Application of forges it rotary presses of Inconel 718 to a geometry of the aeronautical sector component manufacturing sector component manufacturing sector: analysis microestructural
To. Sleeves, M. Santos, S. Varela And J. Saint José of
Introduction
Forges it rotary presses is an incremental process and is cream like an alternative to forges it conventional. Because of said incremental nature, forges it rotary presses is able to reduce the strengths of conformed and obtain big ratios of deformation without cracks in an alone hit. The movements of the toolings are two basically, a rotation and a traslación axial. The useful inferior and upper rotan sincrónicamente while the upper tooling moves vertically to realizar the necessary career to form the piece. What concedes the incremental character to this process is the inclination of the upper tooling on the vertical axis, called angle of nutación. East can vary between 2º and 8º in function of the geometry and material to conform. To continuation shows a diagram of the comparative go in forge rotary presses and conventional as well as of the movements of this first.
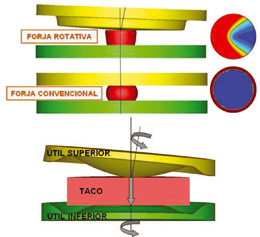
One of the important characteristics of forges it rotary presses is the geometry of mushroom that purchases the swearword as it goes deforming, unlike the barrilete characteristic of forges it conventional [1]. This shapeless incremental process to the swearword according to a new way of deformation improving like this the ratio of deformation by hit, what comports to arrive to geometries ‘near-net-shape' in an alone hit. A direct consequence is the reduction of costs of tooling by the reduction of preformas necessary to attain the final geometry.
Tecnalia, in previous works, developed a model of able simulation to reproduce geometry and strengths involved in a process of forge rotary presses [2,3]. Later it has improved this model including the calculation microestructural during the own process [4,5].
The requests of the components of the aeronautical sector component manufacturing sector component manufacturing sector are very restrictivos, so much from the geometrical point of view like microestructural. In function of the microstructure of a component this presents one or another mechanical behaviour during his useful life, being able to be this resistance to fatigue or to creep. Thus the study of the evolution microestructural even during the process of conformed every time purchases greater importance.
The calculations microestructurales base in the implementation of the equations that govern this evolution based in the temperature, deformation, speed of deformation and initial size of the grain [6]. The parameters that define the previous equations are determined in essays of compressesion of simple and double hit [7].
The material used in this study, Inconel 718, is one of the most used in the aeronautical sector component manufacturing sector component manufacturing sector by resistance to the corrosion, creep and fatigue to high temperatures during the useful life of the component. These advantages see contrarestadas by the narrow window of conformed that possesses. Being this limited between 900 and 1.120 °C [8]. The control of this temperature as well as of the values of deformation and of speed of deformation during the process of conformed comport a control of the final microstructure of the component.
Obtain a microstructure of size of fine grain involves a precise control of the temperature during the process of forges. One of the phases of the Inconel 718 is the phase δ, being his main characteristic the limitation of the growth of the size of grain. Thus if the aim is a microstructure with fine grain is necessary to ensure that it does not surpass the temperature of dissolution of this phase, rondando the 1.020 °C. This phenomenon studies in depth in several publications [9,10].
During the conformed to these temperatures takes place the recristalización whose consequence is a fall of the tensional level in the graphic tension —deformation and nucleación of new grains—. The first involves lower strengths required for the deformation and the second involves afinamiento of the size of grain. In previous works have analysed studies of the process of recristalización in forges it rotary presses [4].
It forges rotary presses: geometry
After the first results of the application of the process of conformed by means of forges it rotary presses to the Inconel 718 [4,5] for the obtaining of a simple geometry of recalcado, in the present work exposes the analysis realizar in an industrial piece of the aeronautical sector component manufacturing sector component manufacturing sector. The geometry of said piece, exposed in the following figure, was supplied by the company Industry of Turbo Propellants, S.A. (ITP).
![It appears 2. [Geometry real piece after the mechanised] It appears 2. [Geometry real piece after the mechanised]](https://img.interempresas.net/fotos/908118.jpeg)
The aim has been to obtain the previous geometry to the mechanised by means of forge rotary presses inside the specifications of available machine. Given the dimensions of the components of the aeronautical sector component manufacturing sector component manufacturing sector, said specifications are a complex requirement being necessary equipment that require big investments.
In this way has obtained the definition of the preforma and the parameters of manufacture that fulfilled the initial requirements of strengths of numerical way. The preforma shows in the following figure.
