El mecanizado del sector del automóvil puede aplicar presión usando los refrigerantes de una manera más estratégica
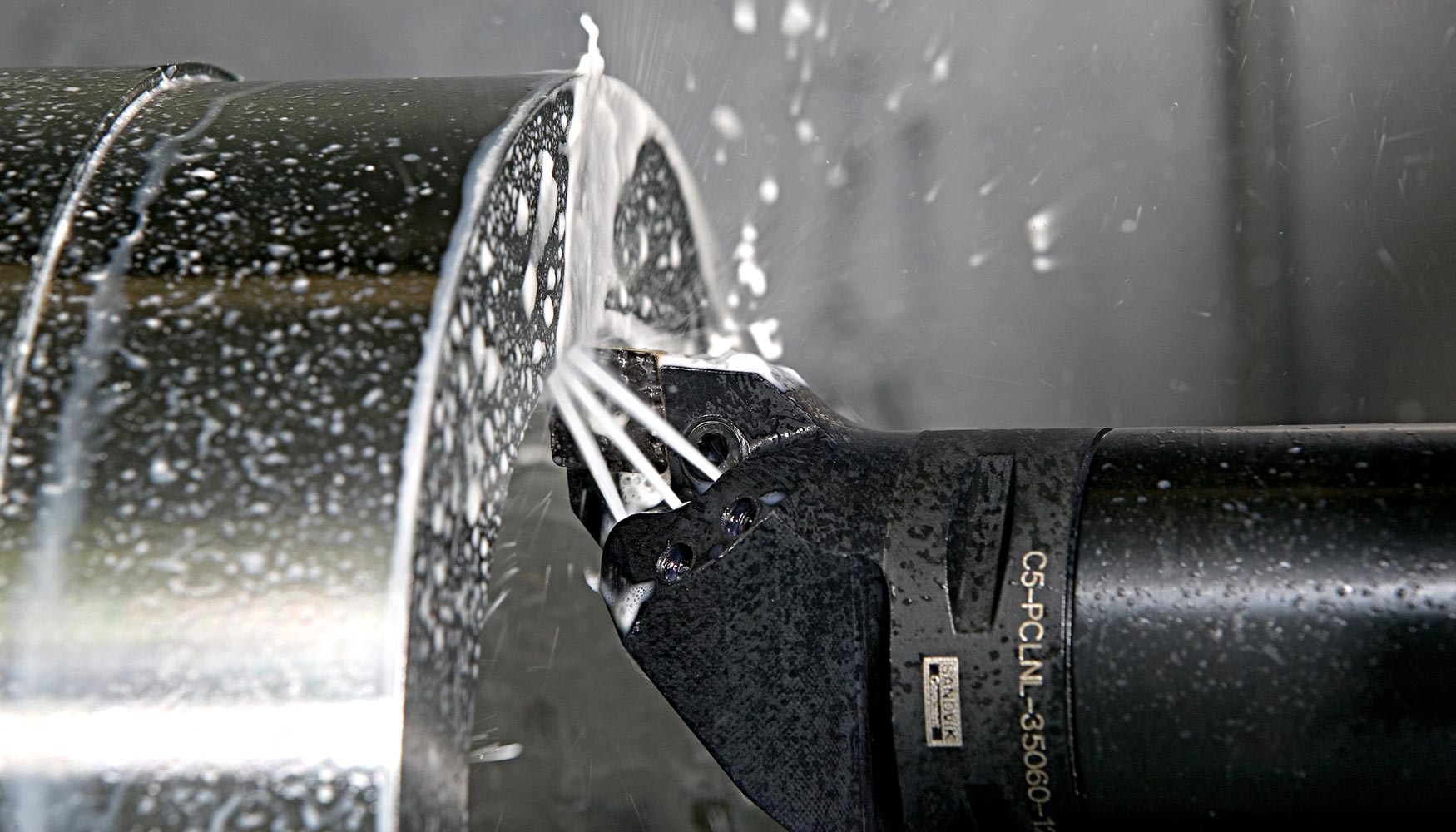
Muchos talleres de máquinas han usado hasta ahora el refrigerante de una manera convencional, dirigiendo un tubo hacia la zona de mecanizado para inundarla, incluso en el caso de los materiales que requieren la presencia de refrigerante durante su mecanizado, como las aleaciones de titanio y las superaleaciones resistentes al calor. El método actual consistente en aplicar el refrigerante a alta presión aporta ventajas nuevas y no solo mejora la eficiencia de torneado de aceros muy dúctiles, sino también de los que se usan, por ejemplo, en las transmisiones.
