Equipos y tecnologías para corte de chapa
Aspectos analíticos y tecnológicos del proceso de punzonado de chapa (1ª parte)
Mateos, S.; Rico, J.C.; Cuesta, E.; Valiño, G.
Departamento de Ingeniería de Fabricación. Universidad de Oviedo
15/03/2002
Departamento de Ingeniería de Fabricación. Universidad de Oviedo
15/03/2002
1.- INTRODUCCIÓN
Los procesos de conformado de chapa en general, y en particular el proceso de punzonado, suelen asociarse con procesos mecánicos relativamente simples de reducida aportación tecnológica y escaso valor añadido. Sin embargo, la realidad es muy diferente ya que estos procesos, al igual que otros procesos de tipo mecánico, están fuertemente influenciados por factores muy diversos relacionados con la máquina, las herramientas, el material y características geométricas de la pieza o el propio entorno del proceso (tabla 1).
El punzonado es una operación de corte de chapas o láminas, generalmente en frío, mediante un dispositivo mecánico formado por dos herramientas: el punzón y la matriz. La aplicación de una fuerza de compresión sobre el punzón obliga a éste a penetrar en la chapa, creando una deformación inicial en régimen elastoplástico seguida de un cizallamiento y rotura del material por propagación rápida de fisuras entre las aristas de corte del punzón y matriz. El proceso termina con la expulsión de la pieza cortada (figura 1).
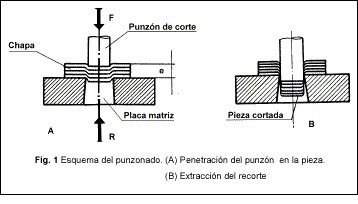
Fig. 1.- Esquema del punzonado (A) Penetración del punzón en la pieza
En general, la mayoría de los estudios efectuados sobre la mecánica del proceso de deformación plástica y corte, tienen como finalidad analizar los defectos que se presentan en el borde de las piezas punzonadas. Los primeros resultados de los estudios sobre los mecanismos de corte en punzonado se producen a comienzos de la década de los cincuenta, en Alemania (Keller) y en Japón (Fukui y Maeda) simultáneamente. Hoy en día, los estudios se centran en la obtención de modelos matemáticos que junto con el método de los elementos finitos permitan el cálculo de las fuerzas, determinar calidad del borde de la pieza y la simulación del proceso.
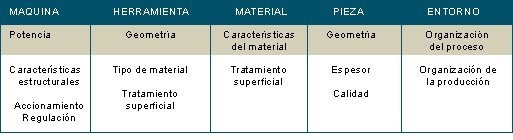
Tabla 1. Distintos factores que intervienen en el punzonado.
2. ANÁLISIS DEL PROCESO DE PUNZONADO
2.1. Mecánica del corte
En el proceso de punzonado se pueden considerar tres etapas (figura 2):
- Deformación: los esfuerzos del punzón sobre la chapa metálica, originan en ésta una deformación, inicialmente elástica y después plástica, alrededor de los bordes del punzón y matriz.
- Penetración: los filos de corte del punzón y matriz penetran dentro del material, produciéndose grietas en el material debido a la concentración de tensiones a lo largo de los filos de corte.
- Fractura: las grietas originadas a uno y otro lado de la chapa se encuentran, originando la separación del material. Asimismo, el punzón continúa su descenso para expulsar el recorte. El juego de corte J, permite la penetración del punzón en la matriz (figura 3) y la expulsión del material cortado.
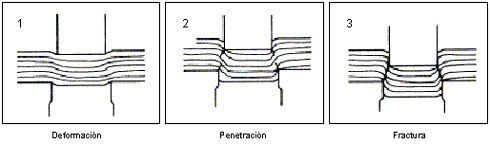
Fig. 2.- Etapas del punzonado
El juego de corte J tiene un efecto importante en el proceso de corte y se define como la distancia lateral entre el filo del punzón y el filo de la matriz. En general, el valor del juego de corte suele expresarse de dos maneras, bien como porcentaje respecto al espesor de la chapa e (juego de corte relativo) o dando el valor de la distancia entre los filos. En el caso de punzones de sección circular, el juego de corte será la mitad de la diferencia de diámetros de la matriz y el punzón, aunque es frecuente encontrar datos de fabricantes que se refieren a la diferencia de diámetros de la matriz y punzón (2J).
