Tecnologías de corte de chapa
Procesos térmicos:
- Oxicorte (de tipo químico)
- Plasma
- Láser
Procesos de erosión:
- Corte con agua
- Corte con agua con abrasivos
Procesos mecánicos:
- Punzonado
- Cizallado
- Aserrado
Oxicorte
Es un proceso de combustión en el que lógicamente se necesitan tres agentes: un combustible, en corte de acero va ser el hierro, un comburente que puede ser el oxigeno y un iniciador de esa combustión que va ser una llama. Por supuesto, el hierro en presencia del aire, donde hay oxigeno, no va a entrar en combustión y necesitamos reunir una serie de condiciones que nos permitan alcanzar una temperatura elevada en el orden de 800º. La llama calentará el material hasta alcanzar esta temperatura y lo lograremos mediante la mezcla de oxígeno con un gas combustible. Esta llama hará el proceso de precalentamiento hasta llegar al proceso de oxidación final.
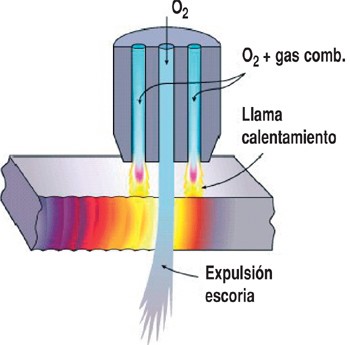
Para que un material pueda ser tratado con oxicorte la temperatura de fusión del óxido debe ser menor a la temperatura de fusión del metal. Esto ocurre con el hierro ya que su temperatura de fusión es inferior a la del propio acero, de modo que se puede cortar simplemente fundiendo el óxido sin fundir el metal.
Este característica no es muy común en todos los materiales, de hecho, en la mayoría de los metales ocurre lo contrario ya que tienen un punto de fusión inferior al del óxido con lo cual se fundirían antes.
Por ejemplo, dos materiales que no se pueden cortar fácilmente mediante oxicorte son aquellos que tienen elementos aleantes como el aluminio, el cromo, o el magnesio, o que tengan un contenido muy elevado de carbón.
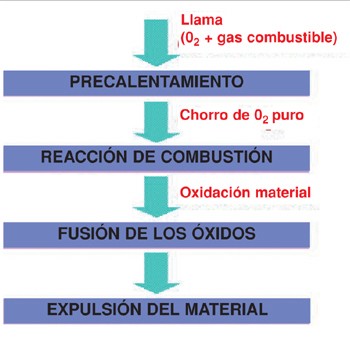
En cuanto al gas combustible que utilizamos para originar la llama que calienta el material, tenemos el acetileno, el propano o el MAPP (abreviación de metal, acetileno y propileno).
Cada una de las empresas dedicadas a producir todos estos gases han ido creando nuevas mezclas y nuevas composiciones de gases buscando que su temperatura y capacidad calorífica sean iguales
El acetileno alcanza una mayor capacidad calorífica y una mayor temperatura frente al resto de gases. Su calentamiento ocurre en el centro de la llama, con lo cual está en la zona que precisamente queremos cortar, por lo tanto puede ser el más apropiado para este proceso de corte.
Existen otros gases como el propano que tienen una temperatura un poco inferior y por lo tanto con un deceso bastante importante de la capacidad calorífica. El MAPP, es un caso intermedio entre el acetileno y el propano con temperatura y poder calorífico intermedios.
Otros gases como el gas natural, tienen una temperatura muy elevada pero tienen un poder calorífico muy bajo y aunque puede que no sirva para la parte inicial del proceso, podría funcionar una vez que éste ya ha empezado y se está realizando el corte, aún teniendo un poder calorífico reducido.
Dentro de las ventajas de este proceso encontramos las siguientes:
- Baja inversión / bajo coste de operación
- Capacidad para cortar grandes espesores
- Uso de varias antorchas simultáneamente: aunque la baja velocidad de corte se ha visto como uno de los inconvenientes, también es cierto que en grandes producciones la máquina de corte puede equiparse con varias boquillas, de tal manera que puede estar cortando simultáneamente piezas similares al mismo tiempo, así que en caso de necesitar una producción acelerada y que el número de piezas sea de series muy grandes podríamos aumentar bastante esta velocidad.
