Entrevista a Oliver Stammen, jefe de ventas en Thielenhaus Technologies
En la actual era de la miniaturización cada vez se da más importancia a la perfección geométrica en los componentes. Como especialista en acabado, no sólo debe preocuparse por la topografía de las superficies, sino también por las formas geométricas. ¿Qué problemas se plantean hoy en día a la hora de cumplir las exigencias?
Por lo general, las dificultades radican en las exigencias geométricas indicadas en los bocetos y en los márgenes de tolerancia, que cada vez son menores. Si, mediante su proceso actual, los encargados no logran mantenerse dentro del margen de desviación permitido, deberán buscar un proceso alternativo o una forma de optimizar el proceso ya existente.
Por motivos económicos, las pequeñas empresas se están decantando por una optimización del proceso antes que por una nueva inversión. En este sentido, ¿no se están introduciendo en un terreno mucho más complejo?
En realidad, sí. Por ello, primero deberían analizar el esfuerzo necesario para adaptar sus procesos tradicionales a las exigencias. Entre otras cosas, se deben considerar la cualificación de los operarios a cargo de las máquinas, los costes de las herramientas necesarias para cumplir el grado de exigencia más alto, la ampliación de los ciclos de trabajo, el incremento de recursos para el control de calidad y, en ocasiones, también los ciclos de ajuste y una tasa mayor de defectuosidad. Finalmente, se debe garantizar la capacidad de reproducción de las mismas condiciones en todo el lote de componentes. Los procesos existentes se pueden forzar, pero siempre dentro de unos límites.
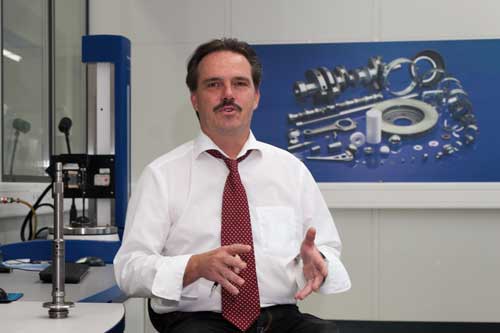
Dentro de esos límites, ¿no es más razonable ampliar la cadena de procesos con una operación más de mecanizado?
En principio, la empresa debe comprobar si el material de que dispone está bien empleado. En este sentido, se debe tener en consideración que las exigencias de calidad no van a desplomarse en el futuro, sino que seguirán aumentando e irán surgiendo criterios de valoración adicionales, como por ejemplo el análisis de Fourier. Por supuesto, una operación adicional también incrementa los costes unitarios y, a menudo, los resultados de esa inversión no se pueden evaluar en base a un solo pedido, en especial en los casos de empresas proveedoras.
¿Cuál cree usted que es la solución a ese problema?
Cuando existe el peligro de que un proceso existente se lleve más allá de los límites, se debe descartar como objetivo principal la ampliación de la cadena de procesos con una máquina especial. En ese caso, lo primero que se debe intentar es una combinación de métodos. En el caso más simple, esto consistirá en la integración de una máquina de Microfinish en la máquina-herramienta ya disponible. Si esto no fuera posible, es más rentable invertir en una máquina de acabado flexible y que incorpore la tecnología más moderna, que pueda configurarse de forma sencilla para el desempeño de otras tareas. Por ejemplo, nosotros hemos desarrollado sistemas modulares que el propio encargado puede adaptar para la realización de otras tareas mediante la conexión o desconexión de los módulos. De este modo, se posibilita la combinación de procesos. Además, dado que la reutilización de estas máquinas en el mercado es considerablemente mayor debido a su flexibilidad, también gozan de una mejor valoración entre los bancos de crédito, lo cual lleva a unos costes de financiación más bajos en comparación con las máquinas especiales.
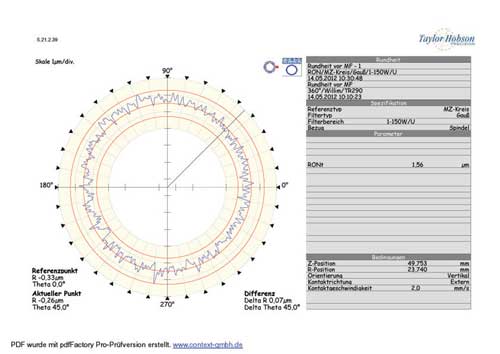
¿Qué problemas relacionados con la geometría afectan a las empresas en la práctica?