![It appears 3. [Preforma Of forge rotary presses] It appears 3. [Preforma Of forge rotary presses]](https://img.interempresas.net/fotos/908119.jpeg)
The parameters of process used have been:
- Speeds of the process: 70 rpm and 0,8 mm/s
- Temperature of toolings: 500 °C
The relation of speeds is relatively slow in comparison with the used for pieces of other sectors, like the automotive sector. The definition of the temperature of the toolings comes from of the previous work realizar on a simple geometry of recalcado.
With the parameters mentioned the necessary strength for the manufacture of said preforma reaches values until 1.700 tonnes in function of the initial temperature of the swearword. As it shows in the following graphic, the necessary strength reduces increasing the temperature of the swearword, of 970 to 1.000 °C. However, this increase of temperature finds limited by the final conditions of microstructure required. These strengths are relatively small comparable with the conventional processes of forges.
![It appears 4. [Comparative of strengths for the preforma to different initial temperatures in forge rotary presses] It appears 4. [Comparative of strengths for the preforma to different initial temperatures in forge rotary presses]](https://img.interempresas.net/fotos/908123.jpeg)
Optimisation of the initial temperature of the swearword
The systematic increase of the initial temperature of the swearword translates in a reduction of strengths. However, the final microstructure (afinamiento of grain and homogeneity) can see damaged considerably still forging inside the window of work defined for the Inconel 718, between 900 and 1.120 °C. The aim of this section is the obtaining of the geometry with size of fine grain (elder that 6ASTM) and homogéneo in all the section of the same.
The numerical results microestructurales taking like initial temperature of the swearword 970 and 1.000 °C show in the following figure. The initial conditions of process are the marked speeds in the previous section, 70 rpm and 0,8 mm/s, as well as temperature of toolings of 500 °C. The size of initial grain to the beginning of forges it rotary presses has been 9ASTM.
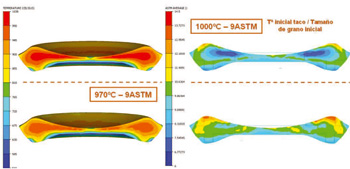
For the case of initial temperature the same to 1.000 °C, in the central zone of the section the temperature increases above the initial because of the warming by plastic deformation. This increase of temperature for the case of the Inconel 718 can arrive to reach the 60 °C [11]. Because of this effect, the temperature in this central zone surpasses the temperature of dissolution of phase δ, mentioned previously, what involves a growth of the size of grain in this zone. Like this it reflects in the image of the microstructure where the size of grain has increased of 9ASTM initial to values between 6.7 and 7.5ASTM.
In the following graphic show the maximum values and minimum of the size of grain for each one of the two previous cases.
![It appears 6. [Size of maximum grain and minimum. Optimisation of the initial temperature of the swearword] It appears 6. [Size of maximum grain and minimum. Optimisation of the initial temperature of the swearword]](https://img.interempresas.net/fotos/908125.jpeg)
Appreciates like the case of 1.000 °C possesses a more heterogeneous microstructure that the case of 970°C because of the growth of grain mentioned previously. In this way it remains reflected the temperature of 970 °C initials like the most ideal for this geometry in forges it rotary presses.
It forges rotary presses: geometry climbing
After the results obtained previously arises the need of the realisation of an experimental piece. For this will use the experimental machine of forge rotary presses that has Tecnalia in his installations developed jointly with the company Industries Puigjaner, S.A. (DENN), showed in the following image.
![It appears 7. [Machine of forge rotary presses developed jointly between DENN and Tecnalia] It appears 7. [Machine of forge rotary presses developed jointly between DENN and Tecnalia]](https://img.interempresas.net/fotos/908126.jpeg)
Because of the dimensions of the piece is necessary scalar said geometry to values of strengths and apt geometry for the experimental machine. Thus, the escalado chosen is 1/3. This involves a geometrical reduction as it shows in the following table, so much for the initial swearword as for the preforma after forges it rotary presses:
![Table 1. [Comparative geometrical of the initial swearword and preforma after forges it rotary presses to scale real and climbing 1/3]... Table 1. [Comparative geometrical of the initial swearword and preforma after forges it rotary presses to scale real and climbing 1/3]...](https://img.interempresas.net/fotos/908127.jpeg)
Comparative geometry to scale real and climbing 1/3
In the present section realizar the comparative between preforma climbing to real size and the climbing 1/3. In the comparative studies so much the strengths like the distribution of temperatures and size of grain in the transversal section of the preforma.
