Corte de chapa por plasma
Clasificación de las tecnologías de corte por plasma
Hablando genéricamente de los tipos de plasma es posible distinguir dos grandes clasificaciones:
Por aplicación:
Plasma estándar
De cara al corte mecanizado es la derivación del plasma manual que sólo cuenta con un gas: el que efectúa el corte. Esta aplicación es bastante limitada y es poco empleada, ya que solo trabaja para corte de chapas de pequeño espesor.
Plasma dual
Es la tecnología más usada actualmente. Se utiliza un gas como plasma y un segundo gas (que puede ser el mismo) que no realiza la función de corte sino de elemento de protección. Una de las ventajas de esta tecnología es que en ciertos metales, y en particular en acero al carbono, el plasma dual puede mejorar un 10 o 15% las velocidades de corte y la calidad. En acero inoxidable y aluminio tiene aplicaciones muy importantes respecto a la calidad de corte. La tecnología dual permite una gran combinación entre plasmas de corte, plasmas de protección y gases de protección, lo que ayuda muchísimo a elevar los valores de productividad y calidad.
Bajo el agua
Se trata de una tecnología muy extendida y muy aplicada actualmente y aún le quedarán muchos años en centros donde se necesiten grandes intensidades de corriente o donde se puedan tener problemas de contaminación, ruido o luz, e incluso efectos térmicos por el aporte de calor.
Aplicaciones especiales
Ya hay plasmas pensados para puntos concretos, tales como las tecnologías que intentan mejorar la calidad de corte de alta definición, o allí donde se pretende conseguir alta calidad por encima de otros criterios como pueda ser la productividad. En este caso la elección del gas es muy importante. Hay que combinar tecnologías así como los propios consumibles e incluso con las fuentes de potencia.
Por tecnología o tipo de proceso:
En esta clasificación cada gas lleva como apellido el gas de corte que lo genera.
Plasma por aire
Se trata de un tipo de corte muy genérico: es por supuesto el gas más barato, pero su calidad es media-baja. Presenta una problemática importante: dado que el aporte de aire es gratuito, su proceso de introducción debe ser revisado con mucho esmero, garantizando que esté muy limpio de partículas de aceite o polvo y sobre todo de humedad. En caso contrario, el gasto de consumibles aumenta muchísimo, de forma que lo que se gana en gases se pierde en el coste de los consumibles.
El aire se utiliza principalmente en acero al carbono aunque en ciertas aplicaciones puede cortar inoxidable y aluminio también, así como el plasma dual acompañado de todos los gases
Plasma por oxígeno
El oxígeno es el gas primordial para corte con acero al carbono siempre que se esté buscando una muy buena calidad. El oxígeno deja unas superficies muy limpias en cuanto al corte, deja pocas rebabas y las angularidades de las superficies cortadas son pequeñas. El problema del oxígeno es que el campo de corte está limitado a los 300 amperios, lo que supone el corte de 25 o 30 mm como máximo.
Plasma por nitrógeno
A partir de 30 mm, en el caso del acero al carbono s preciso cortar con nitrógeno, también aplicable al aluminio y al acero inoxidable. El problema del nitrógeno con el acero al carbono se presenta cuando hay posibles o futuras soldaduras, ya que puede conllevar problemas de nitruración. Así pues, en el caso de que el elemento a cortar requiera un proceso posterior, es preciso analizar con detenimiento qué combinación de gases debe realizarse.
El acero inoxidable de aluminio también obtiene una buena calidad al ser cortado con nitrógeno. Para inoxidable de aluminio la mejor combinación es el H35, nombre genérico o estándar de una mezcla al 35% de carbón e hidrógeno. El corte es excelente en cuanto a calidad, muy limpio y presenta unas superficies brillantes.
Tipos de plasma
Por aplicación:
- Estándar
- Dual
- Bajo agua
- Aplicaciones especiales
Por proceso de corte / gas:
- Aire: Ac. Carbono, Ac. Inoxidable, Aluminio.
- Oxígeno: Ac. Carbono, Cobre.
- Nitrógeno: Ac. Carbono, Ac. Inoxidable, Aluminio.
- H35: Ac. Inoxidable, Aluminio, Cobre.
Aspectos valorables en la inversión
- Materiales a cortar.
- Calidad de corte.
- Productividad.
- Coste de inversión.
- Coste / m. cortado.
- Aplicación del material cortado.
- Automatización de proceso.
- Otros (Seguridad, Medio Ambiente,.....)
El plasma frente al láser y el oxicorte
El plasma corta cualquier elemento metálico, incluso metales no férreos como el titanio. En este sentido tiene un campo de aplicación total. En el caso de inoxidable o de aluminio la comparativa frente al láser en cuanto a calidad resulta inferior. Frente a la actual limitación de láser a nivel de corte hoy es posible cortar con un plasma más de 100 mm de acero inoxidable. El campo de aplicación en corte de metales ahora es importantísimo. En acero al carbono y frente al oxigás, el plasma ha ido avanzando año tras año. En lo que se entendía hace años como espesores absolutamente limitados para corte con oxigás, el plasma, a nivel de rentabilidad y de velocidad de corte, incluso de costos de procesos, va ganando terreno.