Ya no basta simplemente con aplicar un chorro de refrigerante ni con inundar con este la zona de mecanizado. Para aplicar los refrigerantes con eficacia y justificar su participación de hasta un 15% en el coste total de la pieza es preciso que marquen una diferencia real en el mecanizado moderno. Los refrigerantes se deben usar en forma de chorros laminares con presión, en un volumen suficiente y dirigidos con exactitud hacia el lugar correcto. La aplicación de refrigerante a alta presión (HPC) conlleva una diferencia notable en términos de:
- distribución del calor
- formación y evacuación de la viruta
- empastamiento del material de la pieza de trabajo en el filo
- desgaste de la herramienta
- integridad superficial
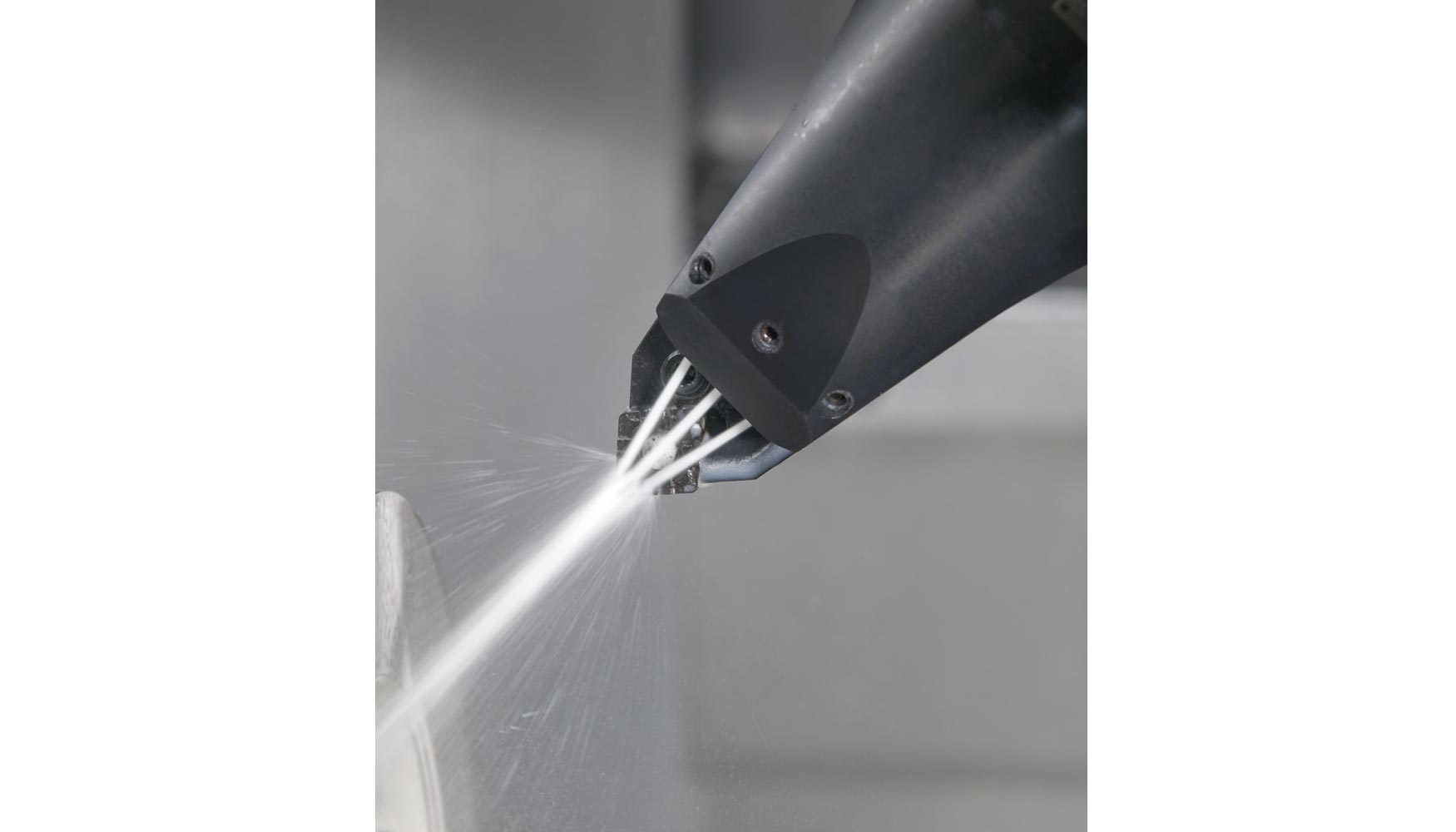
Ya en los años 80, Sandvik Coromant empezó a explorar las posibilidades y a desarrollar las primeras versiones de un sistema de refrigerante a alta presión. Estas se basaban en la investigación de chorros de refrigerante dirigidos con precisión y a altísimas presiones (100 a 1.000 bar) y pasaron a formar parte de las herramientas usadas para mecanizar materiales exigentes en cuanto a mecanizabilidad y control de viruta. Los chorros de refrigerante fuerzan su paso y crean así una cuña de fluido entre la viruta y el filo. La longitud de contacto se reduce gracias a la disminución de la temperatura en la zona de mecanizado. Otro efecto es la posibilidad de influir en la forma de la viruta y mejorar así su control; en algunos casos, se puede llegar a provocar la rotura de la viruta con materiales que la geometría de la plaquita no logra romper fácilmente.