- Buena opción cuando haya operaciones secundarias, como mecanizado posterior o fresado.
- Como inconvenientes encontramos:
- Baja velocidad de corte, teniendo en cuanta la anotación anterior.
- Necesita tiempo de precalentamiento
- La zona afectada térmicamente es grande
- Alabeo de la chapa
- Limitación a aceros de baja aleación
- Problemas con inoxidables y aleaciones de Aluminio
- Tolerancias más amplias que en plasma, agua o láser
Gas | Temperatura Llama (ºC) | Proporción O2/gas | Capacidad Calorífica (kJ/m3) |
Acetileno | 3160 | 1:5 | 18890 |
Propano | 2810 | 4,3:1 | 10433 |
MAPP | 2927 | 3,3:1 | 15445 |
Propileno | 2872 | 3,7:1 | 16000 |
Gas natural | 2770 | 1,8:1 | 1490 |
Corte por plasma
En muchas bibliografías se habla del plasma como un cuarto estado de la materia, sin embrago, el plasma no es más que un gas ionizado, es decir, que conduce la electricidad y que por lo tanto es capaz de alcanzar una temperatura muy elevada, la suficiente como para que al proyectarse sobre una pieza la funda.
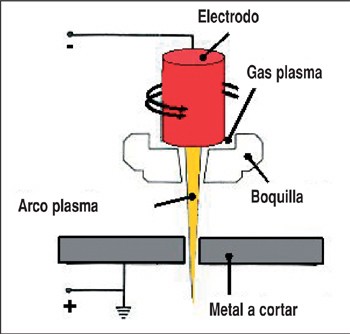
Si se reduce mucho la sección por donde pasa la corriente se estará aumentando la resistencia, provocando un calentamiento del gas alcanzando temperaturas muy elevadas y velocidades muy altas, más o menos la velocidad del sonido.
Este gas caliente es el que se aporta sobre la pieza y es el que consigue la fusión y la propia presión del gas, además evacua ese material fundido por la parte inferior de la chapa.
Una de las principales causas de las investigaciones que se realizan al respecto desde la década de los cincuenta, es la de acelerar el proceso a través de temperaturas más elevadas, por lo cual se han desarrollado varios tipos de procesos dentro del corte por plasma:
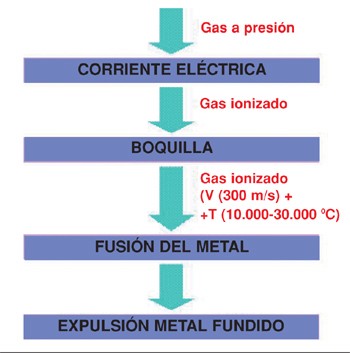
Tipos de procesos:
- Arco transferido / No transferido:
Generalmente es el más usado ya que se precalienta el material y se favorece el proceso de fusión del mismo.
- En seco: tiene varias opciones:
- Sin gas de aportación: se utiliza un solo gas para calentar y fundir la pieza
- Con gas de protección: se inyecta alrededor de la boquilla del método convencional y crea una zona que restringe la proyección del gas ionizado y además la mantiene limpia.
- Aire como gas plasma: favorece la oxidación del material y una reacción exotérmica que generalmente también favorece el proceso.
- Con agua:
- Arco protegido por agua, en vez de utilizar el gas protector en la parte exterior de la boquilla, se utiliza agua inyectada a presión lo que favorece la refrigeración de la boquilla, pieza que sufre bastante durante el proceso por las altas temperaturas. El agua también consigue que esta zona esté limpia subiendo la calidad del corte, y restringe la temperatura en la zona con lo que se acelera la velocidad.
- Arco sumergido
- Reduce el ruido y la radiación ultravioleta
- Evita la formación de humos y gases
- Se reduce la velocidad (10 – 20%)
- Peligro de pequeñas explosiones: debido al hidrógeno, ya que con la pieza completamente sumergida en agua puede presentarse una disociación de la misma, el oxígeno se va por el material fundido y el hidrógeno se deposita sobre todo en la parte inferior de la chapa. Para evitar esto se mantiene el agua en constante agitación.