Nuestras máquinas se utilizan con más frecuencia para conseguir mejoras en la planicidad durante el alisado; en la circularidad de los componentes ondulados y cilíndricos, así como de las esferas y casquetes, y en la rectitud, por ejemplo, de los caminos de rodadura de los rodamientos.
¿Qué novedades aporta el método de Microfinish?
Este método, que lleva probando su eficacia ya desde hace décadas y que aun hoy en día sigue evolucionando, garantiza la más alta precisión geométrica y las tolerancias dimensionales más ajustadas en el tiempo de mecanizado más reducido, de forma que el esfuerzo habitual de clasificación y emparejamiento puede eliminarse. Hablamos, en este caso, de eficiencia geométrica. Según nuestras necesidades y los parámetros que introduzcamos, el método de Microfinish garantiza acabados uniformes que, a menudo, rondan un valor Ra de 0,05 µm y superficies de contacto con una Rmr hasta un 99,99%. Debido a la baja temperatura de trabajo, la estructura superficial de las zonas periféricas es, tras el mecanizado, considerablemente más resistente que antes. De este modo, mediante la creación de estructuras planas, se puede influir de forma directa, por ejemplo, en las propiedades de fricción y deslizamiento importantes en el plano de la eficiencia energética.
Un grupo de investigadores fineses y americanos del sector automovilístico ha calculado, por ejemplo, que tan sólo un quinto de cada litro de combustible se destina a la propulsión del vehículo. El resto se pierde en forma de calor y fricción en el motor, hasta un 35%, y en los engranajes, hasta un 15%. En el futuro, con el objetivo de evitar estas pérdidas, seguramente se reducirán de forma drástica los márgenes de tolerancia de los componentes correspondientes, lo cual hará que el acabado de superficies tome una gran importancia. En los demás sectores, las medidas que se implanten en relación con la eficiencia energética también desembocarán en un grado mayor de exigencia con respecto a las piezas de trabajo.
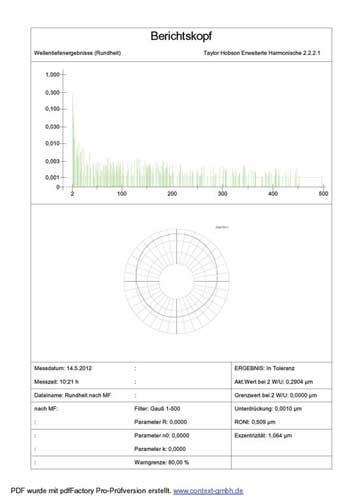
¿Tiene este método alguna ventaja más?
Sí, ya que todos los métodos de mecanizado convencionales tienen límites que dan como resultado una desviación de la forma matemática óptima. Esos límites se eliminan en gran parte con el uso de Microfinish, porque este método superpone los movimientos del mecanizado. Al conseguir el mayor solapamiento de herramienta y pieza de trabajo posible, podemos, por ejemplo, eliminar la deformación en los cojinetes de un eje. Además, también se hacen posibles perfiles logarítmicos y estructuras superficiales de gran complejidad. Debido al mecanizado, también aumentan considerablemente las tensiones de compresión propias positivas en la superficie, de modo que esta se vuelve más resistente. Los componentes pueden, de este modo, hacerse más pequeños a la vez que mantienen la misma resistencia. Eso y la minimización de los valores de fricción son los factores clave para la eficiencia energética que tanto se fomenta en todos los sentidos hoy en día.
Además, nuestro método consigue minimizar los ruidos, eliminarlos e incluso adaptarlos según las necesidades. Estas exigencias se multiplican con el tiempo, y no sólo en lo que se refiere a las piezas de los engranajes y las piezas de dirección. Los ruidos se originan por las vibraciones y, en base a un análisis de Fourier, se pueden eliminar las vibraciones en las áreas más complejas mediante un mecanizado directo de las mismas. En este sentido, cuanto menos se desvíe un componente de su forma geométrica óptima, mejor será el valor de vibración.
O, por ejemplo, una superficie puede necesitar brillo especular para usarla como base para circuitos impresos integrados, es decir, que la pieza de trabajo se convierte en una placa. Incluso se pueden utilizar esos brillos especulares o marcas de micromecanizado voluntarias para crear efectos interesantes y mejorar el tan importante diseño en los productos de alta calidad.
Volvamos al tema de las vibraciones, ya que no sólo originan ruido sino que, además, debido a las interferencias que provocan, pueden tener un efecto negativo en la vida útil del componente aislado o de todo el conjunto. Ilústrenos con un ejemplo de las diferencias en este sentido entre el método de mecanizado con Microfinish y un método convencional.
