Temple de hojas de cuchillos de acero al CR 13%
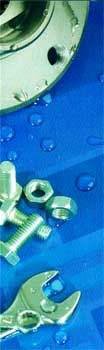
Estos hornos se construyen en elementos modulares, con diversos anchos de cinta, adaptándose a las exigencias de producción, lo cual permite efectuar la regulación de temperatura en varias zonas, obteniendo una mayor uniformidad de temperatura en toda la longitud de la mufla, así como unos resultados excelentes en el temple.
El sistema de calefacción se realiza mediante resistencias eléctricas con tensiones reducidas, debido a la alta temperatura de trabajo 1.000-1.150 ºC.
El enfriamiento se efectúa, a continuación del temple, en cámaras de agua de doble pared, con circulación en sentido contrario al avance de la cinta transportadora, obteniendo un enfriamiento progresivo y uniforme en toda la carga.
Como gas de protección se utiliza normalmente, en caso de producciones pequeñas o medias (20-80 Kg/hora), el amoniaco disociado (75% H2 + 25% N2). Para producciones superiores se recomienda el uso de "FORMIGAS", procedente de baterías de botellas o suministro en tanques con equipo de mezcla. Esta último sistema permite la variación de los porcentajes de H2+N2, y en los casos que el proceso de fabricación lo permita, se puede utilizar un porcentaje más alto de N2, lo que es sensiblemente más económico.
A continuación del temple, se debe realizar un revenido en horno con circulación forzada de aire, continuo o estático, con o sin gas de protección. Este punto siempre depende de los resultados que deseemos obtener.
Con los elementos anteriormente descritos se pueden obtener los siguientes resultados:
MATERIAL:
RESULTADOS:
Después del revenido.......54 – 56 HRC.
ESTRUCTURA:
ESTADO DE LA SUPERFICIE:
VENTAJAS DEL SISTEMA:
- Temple sin prensa.
- No es necesario atar las piezas.
- Sin descarburación.
- Sin sobrecalentamientos.
- Superficie blanca brillante. Las hojas se rectifican antes del temple.
- Superficie limpia sin manchas.
- Deformación nula.
- No es necesario lavado o decapado.
- Dureza máxima y uniforme.
- Sin contaminación del aire o del agua.
- Economía en la mano de obra.
- Disminución de los costes de producción.
Además, se puede dotar a los hornos de diversos elementos y accesorios que se reseñan a continuación:
A) Encendido automático del gas de protección
Para asegurar la combustión continua del gas de protección en la entrada y salida de la mufla, así como en la chimenea intermedia, se procede a la formación de cortinas de llama producidas por medio de un dispositivo que garantiza dicha combustión.
El dispositivo comprende:
- Pulsador de marcha-paro.
- Centralita electrónica de mando.
- Bobina de encendido por alta tensión.
- Electrodos de encendido.
- Cables de conexión.
Funcionamiento:
Sobre la centralita electrónica va montado un rele que vigila la función de la chispa de encendido continua.
Este relé cierra una válvula electro-magnética que corta el suministro de gas de protección en caso de fallo de las chispas.
El mando de éste dispositivo está montado en la parte frontal del cuadro de mandos.
B) Sistema de enjuague automático con N2
Debido a que se trabaja con gas explosivo, 75% H2, para evitar las posibles explosiones en la mufla se instala un dispositivo de enjuague automático para las puestas en marcha, paradas, cortes del suministro del gas de protección o fallos de la corriente de alimentación.
El dispositivo comprende:
- Tubería de conexión.
- Detector magnético con rele, montado sobre el medidor de caudal del gas.
- 2 válvulas electro-magnéticas.
- 2 válvulas de regulación.
- 1 diafragma para el nitrógeno.
- Interruptores, lámparas de señalización de función, señal luminosa y acústica e interruptor de puesta a cero.
El mando de este dispositivo se monta en el frontal del cuadro de mandos. Las botellas de N2, deben ir provistas de un mano reductor de 200 a 0.3 bars.
D) Disociador de amoníaco
Para la producción del gas de protección, puede montarse un generador de gas autónomo, que disocia el amoníaco y produce una mezcla gaseosa con una concentración de 75% H2 + 25% N2, con un punto de rocío de aproximadamente – 35 ºC.
El generador está compuesto por una retorta catalizadora, construida con acero de alta aleación (INCONEL-600) en cuyo interior se encuentra un preparado de carbón-níquel que absorbe las impurezas que proceden del amoníaco, un sistema de calefacción por medio de resistencias en forma de espiral integradas en un módulo de fibras cerámicas prensadas al vacío, todo ello montado en un chasis metálico, con su correspondiente aislamiento térmico. El generador puede montarse integrado en el zócalo del horno, o, de forma independiente, en las proximidades de la instalación.
La instalación comprende:
- Sistema de regulación de temperatura y fusible contra rotura del termopar.
- Retorta de disociación intercambiable.
- Salida con electro-válvula incorporada.
- Tuberías de conexión hasta dos entradas en el horno.
Los elementos de control y mando se montan en el cuadro general o bien en un armario independiente para el disociador
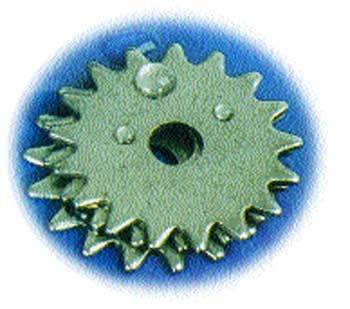