Se aprendió mucho sobre el efecto de la distribución de la presión del refrigerante y del tamaño de las boquillas de refrigerante. Mediante la variación de los datos del chorro se consiguió un formador de viruta variable y pasó a ser posible guiar las virutas delgadas hacia la dirección deseada y hasta determinar su longitud. Se llevaron a cabo instalaciones a una escala limitada con el fin de poder resolver los posibles problemas, en particular en las industrias de la energía y aeroespacial y en la fabricación de cojinetes de bolas.
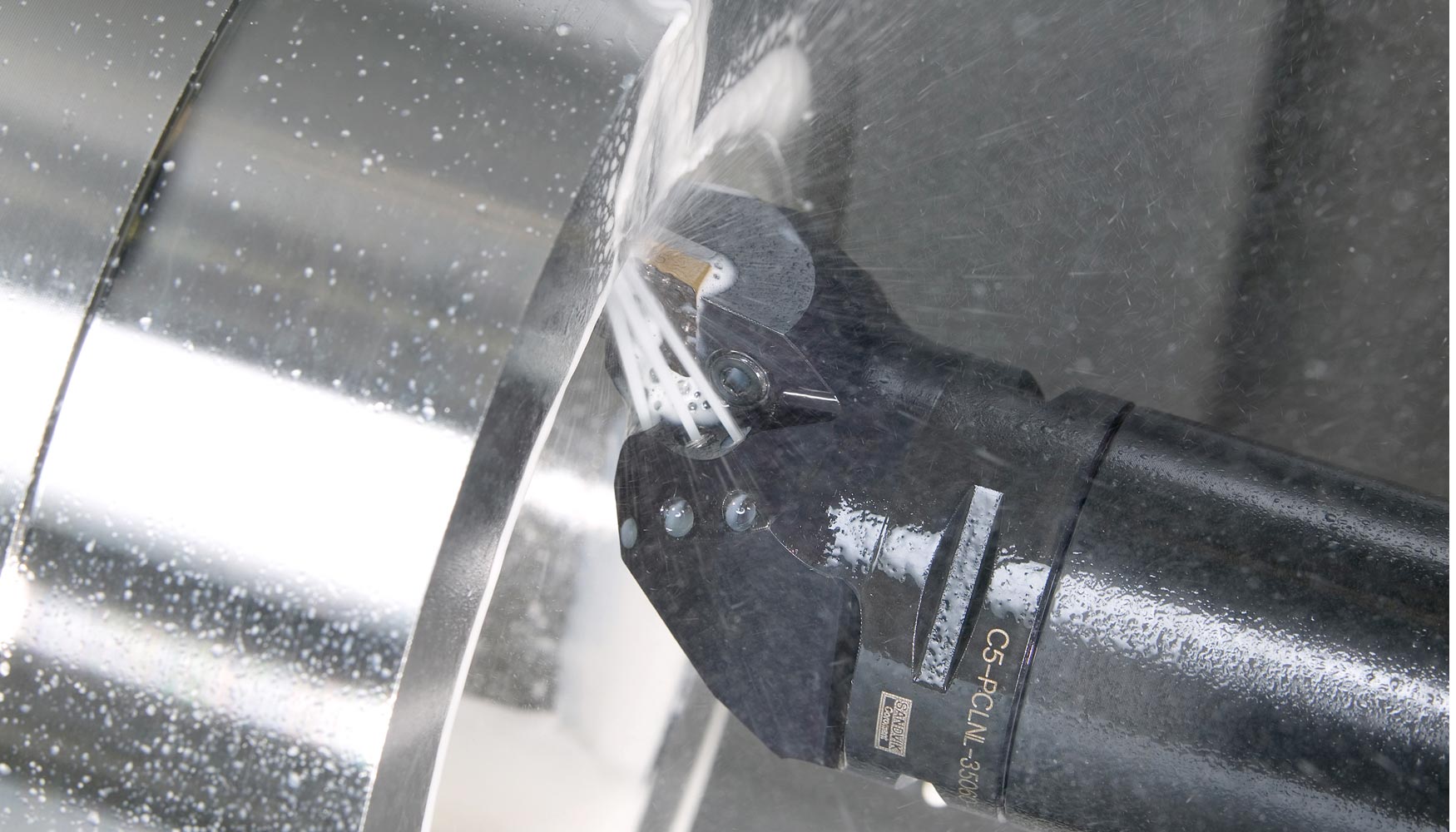
Hoy en día, la mayoría de máquinas de CNC cuentan con un suministro de refrigerante a presiones de 70 a 100 bar, lo que permite integrar el sistema HPC para obtener una diferencia señalada en cuanto a rendimiento y resultados con materiales no tenidos en cuenta inicialmente. La tecnología ha evolucionado para facilitar un importante factor de optimización, también con aceros, acero inoxidable y aluminio, así como para convertirse en un accesorio de fácil adopción. Se dispone de herramientas estándar con canalización integrada del refrigerante y equipamiento para el mecanizado asistido por chorros de precisión de refrigerante a alta presión.
Las herramientas HPC más recientes están equipadas para proporcionar chorros de refrigerante dirigidos con precisión y con flujo laminar paralelo. Los chorros provocan una cuña hidráulica entre la plaquita y la viruta, lo que afecta a la forma de la viruta y al flujo y reduce la temperatura en la zona de mecanizado. Usar una o varias boquillas montadas cerca del filo que proyecten con precisión los chorros de alta velocidad fuerza la viruta a separarse