Technologies for the taladrado of aeronautical sector component manufacturing sector component manufacturing materials advanced
On the other hand, the improvement in the productive performance of the companies in the 21st century does not have to accommodate in scoop to linear approaches that only contemplate economic profits, forgetting no only the socioeconomic context in which they find immersed, but, to his time, the responsibility in front of a global society that demands increasingly a maximum respect to the environingingment and a rational use of the energetic resources that reflect in an approach to optimum levels of energetic efficiency in the systems of manufacture.
In the sense of the previously exposed, the development of technologies and material that open new roads in the air transport has been a continuous worry in the aerospace industry. In the actuality, the majority of the companies aeronautical sector component manufacturing sector component manufacturing constructors contemplate the use of alloys of aluminium very known or some of his sufficiently studied variants. Like this, they employ , basically, alloys of the series 2XXX (To the-Cu), like the UNS To92024, and of the series 7XXX (To the-Zn), like the UNS To97075 or the UNS To97050 or his more recent variants like the UNS To97150. These alloys have come using because of his excellent relation weigh/physical properties-chemical/cost. The continuous research of improvements in the productive performance and in service of the aeronautical sector component manufacturing sector component manufacturing elements carries achieve the development of materials that optimise the previously exposed relation.
Like this, open three roads of investigation that tend to improve it [6]:
- Decrease of weight. The reduction of weight of the structure of the aeroplane allows the possibility to incorporate a greater load without need to increase the energetic consumption for his trip. This reduction of weight contemplates the employment of materials lighter that, like minimum, ensure the same properties that the used traditionally, what guarantees a maintenance of the excellent conditions of hygiene showed until the moment. These ambitious aims require a revolutionary change in the applicable technology to this industrial state. In this line find the tending investigations to the modification of the already existent alloys, to the development of new alloys and to the application of other lighter materials. In the related with the most specific appearances of this project would fit to stand out the development and application of alloys of To the-Li, (UNS To92098 and his variant at present in phase of study UNS To92198), in his day abandoned by problems of corrosion and restarted in the actuality (fits to quote like example the fact that it is one of the lines prioritarias of marked investigation by Airbus —Airbus R&D Strategic Program— in the year 2005). On the other hand, the application of materials no metallic that cause a marked reduction of weight, as it is the case of the materials composed of organic matrix (NMMC, Non-Metal Matrix Composites), especially the Fibre of Carbon (FC) is increasingly widespread and his percentage of presence in the aircraft is increasingly high. In fact, although the use of materials composed for the manufacture of components of aeronautical sector component manufacturing sector component manufacturing structures in commercial aeroplanes can retrotraerse to the program ACEE (Aircraft Power Efficiency) of the Nasa in the seventies, at present, the employment of materials composed in aeronautical sector component manufacturing sector component manufacturing structures is very high so much in commercial aeroplanes of last generation like the Boeing 787 or the Airbus To350, in which the compound materials can constitute more than 50% of the structure, as in military aeroplanes (To 400M) or helicopters, in which, in some cases, arrives, even, to surpass with amplitude.
- Improves in the physical properties-chemical. The improvement of the properties looks for from the incorporation of materials like the alloys of titanium (fundamentally the alloy You6To the4V), light, with good mechanical properties and highly resistant to the corrosion, or like the already mentioned NMMC that allow, solos or in combination with other metallic materials forming FML (Fiber Metal Laminates), have of excellent values of a lot of properties fisico-chemical with a remarkable reduction of the effective weight. Precisely the use of the combinations FC/You6To the4V, FC/Alloy of Aluminium and FC/Alloy of Aluminium/You6To the4V are the FML more frequent in the aerospace industry. In particular, the first have a special importance due to the fact that they do not form a galvanic pair so accused as in the case of the combination FC/Alloy of Aluminium. Incidentally, in relation with this type of improvements, the investigations also direct to the application of possible modifications in the processes of manufacture that allow to improve the performance in service in materials more commonly employees, applying new treatments of finishing that improve properties in surface like the corrosion or his combination with other mechanical properties as it is the case of the corrosion under tension (CBT). Finally, another of the possibilities tackled in this line contemplates the improvement of the properties in surface without need of employment of superficial treatments but, directly, from a situation of commitment bet
- Decrease of the cost. At present, to the hour to do reference to the cost, do not have to have only in account the economic appearances in absolute terms, but, incidentally, also have to contemplate the appearances related with the environingingmental impact of the materials and his processed. A situation of commitment between both appearances has when they delete intermediate stages in the process of manufacture of the distinct elements, what, of direct way, affects to the time of manufactura and to the energetic consumption associated. Other factors, like the adecuación of the parameters, the elongation of the life of the tooling or the employment of technologies cleaner influence positively on the two previously mentioned appearances.