- Alta definición
Se busca una densidad de energía muy elevada. La densidad de energía es la intensidad de la corriente por centímetro cuadrado y lo que se busca con este proceso es que esté mucho más elevada que con cualquier tipo de corte por plasma convencional. Se consiguen densidades tres veces más altas, del orden de 6000 o 9000 amperios por centímetro cuadrado, acelerando la velocidad de corte. Este proceso compite con el láser para cortar espesores bastante reducidos, tanto en velocidad como en calidad de corte.
La limitación para cortar con plasma es simplemente que el material que se esté cortando sea conductor de la electricidad.
Gases para distintos materiales
Material | Gas de corte | Gas de aportación | Rango aplicación | ||||||
Acero | Aire02 | Aire | 1 a 20 mm | ||||||
Inoxidable | Aire 02,N2, Ar/H2/N2 | Aire, N2+Propano | Espesores >6 mm Alta calidad pieza Grandes espesores+ calidad Grandes espesores | ||||||
Aleaciones | Aire, N2,N2, Ar/H2 | Aire,N2,N2+ propano | Bajo contenido Al, 1 a 3 mm espesor,2 a 19 mm espesor, Grandes espesores |
Corte por agua + abrasivo
Sin embargo, el origen es un poco anterior a eso ya que la primera persona que se encargo de desarrollar el tema del agua como herramienta de corte fue Norman Franz, un ingeniero forestal que trabajaba en el desarrollo de nuevas tecnologías para el corte de madera, llegando a hacer unas máquinas prototipo con las que experimentó intentando alcanzar grandes presiones de agua, bastante mayores de las que se utilizan hoy industrialmente. El problema era que no se podía mantener esa presión de forma continua.
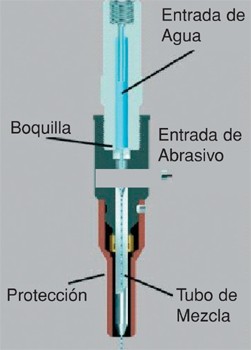
Lo principal es alcanzar una presión muy elevada del agua, una de las máximas que se alcanzan actualmente es de 414 MPa, 40.000 N/cm. La forma de conseguir esta presión es mediante una bomba que se denomina intensificador, que fue introducida por Ingresa Run, y que nos permite alcanzar estas presiones de agua.
El agua a presión se hace pasar por una boquilla muy reducida y se consigue una velocidad muy alta, del orden de 3 veces la del sonido. Esta velocidad tiene como finalidad arrancar el corte. Luego, se pasa a la cámara donde se le añade el abrasivo y así sale por un extremo para cortar el material.
Tal vez uno de los problemas con los procesos de corte por agua es que a medida que avanza el chorro, este se flexiona o electa hacía atrás y hace que la parte superior de la pieza se corte antes que la inferior. Si se hace un corte recto no hay problema, pero si es necesario cortar esquinas interiores tendríamos que avanzar el corte para poder cortar la parte inferior y superior, lo que al final nos puede dar un mal acabado y en algunas aplicaciones se tendría que rechazar el producto.
Otro problema es el de la inclinación de los bordes, normalmente la zona superior que está enfrentada al chorro tiene una abertura mayor que en la parte inferior. El sistema de corte dinámico controla para reducir estos problemas, en este caso, reduciendo la velocidad antes de llegar a las esquinas se evitan estas entradas en la parte superior de la pieza y en el caso de los bordes inclinados se corrige la inclinación de la boquilla.
