Soluciones de software para impresiones 3D
La fabricación aditiva revolucionará la industria de la fabricación a medio-largo plazo. Las novedades diarias en materiales —metales, termoplásticos, cera, polvo de mármol, etc.— y en impresoras propician el crecimiento y explosión de esta tecnología en numerosos ámbitos. En su estudio global acerca de impresión 3D del año 2016, Enerst&Young [1] señala que el 24% de los directivos de empresas del sector fabricación, logística y energía consideran la fabricación 3D como tecnología estratégica dentro de su empresa. Este dato se ve respaldado con el estudio de Gartner [2] 'Qué supone la impresión 3D en tu cadena de suministro' de marzo 2016, en el que se concluye que el 65% de las empresas invertirá en fabricación 3D en los próximos 2 años y solo un 10% asegura no tener intención de utilizarla.
La fabricación aditiva se enfrenta a dos retos cruciales para consolidarse como esta revolucionaria tecnología que pretende marcar el futuro de la fabricación. El primero, la garantía de la calidad de los productos fabricados. El segundo, y más difícil de llevar a cabo, la integración con los demás procesos de la cadena de producción. Dentro de una cadena de producción en la que se integra la impresión 3D, las fases de diseño, planificación, fabricación y control no están debidamente conectadas. La figura 1 muestra cómo debería ser esa integración: todos los actores participan en el proceso e intercambian información para optimizar el funcionamiento global.
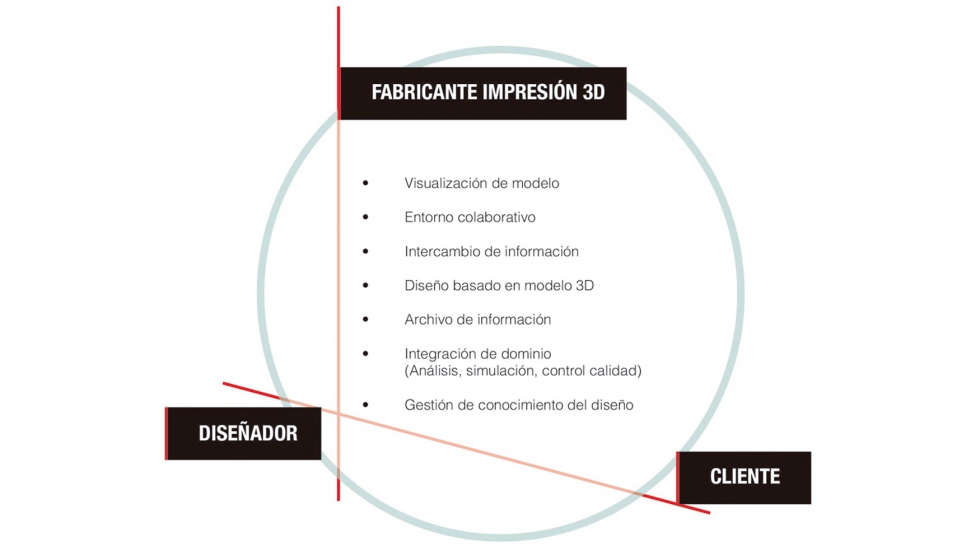
La principal limitación viene determinada por la necesidad de las impresoras 3D de trabajar, a la hora de definir formas, con archivos.stl, un formato de diseño asistido por ordenador (CAD), basado en superficies definidas mediante triángulos desestructurados, definidos por los vectores normales a su superficie y la posición de los nodos. Las impresoras de fabricación 3D trabajan por capas, por lo que, para todo el rango axial de una pieza necesitan tener el contorno cerrado 2D.