1.1 Strength
The same reduction seen in geometry can see in ranks of strengths, as it appreciates in the following graphic.
![It appears 8. [Comparative of strengths between preforma to scale real and climbing 1/3] It appears 8. [Comparative of strengths between preforma to scale real and climbing 1/3]](https://img.interempresas.net/fotos/908128.jpeg)
1.2 Temperature and size of grain
In the following figures presents the comparative in temperatures and size of grain concerning the preforma of forge rotary presses to scale real and climbing 1/3. Both geometries were obtained by forge rotary presses with the following parameters of process: 70 rpm and 0,8 mm/s, temperature of equal toolings to 500 °C, size of initial grain of forges it rotary presses 9ASTM and initial temperature of equal swearword to 970 °C.
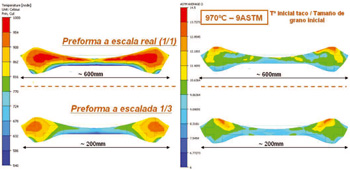
As it appreciates in the images, the preforma to scale real possesses upper temperatures in the centre of the transversal section. This is had to fundamentally to the size of the piece, that is to say, to greater greater size is the deformation and like greater consequence is the increase of temperature by plastic deformation. In spite of this increase of temperature, when splitting of a temperature of 970 °C at the end of the process does not exceed the 1.020 °C, temperature of dissolution of the phase δ, from which the size of grain begins to grow. By this reason, for both cases the microstructure obtained is similar regarding homogeneity and size of grain.
In the following graphic show the maximum values and minimum of the size of grain for each one of the two previous cases.
![It appears 10. [Size of maximum grain and minimum. Comparative of the escalado] It appears 10. [Size of maximum grain and minimum. Comparative of the escalado]](https://img.interempresas.net/fotos/908130.jpeg)
Like conclusion obtains the verification of the similarity in both cases, escalado 1/3 and real, of the homogeneity and the afinamiento of grain.
2. Influence of parameters of the process on the preforma climbing 1/3
After the comparative realizar in the previous section, in the present section studies the influence of different parameters on the final microstructure. The parameters selected have been the size of initial grain, the speed of the process and the angle of nutación.
2.1 Size of initial grain
To be able to see the influence of this parameter have analysed two cases, one splitting of 4ASTM and another of 9ASTM like size of initial grain. The initial parameters of process are equal for both cases: speeds of 70 rpm and 0,8 mm/s, temperature of equal toolings to 500 °C and initial temperature of the previous swearword to forges it rotary presses equal to 970 °C.
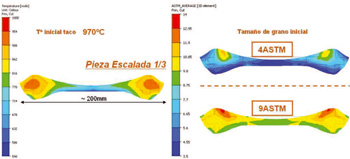
Like conclusion of the previous images, the distribution obtained is homogénea when the size of fine initial grain is 9ASTM. In the case of size of initial grain the same to 4ASTM needs increase the temperature to guarantee the recristalización in all or at least big part of the geometry and obtain a fine final microstructure and homogénea.
In the following graphic show the maximum values and minimum of the size of grain for each one of the two previous cases.
![It appears 12. [Size of maximum grain and minimum. Influence of the size of initial grain] It appears 12. [Size of maximum grain and minimum. Influence of the size of initial grain]](https://img.interempresas.net/fotos/908133.jpeg)
In the graphic previous remains patent again the homogeneity of the microstructure splitting of a size of fine grain. In this way they establish the two variants of work in function of the size of initial grain for the case whose put was the obtaining of a fine microstructure and homogénea. Splitting of size of fine grain the aim to achieve during the process of conformed is not increasing the temperature above the temperature of dissolution of the phase δ so as to not worsening the already fine microstructure initial. However, splitting of size of earthy grain the aim of the process of conformed is recristalizar the greater section of the possible geometry to fine-tune the size of initial grain.
2.2 Speed of conformed
The study of the influence of the speed of conformed is cream of the need to adapt the parameters of the geometry climbing to the parameters of the available experimental machine in Tecnalia. The speeds of process used in the case of the real geometry were conditioned by the size of the piece. The reduction of the speed of work is directly proportional to the reduction of pairs and efforts. However, in the case of the piece climbing to 1/3 is possible to increase this speed allowing realizar an analysis of the sensitivity of this parameter.