Utilisation of materials composed in the manufacture of aircraft
The properties associated to the compound materials cover widely the rank of improvements previously exposed had to, essentially, to his high structural efficiency, making possible manufacture aircraft and other systems of collective and individual transport in which it can reach a considerable saving in direct operative costs, by a part by the saving of fuel because of having of structures lighter, and by another by the considerable decrease of problems of corrosion and deterioration of structures. On the other hand, the employment of these materials does feasible the realisation of wits that resulted impossible or very difficult to realise with the employment of classical materials of engineering.
These materials have besides undoubted advantages tied to the exigencias of a greater hygiene, lower consumption of power and of costs of maintenance or prevention of risks that characterise nowadays to the air transport [6], in front of other materials in these uses, as excellent relation between mechanical resistance and weight, rigidity, increase of the useful life thanks to his good resistance to the fatigue, resistance to the corrosion, resistance to the abrasion, acoustic isolation and his ductility that allows to give them the form demanded by the design, what allows to increase the monolithic elements, reducing of this form the components for assembling and, in consequence, the points of union, that are, with frequency, the more critics in the structure of an aircraft.
Besides, the compound materials can consider at present like a new type of material with the sufficient maturity as to be able to employ of massive form with a high degree of reliability. However, they exist a lot of appearances, so much of the own material as of the technologies to them associated, that are not totally mature and exists a considerable capacity of improvement, so much in the provision and characteristic of the materials in yes, as in the processes and technologies associated to the employment and put in service of the structural elements realised with this type of material [7-9].
In the actuality, the world-wide market of the compound materials grows from mediated of the years 90 to 5,7% annual. The growth is more favourable for thermoplastic compounds that for thermostable compounds: 9% and 3% annual, respectively; however, the thermostable materials, represent even more of the two third parts of the market [10].
In the figure 1, can observe the percentage of the main materials of reinforcement and matrix more used, on the other hand, in the figure 2, can appreciate the form of these reinforcements [11].
![It appears 1. Main materials used in the matrix and in the reinforcement. Adapted of [11] It appears 1. Main materials used in the matrix and in the reinforcement. Adapted of [11]](https://img.interempresas.net/fotos/769540.jpeg)
![It appears 2. Main forms of the reinforcements used in the compound materials. Adapted of [11] It appears 2. Main forms of the reinforcements used in the compound materials. Adapted of [11]](https://img.interempresas.net/fotos/769541.jpeg)
In this line find the tending investigations to the application of materials no metallic that cause a marked reduction of weight, as it is the case of the materials composed of organic matrix, especially the reinforced with fibre of carbon (Carbon Fiber Reinforced plastics-CFRP), whose employment is increasingly widespread and his percentage of presence in the aircraft is increasingly high.
Regarding needs of material, the civil aviation is, with difference, the aeronautical sector component manufacturing sector component manufacturing segment that elder consummate demand, but the materials composed also are going in with strength in the rest of segments. A tendency of this milestone appreciates in the increase of the percentage of utilisation of materials composed in an aeroplane, from 5% in the decade of the years 80, to 50% used at present.
Of generic form, the utilisation of compound material (basically of fibre of carbon with polymeric matrix) in the aeronautical sector component manufacturing sector component manufacturing industry can estimate in [2-5]:
- commercial Aircraft: 21.000 tonnes in 2007-2011 (33.000 tonnes in 2012-2016).
- Executive and general aviation: 1.200 tonnes in 2007-2011.
- Aircraft of rotatory wing: 3.000 tonnes MC in 2007-2012.
- Military aircraft: 2.300 tonnes in 2007-2011.
- Launch vehicles: 1.500 tonnes in 2007-2011.