Por otra parte, los diferentes sistemas de la cadena de producción están aislados con muy pocas o nulas opciones de integración o interoperabilidad con el resto de soluciones. Por ejemplo, los modelos CAD basados en el estándar STEP están orientados a procesos de fabricación sustractivos o de corte, donde las propiedades del material son invariables en todo el volumen y en los que es complicado introducir cavidades que permitan generar los beneficios de la impresión 3D. El intercambio de datos geométricos 3D al integrar un sistema de digitalizado para el control de calidad o hacer ingeniería inversa donde se trabaja con nubes de puntos grandes (>10 millones) supone otro problema, y es necesario trabajar con triángulos curvados para reducir el tamaño de los archivos o introducir el concepto de voxeles texturizados que no soporta el actual formato *.stl.
Dentro de este contexto, la figura 2 muestra cuál es el proceso completo para la integración de la fabricación 3D en una línea de producción. Esta línea está formada por distintas etapas: el punto de partida es el diseño de producto; a continuación, es necesario planificar el proceso y proceder al análisis de materiales mediante la simulación de las propiedades térmicas y mecánicas del producto final. La siguiente fase incluye la fabricación en sí misma con el correspondiente control de calidad dimensional y mecanizado, si fuese necesario. El proceso completo se ve retroalimentado con un control de calidad para la mejora continua.
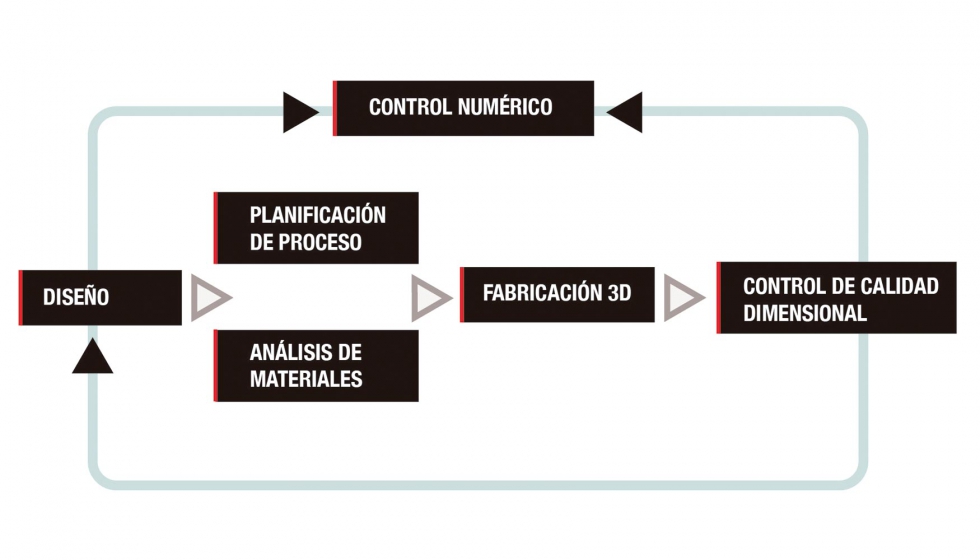
Para dar solución a la problemática actual, la industria está trabajando en tres direcciones: la primera medida es la estandarización del intercambio de información. El estándar ISO STEP es uno de los más utilizados en el sector de la automoción y el aeroespacial. Permite la descripción de producto en datos que se pueden intercambiar con otras herramientas y guardar en bases de datos. De la unión de los estándares AP 203 y AP 214 se ha creado el STEP 242 [3] cubriendo el diseño eléctrico, las geometrías 3D, el diseño compuesto, el mecánico y los datos de gestión de producto. Otra opción que se maneja es la implementación del estándar QIF (Quality Information FrameWork [4]) dentro de todo el proceso, para que la información sea compartida en archivos XML estructurados en tablas con la definición de la pieza y sus atributos principales.
En segundo lugar, surge la necesidad de crear un archivo propio para impresión, como el formato *.AFM (Additive Manufacturing File Format), un estándar basado en lenguaje XML que permite la descripción de la forma y composición de los objetos 3D. El hecho de que permita la definición del color, los materiales, los tipos de redes, etc… lo hace mucho más funcional para la integración de la fabricación aditiva en aplicaciones de producción industrial.