Like first consequence of the variation of the speed of the process arises the variation of the strengths in the same. In the following graphic visualises the evolution of the strength during the process of forge rotary presses for three different speeds of process, a corresponding to the speeds of the to scale real geometry, 70 rpm and 0,8 mm/s, and two corresponding to the speeds adapted to the experimental machine situated in Tecnalia, 300 rpm with the variation between 15 and 5 mm/s.
![It appears 13. [Comparative of strengths for different speeds of process of foja rotary presses] It appears 13. [Comparative of strengths for different speeds of process of foja rotary presses]](https://img.interempresas.net/fotos/908153.jpeg)
The maximum strength obtained for the speed of conformed of 70 rpm and 0,8 mm/s finds between the resultant of the others two faster speeds.
To continuation show the corresponding figures to the comparative temperature - microstructure for the different speeds of process, as in previous sections. The initial parameters for all the cases have been initial temperature of the swearword 970 °C, size of initial grain 9ASTM and temperature of equal toolings to 500 °C.
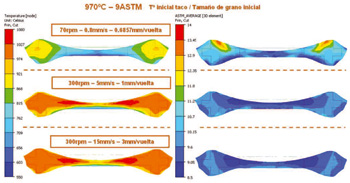
The fastest speeds of process originate a distribution more homogénea of the microstructure. By the contrary, are these those that ocasionan greater temperature in the inner zones of the geometry ocasionando growth of the size of grain in these zones. However, this phenomenon will remain controlled taking an initial temperature adapted to the parameters of the process.
In the following graphic show the maximum values and minimum of the size of grain for each one of the three previous cases.
![It appears 15. [Size of maximum grain and minimum. Influence of the speed of the process] It appears 15. [Size of maximum grain and minimum. Influence of the speed of the process]](https://img.interempresas.net/fotos/908156.jpeg)
In the figure 15 have represented the maximum values and minima of size of grain for the distinct cinematic cases studied, remaining reflected the tendency to the homogeneity of grain to measure that increase the speed of conformed.
2.3 Angle of nutación
The angle of nutación is the angle that forms the axis of the upper tooling with the vertical. The increase of this angle originates the increase of the incremental character of the process. That is to say, when increasing the angle, the section of the upper tooling in contact with the swearword, manager of the conformed, reduces what comports to the reduction of the necessary strengths for the conformed.
In the following figure represents said tooling bent with two angles of nutación different, 5º and 2º. All the exposed cases until this section have been realizar with an angle of nutación of 5º.
![It appears 16. [Upper tooling with different angles of nutación] It appears 16. [Upper tooling with different angles of nutación]](https://img.interempresas.net/fotos/908157.jpeg)
The strengths required for both processes expose to continuation. It is appreciable the reduction of the tonelaje necessary to deform the same geometry increasing the angle of nutación of 2º to 5º.
![It appears 17. [Comparative of strengths for angles of nutación of foja rotary presses] It appears 17. [Comparative of strengths for angles of nutación of foja rotary presses]](https://img.interempresas.net/fotos/908158.jpeg)
To continuation show the corresponding figures to the comparative temperature – microstructure for the different angles of nutación. The initial parameters for all the cases have been initial temperature of the swearword 970 °C, size of initial grain 9ASTM, temperature of equal toolings to 500 °C and speeds of 300 rpm and 5 mm/s.

The most accused differences see in the temperature reached in the central zone, being the case of the angle of 5º upper to the of 2º. By the contrary, the effect in the microstructure is practically invalid.
In the following graphic show the maximum values and minimum of the size of grain for each one of the two previous cases.
![It appears 19. [Size of maximum grain and minimum. Influence of the angle of nutación] It appears 19. [Size of maximum grain and minimum. Influence of the angle of nutación]](https://img.interempresas.net/fotos/908160.jpeg)
Conclusions
In the present article exposes the study of the parameters obtained of a piece of the aeronautical sector component manufacturing sector component manufacturing sector so as to manufacture it by means of the incremental process of conformed designated forge rotary presses applied to one of the most used materials in said sector, the Inconel 718.
The first step was to define the preforma and the parameters of necessary process for the manufacture of the component to study inside the specifications of available machines in the market.
So as to be able to realizar an experimental validation, escaló the geometry to 1/3 of the real dimensions to be able to adapt the process to the experimental machine of forge rotary presses available in Tecnalia.