Sin embargo, este proceso tiene las siguientes ventajas:
- No se origina una zona afectada térmicamente
- Puede cortar cualquier material con amplio rango espesores
- No requiere operaciones secundarias
- Kerf reducido (0,5 – 1 mm)
- Fuerza de corte pequeña (1,4 – 2,3 kg)
- Proceso limpio, sin gases
- Puede realizar agujeros para iniciar corte
- Proceso seguro (baja compresibilidad del agua)
- Corta formas y geometrías de gran detalle
- Finalmente, como otros inconvenientes de este proceso, encontramos:
- Más lento que oxicorte o plasma
- Coste elevado de abrasivo (0,23 kg/min a 1 kg/min
- Ruido
- Inversión inicial elevada (mayor que oxicorte o plasma)
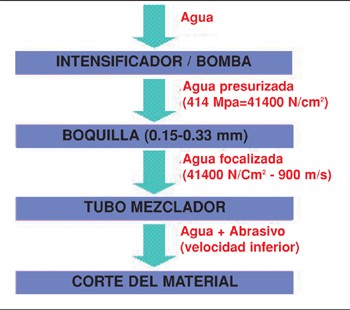
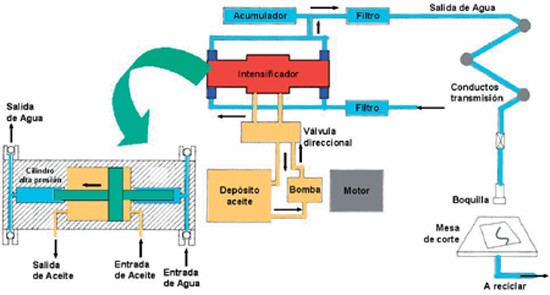
Corte por láser
Todo esto se hace dentro de un resonador que es una cámara con dos espejos en sus extremos en donde rebotan las radiaciones luminosas amplificándose. Uno de estos espejos es semitransparente, en algunas partes refleja el material y en otras lo deja pasar.
Para conducir este láser a la zona que queremos cortar se usan los espejos deflectores y una vez que llega al cabezal de zona se focaliza reduciendo el diámetro del haz con el fin de aumentar la potencia y por tanto la temperatura.
Algunos tipos de láser de los que más se habla industrialmente son:
Láser de CO2
- Su medio activo son moléculas de CO2
- La excitación del medio se realiza mediante corriente eléctrica
- La radiación emitida es de 10,6 mm
- Requiere espejos para conducir el haz láser = Mayor complejidad
- Tiene un mayor coste y mayor mantenimiento
- Potencia de 1500 a 6000 W
- Es muy usado industrialmente (85%)
Láser Nd:YAG
- Su medio activo es un cristal de granate de Itrio y Aluminio (YAG) dopado con iones de Nd
- El medio activo se excita mediante lámpara flash de alta intensidad
- Radiación emitida es de 1,064 mm (Se conduce por fibra óptica)
- No requiere espejos para conducir el haz láser
- Interactúa mejor que el láser de CO2 con materiales como: aceros galvanizado, Al, Cu, Latón, etc.Potencia de 2550 a 4500 W. Poco usado industrialmente del proceso de corte por láser de Nd:YAG
Entre las ventajas del proceso de corte por láser encontramos las siguientes:
- Más rápido que plasma de alta definición
- Corta perfiles de forma compleja
- Elevada precisión y calidad de piezas cortadas (sobre todo en espesores
- pequeños y medianos)
- Kerf reducido
- Zona Afectada Térmicamente muy reducida
- Variedad de materiales a cortar
- Algunos inconvenientes de este proceso son:
- No puede cortar materiales reflectantes (Al, Cu, etc.)
- Velocidad reducida para espesores < 3 mm
- Inversión inicial elevada (en comparación con oxicorte, plasma o agua)
- Inversión alta / Coste elevado de consumibles (boquillas, electrodos)
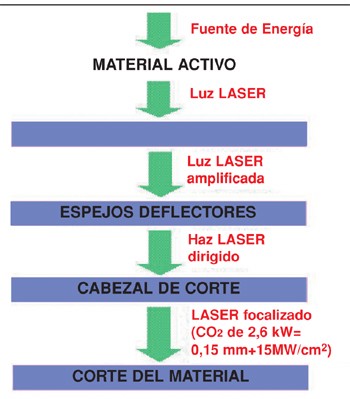
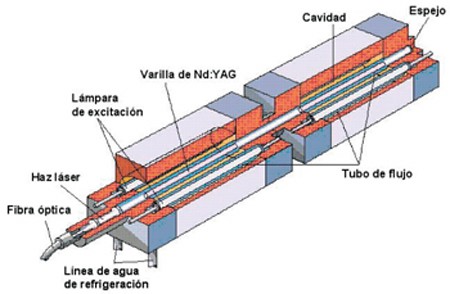
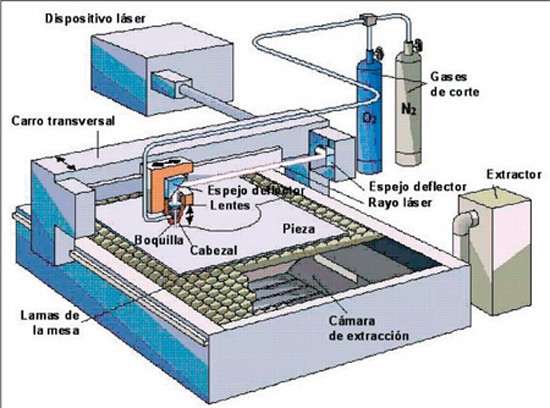
Corte por punzonado
La compresión del material genera una deformación, a medida que avanza la penetración del punzón en el material se inician grietas en los bordes de contacto entre el punzón y la pieza y la matriz y la pieza, y a medida que avanzan esas grietas se produce una rotura o fractura que hace que se separe la chapa del material de recorte, coinciden las dos grietas y el punzón sigue penetrando hasta provocar la expulsión del material cortado.