de la cara de la plaquita y enfría y rompe las virutas a longitudes menores, lo que ayuda a evacuarlas. Actualmente, y a fin de beneficiarse de todas las ventajas de la tecnología HPC, se han desarrollado plaquitas dedicadas que contribuyen a intensificar los efectos del chorro de refrigerante. Estas geometrías de las plaquitas facilitan el proceso y eliminan cualquier efecto negativo que el HPC haya podido tener en algunas plaquitas convencionales como consecuencia de una aplicación errónea. Además de una mayor seguridad del proceso gracias al mejor control de la viruta, el HPC también puede ofrecer un potencial de mejora en la velocidad de corte y un incremento de hasta un 50% en la duración de la vida útil de la herramienta.
Las herramientas modulares también es una base con muchas ventajas para el mecanizado con HPC, en parte para garantizar los cambios rápidos de herramienta y minimizar así las paradas de máquina, pero también para contribuir a asegurar las conexiones y el suministro de refrigerante de la máquina al filo. Coromant Capto, el sistema de mecanizado conforme a la norma ISO, es la plataforma ideal para la tecnología de refrigerante moderna, ya que su diseño incluye el suministro interno de refrigerante a presión. Equipado con Coromant Capto, CoroTurn HP es fácil de incluir para aplicaciones objetivo en las que el HPC marca la diferencia. Con la posibilidad de forzar una cuña de fluido en la zona de mecanizado, especialmente en operaciones clasificadas como mecanizado medio o de acabado, el grosor de viruta es más controlable y la cuña de fluido resulta más fácil de aplicar que en las operaciones más pesadas.