Y, por último, es imprescindible la integración del control de calidad dimensional, ante la cual surgen dos posibles soluciones: la primera, para aquellas aplicaciones en la que los lotes sean pequeños o la fabricación aditiva no sea la tecnología fundamental, existe la posibilidad de acudir a servicios de control de calidad dimensional, como M3WorkSpace de Innovalia Metrology, en el que metrólogos expertos realizan las mediciones y envían el informe en formato estandarizado con un contenido personalizado. La segunda posibilidad es la integración de sistemas de digitalizado 3D de alta resolución (al menos 1 orden de magnitud menor que la resolución de la impresión 3D), como M3 Portable [5], que con los sistemas de impresión, permite la automatización y personalización del proceso, gracias a su adecuación a los estándares mencionados en las instalaciones del fabricante.
Ambas soluciones deben ser compatibles con el estándar STEP 242 para que la extracción de los datos metrológicos de la pieza sea posible. De esta forma, se agiliza el proceso de digitalizado, extracción de información y reporte, haciendo posible su integración directa en el modelo.
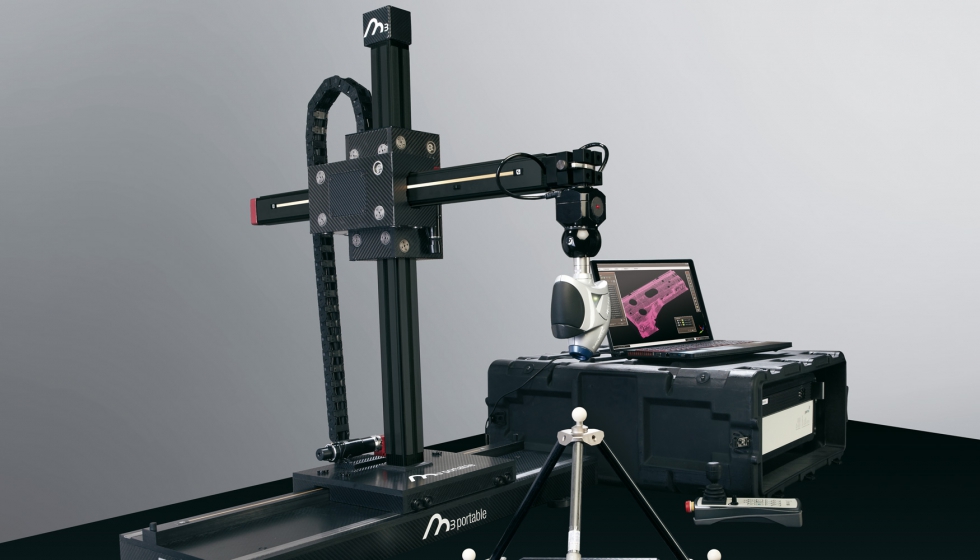
La fabricación 3D es una tecnología en pleno desarrollo que ofrece una gran variedad de oportunidades debido a su flexibilidad en cuanto a materiales y formas pero, para que su implementación como tecnología de producción sea posible, necesita mejorar su comunicación con el resto de procesos: diseño, planificación y control de calidad. Para ello, se trabaja en soluciones de software como la estandarización del intercambio de la información mediante STEP 242 y QIF o la implementación de formatos de archivo propios para la impresión que incrementen la información sobre la pieza y permitan la explotación de las capacidades técnicas. Además, es importante tener en cuenta que los equipos de impresión deben estar integrados o sincronizados con equipos/servicios de digitalización que controlen la calidad dimensional, permitiendo así la verificación del producto final y la mejora del proceso a todos los niveles, desde el diseño a la producción.
Referencias
[1] EY’s Global 3D printing Report 2016
[2] What 3D Printing Means for Your Supply Chain. GARTNER (01 March 2016 ID: G00298100)
[3] Whitepaper Development of STEP AP 242 ed2 “Managed Model Based 3D Engineering”
[4] http://qifstandards.org/
[5] ISO / ASTM52915 – 16: Standard Specification for Additive Manufacturing File Format (AMF) Version 1.2
[5] http://www.m3portable.com/en/