirará adelante.
Sin embargo, tanta exigencia sin subvenciones, ¿no encarece el producto?
Por suerte, no. Y ello es gracias a que las empresas han incrementado su productividad de manera exponencial. En los últimos 10-15 años, por la necesidad de la crisis, las empresas apostaron por adelgazar sus estructuras, pero convirtiéndose en mucho más eficientes. Los nuevos materiales sí pueden encarecer el producto, pero las empresas ahora saben cómo contrarrestar este sobrecoste. Y para ello cuentan con una ayuda fundamental: la Industria 4.0. La digitalización supone para la industria un cambio radical y aquellas que vayan por este camino, mejorarán aún más su productividad y, en consecuencia, sus resultados.
Tenemos la industria preparada, está bien considerada… ¿Qué hay que hacer para mantener este ritmo en positivo?
Hacer que la industria sea importante para los fabricantes. En los próximos años asistiremos a una concentración de fabricantes de automóviles; habrá fusiones y también veremos cómo las empresas TIC serán un nuevo actor entre las empresas fabricantes con la introducción de software, sensórica… Y ante esta situación, las empresas proveedoras de componentes deben ser hábiles para adaptarse. Estando a su lado, saber qué necesitan, desarrollar producto propio o, en caso de que no sean capaces, crear ‘joint ventures’ que les permitan hacerlo. Porque las empresas tecnológicas están cambiando y cambiarán el sector, las necesidades y el modo de entender la automoción. Hoy Google está probando su tecnología en un coche en el que la empresa no ha intervenido. Pero hablamos del coche de Google porque la tecnología es suya. El coche eléctrico es un primer paso para el coche autónomo; al que llamamos el coche del futuro, la sofisticación máxima. Y tras esta evolución deben encontrarse las empresas fabricantes de componentes, de piezas, de moldes…
Precisamente la fabricación de moldes fue uno de los sectores que más sufrió la deslocalización, aunque parece que retorna.
Sí, sin duda. La presión de los fabricantes de automóviles llevó a los fabricantes de piezas buscar proveedores de matrices, moldes y componentes en países asiáticos donde el coste era menor. Pero desde hace unos cinco años, el sector se está recuperando porque se han dado cuenta que lo barato puede salir caro al final. Unitariamente, un molde o una matriz fabricado en Asia está, posiblemente, a un 50% mejor de precio. Pero hay que sumar el coste logístico, que supone un 10% del coste. Y, además, al llegar a Europa, el molde o la matriz había que acabarla por cuestiones de calidad. Lo que supone un 30% más… al final, el margen de diferencia era de un … ¡10%! Y mejorando la productividad es posible competir para este 10%. Y es lo que hizo la industria local. Por ello la producción de moldes y matrices se está recuperando. De nuevo, con competitividad, inversión, creatividad, I+D… Por precio no podremos competir, pero por know-how, sí.