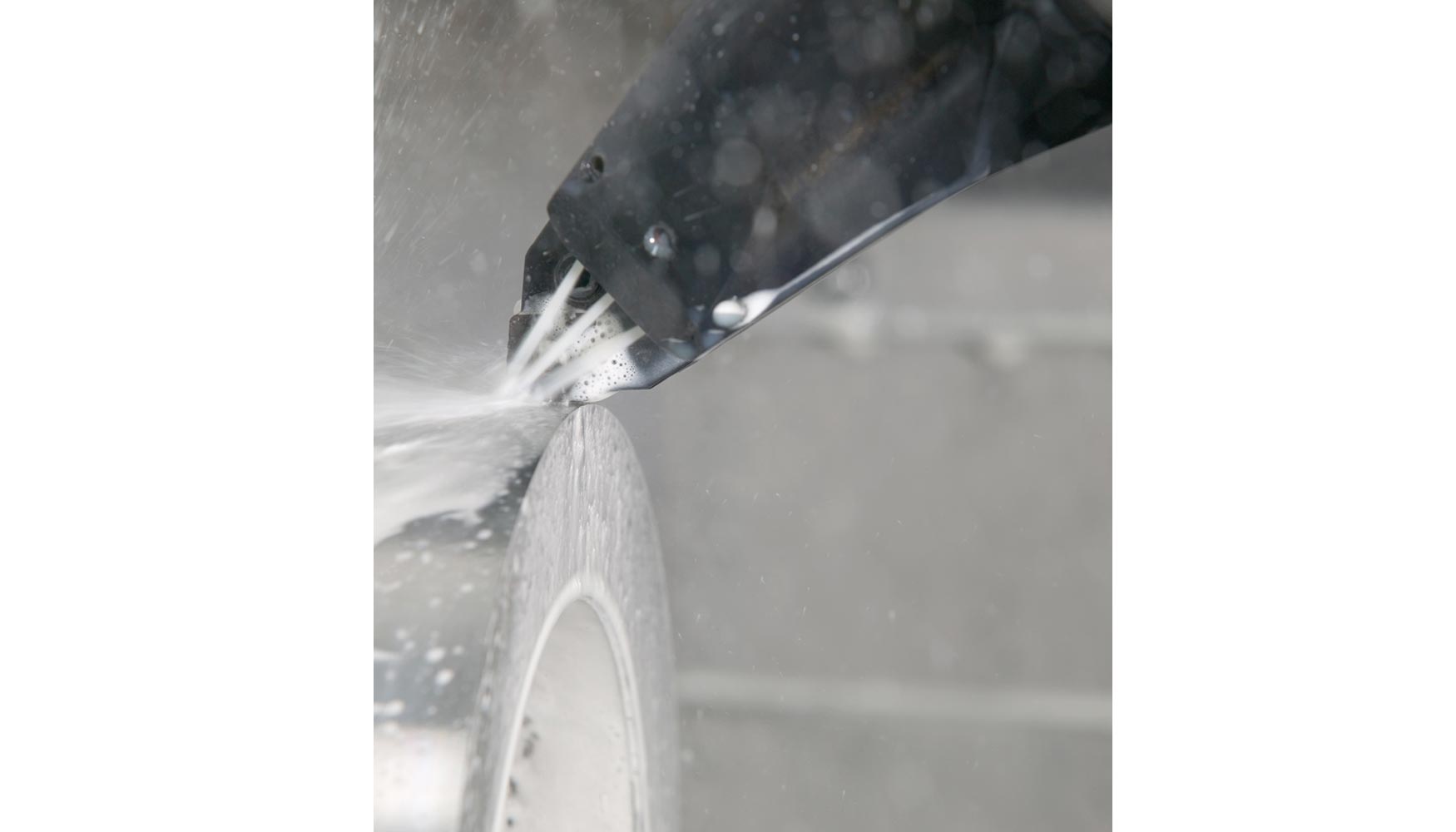
La aplicación del mecanizado de alta presión no debería verse como un medio para compensar las carencias debidas a otros factores de la aplicación, como el uso de plaquitas inadecuadas, inestabilidad, datos de corte incorrectos, etc. El HPC es un optimizador básicamente cuando las operaciones están establecidas de manera correcta. Este planteamiento proporcionará los medios para acortar los tiempos de ciclo, mejorar la consistencia de la calidad de los componentes y aumentar la seguridad del proceso en las operaciones de torneado, mandrinado y tronzado y ranurado.