The current world-wide capacity of production of fibre of carbon of aerospace degree estimates in some 60.000 tonnes/year.
As it has commented previously, the introduction of the materials composed in civil aviation had his starts in the years 80 and although with a very small repercussion in the total of the aircraft, little by little the percentage of compound materials has gone increasing of significant way. In the case of the Airbus To380, the use of compound materials reaches almost 25% of the total of the structure and in the Boeing B787 (figure 3) arrives to 50% of the structural weight, of the same order that in the Airbus To350XWB (figure 4), that will reach 52%. These values are perhaps more indicativos when they expresses in volumetric terms (a B787 has roughly 80% of structure of materials composed in volume).
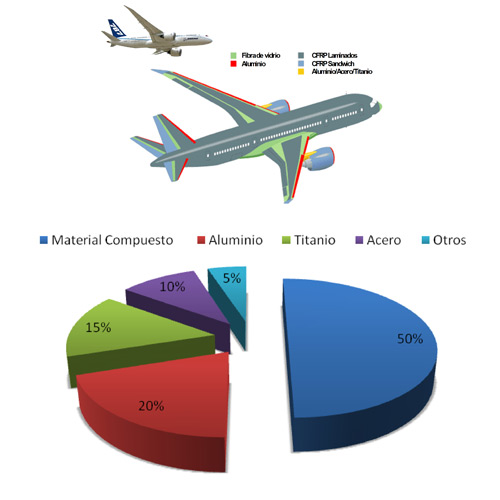
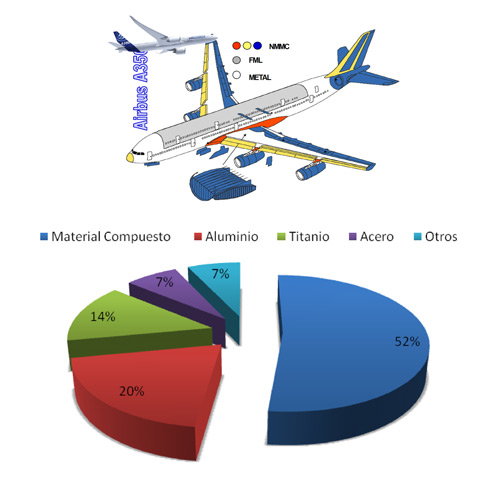
In spite of his undoubted advantages, these materials present in the actuality a series of problems. In effect, the costs of manufacture are high (costly investments in installations and equipment), costly programs of evaluation, qualification and certification of structures. It can have variations in the rigidity and the mechanical resistance of the compounds (in determinate circumstances), low resistance to the impact, low electrical conductivity, costs of high materials, entrance of water in structures sándwich and difficult recycled, etc. [12, 18-21]. Besides, the controls of the pieces manufactured (visual inspection, X-rays, ultrasounds and essays of resistance) to detect the main defects that can present in the same can result especially costly. These defects, between which can quote the discontinuidades between plates produced by the existence of air trapped, the fault of resin, delaminaciones that appear during the cured, cured incomplete of the resin, excess of resin between plates, porosidad, wrong orientation of the plates to form the laminado, damage in the fibres, inclusions, variations in the thickness and unacceptable unions can result especially critics for the hygiene [24-28].
Incidentally, the components and pieces realised with this type of materials are usually manufactured for a concrete application. Besides, because of exigencias technical of quality and of assembling, these have to be subjected to different operations of conformed. One of the processes more widely employees are the processes of mechanised.
Mechanised of compound materials employees in the aeronautical sector component manufacturing sector component manufacturing industry
The processes of mechanised of compound materials differ significantly in many respects of the mechanised of metallic materials [26,31], since they comport like materials no homogéneos and anisotropic, depending on the characteristics and the content of his constituents (matrix and reinforcements). Because of this, during the process of cut, the tools go in in contact alternatively with the fibre of carbon and the matrix, where the answer of each one is totally different. Besides, it is necessary to take into account that two materials composed never comport the same to the hour to be mechanised, even having been manufactured with the same process [24].