Respecto a la calidad de corte, en el marco de los tres métodos térmicos el plasma es el que más acusa cualquier alteración o variación en todos los parámetros que puedan afectar la calidad. Estos parámetros pasan primero por el corte mecanizado y la máquina como la mano que guía el elemento cortante.
El plasma es un elemento que no sólo acusa cualquier imperfección mecánica, sino que la aumenta. Por tanto, éste es uno de los puntos fundamentales en el corte por plasma, así como el oxigás es un tipo de corte en el que no es realmente necesaria demasiada precisión mecánica.
El plasma también es muy susceptible a los cambios en las combinaciones de gases, a las velocidades de corte e incluso al posicionamiento del soplete de altura. Si la conicidad del plasma no coincide con el posicionamiento de la chapa, esa será la conicidad que refleje la chapa cortada.
Vendrá dada por las velocidades de corte que consigan y el número de sopletes o de estaciones de corte que sean aplicables. Hoy en día aunque es técnicamente posible utilizar más de dos fuentes lo usual es no pasar de esas dos fuentes de plasma cortando. Luego veremos que al nivel de la diferencia de velocidades, incluso dos estaciones de corte plasma frente a 6 ó 7 de oxigás, pueden ser más rentables productivamente.
* Coste de la inversión
Estas cifras son muy difíciles de evaluar. Tomando como referencia la de un corte de velocidad más o menos rentable, entre oxigás, plasma o láser habría que elegir un plasma de unos 2.000 amperios para un corte de 25 mm de espesor y un láser de 3.000 o 4.000 W. El plasma presenta un incremento de coste frente al oxigás no solamente por el hecho de la inclusión del propio plasma como equipo de corte sino también por los requerimientos de precisión mecánica de la máquina.
El coste por metro cortado siempre se ha tomado como referencia al considerar la rentabilidad del proceso. Hoy en día se toma la barrera de los 25 mm de plasma frente al oxigás debido a las velocidades de corte que se empiezan a conseguir, ya que los costes del proceso son menores debido a la tecnología de los consumibles.
La aplicación del material cortado
Será otro de los puntos a tener en cuenta, en particular en cuanto a la soldabilidad. A considerar los gases que se utilizan, así como el tipo de corte a efectuar, ya que el plasma puede requerir un considerable nivel de consumo el’ectrico si incluye muchos taladros.
La automatización del proceso
Una máquina plasma está preparada para trabajar sin ningún tipo de auxilio exterior. Sin embargo, hay que tener en cuenta aspectos como la seguridad y el medio ambiente debido a la extracción de humos.
Selección del plasma
En la selección del plasma es preciso contemplar la velocidad de corte oxigás que permanece prácticamente estable. En este entorno basta con 100 o 200 amperios para triplicar o cuadriplicar las velocidades de corte. Si ya se están considerando plasmas de 400 amperios, incluso en 25 mm, se llega al entorno de 2000 mm/min, lo que supone triplicar la velocidad de corte.
En costes por metro cortado, la rentabilidad del proceso de plasma es importante siempre que nos situemos en el rango más suave de aplicación.
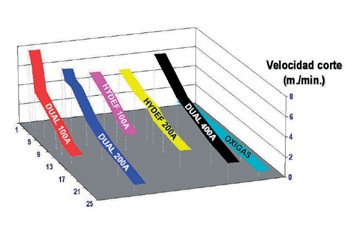
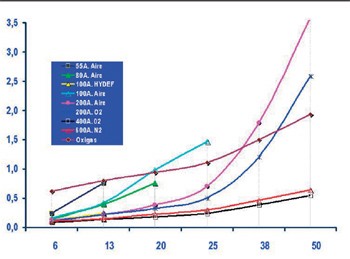
Requerimientos del sistema
Velocidad
Unos de los puntos importantes a la hora de evaluar una máquina de plasma son las velocidades con las que se va a mover el proceso. En situaciones exageradas, con un plasma de 200 amperios es posible cortar chapas de 40 mm a 300 mm/min e incluso menos, pero también podrá cortarse chapa de pocos milímetros a 8.000 y 10.000 mm/min. Esto ofrece un margen de aplicaciones muy amplio en cuanto a velocidad.
La situación más desfavorable en cuanto al corte es que la velocidad máxima no pueda ser la que marque la máxima velocidad de posicionamiento de la máquina, pues es preciso otorgar un cierto margen de movimiento. Además, todo lo que sea aumentar la velocidad de posicionamiento de la máquina supone mayor productividad del sistema.
Todos estos son los factores a conjugar cuando se define la máquina dada una velocidad máxima de desplazamiento. Por regla general, las máquinas se pueden estar moviendo también entre 15 m/min y 40 m/min, dependiendo también, por supuesto, de la longitud de la rodadura y de otros factores.