Entre las ventajas de este proceso encontramos las siguientes:
- Permite cortar y además operaciones de conformado
- Más barato que el Láser para el corte de golpes sueltos (tiempos = décimas segundo)
- En la actualidad hay máquinas de mucha velocidad (1200 golpes/min en punzonado
y 2800 golpes/min en mascado)
Inconvenientes:
- Requiere operaciones secundarias de acabado (cuello de botella)
- Problemas para cortar espesores muy elevados (agujeros de gran diámetro)
- Coste de herramientas y reafilado
Para finalizar, no podríamos decir con exactitud cuál de todos los procesos anteriormente citados es la mejor tecnología de corte, tal vez lo que tendríamos que tener en cuenta son los siguientes datos de referencia para elegir el que más se adapte a nuestras necesidades:
- Tipo de material a cortar
- Espesores de corte
- Velocidad de corte
- Acabado pieza cortada
- Precisión
- Zona afectada térmicamente
- Necesidad de operaciones secundarias
- Complejidad de la pieza a cortar
- Costes de operación
- Inversión necesaria.
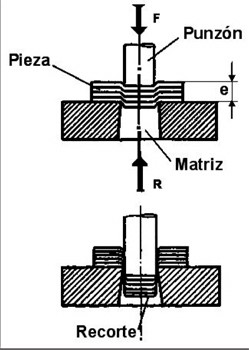
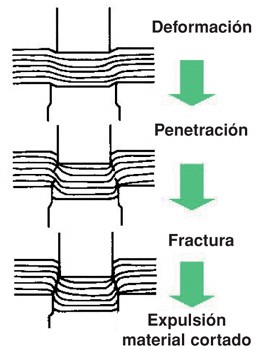
Comparación final
Material | Oxicorte | Plasma | Plasma alta definición | Agua Abrasivo | Láser CO2 | Láser Nd:YAG | Punzonado |
Acero al C | 500 | 90 | 13 | 180 | 20 | 10 | 10 |
Inoxidable | - | 90 | 13 | 100 | 12 | 10 | 10 |
Aluminio | - | 150 | 13 | 180 | 10 | 5 | 10 |
Cobre | - | 60 | 13 | 100 | - | 5 | 10 |
Níquel | - | 75 | 13 | 75 | 10 | 10 | - |
Titanio | 300 | 75 | 13 | 180 | 10 | 10 | - |
Madera | - | - | - | 100 | 25 | - | |
Papel | - | - | - | - | V | - | V |
Polímeros | - | - | - | V | 2 | - | V |
Vidrio | - | - | - | V | 2 | 2 | - |
Cerámica | - | - | - | 2 | 2 | - | |
Goma | - | - | - | V | 10 | - | V |
Material | Espesor (mm) | Velocidad (mm/min) | ||||
Oxicorte | Plasma | Agua | Láser CO2, (1 kW) | Láser Nd:YAG,(0,8 kW) | ||
Acero | 5 | 700 | 4500(*) | 200 | 2200 | 600 |
20 | 400 | 2000(*) | 50 | - | ||
Inoxidable | 3 | - | 5000(*) | 200 | 6500 | 900 |
40 | - | 500(*) | 10-20 | - | ||
Aluminio | 2 | - | 6000(*) | 800 | 1000 | 1200 |
40 | - | 1200(*) | 80 | - |
(**) Ar/H2 y 240A
(***) Potencia láser = 1000 w