Technologies in the taladrado of materials composed in the aeronautical sector component manufacturing sector component manufacturing industry
One of the most critical processes in the mechanised of compound materials is the taladrado. This has to to the big number of orifices that are necessary to realise during the operations of setting in structural elements. Because of this, is necessary to study the current problems that surround the mechanised of fibre of carbon with matrix epoxídica in the aeronautical sector component manufacturing sector component manufacturing industry [33-36].
Like consequence of the exposed previously and because of the characteristics described of these materials, arises the need to modify or adapt in the industry the tools and technical of mechanised traditional incorporating new improvements to the minimum cost. In definite, the mechanised of compound materials pursues the improvement of the process. This aim has to achieve in conditions that favour a minimum cost of power and the lower repercussion in the environingingment, without sacrificing the functionality of the pieces obtained.
In this context, contemplates the possibility to do use of technologies no conventional of mechanised, as they are the cut by laser or the cut by chorro of water and substitute the manual or semi-automatic means, that were and are in a lot of cases the used in the aeronautical sector component manufacturing sector component manufacturing industry.
The use of these technologies in the mechanised of these materials has grown considerably in the last years, although the investigations keep on being more intense regarding the conventional technologies, appears 5.
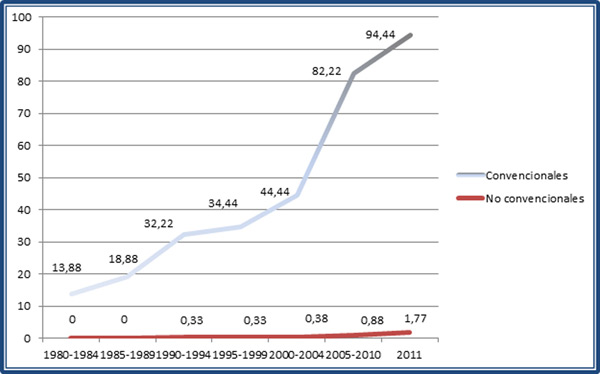
In any case, is necessary to have of elements of trial to be able to effect a comparative analysis that allow to select the most adapted technologies for the taladrado of this type of materials on the base of criteria of near to the usually employed variables, as they are material to mechanise, tool: geometry and material, parameters of cut, strengths of cutting and power of cut, process of mechanised, typology of the shaving, superficial finishing, friction and temperature of cut, lubricación, wear and life of tool and vibrations.
In the case of the CFRP, the quality of the holes is determined mainly by geometrical defects, the delaminación, and the thermal sensors damage [1, 7, 11]. In the table 1 reproduces , a comparative table in which resume the defectología of the holes developed by distinct technical.
Table 1. Defectología Of the taladros by different technologies
Type of Defect |
conventional Technology |
Technology Laser |
Technology AWJM |
Delaminación |
X |
|
X |
Conicidad |
|
X |
X |
DO (Zone affected térmicamente) |
X |
X |
|
Circularidad |
X |
X |
X |
Cilindricidad |
X |
X |
X |
The delaminación is characterised by the separation of adjacent layers of the laminado caused by an external action and depends no only of the nature of the fibre or of the resin but also of the properties of the union. The conicidad is not more than a uniform difference of diameter that results in one coins or a conical figure. The circular defect is related with the orientation of the fibres of the layer affected and depends on the angular position of the axles of cutting [10], the unilateral behaviour of the fibres of carbon drives to the elliptical form of the hole. The zone affected térmicamente (DO, of Heat Affected Zone) limits to the region in which the temperature exceeds to the temperature of vaporisation of the matrix [11].
In accordance with [12-20] the main studies for the taladrado conventional of CFRP have oriented to the analysis of the employment of the broaches with different composition, coatings, geometry and parameters of cut, based, fundamentally in the characterisation of the delaminación and the establishment of correlations with the strength of push exerted. Incidentally, they have realised studies of rugosidad, thermal sensors damage [9, 10, 21-23], throwing in fault the existence of systematic studies in which they contemplate the distinct variables.
In the case of the taladrado with do laser (LBM, of Laser Beam Machining) the own characteristics of the technician [24] have motivated that the evaluation of the quality of the holes have centred , especially, in the thermal sensors damage and the deviations macrogeométricas of conicidad [11, 15, 25-27], in addition to the same type of studies realised for taladrados conventional.