Pongamos, por ejemplo, una pieza ondulada con cojinete como un eje en un engranaje: en principio, un cilindro con una caída definida en los bordes. La pieza de trabajo presenta a menudo una dureza de aprox. 58 HRC. Los métodos de mecanizado típicos para el cojinete son el torneado y el rectificado. Durante el torneado, se produce un contacto más o menos puntiforme entre la cuchilla y la pieza de trabajo, mientras que durante el rectificado ese contacto es lineal. En ambos métodos, tan sólo es posible un solapamiento de la herramienta muy bajo. La ventaja es un volumen de virutas muy alto; sin embargo, también existe el inconveniente de que las pequeñas vibraciones se marcan sobre la superficie de la pieza de trabajo y la deforman. Ahora, estas vibraciones pueden contrarrestarse integrando guías con atenuadores, grandes medidas en la bancada de la máquina y cojinetes hidrostáticos al construir la máquina, lo cual, naturalmente, la encarece considerablemente. De este modo, se consigue que las vibraciones se ajusten a unos márgenes de tolerancia menores, aunque no se eliminan por completo. Después de todo, las vibraciones también se originan en la propia pieza de trabajo, que tiene su propia respuesta de resonancia.
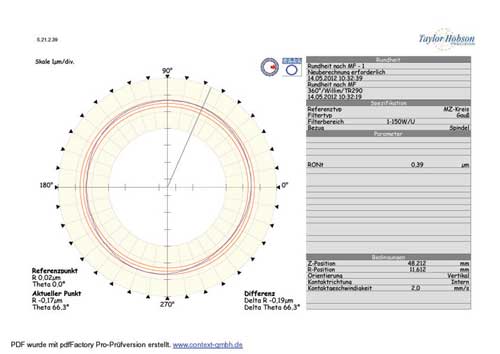
En los casos más extremos, ¿se forman marcas de vibración?
Sí, en esos casos, hablamos de vibraciones con una amplitud alta. Sin embargo, también las vibraciones de amplitud baja, es decir, con senos de dimensiones micro o nanométricas, desempeñan un papel en la producción de ruido y la vida útil del componente mecanizado. Por lo tanto, si se desliza un rodamiento de agujas por la superficie del cilindro, la aguja establece un contacto lineal con la ondulación. Ésta se acelera durante el rodado del cojinete de forma radial. Dicha aceleración, que puede ser de intensidad variable, produce tanto ruidos como un mayor desgaste. En los procesos de contacto lineal o puntiforme, esto no se puede evitar.
¿Cómo se puede evitar este inconveniente?
Si se selecciona una herramienta que establece un contacto superficial amplio con respecto a la pieza de trabajo, como la presión de una semicoquilla sobre el cojinete, las vibraciones no se pueden marcar en forma de ondulaciones o se consigue eliminar la deformación ya existente, porque, en principio, con la semicoquilla sólo se aplanan las crestas de las ondulaciones. En el método de Microfinish, la herramienta oscila además de forma axial. Gracias al solapamiento de estos movimientos y en combinación con la rotación de la pieza de trabajo, se fuerzan una micro y macrogeometrías muy altas. En este sentido, se utilizan herramientas de cinta con placas de compresión o herramientas de piedra ajustadas con distintas uniones y punzones según las necesidades.
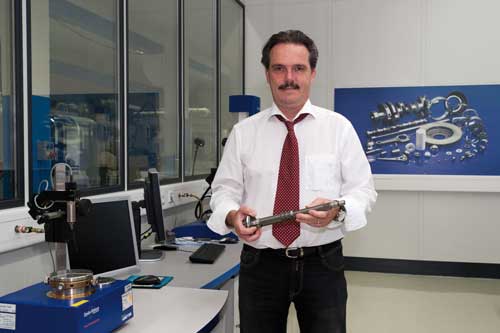
¿Qué resultados se pueden alcanzar?
Los resultados dependen, naturalmente, de la calidad del premecanizado. Sin embargo, se pueden conseguir irregularidades geométricas, por ejemplo, en cuanto a circularidad y forma cilíndrica, de menos de 1 µm. A esto se añade el análisis de Fourier y, como resultado, se influye de forma positiva en la emisión de ruido. Todo esto podemos demostrárselo con piezas de trabajo en máquinas reales a los interesados en este método y documentarlo con las mediciones correspondientes. Además, se pueden crear muestras límite para todas las piezas de trabajo, mediante las cuales se compruebe hasta qué punto se mejoran los procesos existentes y se optimizan sus costes, sin influir negativamente en el resultado final.