El corte por punzonado produce varias características en los bordes de la chapa y del material cortado. Estas características son (figura 3):
- Deformación plástica caracterizada por un pequeño radio R.
- Zona bruñida de aspecto brillante caracterizada por el ancho D.
- Fractura angular, con aspecto mate, definida por la penetración P.
- Rebaba caracterizada por su altura H.
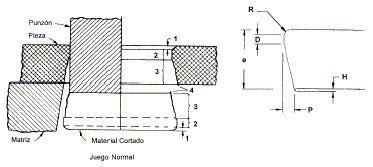
Fig. 3.- Características del borde de corte con juego normal
Todas estas características del borde cortado dependen del tipo, dureza y espesor del material, juego entre punzón y matriz, estado de los filos de corte, sujeción del material y tamaño del punzón en relación al espesor de la chapa. Las dimensiones de la zona 2 (figura 3) las determina el punzón, en el caso de la chapa, o la matriz, en el caso del material cortado.
La extensión de la zona 1 deformada plásticamente junto con la zona 2 bruñida, se representan como porcentaje del espesor del material y definen la distancia recorrida por el punzón antes de la fractura del material. El porcentaje de la penetración del punzón varía con el tipo y dureza del material. Así, a medida que aumenta la dureza del material, el porcentaje de penetración del punzón decrece. Por otro lado, la penetración del punzón aumenta cuando el tamaño del punzón es menor que 1,5 veces el espesor de la chapa, debido al alto esfuerzo de compresión a que está sometido el material en la zona de corte.
La fractura angular y la calidad del corte dependen del juego entre matriz y punzón. Con un juego insuficiente entre punzón y matriz, se produce un corte secundario. Las grietas iniciales correspondientes al punzón y matriz no están alineadas, y por tanto, no llegan a encontrarse (figura 4). El descenso continuado del punzón produce la prolongación de las grietas y la superficie no cortada entre ellas se romperá en una fractura secundaria. En la parte inferior de la carrera del punzón, se produce un corte secundario y una segunda zona bruñida (figura 5-B). La disminución del juego, por debajo de los valores normales, provoca la disminución de todos los defectos de forma, mejorando por lo tanto, la precisión de los bordes obtenidos.
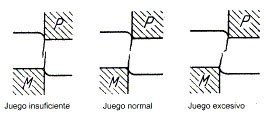
Fig. 4.- Posición relativa de las grietas según el juego
Cuando el juego empleado es demasiado bajo empiezan a aparecer cortes secundarios que perjudican la calidad de los bordes. Hay que destacar, que al disminuir el juego de corte se produce una mejora en la precisión de la pieza, sin embargo, otros factores como el desgaste de las herramientas o la energía consumida se ven afectados negativamente. En el caso de tener un juego de corte excesivo (figura 5-A) aparece una deformación plástica excesiva, una parte bruñida menor y una altura de rebaba mayor. Por otro lado, hay que resaltar que, al aumentar el juego de corte por encima de los valores normales, se consigue aumentar la vida de la herramienta en detrimento de la precisión obtenida en los bordes. Así, el juego de corte apropiado será aquel que no cause un corte secundario y tenga una deformación plástica y altura de rebaba pequeñas.

Fig. 5.- Características del borde con juego excesivo e insuficiente
Desde el punto de vista de la mecánica de la fractura del material, puede considerarse que el funcionamiento del proceso es óptimo cuando las grietas iniciadas desde el punzón y matriz se encuentran alineadas. Puesto que el juego de corte es el parámetro que afecta más directamente a la mecánica de la fractura del material, el juego de corte óptimo deberá ser capaz de proporcionar esta alineación.
2.2. Fuerzas en el punzonado
La fuerza de corte varia en función del juego manteniendo los demás parámetros constantes. En figura 6, se representa la fuerza ejercida por un punzón de 10 mm de diámetro y su desplazamiento al cortar una chapa de acero de 2,8 mm de espesor, con diferentes juegos de corte. En general, las curvas pueden ser descompuestas en dos partes claramente diferenciadas: una primera en la que la fuerza aumenta desde cero hasta su valor máximo, punto éste correspondiente al inicio de la fractura, y una segunda en la que las grietas crecen y se completa el corte del material. La primera zona presenta un aspecto muy similar en todas las curvas, sin embargo, desde el momento en que se inicia la fractura, se desarrollan fluctuaciones importantes para los distintos juegos.