Regarding the parameters of study for the quality of the holes by taladrado laser, have served like base also for the study of the quality of the orifices by means of mechanised with chorro of water (WJM, of Waterjet Machining, or AWJM, of Abrasive Waterjet Machining) [44, 48].
From the data collected in the bibliography, in the table 2, has established a comparative summary for the distinct technologies employed.
Table 2. Comparative between technologies
|
conventional Technology |
Technology Laser |
Technology AWJM |
Source of Power |
Mechanics |
Luz |
Hidromecánica |
initial Investment |
Average |
Alta |
Alta |
Cost of operation |
Average |
Under |
Low-Half |
Cost of the team |
Half |
High |
High |
Maintenance |
Half |
Under |
Half |
Flexibility |
Average |
Alta |
Alta |
Time of operation |
High |
Under |
Half |
Pollution |
Average |
Drop |
Average |
Production of dust |
If |
No |
No |
Production of gases |
No |
If |
No |
Need of taladro initial |
No |
No |
No |
Precision |
Good |
Alta |
Average |
Size of the hole |
Half |
All |
Half and Big |
blind Hole |
If |
No |
No |
Thickness limited |
If |
If |
No |
Effect taper |
No |
If |
If |
Risk of delaminación |
If |
No |
If |
Strengths of cut |
Alta |
Non-existent |
Drop |
DO |
Average |
Alta |
Non-existent |
Conclusions
The improvement of the performance in a process and system of manufacture has to contemplate economic appearances, energetic and environingingmental. In the aeronautical sector component manufacturing sector component manufacturing industry, an approximation to the maximisation of the performance can llevar from the employment of materials lighter and with better properties physical chemistries. Between these materials find the compound materials reinforced with fibre of carbon, whose employment is extending until reaching upper percentages to 50% in the structural elements of the aircraft. These materials have to bear different processes of conformed before adopting his final form. Between said processes find the processes of mechanised and, very especially, the processes of taladrado. The nature of these materials does that his maquinabilidad present special difficulties, what reflects in a defectología specific very characteristic in the case of the processes of taladrado. In these processes, in the last years has treated to apply a group of technologies no conventional that can improve the performance.
Of all the previously pointed, fits to stand out that each one of the distinguished technologies produces a type of defectología to the piece mechanised that affects to the quality of the orifice realised. Therefore, have to study the parameters that govern the process of cut to attain minimise said damages. On the other hand, the processing of this material by means of the no conventional technicians is quite viable, but has to remark that it does not exist a process of mechanised ideal in yes, but depending on diverse parameters will exist a more adapted process for the taladrado [45-50].
References
- P. Mayuet. ‘Methodological proposal and First Results for the Study of the Quality of the Taladrado of Materials Composed of Fibre of Carbon with Matrix Epoxídica'. University of Cádiz, Upper School of Engineering, Máster University in Engineering of Manufacture. Cádiz (2011).
- ‘Summary of the executive plan of the Spanish aerospace platform'. [On line: 20/06/2.012]. URL: http://www.plataforma-aeroespacial.org/
- ‘Strategic diary of aerospace investigation. Executive summary'. [On line: 20/06/2.012]. URL: http://www.plataforma-aeroespacial.org/
- ‘What are the JTI?' [On line: 22/11/2.011]. URL:http://www.oemicinn.es/programas-e-iniciativas/iniciativas-tecnologicas-conjuntas-jtis/ultimas-noticias/reportaje-que-son-las-jti
- ‘Harmonisation of the activities in materials composed for aeronautical sector component manufacturing sector component manufacturing and the space in Spain'. [On line: 22/11/2.011]. URL: http://www.plataforma-aeroespacial.org/
- J. Salguero. ‘Study of the process of milling peripheral of high speed of the alloy of aerospace use UNS To92024-T3'. University of Cádiz, Upper School of Engineering, Interuniversity Program of Doctorate in Engineering of Manufacture. Cádiz (2008).
- M. Álvarez. ‘Preliminary study of the taladrado of materials composed of aeronautical sector component manufacturing sector component manufacturing use'. University of Cádiz, Upper School of Engineering, Interuniversity Program of Doctorate in Engineering of Manufacture. Cádiz (2008).