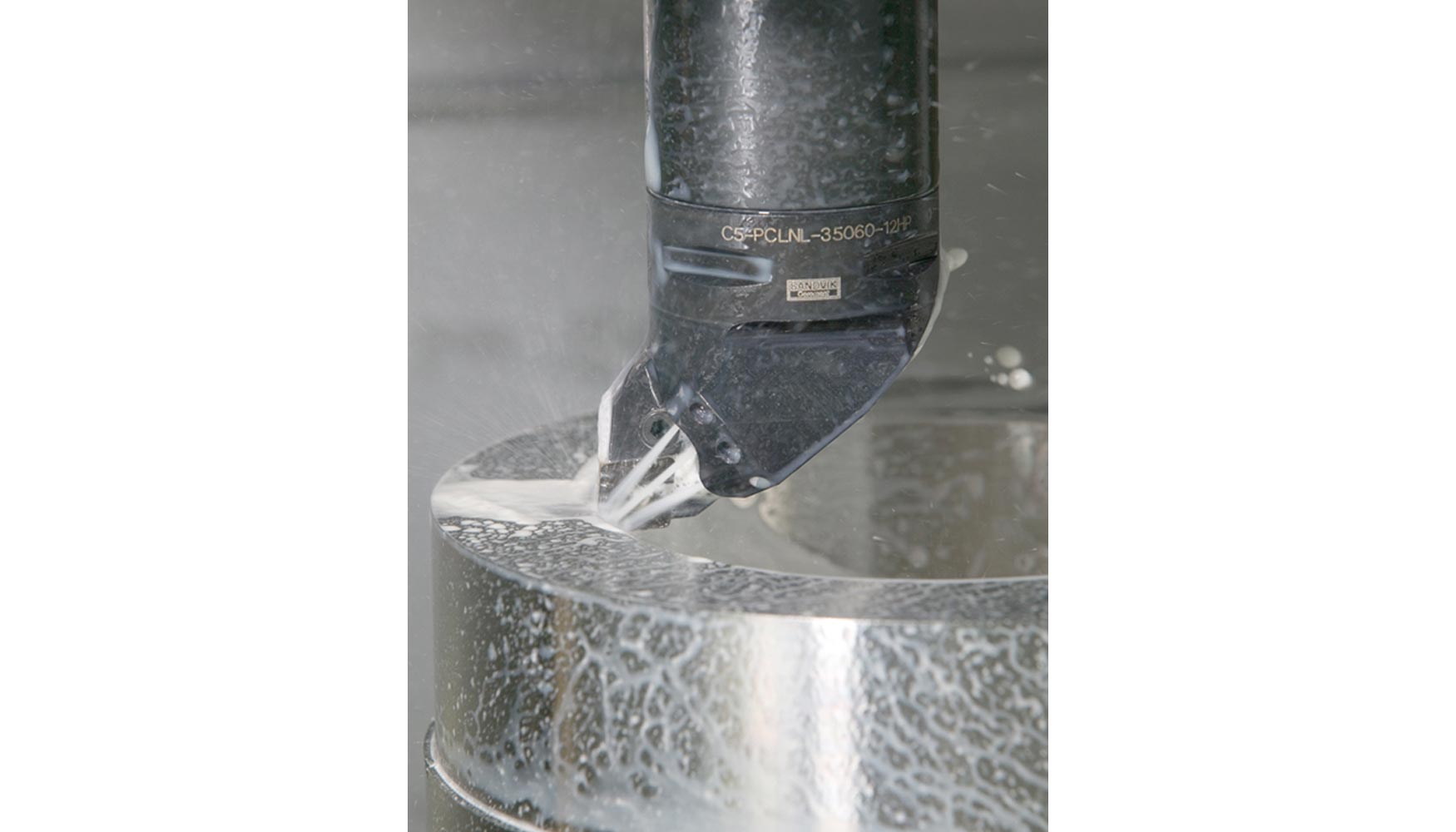