Aceleración
La aceleración del sistema es tal vez unos de los puntos clave. El plasma requiere de respuestas muy rápidas. Por ejemplo, en las esquinas la calidad de corte se resiente en gran medida. Todo ello se basa en la relación entre la potencia empleada por la máquina y el peso total del sistema, teniendo en cuenta que, normalmente, la máquina tendrá dos motores, uno de forma longitudinal y otro de forma transversal.
La tecnología de motores que se ha impuesto es la "brushless de corriente alterna", sobre todo en lo que supone la regularidad de los pares de motores independientemente de las revoluciones - muy importante viendo las diferentes situaciones de velocidad en la máquina.
Control numérico
A nivel de control numérico se ha avanzado muchísimo. Una de sus funciones es la de gestionar todo el sistema máquina-plasma, teniendo que comandar todos los cuadros de gases, posicionamientos de chapa, etc. Hay que tener en cuenta que con la tecnología actual en PC se ha avanzado en el mismo sentido que en cualquier otro sector de la informática.
También es muy importante el control de altura del soplete, del que depende en gran parte la calidad de corte. Se gestionan dos parámetros: el posicionamiento de inicio de la perforación y el seguimiento de la altura. Este factor es crítico respecto a la calidad, y al hecho de no dejar angularidades excesivas.
Higiene y medio ambiente
Cada día se ha ido tomando más conciencia de los aspectos relativos a la higiene y el medio ambiente. Actualmente, por ley, es obligatoria la extracción y limpieza de los humos. Los humos del plasma son realmente tóxicos, pues contienen partículas de cromo y níquel que hay que extraer y limpiar. Existe una normativa de higiene en cuanto a la extracción de los humos de plasma que regula su tratamiento: es preciso filtrarlos. También existe una normativa de gestión de residuos que dicta lo que hay que hacer con las partículas que se recogen. Se dispone en la actualidad de mesas de aspiración y filtros autolimpiables, tecnología que apunta a ser la del futuro para garantizar la extracción y limpieza.
En cuanto a la seguridad a nivel óptico, según la norma 379, una protección 11 a 13 es inferior a la de la soldadura, debe tener protección acústica en caso de que supere los 85 dB que pueden ser superados en muchas fuentes plasma y, finalmente, es necesario considerar las directivas acera de baja tensión y compatibilidad electromagnética.
Condicionantes mecánicos
- Calidad / Tolerancias de corte
(DIN 2310 y 22768)
- Velocidad necesaria corte plasma
- Desplazamientos en vacío
- Velocidad máxima de desplazamiento
- Aceleración total del sistema
- Relación Potencia / Peso total del sistema.
(Motorización)
Control numérico
- Gestión de movimiento de la máquina
- Aplicaciones concretas para plasma
- Personalización a las necesidades del usuario
Software de diseño.
Control de altura del soplete
- Depende calidad de corte y gasto
de consumibles.
- 2 parámetros a controlar:
Seguimiento de altura durante
el proceso de corte
Distancia de perforación
Higiene / Medio Ambiente
- Obligatoriedad de extracción
y filtración de humos
- Ley de Prevención
- Normativa Medio Ambiente
- Gestión de residuos
Seguridad
- Óptica: EN-379 Protección 11 a 13
- Acústica: Protección si supera máximo
admisible 85 dB
- Eléctrica: Dir. Baja Tensión y Compatibilidad. Electromagnética.
Tendencias de futuro
El plasma como sistema de corte se está alimentando de la cultura del láser en cuanto a productividad máxima se refiere. Así, algo bastante común en el láser se está empezando a asumir en el plasma, como por ejemplo los sistemas de carga y descarga semiautomáticos de chapa, posicionamiento totalmente automatizado, lectura de los datos de chapa, espesores, incluso configuración automática de la parametrización de CNC.
Los sistemas actuales tienen un grado de autodiagnóstico mucho más avanzado.
máquina-plasma, teniendo que comandar todos los cuadros de gases, posicionamientos de chapa, etc. Hay que tener en cuenta que con la tecnología actual en PC se ha avanzado en el mismo sentido que en cualquier otro sector de la informática
La tendencia es tratar el CNC como un elemento más de una red incluida en el sistema de la factoría, y esta conexión puede utilizarse para el intercambio de datos, control remoto, etc. Los fabricantes de plasma están haciendo un esfuerzo importante para aumentar la relación entre la velocidad de corte y la intensidad de corriente, es decir, mejorar la rentabilidad de los sistemas a nivel energético. Se están consiguiendo velocidades de corte espectaculares con corrientes relativamente pequeñas
Automatización total del proceso
- Carga / descarga de chapa
- Posicionamiento / medición espesor
- Configuración parámetros de corte
Diagnosis del sistema
Conexión remota del equipo
Aumento relación velocidad de corte/ intensidad de corriente
Consumibles de mayor duración.