- ‘Material Composed in the aeronautical sector component manufacturing sector component manufacturing sector component manufacturing Industry'. [On line: 24/06/2.012]. URL:http://es.scribd.com/doc/6114467/materiales-compuestos-aeronautica-airbus
- ‘Material Composed in the aeronautical sector component manufacturing sector component manufacturing sector component manufacturing Industry. New developments of materials composed of organic matrix'. [On line: 24/06/2.012]. URL: http://www.urjc.es/fundacion/cursos_verano/ponencias/josesanchez.pdf
- ‘Material day composed for aeronautical sector component manufacturing sector component manufacturing and the space in Spain'. FIDAMC. Spain (2010).
- A.m. Abrao, P.And. Faria, J.C. Blond fields, P. Reis, J. Paulo Davim. ‘Drilling of fiber reinforced plastics: To review. Journal of Material Processing Technology', Volume 186 (2007). 1-7.
- M. S. Carrilero, M. Marcos. ‘Parametric relations in the Mechanised', Service of Publications of the University of Cádiz. Cádiz (Spain). 1994.
- ‘The Mechanised Modern (Practical Manual)', Sandvik Coromant, Dtpo. Of Technical Editions, First edition (Spain).1994.
- H. The-Hofy. ‘Machining Processes. Conventional and Non-Conventional Processes'. Taylor and Francis Group. UK. 2007
- G. Boothroyd, W. To. Knight. ‘Fundamental of machining and machine tools Marcel Dekker', Inc. Second Edition. 1989.
- N. Marín, ‘Analysis termomecánico of the influence of the geometrical wear of the tools in processes of orthogonal cutting of stainless steels austeníticos', University Carlos III, Leganés, Madrid (Spain).
- M. Batiste. ‘Characterisation of elements of wear of tool of cut by secondary adhesion in the turning in dry of alloys of aluminium', University of Cádiz, Upper School of Engineering, Máster Official in Engineering of Manufacture. Cádiz (2008).
- S. Rawat, H. Attia. ‘Wear mechanisms and tool life management of Wc-Co drills dry high Speed drilling of woven carbon fibre composites'. Wear, Volume 267 (2009). 1022-1030.
- S.C. Lin, I.K. Chen. Drilling carbon fiber-reinforced composite Material at high speed. Wear, Volume 194 (1996). 156-162.
- S. Abrate, D.To. Walton. ‘Machining of composite Material. Part I: t
- R. Piquet, B. Ferret, F. Lachaud, P. Swider. ‘Experimental analysis of drilling damage in thin coal/epoxy plate using special drills'. Composites: part To. Applied sciencie and manufacturing, Volume 131 (2000). 1107-1115.
- M. Álvarez, M. Sánchez-Carrilero, B. Grille, J. M. Sánchez, F. Torres, M. Mud, J. M. González, M. Marcos. ‘Study of the taladrado of fibre of carbon'. Annals of Mechanical Engineering, Volume 14 (2003). 1635-1638.
- F. Girot. ‘Mechanised of compound materials. Seminar of Engineering of Mechanised of Compound Materials'. University of Cádiz, 2012.
- R. Teti. ‘Machining of composite materials'. CIRP Annals - Manufacturing Technology, 51(2002) 611-634
- H.K. Tönshoff, W. Spintig, W. König. ‘Machining of holes developments in drilling technology'. CIRP Annals - Manufacturing Technology, 43 (1994). 551-561.
- ‘Technology of manufacture' [On line: 20/11/2.011]. URL: http://www.izaro.com/contenidos/ver.php?id=es&=3&his=32&co=1297422668
- ‘Efficiency in despegue'. Metalworking world. Sandvik Coromant. Volume 1 of the year 2010.
- Precorp. ‘Aerospace solutions'. Catalogue of aeronautical sector component manufacturing sector component manufacturing tools, 2012.
- W. König, C. Wulf, P. Graβ, H, Willerscheid. ‘Machining of fibre reinforced plastics'. Annals of the CIRP, 34 (1985). 537-548.
- R. Piquet, B. Ferret, F. Lachaud, P. Swider. ‘Experimental analysis of drilling damage in thin coal/epoxy plate using special drills. Composites: part To. Applied sciencie and manufacturing', Volume 131 (2000). 1107-1115.