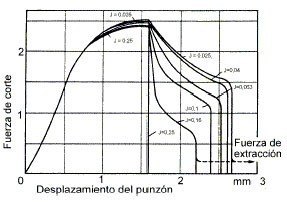
Fig. 6.- Influencia del juego de corte J sobre la fuerza de corte
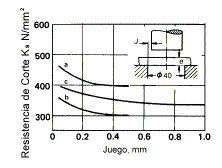
Fig. 7.- Resistencia de corte por punzonado según el juego.
a) sr= 630N/mm2, e= 5mm;
b) sr=450 N/mm2, e=5mm;
c) sr=460 N/mm2, e=10mm
La formación de la grieta puede asociarse a los descensos repentinos que se aprecian en los diagramas. Cuando las grietas originadas no se encuentran alineadas, las fuertes pendientes de descenso tienden a suavizarse, llegando en algunas ocasiones a la horizontalidad. En estos casos, suele producirse nuevamente disminuciones importantes de la fuerza debido a la formación de cortes secundarios. Como consecuencia de las fluctuaciones producidas en la disminución de la fuerza, se produce un aumento del área encerrada por el diagrama, y por tanto, de la energía consumida en el proceso. Por esta razón, cuando en el corte de la chapa las grietas presentan la misma alineación, la energía consumida por el proceso resulta mínima.
La resistencia de corte por punzonado ks será, a partir de la máxima fuerza de corte Fs máx:

donde As es el área calculada a partir del espesor de la chapa e y el perímetro lp de corte:

y ks incluye los efectos del juego de corte, desgaste de la herramienta y la influencia de otros parámetros, como las propiedades del material, espesor y forma del contorno del punzón.
La resistencia al corte por punzonado ks decrece con el aumento del juego de corte, siendo su variación de aproximadamente un 14% en el rango de J = 0,01 ¸ 0,1e. En la figura 7 se puede observar este efecto, utilizando tres materiales distintos y punzones perfectamente afilados. Conforme se realizan punzonados, el punzón sufre un desgaste que tiene como consecuencia un incremento de ks de hasta 1,6 veces. Por otro lado, la resistencia de corte se ve afectada por el diámetro del agujero punzonado, así el valor de la resistencia de corte decrece con el aumento del diámetro del punzón si se mantienen las demás condiciones constantes (figura 8). Otro factor de influencia, es la forma de la sección del punzón. En las zonas de gran curvatura existe una concentración de tensiones, motivo por el cual es más frecuente la rotura del punzón en las esquinas angulosas.
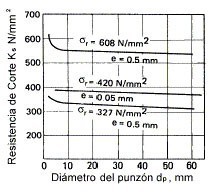
Fig. 8.- Efecto del diámetro del punzón en la resistencia al punzonado
En la práctica, en la industria se estima el valor de ks mediante la tensión máxima de cizallamiento tB, y la fuerza máxima de corte mediante:

El valor de tB se obtiene de tablas o a partir de la resistencia a la rotura sr. Por lo general, se toma como resistencia de cizallamiento tB un valor igual al 80% de la resistencia de rotura, sin embargo, esta proporción varía con el tipo y espesor del material.
Según estudios realizados por Oehler, existe una dependencia lineal entre la resistencia a la cizalladura y el logaritmo de la relación dp/e. Según estos estudios:
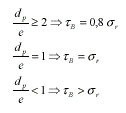
Una vez cortado el material, debe ser expulsado a través de la matriz, que en general tiene forma cónica para facilitar la extracción y dificultar el regreso del material cortado con el retroceso del punzón. La fuerza necesaria debe vencer el rozamiento y compresión radial entre el punzón y la chapa y entre la pieza cortada y la matriz. Parte de estas fuerzas también están presentes durante el retroceso del punzón debido al rozamiento de la chapa con el punzón. Esta fuerza de extracción suele expresarse como porcentaje de la fuerza necesaria para el punzonado y depende del material y del juego de corte.
Otro factor a tener en cuenta, es el estado del punzón. Así por ejemplo, el progresivo embotamiento sufrido por éste, origina un aumento de la fuerza de corte, y al mismo tiempo una disminución de la fuerza de retroceso.