Like conclusion of the analysis of the variables of process is possible to affirm:
- For the obtaining of microstructures of size of fine grain and homogéneo, distinguish two strategies of conformed in function of the size of initial grain of the swearword:
- For sizes of fine initial grain ( 9ASTM): the aim of the process of conformed is not increasing the temperature above the temperature of dissolution of the phase δ of the Inconel 718 to avoid the growth of the size of grain, keeping in this way the fine microstructure and homogénea initial.
- For sizes of earthy initial grain ( 4ASTM): the aim of the process of conformed is recristalizar the grain. This sees favoured when increasing the initial temperature of the swearword.
- The final microstructure of a piece is independent of the angle of nutación used for forges it rotary presses.
- The keys for the obtaining of a microstructure homogénea and fine are, therefore:
- Split of size of fine grain.
- Split of an initial temperature of swearword the sufficiently small ( 970 °C) not to surpass the temperature of dissolution of the phase δ during the process of conformed.
- Speeds of conformed fast, from 1mm/s, involving greater speeds of deformation.
Future work
The immediate work to develop along the present year is the execution of the responsible essays of the experimental validation of the numerical work presented in this article and for which already has designed the leaf of route of manufacture.
Gratitudes
This work is funded by the program Etortek of the Basque Government, in concrete by the project of reference ProFUTURE (IE10-271). For the execution of this work have been indispensable the collaboration of the companies Industries Puigjaner, S.A. (DENN) and Industry of Turbo Propellants, S.A. (ITP). Tecnalia in collaboration with DENN developed a machine of forge rotary presses that it will be used to realizar the experimental validation of the present work in the near future. This work had not been possible without the geometrical data provided by ITP.
References
[1] G. Liu, S.J. Yuan, Z.R. Wang, D.C. Zhou. “Explanation of the mushroom effect in the rotary presses forging of To cylinder”: submitted to Journal of Materials Processing Technology (2004)
[2] X. Mateu, J.F. Puigjaner, M. Albea, J. Saint José, M. T. Santos, S. Varela. “Process design and simulation of aluminium wheel disk manufactured by rotary presses forge and flowforming”: submitted to 3rd ASIAFORGE Meeting (2010)
[3] J. Saint José, M. T. Santos, S. Varela, M. Albea, X. Medan, J. F. Puigjaner. “Material reduction costs by new rotary presses processes: rotary presses forging and flowforming”: submitted to 30rd SENAFOR Congress 2010 (2010)
[4] To, Sleeves, M. Santos, J. Saint Jose, G. Atxaga, Or. Adarraga, Microstructural behaviour in Rotary presses Forging of Inconel 718, submitted to ESAFORM 2012 Congress (2012).
[5] To, Sleeves, M. Santos, J.I. Zarazua, J. Saint Jose, G. Atxaga, Or. Adarraga, Sensitivity Analysis to optimise the microstructural properties of an Inconel 718 component manufactured by Rotary presses Forging, submitted to ESAFORM 2013 Congress (2013).
[6] T. ALtan, G. Ngaile, G. Shen. Cod and Hot Forging, Fundamentals and Applications. First edition, ASTM International, 2005
[7] J.R. Cho, H.S. Jeong, D. J. Cha, W. B. Bae, J. W. It reads. “Prediction of microstructural evolution and recrystallization behaviours of To hot working die steel by FEM”: submitted to Journal of materials processing technology (2004)
[8] C.To. Dandre, C.To. Walsh, R.W. Evans, R.C. Reed and H.M. Roberts. “Microstructural evolution of nickel-Base superalloy forgings during ingot-to-billet conversion: process modelling and validation”. Superalloys 2000, Edited by T.M. Pollock, R.D. Kissinger, R.R. Bowman, K.To. Green, M. McLean, S. Olson, and J.J. Schirra. TMS Me Minerals, Metals & Materials Society), 2000
[9] C. Ruiz, To. Obabueki, K. Gillespie, Evaluation of the microstructure and mechanical properties of delta processed alloy 718. The Minerals, Metals & Materials Society (1992) 33-42.
[10] C.To. Dandre, C.To. Walsh, R.W. Evans, R.C. Reed and H.M. Roberts. “Microstructural evolution of nickel-Base superalloy forgings during ingot-to-billet conversion: process modelling and validation”. Minerals, Metals & Materials Society (2000) 85-94.
[11] M. C. Mataya, Simulating microstructural evolution during the hot working of Alloy 718, JOM (1999) 18-26.