- H. Hocheng, C.C. Tsao. ‘The path towards delamination-free drilling of composite materials'. Journal of Material Processing Technology, Volume 167 (2005). 251-264.
- C.C. Tsao. ‘Investigation into the effects of drilling parameters on delamination by various step-core drills'. Journal of Material Processing Technology, Volume 206 (2008). 405-411.
- C.C. Tsao, And.C. Chiu. ‘Evaluation of drilling parameters on thrust force in drilling carbon fiver reinforced plastic (CFRP) composite laminates using compound core-special drills'. International Journal of Machine Tools & Manufacture, Volume 51 (2011). 740-744.
- H. Hocheng, C.C. Tsao. ‘Comprehensive analysis of delamination in drilling of composite materials with various drills Bits'. Journal of Material Processing Technology, Volume 140 (2004). 335-339.
- L.N. López of Lacalle, J.To. Sánchez-Galíndez, To. Lamikiz. ‘Mechanised of high performance'. Technical editions Izaro. Bilbao (Spain). 2004.
- S.C. Lin, I.K. Chen. ‘Drilling carbon fiber-reinforced composite Material at high speed'. Wear, Volume 194 (1996). 156-162.
- W. König, P. Graβ. ‘Quality definition and assessment in drilling of fibre reinforced thermosets'. Annals of the CIRP, Volume 38 (1989). 119-124.
- L.S. Shyha, D.K. Aspinwall, S.L. I praise, S. Bradley. ‘Drill geometry and operating effects when cutting small diameter holes in CFRP'. International Journal of Machine Tools & Manufacture, Volume 49 (2009). 1008-1014.
- To. Langella, L. Nele, To. Maio. ‘To torque and thrust prediction model for drilling of composite materials'. Composites: part To. Applied sciencie and manufacturing, Volume 36 (2005). 83-93.
- M. Álvarez, M. Sánchez-Carrilero, J.And. Ares, J. M. González, M. Marcos. ‘Influence of the relation speed of cutting-advance in the superficial quality of samples taladradas of fibre of carbon'. Magazine of Metallurgy, Volume Ext. (2005). 361-364.
- To. Faraz, D. Biermann, K. Weinert. Cutting edge rounding: an innovate tool wear criterion in drilling CFRP composite laminates. International Journal of Machine Tools & Manufacture, Volume 49 (2005). 1185-1196.
- K. Ogawa, And. Aoyama, H. Inoue, T. Hirogaki, H. Nobe, And. Kitahara, T. Katayama, M. Gunjima. ‘Investigation on cutting mechanism in small diameter drilling for CFRP (thrust Forced and surface roughness at drilled hole wall)'. Composite Structures, Volume 38 (1997), 343-350.
- K. D. Avanish, And. Vinod, Laser beam machining—‘To review, International Journal of Machine Tools & Manufacture 48', (2008), 609-628.
- Z. L. Li, P. L. Chu, H. And. Zheng, and G. C. Lim, ‘Process development of laser machining of carbon fibre reinforced plastic composites', SIMTech technical reports (STR_V10_N1_03_MTG).
- C.And. Yeo, S.C. Tam, S. Jana, M. W.S. Lau, ' To technical review of the laser drilling of aerospace materials', Journal of Materials Processing Technology, 42, (1994),15-49.
- C. F. Cheng, And. C. Tsui, T. W. Clyne, ‘Application of to three-dimensional heat flow model to treat laser drilling of carbon fibre composites', Record Metallurgica, Vol. 46, No. 12, (1998) pp. 4273-4285.
- D.K. Shanmugam, T. Nguyen, J. Wang, ‘To study of delamination on graphite epoxy composites in abrasive waterjet machining, Composites: Part To', 39, (2008), 923-929.
- C. To. Friend, R.W. Clyne, G.G. Valentine, ‘Machining graphite composite materials', Proc. 6th Symp. on Composite Materials in Engineering Design, ed. Noton, B.R., ASM, (1973), 242-250.
- R.B. Adams, ‘Waterjet machining of composites', Society of Manufacturing Engineers, Conference on Composites in Manufacturing, 5th, Los Angeles (EE UU), 1986.