También la velocidad de corte tiene influencia sobre la fuerza de corte. Así, al aumentar dicha velocidad, disminuye la fuerza necesaria, debido fundamentalmente a la elevación de la temperatura del material que se origina con el aumento de la velocidad de deformación.
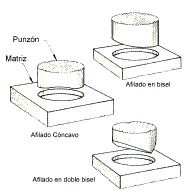
Fig. 9.- Afilados especiales del punzón
Cuando las fuerzas de corte son demasiado elevadas, estas pueden ser reducidas considerablemente mediante un punzonado por corte progresivo, esto es, inclinando el corte del punzón (figura 9). Sin embargo, la variación de la fuerza no supone una variación de la potencia consumida en el proceso.
2.3. Desgaste de la herramienta
La herramienta, durante su trabajo, está sujeta a una serie de acciones mecánicas, térmicas y químicas, que ejercen un efecto de desgaste, y por tanto, es de gran interés conocer los factores que afectan a éste. Entre estos factores, se pueden citar el material de trabajo, el número de punzonados, el material de la herramienta, el diámetro del punzón, el juego de corte y la lubricación.
Todos los mecanismos de desgaste (adhesión, abrasión, etc.) pueden presentarse cuando se realizan operaciones de punzonado, tanto en los punzones como en la matriz sustentadora de la chapa a punzonar. El desgaste se produce en tres zonas: caras, flancos y bordes del punzón y matriz (figura 10).
Los flancos y bordes del punzón y matriz están expuestos a la acción de las superficies generadas en el proceso de corte, y el deslizamiento relativo provoca fenómenos de adhesión en los flancos y bordes.
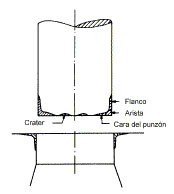
Fig. 10.- Desgaste del punzón y matriz
La pieza punzonada sufre un endurecimiento al deformarse plásticamente, produciendo un crecimiento de las presiones locales y provocando la aparición de partículas más abrasivas. También la alta velocidad de producción da como consecuencia un alto número de impactos, favoreciendo la adhesión de partículas y fatiga de los filos de corte. Simultáneamente, aumenta la temperatura de la matriz, del punzón y de la pieza, por lo se incrementa la adhesión y se favorece la oxidación.
La deformación elástica de la pieza produce un movimiento relativo a lo largo de la cara del punzón, inicialmente hacia el exterior y posteriormente, una vez iniciada la fractura, hacia el interior. Este hecho produce un desgaste abrasivo en la cara frontal del punzón. El pisador limita esta deformación elástica del material, con lo cual se reduce el desgaste del punzón. Por otro lado, la recuperación elástica de la chapa produce un desgaste del flanco del punzón en el movimiento de retracción.
En la superficie lateral del punzón y de la matriz, el desgaste es debido fundamentalmente al mecanismo de adhesión. Otra zona que sufre desgaste, es el borde de corte, que presenta ambos mecanismos de desgaste, no siendo reseñable la influencia del tipo de material de la herramienta sobre el mismo.
Los criterios de inutilidad de la herramienta comúnmente utilizados, son los siguientes:
- Consumo energético y fuerza máxima necesaria en el proceso.
- Altura máxima tolerable de la rebaba generada en el corte.
- Medición del desgaste de las caras, flancos y bordes en el punzón y matriz.
- Medida del aumento del juego de corte como consecuencia del desgaste.
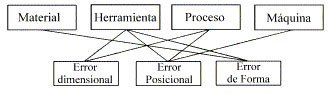
Fig. 11.- Factores que afectan a los defectos geométricos de las piezas punzonadas
Parece lógico establecer modelos de ecuaciones de vida, al igual que en las operaciones de mecanizado por arranque de viruta, que permitan saber con antelación el número de punzonados que es capaz de realizar un conjunto punzón-matriz, antes de ser rechazado. Estos modelos permiten establecer la duración de la herramienta antes de llegar a un valor de desgaste determinado, el cual será función del criterio de optimización elegido (mínimo coste, máxima producción, máxima calidad, etc.). Los estudios realizados sobre este tema son relativamente escasos, sobre todo por la complejidad del mecanismo de desgaste, íntimamente ligado con la vida de la herramienta. Por tanto, resulta difícil establecer modelos sobre una gran base de datos experimentales.
2.4. Precisión de las piezas punzonadas
En el punzonado, como en cualquier otro proceso de fabricación, en necesario establecer las especificaciones de precisión necesarias para satisfacer las necesidades del usuario. Por tanto, resulta interesante hacer un estudio de la precisión, con el fin de poder definir dichas especificaciones, de la forma más acertada posible.
La precisión de las piezas punzonadas puede ser caracterizada por los siguientes defectos: dimensionales, posicionales y de forma. Los factores que afectan a estos defectos son principalmente el material, las herramientas, las variaciones del proceso y la máquina. En la figura 11 aparecen representados los diferentes factores que afectan a cada uno de estos defectos.
Los diámetros del recorte y del agujero, medidos sobre la superficie pulida, deben coincidir en teoría con los del punzón y matriz respectivamente. Estas dimensiones teóricas pueden sufrir alteraciones, debido a la influencia de algunos factores, tales como la inexactitud en las dimensiones de las herramientas, las deformaciones elásticas de éstas o las tensiones elástico-plásticas producidas en el material.
En lo que respecta a los defectos posicionales, estos comprenden dos tipos de imprecisiones geométricas: irregularidades en el contorno del recorte e inexactitudes de los agujeros de las piezas perforadas. Las primeras son debidas normalmente a la falta de coaxialidad entre punzón y matriz, a defectos en las guías o a la inexactitud de forma de las herramientas. En cuanto a la inexactitud de posición de los agujeros, depende de la precisión del sistema de movimiento de la chapa (tabla 2).
Los defectos de forma son aquellos que se presentan en los bordes de la pieza y dependen de las herramientas y del material. Los factores de las herramientas que más afectan a estas imprecisiones geométricas, son el juego de corte, la forma del punzón y el estado de desgaste del filo, mientras que los del material, son la calidad, resistencia y espesor de la chapa.
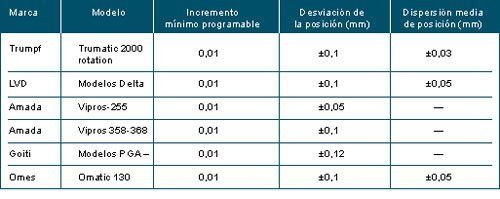
Tabla 2.- Datos de la precisión de diversos modelos de punzonadoras CN según catalogo
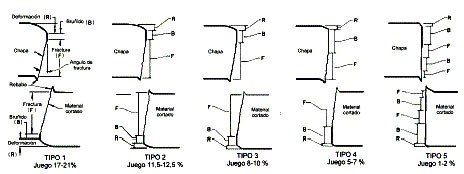
Fig. 12.- Distintos tipos de borde según el juego. Material acero de bajo contenido en carbono
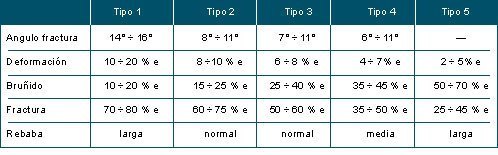
Tabla 3.- Rango aproximado de los valores de los distintos bordes de la figura 12
Los defectos de forma pueden ser controlados mediante el ajuste del juego de corte. Así, según el juego de corte, se pueden obtener cinco tipos de bordes en la chapa punzonada. En la figura 12 pueden observarse de manera esquemática para el punzonado de acero de bajo contenido en carbono. Las características de cada uno de estos tipos de bordes pueden verse en la Tabla 3.
En lo que respecta a las dimensiones del agujero, se ven afectadas por el cambio del juego de corte. Cuando se utilizan juegos de corte que producen bordes como el tipo 4 (figura 13), el diámetro del agujero es alrededor de 0,01 mm menor que el diámetro del punzón. Sin embargo, si se obtiene un borde del tipo 2, el diámetro del agujero es 0,01 mm mayor que el diámetro del punzón.
El valor de la altura de rebaba (H) viene condicionado, en el caso del recorte, por el estado de desgaste del punzón, mientras que en el agujero, éste depende del grado de desgaste de la matriz. Por lo tanto, la altura de la rebaba depende de los mismos factores que el desgaste de las herramientas. La figura 13 muestra la altura de la rebaba en función del número de punzonados efectuados.
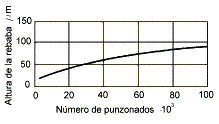
Fig. 13.- Variación de la altura de la rebaba con el número de golpes